In this first section, we will investigate how to plan the mechanical layout
of a tube (valve) amplifier. At this stage, freedom of choice is unlimited,
whereas later it will be restricted. So it is important that the choices and
compromises made now are the best ones. Whilst good planning will not save
a poor design, poor planning can certainly ruin a good one.
Chassis layout
Tube (valve) amplifiers use a number of large components that must be positioned
relative to one another such that the connecting wires between each component
are as short as possible, but that the components and their associated wires
do not interfere with each other. Chassis layout breaks down into the following
considerations:
-- Electromagnetic induction: Minimizing hum induction from chokes and transformers
into each other and into tubes.
-- Heat: Output tubes, etc. are hot and must be cooled. Conversely, capacitors
run cool, and must be kept that way.
-- Unwanted voltage drops: All wires have resistance, so the wiring must
be arranged to minimize any adverse effects of these voltage drops.
-- Electrostatic induction: Minimizing hum from AC power wiring is not often
a problem, because even thin conductive foil provides perfect electrostatic
screening.
-- Mechanical/safety: Achieving an efficient chassis arrangement that is
easily made, maintained, and used.
-- Acoustical: Almost all components are microphonic, but tubes are the worst.
We should consider which components are most sensitive to vibration, and minimize
their exposure to it.
-- Aesthetic: The highest expression of engineering is indistinguishable
from art. If you have a superb chassis layout, it will probably look good.
Conversely, if it looks poor, it is probably a poor layout . . .
We have a seven-dimensional problem. A poor transistor amplifier might be
able to hide behind the fence of negative feed back, but tube (valve) amplifiers
using an output transformer cannot usually tolerate more than 25 dB of feedback
before their stability becomes distinctly questionable. Consequently, layout
is critical to performance.
The large components are generally the mains transformers, output transformers,
power supply chokes, power supply capacitors, and tubes. The traditional way
of deciding how to position them is to cut out pieces of paper of the same
size as the components and shuffle them around on a piece of graph paper. Alternatively,
the lumps themselves can be arranged and glanced at for a few days until the
best layout presents itself.
Even better, components can be shuffled around and a chassis designed using
an engineering drawing package on a computer, with the enormous bonus that
a template of the layout can be printed with all the fixing holes precisely
positioned, saving errors in marking out. Although it takes time to draw a
tube (valve) holder or a transformer precisely, it has only to be done once
and you will quickly build up a library of mechanical parts. In consequence,
the author has almost forgotten how to perform traditional marking out using
a scriber, ruler, and square.
It is vital to make the chassis large enough! This point cannot be emphasized
too strongly. Achieving neat construction on a cramped chassis requires a great
deal more skill and patience than on a spacious chassis. There are many considerations
that must be taken into account, so it is vital that this stage is not rushed.
Each of the following design considerations might not make a great difference
in itself, but the sum of their effects is the difference between a winner
and an ''also ran''.
Electromagnetic induction
Almost all of the larger components either radiate a magnetic field or are
sensitive to one. Not all of a transformer's primary flux reach the secondary.
Leakage flux can induce currents into wires such as tube (valve) grids. Whether,
or not, these currents are significant depends on the signal level and source
impedance at that point, so output tubes are less of a problem than the input
stage.
Coupling between wound components Wound components such as transformers and
chokes can easily couple into one another, so hum can be produced by a mains
transformer inducing current directly into an output trans former. Fortunately,
the cure is reasonably simple, and may be summarized by a simple ratio whose
value must be minimized.
induction = cos θ / d3
The angle theta and distance d are shown in the diagram (see FIG. 1).
Rotating transformer cores by 90 degr. (cos 90 degr. =0), so that the coil
of one transformer (or choke) not aligned with the other is very effective,
and typically results in an immediate 25 dB of practical improvement. Even
better, if one coil is driven from an oscillator whilst the interference developed
in the other is monitored (oscilloscope or amplifier/loudspeaker), careful
adjustment of relative angles can often gain a further 25 dB.
Because coupling decays with the cube of distance [1], as the distance between
offending items is increased, the interference falls away rapidly. However,
simply increasing the gap between two adjacent transformers from 6 to 25mm
does not materially reduce the interference, because the transformers are typically
75mm cubes, and the spacing that applies is the distance between centers, which
has only changed from 81 to 100mm, resulting in only 5.5 dB of theoretical
improvement. In practice, when the transformers are this close, coupling does
not obey the cube law very well because the transformers do not see each other
as point sources, so a 3 dB reduction, or less, is more likely.
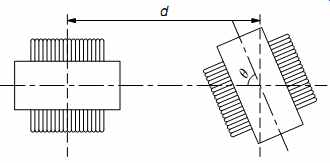
FIG. 1 Orienting transformers for minimum coupling
Although smoothing chokes are gapped, and therefore inevitably leaky, they
do not generally have an appreciable AC voltage across them. So their AC leakage
is low, and they can often be used to screen output transformers from the mains
transformer. The exception to this rule is the choke input power supply which
has a substantial AC voltage across its choke, so its leakage field is capable
of inducing currents into surrounding circuitry.
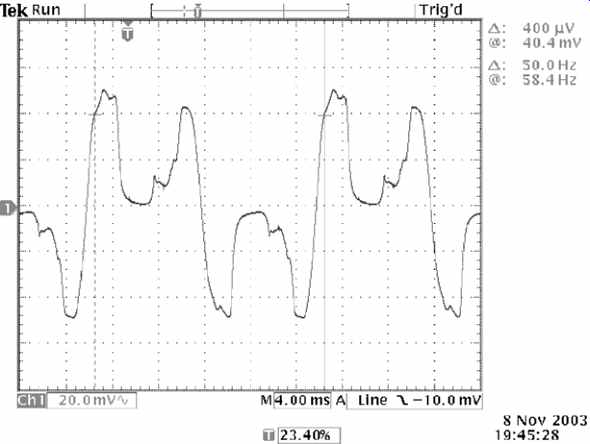
FIG. 2 Leakage flux caused by an unscreened saturating mains transformer
The core of a poorly designed mains transformer can easily be saturated by
the large current pulses drawn by a large reservoir capacitor in combination
with a semiconductor rectifier, producing a particularly noisy leakage flux,
and this can be quickly identified by a search coil (see FIG. 2).
A screening can that totally encloses a transformer significantly attenuates
the high frequency content of any leakage flux. The second guilty party is
a fifty-year-old mains transformer whose core material has deteriorated, but
this transformer is totally enclosed by a thin steel screening can. Note that
the waveform has smoothly rounded edges, indicating far less high frequency
content than the previous example (see FIG. 3).
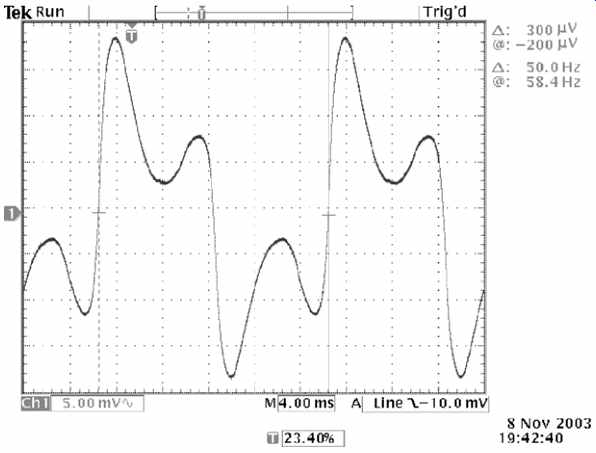
FIG. 3 Leakage flux caused by a screened saturating mains transformer
Transformers and the chassis
All transformers leak flux. The question is whether that is a problem. If
an output transformer leaks flux into the aluminum chassis of a power amplifier,
it probably isn't a problem because aluminum doesn't conduct magnetic flux.
But a mains transformer leaking flux into the steel chassis of a pre-amplifier
is a problem because the steel chassis passes the flux into sensitive signal
circuitry. Fortunately, because μ=0 for non magnetic materials, but μ>5000
for iron, even a small gap is able to prevent flux leaking into the chassis.
A 1-2mm paxolin sheet is ideal, but this may be hard to find. So a (more expensive)
alternative is the polystyrene sheet sold by model shops. (Although un-etched
FR4 PCB material would be ideal, if the copper side were to be placed in contact
with an aluminum chassis, it would electrolytically corrode it, whereas the
face-up copper would oxidize quickly and become unsightly.)
Beware that practical toroidal transformers leak flux and that mounting a
toroid directly onto a steel chassis is just asking for hum problems. However,
the danger of accidentally creating a shorted turn is even greater. Toroids
are secured by a conductive screw pulling a large conductive washer onto the
top of core to clamp the transformer tightly to the chassis. Accidentally connecting
the washer or screw to the chassis by any means other than the bottom of the
central mounting screw would form a shorted turn that could destroy a power
transformer.
Beam tubes and mains transformers
Beam tubes focus their current into thin sheets that pass largely unintercepted
between the horizontal wires of g2.This means that a vertical beam deflection
would affect g2 current, and because g2 is typically supplied from a finite
source resistance, Ohm's law ensures that this would change Vg2, thus changing
Ia. One way of deflecting electrons is with a magnetic field, such as the hum
field from a transformer. Hum due to beam deflection can be minimized by applying
Fleming's left hand rule, and ensuring that the electron beam is never at right
angles to the leakage flux from the transformer. When considering induction
between two transformers, it does not matter which transformer is rotated,
so long as the coils are at 90 degr. to one another. With beam tubes, only
one orientation is ideal with respect to a nearby mains transformer (see FIG. 4).
The tube (valve) is shown in two positions, both the same distance from the
center of the mains transformer, and both with correct beam orientation relative
to the leakage flux from the transformer. However, leakage flux tends to be
concentrated on the axis of the coil, and would also induce hum into the control
grid's circuit, whereas the alternate position has much lower flux density.
(Diagrams of this form portray higher flux density by having more lines in
a given area.)
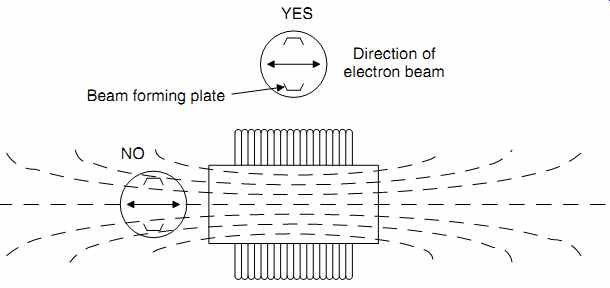
FIG. 4 Beam tubes and mains transformers
Input tubes are very sensitive to hum fields, and should be placed at the
opposite end of the chassis to the mains transformer.
In theory, output transformers should leak less because they operate at a
lower flux density (to reduce distortion). In practice, probing output transformers
and mains transformers with a small search coil failed to show the expected
difference.
The quality of the transformer seems to be the over-riding consideration,
rather than its use. Thus, a Leak TL12 + push-pull output transformer leaked
more flux than a good-quality modern output transformer in a single-ended amplifier,
despite the latter being gapped.
Although, as expected, leakage flux at 90 degr. to the coil's axis cancels
to zero, leakage at the edges of the coil can be comparable with that on axis
because the coil's outermost turn is so far away from the (flux-concentrating)
core (see FIG. 5).
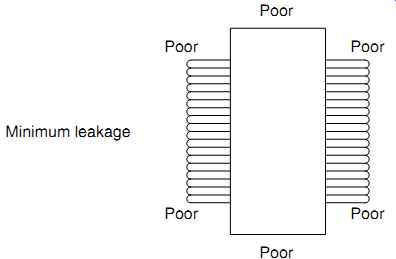
FIG. 5 Transformers leak most flux along the axis of their coils and where
the edges of their coils are furthest from the core
Heat
Heat is the enemy of electronics. Output transformers and chokes are usually
quite cool, so they can move towards the center of the chassis if necessary
(creating a mechanical problem, but we will consider this later). Mains transformers
are generally warm, and it is usually best to mount them towards the edge of
the chassis.
At best heat shortens component life and causes components to drift in value.
At worst, it causes fires. And we intend to use tubes, which are deliberately
heated.
Modes of cooling
There are three methods of transferring heat from one place to another.
Conduction is the most efficient method of heat transfer and requires a conducting
material to bond the heat source physically to its destination. An ideal conductor
would transfer the heat without any temperature drop between source and destination,
and materials having free electrons (electrical conductors) such as copper
and silver are particularly good. As an example, the body of a power transistor
must conduct the heat generated by the (very much smaller) silicon device to
an external heatsink efficiently (see FIG. 6).
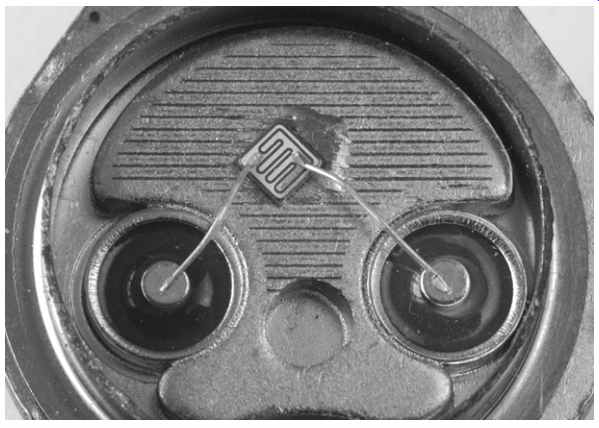 FIG. 6 The inside of a 2N3055 15 A 115W power transistor. Note the relative
size of the silicon device and its wires compared to the case.
Convection relies on the unrestricted movement of a fluid (gas or liquid)
between source and destination. Fluid is heated at the source, expands, and
is displaced by denser cooler fluid, forming a convection current which continuously
pushes hot fluid away and draws cool fluid towards the source. Convection efficiency
can be increased in two ways:
-- If a greater volume of fluid moves per second, more heat can be lost,
so a fan or pump greatly improves heat transfer. The pumped water in a water-cooled
internal combustion engine or central heating system is an example of forced
convection.
-- We choose a fluid that requires more energy for a given temperature rise.
Liquids are better than gases, and water is particularly good. However, although
some transmitter tubes have water-cooled anodes, practical pipe diameters and
pump power mean that there is a limit to the maximum flow rate, and thus the
heat that can be transferred. Even better, changing the state of a material
requires a great deal of energy, and converting water at 100 degr. C to steam
at the same temperature requires six times as much energy as heating the same
mass of water from 20 to 100 degr. C, so the largest tubes are steam cooled.
Radiation (strictly, electromagnetic radiation) does not require a physical
medium between heat source and destination, but it is the least efficient means
of transferring heat. Radiation losses are governed by Stefan's law:
E =~ &dsigma;T^4
Where:
E=power per unit area
σ =Stefan's constant=5.67x10^-8 W/K^4/m^2
T=absolute temperature= degr. C+273.16
Because heat loss is proportional to the fourth power of temperature, particularly
hot bodies, such as the Sun, can transfer heat quite effectively by radiation.
Tube (valve) cooling and positioning
Output tubes are hot, and must be allowed to cool properly.
Typical audio tubes place the anode within an evacuated glass envelope, so
the anode cannot lose heat by convection. The supporting wires from the anode
to outside connectors are quite thin, so the anode cannot lose heat by conduction.
The only remaining method of heat transfer is radiation.
Radiation obeys reciprocity, in that a good reflector is a good insulator,
so domestic kettles are shiny metal or white plastic.
Conversely, matt black absorbs well, so anodes are often blackened to allow
them to radiate more efficiently.
Although we think of glass as being optically transparent, some light is inevitably
lost in transmission. Similarly, glass is imperfectly transparent to infrared
radiation. Radiation that is not transmitted is absorbed and heats the glass.
So some of the received heat from the anode can be lost by convection if air
is allowed to flow freely past the tube (valve) envelope. Very roughly, the
envelope splits heat losses from the tube (valve) equally between convection
and radiation. Thus, efficient cooling requires that we consider how a tube
(valve) can radiate, and how easily convection currents can flow past the envelope.
Power tubes should be separated from one another by a spacing of 1 1/ 2 envelope
widths or more, otherwise they heat each other by radiation. But a useful trick
can be applied to the radiant heat received by a valve. Many tubes, particularly
small-signal tubes, have an anode with quite a narrow cross section. Received
radiant heat is proportional to the area seen at the destination, so rotating
a tube (valve) to present a narrow cross section to the source can reduce heating
from adjacent power tubes. By reciprocity, if the source also has a narrow
cross section, rotating the source to present a small area to the destination
also reduces transmission. This technique is particularly useful for circuits
such as differential pairs or phase splitters where electrical considerations
dictate that the two tubes be close together, but it can also be used to reduce
heat received from a nearby power tube (valve) (see FIG. 7).
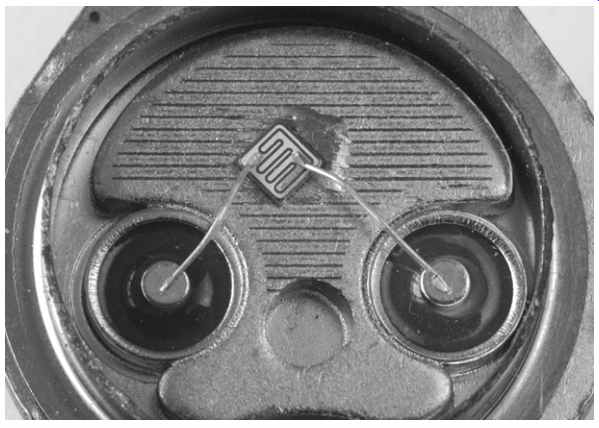
FIG. 7 Careful anode orientation allows closer spacing along the anode's
narrow axis
Placing power tubes in the middle of a chassis is not likely to be a good
idea because the chassis severely restricts convection currents. Mounting a
tube (valve) horizontally can improve convection efficiency because it exposes
the envelope to a larger cross section of cooling air. However, this could
conceivably cause a hot control grid to sag onto the nearby cathode, with disastrous
results. So check the manufacturer's full data sheet to see if there are any
strictures about mounting position. If it doesn't cause other problems, align
the socket so that the plane of the grid wires is vertical [2], preventing
them from being able to sag onto the cathode.
Early tubes have cylindrical electrodes, so viewed down their axis, electrons
strike the anode equally from all points of the compass. Since the electron
density is equal at all angles, the anode temperature is also equal at all
angles. However, beam tetrodes do not have axial symmetry, and direct their
beam of electrons along a single diameter, causing the anode to heat unequally.
Bearing in mind that the glass envelope converts half of the radian the at
loss from the anode to convection loss from the envelope, a horizontally mounted
beam tetrode should be rotated on its axis so that the hottest parts are at
the sides, allowing them to be efficiently cooled by convection, rather than
at top and bottom. As an example, see GEC's recommended alignment for the KT66
[3] (see FIG. 8).
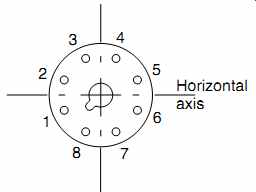
FIG. 8 GEC recommended orientation of tube (valve) base for horizontally
mounted KT66.
Because the sections of a KT66's envelope between pins 1 and 2, and 5 and
6 are the hottest, when mounting a push-pull pair of KT66 vertically, it makes
sense to ensure that pins 7 and 8 of one tube (valve) face pins 7 and 8, or
3 and 4, rather than 1 and 2, or 5 and 6.
Mounting tube (valve) sockets on perforated sheet greatly assists cooling
by allowing a convection current to flow past the valve, but as the hole area
of such sheet is typically only _40%, it is still not perfect. If better cooling
is needed, the tube (valve) socket can be centrally mounted on a wire fan guard,
and if even that isn't sufficient to keep the envelope temperature below the
manufacturer's specified maximum, a low-noise fan can be mounted on pillars
underneath the chassis using the same screws that secure the fan guard (see
FIG. 9).
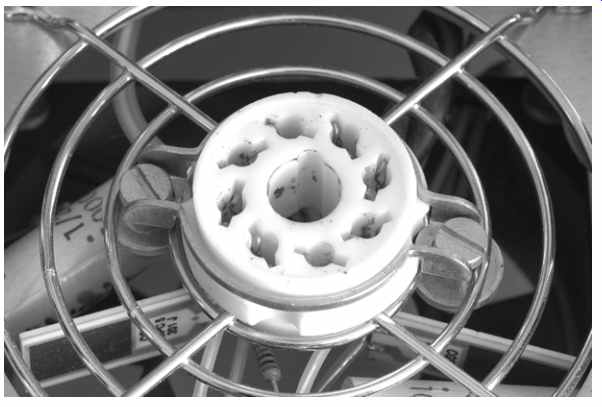
FIG. 9 With care (and large washers), a tube (valve) socket can be mounted
on a fan guard, allowing almost unrestricted airflow.
Using the chassis as a heatsink
Some small components such as power resistors and regulator ICs, unavoidably
generate significant heat. Resistors are commonly mounted on stand-offs to
allow an unimpeded air flow, and regulators are often fitted with small finned
aluminum heatsinks. Neither of these strategies is ideal because they attempt
to lose heat by convection to still air enclosed by the chassis.
Convection cooling only works if there is a free flow of cooler air past the
hot component. Once the cooling flow stops, the hot component is surrounded
by still air, which is a good insulator, and its temperature quickly rises.
Eventually, the still air begins to lose its heat by conduction to the surrounding
chassis, and an equilibrium results with a high internal air temperature and
a hot component.
A high air temperature within the chassis is undesirable because:
-- The components causing the high air temperature are unnecessarily hot,
and even though they may have been designed to withstand heat, their working
life is inevitably reduced.
-- Electrolytic capacitors are extremely sensitive to heat, and a very rough
rule of thumb is that their working life halves for each 10 degr. C rise in
temperature. Capacitor manufacturers' data sheets include extremely useful
charts that allow lifetime pre dictions to be made from ambient temperature
and capacitor ripple current, so it is well worth looking up the full data
sheet for your particular capacitor at the manufacturer's website.
-- Components having a critical value, such as in equalization or biasing
networks will drift away from their optimum value as a consequence of heating
from the air.
Ultimately, we can only lose heat to the surrounding air, and the larger the
surface presented to the air, the more efficiently it will cool. This means
that the best way to cool components is to ensure that they are thermally bonded
to the chassis, using a thin smear of heatsink compound.
Heatsink compound is not a particularly good conductor of heat, but it is
far better than air. The purpose of heatsink compound is to fill the tiny insulating
air gaps that result from placing two imperfectly smooth surfaces together.
Too much compound worsens cooling. Most people (and this includes manufacturers)
use too much. A thin, even smear applied to both mating surfaces is all that
is required. Beware that the screws bonding the bracket to the chassis can
loosen at operational temperature. So check them for tightness when fully warmed-up,
otherwise the compromised thermal bond can cause the semiconductors to be hotter
than expected, and worse, the erratic bond can cause drift.
A useful secondary advantage of mounting aluminum-clad or TO-220 resistors
directly onto the chassis is that they provide convenient mounting tags for
other components. It may seem unnerving to touch a chassis with hotspots due
to local heat sinking, but this technique minimizes the internal air tempera
ture, and thus minimizes the heating of sensitive components.
Efficient convection requires a free flow of cool air to replace hot air.
Although most designers recognize the importance of allowing adequate ventilation
by providing holes in the top of a chassis near hot components, air must also
be free to enter the chassis from the bottom if an efficient convection current
is to flow. Thus, the ideal solution is to make the entire underside of the
chassis from perforated steel or aluminum, and support it on feet _20mm high
(to allow air to flow into the underside of the chassis) (see FIG. 10).
If necessary, individual components can be cooled even more efficiently by
bonding them directly to a finned heatsink fitted to the outside of the chassis,
as is common with transistor amplifiers. Although this technique most obviously
springs to mind when considering large power amplifiers or power sup plies,
precision pre-amplifiers should have their internal temperature rise minimized
in order to prevent equalization networks drifting in value, so it could be
worth bonding anode load resistors to an external heatsink.
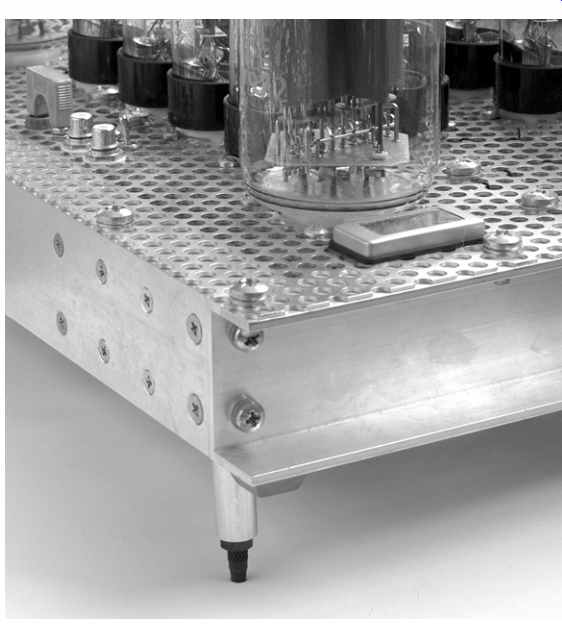
FIG. 10 Perforated sheet and tall feet allow excellent cooling
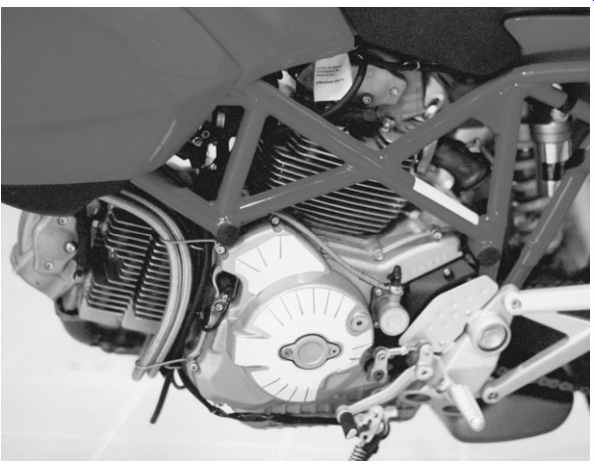
FIG. 11 Ducati Monster has barrels with fins aligned in the direction
of air flow
When finned heatsinks are used, it is most important to orient them correctly.
Heatsink manufacturers specify thermal resistance ( degr. C/W) with the fins
vertical in free air because this maximizes the surface area available to the
natural cooling convection current flowing up the fins. Despite this, the author
has lost count of the number of commercial amplifiers having horizontal heat
sinks. Heatsinks cost money, so why degrade their performance? The prettiest
example that the author can find of the importance of the correct fin direction
is a motorcycle (see FIG. 11).
The engine is a V-twin. The pistons are identical and run in barrels that
are detachable from the crankcase. Despite the increased production cost, the
two barrels are different, one having longitudinal fins, the other latitudinal,
and this is done solely to optimize cooling. Your amplifier's fins do not have
a forced 100mph horizontal convection current, so they need to be vertical.
Cold tube (valve) heater surge current
The resistance of a conductor such as a tube (valve) heater filament changes
significantly with temperature in accordance with the following equation:
Rt = R0 (1 + alpha t)
Where:
R0 =cold resistance
Rt =resistance at temperature t
alpha=thermal coefficient of electrical conductivity (0.0045 per degr. C for
pure tungsten)
t=temperature change
Normally the temperature rise of conductors in electronics is too small for
the effect to be noticeable, but a thoriated tungsten filament operates at
~ 1975K, so that at an ambient temperature of 20 degr. C (293K), its resistance
is much lower, and theory predicts that it very briefly draws 8.6 times the
operating current. In practice, the surge current is limited by the current
capability of the supply, perhaps to only half the predicted value.
Indirectly heated tubes operate their filaments at ~1650K, resulting in a
theoretical surge current of ~7 times the operating current, although measurements
suggest that a ratio of ~5:1 is more appropriate. More significantly, the thermal
inertia of the cathode sleeve slows heating, so the surge current lasts for
a few seconds, and could be sufficient to blow a poorly chosen mains fuse.
Further, it would not be prudent to use heater wiring of a rating only just
sufficient to cope with the steady-state current if long-term reliability were
required.
Wire ratings
Wires have resistance, so passing a current causes self-heating (P=I^2 R).
If the wire becomes too hot, the insulation may catch fire, so it is important
to ensure that the wiring is rated appropriately for the current to be passed.
This means that wire current ratings are determined by ambient temperature,
ability to cool, and the temperature rating of the insulator. As a very rough
guide to wires having PVC insulation:
Conductor diameter (mm) | Maximum current (A)
- 0.6 | 1.5
- 1.0 | 3.0
- 1.7 | 4.5
- 2.0 | 6.0
Component catalogues are good sources of information on the suitability of
a particular wire.
High-temperature insulators (such as PTFE) allow a higher current rating than
might be expected from a given conductor diameter, but the penalty is higher
resistance, so voltage drops along that wire will be proportionately higher,
and this can become significant in the capacitor/rectifier/transformer loop
of a power supply.
Arcing and insulation breakdown should not be a problem at the voltages found
within most tube (valve) amplifiers, but it is still advisable to maintain
2-3mm separation between conductors with a high voltage between them, unless
each conductor is insulated. As an example, hardwiring with bare wire touching
the surface of a capacitor with wound polypropylene tape insulation is not
advised, but a sleeved wire touching the same capacitor would be unlikely to
constitute a safety hazard.
Unwanted voltage drops
All wires have resistance which is proportional to their length, and inversely
proportional to their cross-sectional area.
Although the currents in tube (valve) circuitry are typically quite low, making
the voltage drops proportionately low, once we consider that we want a signal
to noise ratio of >90 dB, the voltage drops caused by small resistances
become significant.
The highest currents, and therefore highest voltage drops occur in the loop
from transformer via rectifier to reservoir capacitor and back again. A capacitor
input filter draws pulses of current at twice mains frequency from the transformer
that are typically four to six times greater than the DC load current. It is
essential that the wires carrying these pulses are as low resistance, and therefore,
as short as possible, which means that the rectifier and associated reservoir
capacitor should be close to its mains transformer. It's the same logic that
puts the battery in a car's engine compartment. (The original Mini was intended
to be rear wheel drive from a 500 cc longitudinally mounted engine, but this
proved to be underpowered, so the only way to fit a larger engine was to mount
it transversely, but that left insufficient room for the battery, forcing it
into the boot, requiring a long, very thick wire to the starter motor.) When
an output stage enters Class B, it draws current pulses at twice the audio
signal's frequency from the power supply. To prevent these pulses breaking
into driver circuitry and increasing distortion, the loop from audio load to
reservoir capacitor should be made as small as possible. This means that output
transformers should be close to their HT capacitor.
The potential effects of unwanted voltage drops usually deter mine the 0V
signal ground scheme, often known colloquially as grounding or grounding. There
are fundamentally two methods of dealing with grounding:
-- ''Earth follows signal'': The 0V signal ground wire follows the path of
the signal. In order to minimize unwanted voltage drops along this (necessarily
long) wire, it has a large cross-section so this brute force strategy leads
to 1.6mm (16 swg) tinned copper bus-bars.
-- Star ground: All connections to the 0V signal ground are made at a single
point. Because the distance between individual connections is so small, the
impedance is small, so unwanted voltage drops are also small.
The significance of these two wiring schemes is that the choice between them
needs to be made at a very early stage. ''Earth follows signal'' tends to produce
long slim mechanical layouts, whereas an ideally implemented star ground tends
to produce square or even circular layouts centered about the star ground.
The significance of unwanted voltage drops is so great that it dominates the
gross mechanical layout of an example later in this section, whilst detailed
electrical implications will be covered in Section 3.
More powerful amplifiers are heavier, and in an effort to split the weight
into two manageable chassis, you might consider having a remote power supply,
necessitating an umbilical cable to connect between the chassis. Beware that
the heater wiring linking the two chassis needs to be of a much higher current
rating than normal in order to reduce the unwanted voltage drop over this increased
distance, possibly necessitating an umbilical connector with a larger diameter
cable entry.
Electrostatic induction
Electrostatic coupling is capacitive coupling. Minimizing the capacitance
between two circuits minimizes the interference.
Remembering the equation for the parallel plate capacitor:
C = Ae0er / d
Where:
A =area of plates
d =distance between plates
e0 =permittivity of free space ~8.854x10^-12
er =relative permittivity of dielectric between the plates
We should aim to attack all parts of this equation to minimize capacitance.
Reducing plate area means keeping wires short and crossing them at right angles,
whilst increasing plate distance means keeping parallel wires apart. In terms
of chassis layout, this means that the output tubes should be reasonably close
to the output transformer and the driver circuitry should be reasonably close
to the output tubes.
In a high-impedance circuit such as a constant current sink, a chassis-mounted
transistor causes a conflict between thermal and electrostatic considerations
because the collector is invariably connected to the transistor case. Screwing
a TO-126 transistor such as an MJE340 to an grounded chassis using an insulating
kit adds ~6 pF shunt capacitance, completely negating any efforts we may have
made in designing a wide-bandwidth constant current sink. In this instance,
we are forced to compromise our thermal considerations and lose heat directly
to the air within the chassis using a small finned heatsink.
Fortunately, capacitance to chassis from aluminum-clad or transistor-style
resistors used as anode or cathode loads is not a problem at audio frequencies.
Because one end of the resistor is at AC ground, but the capacitance is distributed
along the resistor, the total capacitance to ground is effectively halved, and
because the impedances are lower than in a constant current sink, the stray
capacitance becomes insignificant.
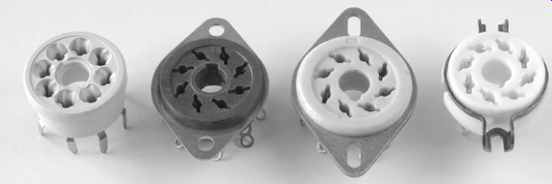
FIG. 12 Octal sockets. Note that the chassis-mount types all have different
mounting centers
Tube (valve) sockets
There is a variety of different types of tube (valve) socket available for
a given tube (valve) type (see FIG. 12).
All three of the chassis-mounting International Octal sockets in the photograph
have different spacings for their securing screws, so it is vital to make a
firm decision about which socket type is to be used, and whether the circuit
is to be hard-wired or PCB. One point that may be worth considering when choosing
Octal sockets is that NOS McMurdo phenolic sockets have the same hole spacings
as Loctal sockets, allowing an easy change from 6SN7 to 7N7 at a later date.
Another consideration is positioning of heater wiring. Taking the B9A base
as an example, most tubes using this base have their heaters connected between
pins 4 and 5, although heating the popular ECC83/12AX7 from 6.3V requires a
link between pins 4 and 5, and the other heater wire must be taken across the
center of the socket to pin 9. McMurdo B9A tube (valve) sockets were designed
to that if the axis of the socket was aligned at 45 degr. to the edge of the
chassis, pins 4 and 5 were closest to the chassis edge, minimizing hum from
heater wiring (see FIG. 13).
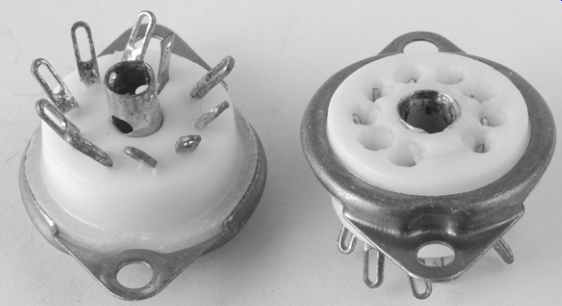
FIG. 13 McMurdo B9A sockets position the heater pins (4, 5) close to the
edge of the chassis provided that the mounting holes are at a 45 degr. angle
to the edge
Traditional tube (valve) amplifiers always had tube (valve) sockets aligned
so that their heater pins were closest to the chassis edge, thus minimizing
the length of exposed heater wiring . . .
How electrostatic screening works Electrostatic screening works by placing
an grounded conductive barrier between the source of interference and the sensitive
circuit (see FIG. 14).
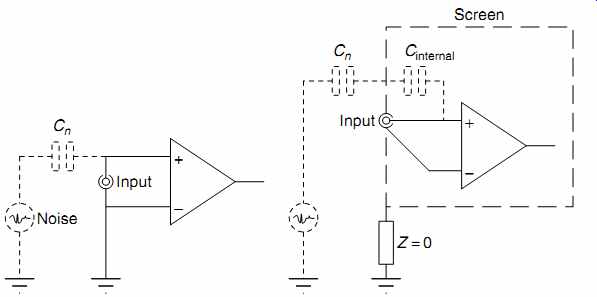
FIG. 14 Screening breaks one capacitance into two, center-tapped by an
ground
As can be seen from the diagram, the screen diverts noise currents from the
source to ground. If there is any impedance between the screen and RF ground,
the noise current can develop a noise voltage across it, causing the screen
to induce noise into its enclosed (sensitive) circuitry.
Alternatively, the impedance from the screen to RF ground can be considered
to be the lower leg of a potential divider, and the capacitance from screen
to noise source the upper leg. The lower leg could be a length of conductor,
which has inductance, thus forming a 12 dB/octave filter in conjunction with
the capacitor. To maximize the effect of screening, the screen must have a
low-resistance, low-inductance path to chassis.
When resistances and inductances are connected in parallel, the total value
falls, so the screen should ideally contact the chassis at multiple points
to minimize impedance and maximize screening. This is why RF designers cut
the flanges of the lids containing their circuitry - it ensures that each finger
firmly contacts the case, and minimizes impedance at RF (see FIG. 15).

FIG. 15 Lids with fingers allow multiple low resistance, low inductance
contacts
From an audio point of view, screening cans should be firmly screwed to the
chassis at multiple points using shakeproof washers to ensure a gas-tight connection
that does not deteriorate over the years. Pre-amplifiers using choke interstage
smoothing should ideally use oil-filled chokes, not because the oil confers
any advantage, but because the metal can needed to contain the oil provides
electrostatic screening.
Tubes that are sensitive to electrostatic hum can be enclosed by an grounded
metal screening can. Tube (valve) screening cans are not created equal. Perfect
screening would enclose the tube (valve) completely, but that would prevent
heat from escaping, making the tube (valve) significantly hotter, and reducing
its life [2]. It is easy to raise a valve's temperature, but lowering it is
much harder.
Screening cans are therefore a compromise between screening and cooling (see
FIG. 16).
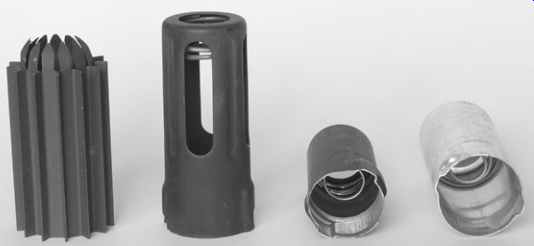
FIG. 16 Selection of tube (valve) screening cans
cont>>
|