AMAZON multi-meters discounts
AMAZON oscilloscope discounts
Vibration sensors are sensors for measuring, displaying and analyzing:
- Acceleration
- Displacement
- Linear velocity
- Proximity
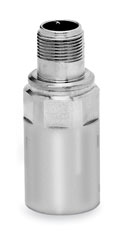
Above: A typical vibration sensor. This one is thread-mountable and made of stainless steel.
Vibration sensors may be used on a stand-alone basis, or as
a component in a data-acquisition
system.
Vibration sensors are available and sold in several forms, including:
- Packaged transducers
- Raw sensing elements
- As a sensor system or instrument which incorporates useful features
such as totalizing, local or remote display and data
recording
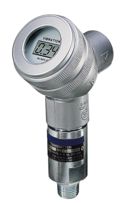
Above: An indicating model vibration transmitter.
This one comes in handy if you need to observe vibration (and take written
notes) at the equipment or machine being monitored.
Vibration sensors may have from one to three axes of measurement;
the multiple axes normally being orthogonal to each other.
Vibration sensors operate on myriad physical principles. The
most common are:
- piezoelectric
- capacitance
- null-balance
- strain
gage
- resonance beam
- piezo-resistive
- magnetic induction
- newer MEMS
technology allows for the integration of mechanical elements, sensors,
actuators, and electronics on a common silicon substrate through micro-fabrication
technology
Vibration sensor selection criteria:
- Accuracy (% of allowable error over the full measurement
range of the device)
- Environmental conditions (in which sensor(s) are to be used
in. Example: humidity, temperature, maximum shock and vibration the
vibration sensors will be able to handle. I.e., amount of abuse the
device can tolerate before it stops performing -- which is different
from how much vibration or acceleration vibration sensors can measure.)
- Frequency range, in Hz (see figure below of frequency vs.
sensitivity)
- Measuring range (in G’s for acceleration, inches/second
for linear velocity (or other distance over time), and inches or other
distance for displacement and proximity))
- Transverse sensitivity (this is the effect a force orthogonal
to one being measured can have on the reading; given as % of full-scale
of allowable interference). See figure below of frequency vs. sensitivity
- Other selection criteria include electrical output options
(depends on the system being used with the vibration sensors). Typical
analog options are: voltage, current or frequency. Digital output choices
are: standard parallel and serial signals. Another option is to use
vibration sensors with an output of a change in state of switches or
alarms. Also, these sensors can have acceleration, velocity, or displacement
as output by either integrating or differentiating their primary output.
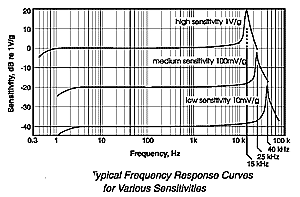 |
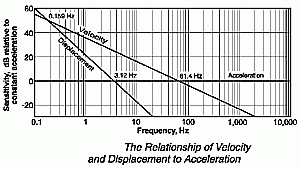 |
Criteria for mounting vibration sensors:
- Stud mounting (most secure)
- Threaded on to machine, equipment or device being monitored (see
thread-mount sensor below)
- Other methods include:
- Electrical and /or ground isolation may be required in certain cases
(see sensor power schematic below)
- Triaxial mounting cubes (see figure beelow) may also be used to mount
three vibration sensors together in an orthogonal configuration (this
allows one mounting surface on the monitored device has to be used for
all three)
- Your ultimate choice must be weighed based on your specific
application and ability
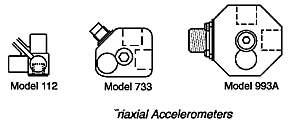 |
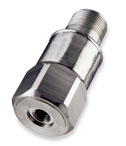
Above: thread-mount sensor |
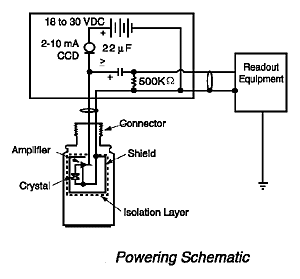
Above: Sensor power schematic |
|
|