(source: Electronics World, Nov. 1971)
By T/Sgt. EDWARD H. BRESLIN / Lowry Air Force Base, Colo.
Advent of IC's, modular designs, and miniaturized parts has
made new soldering techniques and tools a virtual necessity.
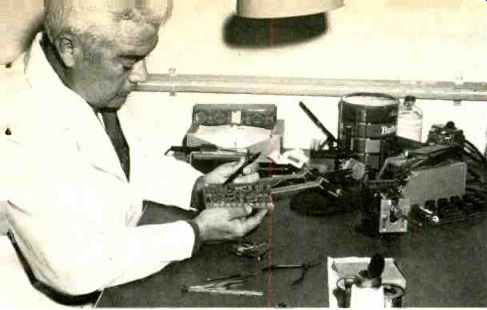
-- Author points out one of the encapsulated microcircuits which require precision soldering. NASA has established new high reliability standards
and Lowry AFB has developed tools.
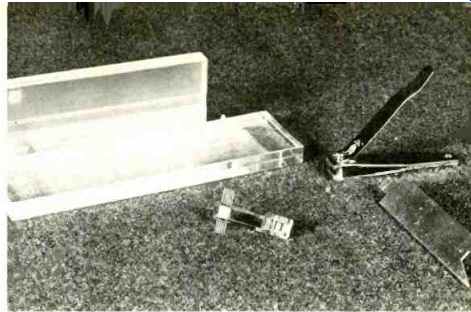
-- Some of the improvised soldering tools used at Lowry. Plastic blocks
bend wire leads, hair clip serves as heatsink, nail clipper is used to
cut wires, and the flat tool shapes the circuits.
IT all began during early space flights when bits of floating soldering
debris plagued the astronauts. NASA researchers solved the problem and
then imposed rigid new soldering standards on the aerospace industry.
As a vitally concerned party, the U.S. Air Force-through its Air Training
Command--immediately dispatched experts to learn the new high-reliability
soldering and microelectronic procedures, and today teaches them in continuing
courses at three of its large technical training centers.
Have you ever worked on an IC chip 1/8" X 1/8" X 1/64"?
This miniaturization poses undreamed-of precision soldering problems.
Since multi-lead, multi-circuit epoxy capsules allow minimal tolerance,
former standard soldering procedures became unacceptable.
A new family of solders had to be developed. Miniscule circuits, extremely
sensitive to heat, need solder which melts at low temperatures and quickly
passes through the plastic state. Circuits which can tolerate rapid temperature
changes, but not prolonged heat, require an eutectic solder which instantaneously
changes from solid to liquid.
The new technology also called for an impractically large number of new
irons and "mini-tips." Based on the rules for choosing the right
iron for the right job-terminal thermal point, dissipation, and recovery
rates--several irons were developed in which heat at the work surface
(the single most important factor in any soldering operation), could be
controlled by a variable transformer. With this, a 120-V, 25-W power source
could be reduced to the point where the job could be done with the lowest
possible heat.
Proper fluxes, cleaning solvents, and conformal coatings are equally
important to the efficiency of the finished job.
(The latter are plastic sprays which waterproof, bind, and assure even
distribution of heat to the part.) The fantastic growth of miniaturized
electronic technology far outstripped the manufacture of tools for servicing
them, so some makeshifts were developed in the field. For instance, at
Lowry AFB, technicians discovered that dental probes perform well in delicate
areas and that a metal hair clamp with flat arms holds the chip perfectly
without interfering with the soldering process. It also aids in distributing
the heat evenly. Such ingenuity hints at the dawn of a new era for the
micro-miniaturization soldering expert.
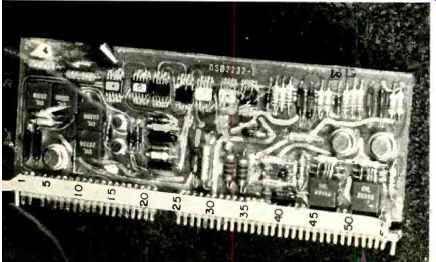
--- Pen points to one of the micro-mini circuits on component board
used for student practice in high-reliability soldering.
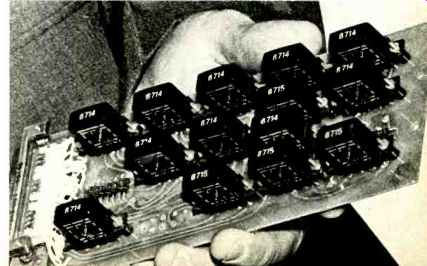
--This relay matrix circuit board is an example of components serviced
by students in Lowry AFB soldering course.
|