<<prev.
A pre-amplifier example
When the RIAA pre-amplifier is selected, one channel is very low level and
distorted. Bear in mind that the cartridge or associated pick-up arm wiring
could have failed. One obvious test is to set your DVM to its resistance range
and check continuity from tip to sleeve of each phono plug, but this is not
a good idea.
Momentarily passing DC through a moving magnet cartridge is likely to magnetize
its core permanently and increase distortion. A far better solution is simply
to swap the phono plugs over and see if the fault swaps channels. If it does,
the fault is in the arm or cartridge, if it doesn't, the fault is in the pre-amplifier.
If, like the author, you have chosen to use a DIN plug as your connection
from pick-up arm to pre-amplifier, you can't easily do this swap (although
you could make up a short adaptor lead for swapping channels). There are other
ways of testing each channel of the pre-amplifier:
-- Tap the input tube of each channel gently and listen to each loudspeaker.
Since tubes are invariably slightly microphonic, the thump/ting should be equally
loud from each loudspeaker.
-- Turn up the volume fully, and listen for hiss on each channel.
If one channel is significantly quieter than the other, it suggests that the
signal from the first stage is not being amplified. The noise should be a clean
hiss. Uneven noise suggests a faulty connection.
-- With the volume turned fairly well down, put your finger on each input
of the amplifier. This should cause a loud hum. (If you do this test at the
cartridge pins, beware that the loud hum doesn't make you jump and hit the
stylus.) Having established that the pre-amplifier is genuinely at fault, we
know that it is very unlikely to be the LT or HT power supplies (unless built
as dual mono) because one channel works, so it's time to look at a circuit
diagram (see FIG. 4).
Looking at the circuit, we see that there is a lot of fragile silicon (is
there any other kind?).We ought to first work out what the circuit is doing.
The first stage is pretty conventional, although the LED bias in the cathode
is a useful indicator that shows whether the stage is passing HT current. The
first stage is followed by conventional 75 ms passive equalization, although
the 12 k resistor in series with the 270 pF capacitor indicates that 3.18 ms
has also been implemented. The second stage also has LED bias, and has a cascode
constant current load (to minimize distortion), and this is direct coupled
to a cathode follower. The cathode follower has a simple constant current load
and provides a low (and unchanging) output resistance to drive the 3180/318
ms passive equalization which is direct coupled to the output cathode follower.
The quickest way to find the fault in this circuit would be to start at the
input tube, and measure the DC voltage on the output of each tube with the
circuit fully powered. We should be careful not to slip with the probes and
create extra faults! The input tube is a conventional common cathode, so even
if we didn't know that the design voltage is 126V, we could check to see that
it is somewhere between 1/3 HT and 2/3 HT. When faultfinding, we really don't
quibble about precise voltages, we look for things to be ''roughly right''
or clearly wrong.
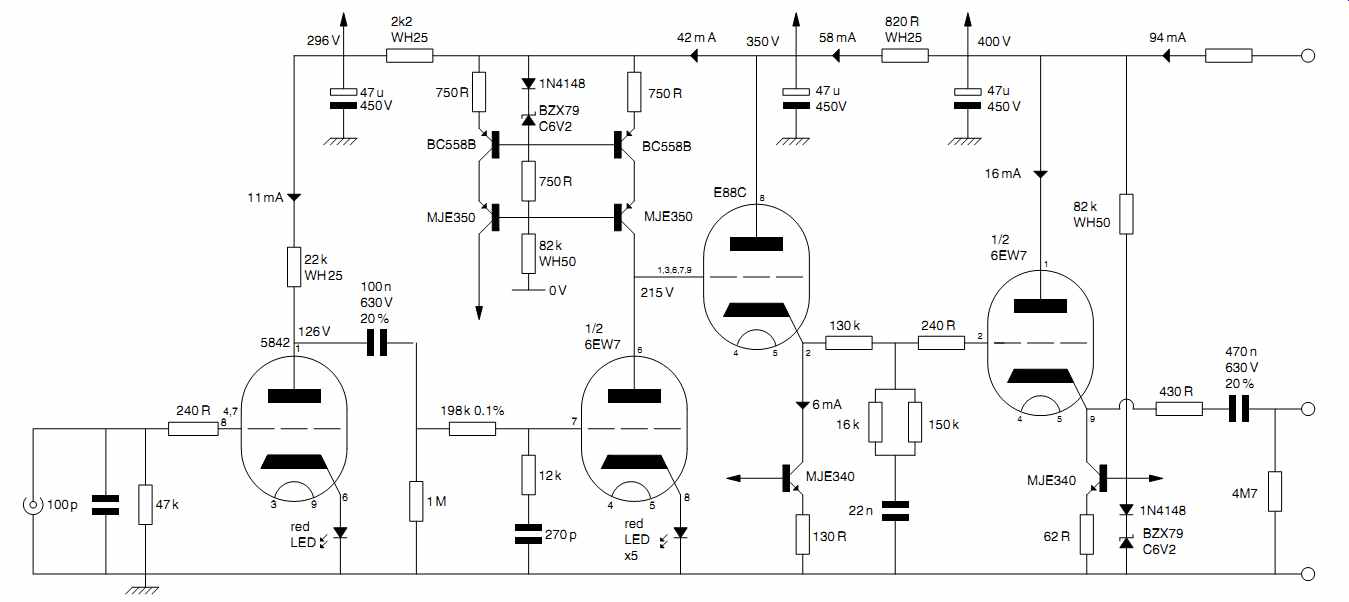
FIG. 4 RIAA stage with active loads.
Although the anode circuit of the second stage looks complex, we can ignore
the silicon for the moment, and just check the anode voltage using the same
1/3 HT to 2/3 HT criterion. Because it's so very easy to slip with a DVM probe,
it's safer to measure the anode voltage on the tube socket rather than on the
collector of the MJE350 (where you could slip and short to either of the adjacent
pins). Because the third stage is a cathode follower, its output is on its
cathode, and for any cathode follower DC coupled from the preceding anode,
its cathode should be a few volts higher than that anode voltage. The fourth
stage is also a DC-coupled cathode follower, so its voltage should be a few
volts higher than the voltage at the cathode of the preceding cathode follower.
Perhaps when we measure, we find that the anode of the second tube is at 30V.
This is too low and indicates a fault. We also notice that the LEDs in the
cathode circuit aren't glowing, and this suggests that the tube is not drawing
any significant current. It looks as though we need to investigate the silicon.
If the tube is not drawing current, the fault is far more likely to be in
the constant current load, so we need to check that the constant current load
is being told to do the right thing.
When working with transistors, we generally make the sweeping assumption that
the base draws zero current. This assumption hugely simplifies faultfinding
because it means that we can predict the voltages looking down the bias chain
formed by the 1N4148 diode, BZX79 C6V2 Zener diode, 750-ohm resistor and 82
kOhm wire wound resistor. Because the wirewound resistor is nice and big, it
is easy to touch with the DVM's probe. Together, we would expect the two diodes
to drop 6.9V,and in comparison with the 82kOhm, the 750Ohm won't drop much,
so we should expect the voltage across the 82 k-ohm resistor to be about 10V
less than the HT.
Having measured the drop across the 82 k-ohm resistor, and found that it looks
roughly correct, that suggests that the bias chain is correct. We now need
to check the transistors. The easiest way to check a transistor is to check
the voltage drop across its base-emitter junction, which should be ~0.7V. It's
very tricky to connect two probes directly to a transistor safely, so we find
other, larger, points that are connected to the base and emitter to check the
transistors. They turn out to be correct, so we deduce that the 750 Ohm current
programming resistor has failed open circuit. Just to be certain, we switch
the power off, leaving a meter monitoring the HT, and use a DVM that is guaranteed
not to switch diodes on, to measure the 750-ohm resistor before removing and
replacing it. Unfortunately, when we measure, we find that the 750-ohm resistor
is innocent.
Despite having confidently predicted that the silicon circuitry would be at
fault, it seems that it is not faulty. If it isn't faulty, then it must be
sourcing a current down to 0V, and if the current isn't going through the tube,
it must be going some where else. The next check we could make is to measure
the voltage across the 750 Ohm current programming resistor.
Between them, the Zener and 1N4148 diodes drop 6.9V and this voltage is across
the base-emitter junction of the transistor plus 750-ohm resistor. The base-emitter
junction drops 0.7V, so we should expect to see 6.2V across the 750-ohm resistor,
exactly the same as the Zener voltage. We measure the drop and it is correct.
There's no longer any doubt about it, the constant current load is working
correctly, and is delivering 6.2V/ 750-Ohm=8.27mA; it's just not going where
it should.
We now need to look very carefully, perhaps with a magnifying glass and very
bright torch to see if there are any whiskers of wire lurking on the second
tube's socket, and because it is DC coupled to the third tube, we need to check
that too. Cleaning the bases with a stiff brush whilst vacuuming is often a
good idea. Unfortunately, even this doesn't clear the fault.
Power transistors have their collectors connected to their case, so when we
bolt them to a heatsink, we have to use an insulating kit. The MJE350 dissipates
1.1W, which is a little more than it can comfortably dissipate without a heatsink,
so it was screwed to the chassis. (This is not ideal because it adds ~6pF to
the output capacitance of the constant current source.) We unscrew the transistor,
lift it clear, and apply power for just long enough to see the five LEDs light
up and the anode voltage of the second stage rise to 180V. The insulating washer
was faulty! Although it is satisfying to find the fault, we must think a little
further. What caused the fault? Did it fall or was it pushed? There's no point
in replacing a component only to have it fail again three months later. We
need to know what caused the failure. The insulating washer might have been
of faulty manufacture, but the far more likely reason is that it has been pulled
against a hole that was not deburred fully. Check the hole on the chassis and
the transistor very carefully. Do not re-use the fixing screw - it might have
had a sharp burr that damaged the washer.
Unusually, because of the capacitance problem, the best repair would be to
fit a small heatsink to the transistor and lose the heat to the air, rather
than to the chassis.
These two examples demonstrated that a little thought at the scene of the
crime can take you to the guilty component, and that no special test equipment
is needed other than a willingness to observe clues and think about what they
are telling you.
The second example, in particular, demonstrates that we need to think about
currents and where they flow. Current doesn't just flow into somewhere and
disappear -- if it did, there would be untidy heaps of electrons everywhere.
AC conditions
Occasionally, testing DC conditions will not reveal the fault.
An oscilloscope to probe around and trace the signal is the obvious approach,
but even if you don't have an oscilloscope, the inherent microphony in tubes
can be useful. Valves can be thumped gently with a screwdriver handle whilst
listening to a ''disposable'' loudspeaker on the output. When the ''ting''
stops dead, the area of the fault has been found and components can be replaced
or tested until the fault is found.
Diagnosing and eliminating hum
There are various ways that hum can find its way into an amplifier:
-- Directly injected from the HT supply
-- From heater wiring
-- Electrostatic pick-up
-- Electromagnetic pick-up
-- Hum loop.
Assuming that hum has been discovered, there are quick checks that can be
made before dragging out the oscilloscope. Does the hum disappear the instant
that you switch the amplifier off, or does it gently fade away? If it disappears
instantly, it could be electromagnetic pick-up from the amplifier's mains transformer,
or power supply hum - either from the heaters or the HT supply.
If it gently fades away, the hum is at the input of the amplifier and could
be electrostatic pick-up (poor screening), a hum loop, or it could already
be present on the signal entering the amplifier.
Does the volume control affect how loud the hum is? If it does, then the hum
is before the volume control. Is the hum only present when one particular input
is selected? If so, unplug that input and if the hum goes away, you are looking
for hum on that particular source equipment. Does the hum change when you touch
the chassis or a lead? If so, you have electrostatic pick-up due to a failed
ground connection. Does the hum change when you move a lead? Leads might be
screened, but if you have a moving coil cartridge, and trail pick-up arm leads
across a mains transformer, you can expect electromagnetic pick-up. Is the
hum dependent on which pieces of equipment are plugged into the mains? If so,
this suggests a hum loop. Unplug all the audio and mains leads, and for each
piece of equipment, check continuity (<0.5 Ohm) between the ground pin of
the mains plug and the body of its phono sockets.
In the unlikely event that two pieces of equipment have continuity between
mains ground and signal ground, you have a hum loop, and it may be necessary
to break the bond between the chassis and 0V signal ground within a piece of
equipment.
Assuming that you have pinned the hum problem down to one piece of equipment,
it is now time to switch on the oscilloscope.
Trigger the oscilloscope from ''line'' so that the oscilloscope is always
triggered when you poke around looking for hum, then touch the probe tip with
your finger to check that the oscilloscope genuinely is triggered, and that
it is ready and able to detect hum (see FIG. 5).
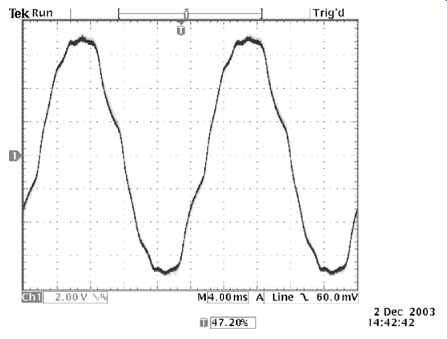
FIG. 5 Typical hum waveform obtained by touching probe tip with finger.
A power amplifier example
Since the patient is a power amplifier, the oscilloscope may be able to show
the hum at the output, so it's worth looking, because the type of hum gives
a clue as to its origin. Bear in mind whilst investigating that you are unlikely
to find squeaky clean waveforms, they will always be messy - either covered
in noise or distorted. If you find something approximating to a sawtooth waveform
at the output of the amplifier, you have HT supply hum from somewhere near
the reservoir capacitor, and it's likely that the hum is being injected directly
into the output stage. The next step is to look for hum on the HT supply, but
this needs to be done very carefully.
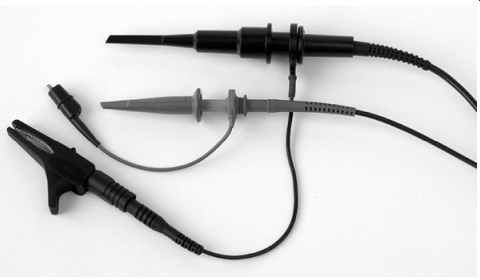
FIG. 6 High-voltage probes tend to be bulkier than normal ones.
Switching the input coupling of the oscilloscope to AC will reject the DC,
allowing the sensitivity of the oscilloscope to be increased until the hum
is clearly visible, but the full HT is still being applied to the probe. Typical
_10 probes can only withstand 200V, and the HT at a power amplifier output
stage is likely to be >300 V. In addition to your _10 probes, you also need
a _100 probe that is rated for high voltages. Bought new, high-voltage oscilloscope
probes are expensive, but you may well be able to find a second hand probe
for a much more reasonable price. If you're looking through a box of old probes,
remember that high-voltage probes tend to be rather bulkier than normal probes
(see FIG. 6).
Assuming that you have a safe means of looking at the HT feeding the output
transformer, <1Vpk-pk is an acceptable ripple amplitude for a push-pull
amplifier, but a single-ended output stage is unable to reject power supply
ripple, so <30mVpk-pk ripple is preferable. These rough guides are appropriate
for conventional loudspeakers, but high-efficiency loudspeakers such as horns
are less tolerant, so <100mVpk_pk (PP) and <3mVpk-pk (SE) might be more
appropriate. The Quad II has a trap for the unwary in that it has substantial
ripple (typically >60Vpk-pk) at the HT feeding the output transformer, but
smooths the HT to the screen grids and relies on tetrode action to reject ripple
at the anodes.
Assuming that there is excessive ripple on the HT feeding the output stage,
something must be done about it. If it is a new fault on an old amplifier,
then an electrolytic capacitor has probably dried out, and it must be replaced
by another of similar value and the same, or higher, voltage rating. If it
is a new amplifier, a component fault is unlikely, and the design needs to
be changed, perhaps by adding a stage of LC smoothing.
A tube microphone example
It's not unusual for hum to come from a variety of sources.
Condenser microphones require an amplifier just behind the capsule that not
only has high input impedance, but amplifies a very small signal, so eliminating
hum is quite a problem. A forty-year-old tube microphone had hum, and although
replacing connectors/cables and attending to ground bonds substantially reduced
the hum, it did not eliminate it, so attention turned to the HT supply (see
FIG. 7).
The supply is a conventional bridge rectifier feeding a reservoir capacitor
followed by resistor/capacitor smoothing and a neon regulator tube. When the
hum at the reservoir capacitor was investigated, instead of it being an even
sawtooth, it had alternating large and small teeth, suggesting that one path
of the bridge rectifier was less able to charge the capacitor than the other
(see FIG. 8).
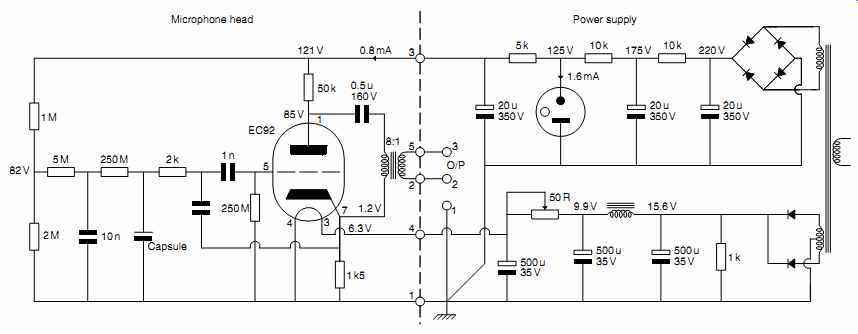
FIG. 7 The power supply for this tube microphone employs extensive filtering
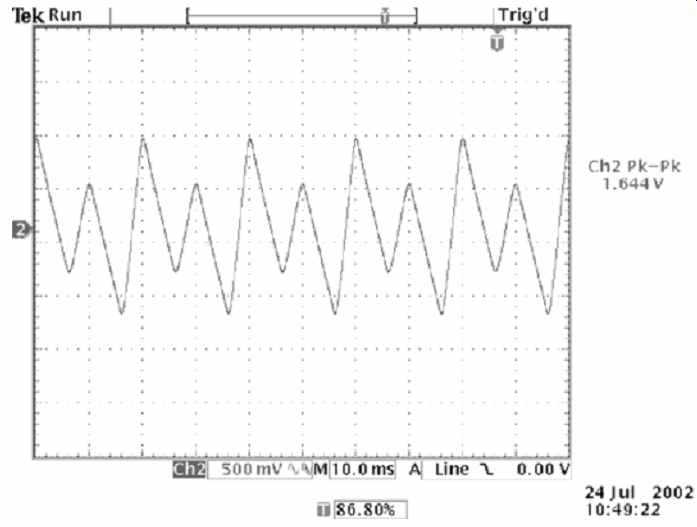
FIG. 8 The unequal sized teeth on this reservoir capacitor ripple waveform were caused by faulty rectification
Replacing the bridge rectifier would restore an even sawtooth, but would only
make a very minor difference to the hum. The hum on the next capacitor down
the chain was investigated.
The hum on this capacitor should have been an almost pure 100Hz sine wave,
yet noise and spikes were present. The capacitor was simply not doing its job
(see FIG. 9).
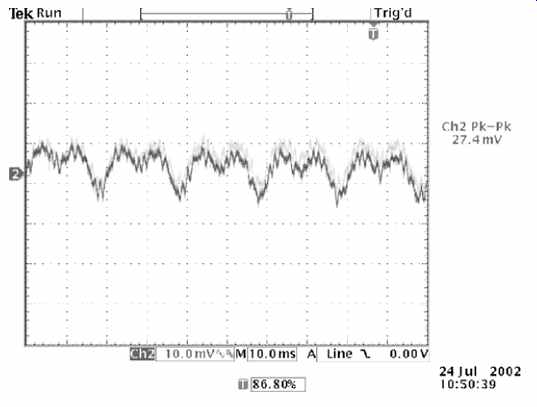
FIG. 9 The hum on this capacitor ought to be almost pure 100Hz, without noise spikes
Given that the power supply was forty years old, it seemed likely that if
one electrolytic capacitor was faulty, then they all were, and if they weren't,
then they soon would be. Replacing the bridge rectifier and all the capacitors made sense.
However, the nastiest fault came to light as the power supply was being gutted
of its (chassis mounting) capacitors. Instead of having positive and negative
solder tags, each capacitor had a single positive solder tag, and the negative
connection was made simply by pressing the aluminum can onto the chassis. Because
there wasn't a star washer between the can and the chassis, the mechanical
joint was not gas-tight and gradually increased in resistance over the years,
so part of the hum was due to this increased resistance. This is a very poor
construction technique, and should be replaced on sight (see FIG. 10).
Modern capacitors are so much smaller that the entire replacement circuit
was built on a small piece of strip board, and this cured the hum. Moral: Sometimes
there are so many small faults that nothing less than a comprehensive rebuild
can effect a full cure.
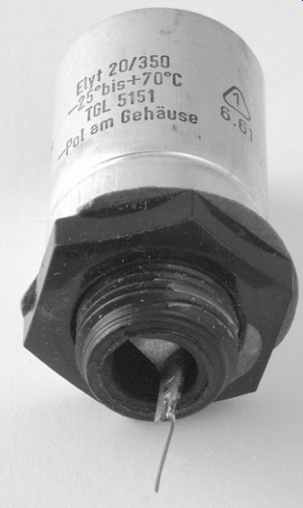
FIG. 10 This capacitor could not make a durable low-resistance negative connection simply by contacting the chassis!
Oscillation
There are various causes of oscillation, and each tends to produce characteristic frequencies:
-- Incorrect polarity of global feedback in power amplifiers tends to produce a loud shriek of oscillation.
-- Excessive global feedback around a power amplifier with poor compensation
or poor output transformers tends to occur between 30 and 300 kHz.
-- Oscillation in individual stages tends to be at radio frequencies, and
could be anywhere between 100 kHz and 100MHz.
-- Motorboating is due to feedback around a number of stages via the common
power supply, and tends to occur at 1Hz.
Global feedback and power oscillators The simplest fault is that a new amplifier
has been built, but when the global negative feedback loop is connected, the
amplifier turns into an oscillator. If, as is usual, the negative loudspeaker
terminal of the amplifier is connected to 0V, then an amplifier with series
applied negative feedback forces the other terminal to become the non-inverted
output. This means that in order to maintain correct polarity, oscillation
in a push-pull amplifier is most easily cured by swapping the signals to the
output tubes at the output from the driver stage (see FIG. 11).
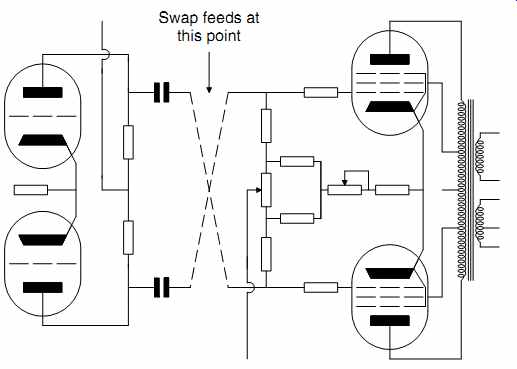
FIG. 11 Correcting polarity in a push-pull amplifier is most easily done
by swapping over feeds at the output of the driver.
Oscillation caused by incorrect polarity of global feedback is slightly more
awkward to cure in single-ended amplifiers, so it's fortunate that they don't
often have it. Because the output transformer primary end are usually designated
anode or HT, the only cure is to swap over the secondary leads (see FIG. 12).
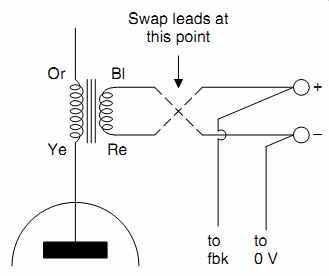
FIG. 12 Correcting polarity in a single-ended amplifier can only be done
by swapping over the output transformer secondary.
In theory, we always know the transformer phasing, and we know which way they
should be connected, so the previous problems never occur. In practice, the
author finds it quicker to wire one channel of a stereo amplifier to one configuration
and the other channel to the opposite polarity. This ensures that one channel
is wrong and one right. The incorrect channel is thus easily identified and
corrected.
Some amplifiers include an output transformer secondary in the cathode circuit
of their output tubes. Practice shows that it can be quicker simply to wire
the cathode feedback winding one way round, apply a signal from an oscillator,
and monitor the output on an oscilloscope. Then, without changing any settings,
swap the connection of the cathode feedback winding.
The connection that produces the lowest output voltage (and no HF oscillation!)
is the correct one.
Global feedback and compensation
The amount of global feedback that an amplifier will tolerate is governed
primarily by its output transformer, so a new transformer requires new compensation.
For various reasons [1] it is the interaction between the input stage and output
transformer that determines the stability of an amplifier when global feedback
is applied, so most amplifiers conform to a pattern:
-- The anode load RL is shunted by a capacitor C1 which may be in series with
a resistor R1.
-- The global feedback resistor (Rfbk) is bypassed with a capacitor C2 which
may be in series with a resistor R2.
We can therefore draw a generic diagram that shows possibilities for adjusting
compensation once Rfbk has been set to give the required gain (see FIG. 13).
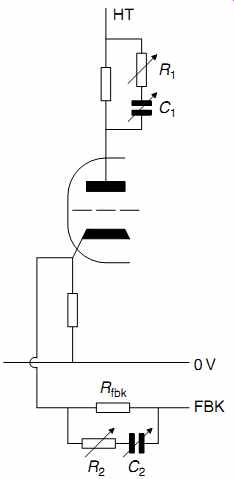
FIG. 13 Global negative feedback often requires additional compensation
components.
The way to determine the optimum values is to fit variable resistors and capacitors
in the appropriate positions, apply a 10 kHz square wave to the input of the
amplifier, monitor the output across a dummy load made from power metal film
resistors -- not wirewound resistors (which are noticeably inductive at such
low values), and adjust the compensation components until the cleanest, sharpest
square wave results. Two variable capacitors are needed, and these are best
obtained from radio fairs. Any dual-gang variable capacitor that could tune
a medium wave radio will do, because they are typically 50-500 pF (best) or
30-365 pF (smaller and slightly newer). For each variable capacitor, connect
the two sections in parallel to produce an ~80-800 pF variable capacitor (see
FIG. 14).
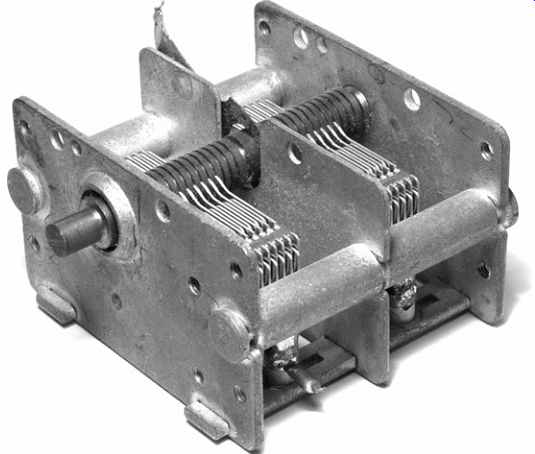
FIG. 14 A salvaged radio capacitor is ideal for determining optimum feedback
compensation
Bear in mind that C1 and R1 are connected to high voltages, so they must have
insulated knobs and be approached with extreme care.
-- The value of C2 is critical. Too little causes the amplifier to oscillate,
too much doesn't significantly lower the amplitude of the ringing, but rounds
the leading edge about which the ringing occurs.
-- R2 may need to be zero to prevent oscillation. A good starting point is
Rfbk/10.
-- The value of R1 is critical for damping the ringing - too little causes
overshoot. A good starting point is RL/10.
-- The value of C1 is not critical, but too high a value rounds the square
wave, and too little causes overshoot at the leading edge. Don't touch the
body of the capacitor while the amplifier is powered.
The quickest way to find the optimum settings is to start without C1 and R1
connected. Adjust C2 to give minimum ringing concomitant with the ringing decaying
exponentially and being superimposed on a sharp leading edge, rather than a
curving edge. (You will be relieved to learn that this condition takes less
time to identify than to describe!) Switch off the amplifier, and unplug it
from the mains, leaving the plug in clear sight. Connect C1 and R1. Apply power
to the amplifier, and adjust C1 and R1 simultaneously for minimum exponentially
decaying ringing on a sharp leading edge (be careful, these components are
connected to high voltages). A minor adjustment of C2 may be necessary.
Strive for an optimum setting of all components with a minimum setting of
C2.
When the input stage is single ended, symmetry between the positive and negative
edges can never be achieved because the tube's non-linear anode characteristics
mean that it can source current slightly better than it can sink current. However,
if the input stage is a differential pair, symmetry is possible, provided that
the compensation network is connected between the anodes (see FIG. 15).
For a differential network, start with R1 =RL/5, and use only one section
of the variable capacitor.
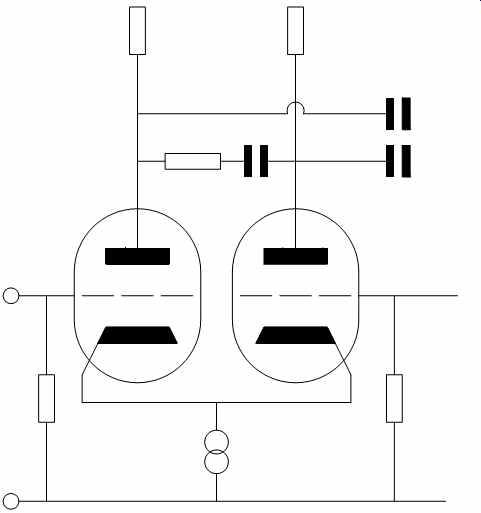
FIG. 15 A differential pair input stage should connect the compensation
components between the anodes
Having carefully set the optimum values, dab a 220 nF (or similar) capacitor
across the output of the amplifier whilst observing the 10 kHz square wave.
Note that adding the capacitor ruins your carefully optimized square wave response
- this implies two things:
-- There's no point in struggling to fit precise values of resistors and capacitors
in the compensation networks. They are a compromise. This is a good thing,
because it means that the nearest standard values in your stock will probably
do.
-- It would be a very good idea if you knew precisely what sort of a load
the amplifier was actually going to drive. And it would be even better if the
load could be made resistive at high frequencies. We will investigate how this
can be done later...
Once you have determined the optimum settings, switch the amplifier off, and
having checked that all the capacitors are discharged, use a DVM to measure
the value of the resistors, and a component bridge to measure the capacitors.
Substitute fixed components and confirm that the amplifier still works as expected.
Optimizing the compensation components doesn't take long, but the results are
worthwhile (see FIG. 16).
FIG. 16 Before and after. Before shows significant ringing. Note the slight
asymmetry in ringing between positive and negative halves of the square wave.
As an unusual commercial example, the Rogers Cadet III doesn't directly shunt
its anode load, but shunts Vgk of the second stage, which amounts to the same
thing, but avoids injecting noise from the power supply. It bypasses its global
feedback resistor with a capacitor, but sets both compensating resistors to
0 Ohm. In addition, a small amount of neutralization (positive feedback) has
been applied from one output tube's anode to the grid of its counterpart. If
the output transformer were perfectly balanced (split bobbin winding), and
the phase splitter were perfectly balanced, we would expect to see a similar
capacitor from the other anode (see FIG. 17).
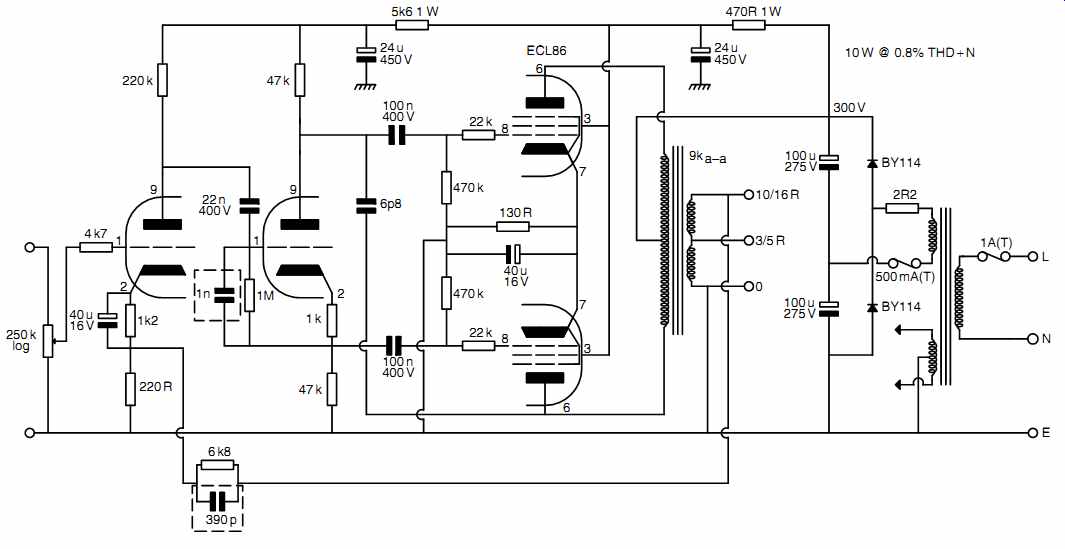
FIG. 17 Rogers Cadet III power amplifier.
Oscillation in individual stages
Cathode followers are particularly likely to oscillate, and when they do so,
it can be at a very high frequency, possibly as high as 100MHz, requiring a
good oscilloscope even to show the problem. Fortunately, cathode followers
can generally be tamed quite easily by adding a grid-stopper resistor and possibly
a cathode-stopper. The grid-stopper must be a non inductive resistor (carbon
film is ideal) soldered as close the grid pin as possible and between any other
circuitry. The value of the grid-stopper resistor must be found by experiment,
but typical values range from 1 to 22 kOhm. If needed, the purpose of a cathode-stopper
resistor is to buffer a capacitive load from the (slightly inductive) output
impedance of the cathode follower. One of the cathode follower's virtues is
its low output impedance, so it seems a shame to raise it by adding series
resistance. Fortunately, cathode-stopper resistors can usually be quite low
value, typically 47-470 Ohm. Another cause of local oscillation is poor HT
decoupling. Adding a 100 nF capacitor between the top of the anode load and
the bottom of the cathode bias resistor often helps (see FIG. 18).
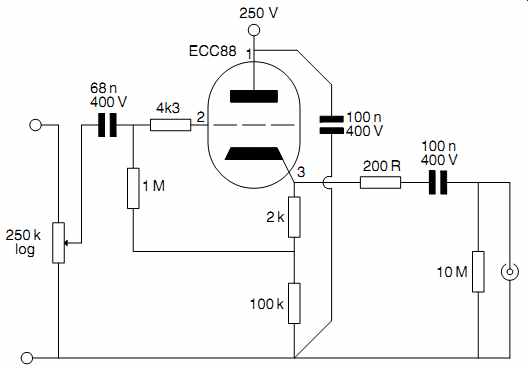
FIG. 18 Cathode followers are particularly susceptible to RF oscillation,
so this example has a grid-stopper, cathode-stopper, and local power supply
decoupling.
Common cathode stages can also oscillate, and grid-stoppers are an almost
universal panacea, but local HT decoupling might also be needed.
Stages can sometimes couple together and oscillate at RF via the heater path.
Ideally, each tube should have each heater pin decoupled to chassis (not 0V
signal ground) by a 10 n capacitor having short leads.
Motorboating
Because motorboating is a low-frequency (1Hz) oscillation due to unwanted
power supply coupling, experiment to see if increasing smoothing capacitance
at one stage changes the frequency. If you can change something, then you must
be near to the source of the fault. The best cure is to reduce the HT source
resistance. A regulator is ideal, but reducing an HT series resistor might
work. Alternatively, reducing smoothing capacitance might be acceptable, depending
on hum. If all else fails, you could resort to the traditional cure of reducing
the value of audio coupling capacitors, but this is not recommended -- why
destroy the audio design because of a power supply problem?
Noise and crackles
Noise and crackles are due to an intermittent conduction path.
The most likely cause is a dry soldered joint. Because the fault is caused
by intermittent contact, tapping joints with a plastic (insulating) pen can
be effective, an even better alternative is to poke the joint with a sharp
(insulated) probe in the manner of an unsympathetic dentist (see FIG. 19).
If the amplifier is old, the fingers in the tube socket may be making poor
contact with the tube pins, so try moving each tube gently in its socket. The
real cure is to replace the socket, but removing the tube and squirting contact
cleaner into the socket (with power off )may effect a temporary cure. Alternatively,
using a small probe to tighten the fingers may be a longer lasting solution.

FIG. 19 A sharp (insulated) probe can be useful for finding dry joints.
Although DIN plugs and sockets have a wiping action when the plug is inserted
(unlike phonos), the silver plating on the better quality connectors can corrode
when a plug or socket is left unmated. The pins in a plug can easily be recovered
by sliding the body back to expose the pins and dipping them in Goddard's Silver
Dip until they are bright and shiny. Sockets are rather harder, and it is easier
simply to replace them.
Luck also plays a part. The author spotted a bulge on the base of an electrolytic
HT capacitor and immediately knew that it should be replaced. Unfortunately,
one of the wires just wouldn't desolder and a closer inspection revealed that
the joint had never been soldered! When bought at a market, the amplifier was
described as ''works well'' - but with a production fault like that it could
never have worked well in its life, and the unsoldered joint explained the
odd crackles heard whilst testing (see FIG. 20).
FIG. 20 Not only is this electrolytic faulty (note the bulge and cracks
adjacent to the tag) but its ground wire was never soldered!
Electrolytic capacitors fail because their electrolyte evaporates, causing
poor and possibly intermittent contact to one of the capacitor plates. Old
electrolytic capacitors are best replaced en masse, rather than searching to
find the noisy offender from a bunch of equally likely suspects.
Intermittent faults
These are the worst to diagnose. They are usually mechanical, so poking around
with a sharp insulated probe can be useful.
A traditional test for a semiconductor was to heat it with a hair dryer to
produce the fault, then selectively cool parts with aerosol freezer. This is
expensive in environmentally unfriendly freezer, so this technique should only
be used as a last resort after probing or thumping with a screwdriver handle.
Squirting freezer spray near a tube is likely to crack the envelope.
Classic amplifiers: comments
The following remarks relate to the author's personal experience of a few
samples of each amplifier, but the comments are included because some guidance
is better than none. Various amplifiers, such as Radford, are not included,
not because the author has any bias against them, but simply because he has
not owned one.
As a very broad generalization, classic amplifiers using more expensive output
tubes are likely to be better. Amplifiers using KT66 may be better than EL34,
which will be more powerful than EL84, and ECL82 or ECL86 are at the bottom
of the heap. Curiously, amplifiers using KT88 may be worse than any of these,
because they may have been designed as public address amplifiers, purely for
their high output power.
The quality of output transformers is crucial. Poor output transformers will
be small for their rating, although C-core transformers may be an exception
to this rule, and are almost always a guarantee of good quality.
Quad II
There are still an awful lot of these about, and they generally require very
little work to restore them to their original performance. Typically, the 180Ohm
3W cathode resistor and its associated 25 mF capacitor need to be replaced.
Quad IIs are popular with tweakers, so there are various modifications.
Mostly the modifications replace the GZ34 with silicon to increase output
power, and others replace the GEC KT66 with EL34 because NOS GEC KT66 tubes
are fearfully expensive, although current production KT66 are said to be satisfactory.
Williamson
These were most frequently made by amateurs, so finding a matching pair is
tricky, and build quality may be less than wonderful. However, at the very
least, the output transformers are well worth salvaging. In the UK, Williamsons
used KT66, but some of the American and Australian variants used the somewhat
less linear (but much cheaper) 807.
Leak TL12 and BBC LSM/8 derivative
This amplifier has an output stage very similar to the Williamson (triode-strapped
KT66 again), and has become very fashionable (read expensive), but they are
likely to be in quite poor condition because of their age.
The BBC LSM/8 lived in a compartment at the bottom of the LSU/10 loudspeaker
(where it became very hot). Because it was intended for studio monitoring,
the amplifier has a transformer balanced input and a volume control. In common
with many BBC loudspeaker amplifiers, some versions included a bass equalizer.
Once these input modifications are removed, the two amplifiers are identical.
BBC amplifiers
Unfortunately, many BBC amplifiers were designed for 25-Ohm loudspeakers and
cannot be modified for 8-ohm without replacing the output transformer. It is
also well worth asking why the BBC disposed of the amplifier, particularly
if it is thought to have come from an impoverished local radio station. Under
the latter circumstances, it is most unlikely that it spent its time cherished
in a protective box in a dry cupboard.
Leak TL12+
This is a completely different beast from the TL12, and is very similar to
a Mullard 5-10 using EL84 output tubes. They are comparatively recent (perhaps
only 35 years old), but by modern standards they are noisy, owing to high sensitivity
and the EF86 input pentode.
Leak Stereo 20
Far more common than the TL12 +, this is almost a pair of TL12 + on one chassis
but sharing a slightly under-rated mains transformer, and with a few other
corners cut. Input tube is the dual triode ECC83, but they are still noisy.
A pair of TL12 + is preferable unless you are only buying the amplifier for
the chassis and transformers. Thanks to the continuous demand by musicians
(guitar amplifiers), modern EL84s are cheap and plentiful, but NOS Mullard
and Siemens EL84s are quite rare and therefore expensive.
Leak TL10
Similar in design to the Mullard 5-20, but uses a 6SN7 phase splitter. Quite
a nice conservatively rated amplifier designed for KT61 (tricky to find), but
can be modified for EL34 or 6L6.
Although many TL10s were made, fewer seem to have survived than the Stereo
20.
All Leak amplifiers are ridiculously over-sensitive. 110mV for full power
(Stereo 20) is far too sensitive and causes all sorts of hum and noise problems.
Rogers Cadet III
10W using ECL86 output tubes. There were two versions, an integrated version
and a separate chassis version. These are ideal for beginners to cut their
teeth on, but not of great intrinsic value. Beware that some rather nasty cost-cutting
means that cathode bias resistors and decoupling capacitors were shared between
the stereo channels, so poor stereo cross talk is probably due to a failed
electrolytic capacitor! Bizarrely, the power supply uses a voltage doubler,
and because this imposes high ripple currents, the two doubler capacitors are
highly likely to need replacement. Oddly, the disc input stage was very good
for its time, but the amplifier needs three ECC807 (m=140, and irreplaceable),
so if you are considering buying one, you must check that the amplifier has
the full complement of undamaged ECC807. |