(source: Electronics World, Mar. 1966)

By SIDNEY L. SILVER
These important components are widely used in industry for indicating small
changes in voltage and current, and operating control circuits when preset
values are reached.
In the field of automation there is an increasing need for simple, inherently
stable control-system components to perform the various process functions
with a high degree of reliability. One of the most useful and versatile
of these components is the meter relay, which combines the functions
of both an indicating meter and a control relay. Meter relays are electro-mechanical
devices which are capable of detecting and indicating extremely small
changes in current or voltage; and when these measured quantities reach
preset limits as determined by adjustable control points, a set of built-in
relay contacts effect the opening and closing of auxiliary circuits.
These instruments are sensitive enough to respond directly to low-level
signals ( without need for any further amplification) from any process variable
that can be measured electrically through the use of a suitable transducer.
They are widely employed to monitor and control such variables as temperature,
radiation level, pressure, moisture content, pH, motor speed, and a multitude
of other physical and chemical phenomena.
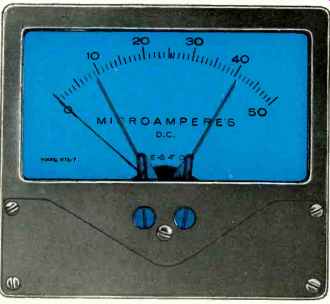
Fig. 1. Typical current-sensitive meter relay. This particular unit incorporates
two screw-adjustable contact pointers
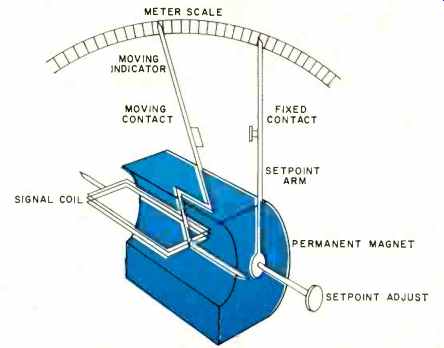
Fig. 2. Cutaway diagram of non-locking meter relay. The various leads for
control signal and load relay are not shown.
Meter relays can function as limit-control devices in which control action
is initiated when the safe operating limit of a measured variable is reached.
In this mode of operation, associated equipment is shut down and protective
warning devices are actuated. The unit is then reset manually each time
the variable reaches a predetermined control point.
In a programmed operation, meter relays can maintain an automated process
at a given level by automatic "on-off" control. In this mode of
operation, the desired control action occurs at a preset limit, but the
device continues to sample the variable periodically without interrupting
the load circuitry. Under these conditions, corrective control action ceases
when the measured variable returns to the proper level.
Meter relays may be broadly classified into three categories according
to their contact arrangement: the nonlocking, locking, and continuous-reading
types. In addition, a new concept in meter-relay design is the optical type
which incorporates solid-state switching to eliminate the usual physical
contacts. A typical, commercially available meter relay with two setpoint
arms is shown in Fig. 1.
Nonlocking Meter Relays
The nonlocking meter relay is a sensitive contact device which depends
solely upon the current flowing through a moving coil for maintaining contact
pressure. Operating on the d'Arsonval principle, as shown in Fig. 2, the
moving coil is attached to an indicating pointer and suspended on jeweled
pivots in the flux gap of a permanent magnet. When the coil is energized
by a signal current, a torque is produced which rotates the coil and causes
the pointer assembly to move across a meter scale in direct proportion to
the signal passed through the coil. The indicating pointer is restrained
by a pair of control springs (not shown) which serve as current leads to
the coil and restore the pointer to zero when the signal current is removed.
In addition, the instrument has an adjustable setpoint arm which is rotatable
along the same axis as the moving indicator and which may be manually adjusted
to any desired point on the meter dial. A moving contact is carried by the
indicating pointer and a fixed mating contact is mounted on the setpoint
arm. Some types are provided with two setpoint arms (each carrying a stationary
contact) which are adjustable for high and low operating values.
Fig. 3A shows the basic circuit of a nonlocking meter relay in which the
moving contact and the fixed contact form a series circuit with an external
load relay that is energized by a d.c. source. When a control signal applied
to the moving coil causes the indicating pointer to reach a predetermined
setpoint, the contacts are forced together, thus closing the load circuit.
If, however, the signal level falls below the set-point, the meter relay
resets itself automatically, and the signal coil restores the moving element
to a position relative to the amount of current in the coil.
One of the basic problems of the nonlocking arrangement is the small force
applied to the moving coil element to close the relay contacts. Since only
a few milligrams of pressure exist at the point of contact, it is necessary
to employ a high-torque meter movement in order to produce a reliable and
definite contact action. To increase contact reliability, a suitable contact
material such as platinum, is generally used because of its extremely low
contact resistance and its relatively high resistance to oxide film formation.
In addition, one of the contacts is made flexible in order to provide a
wiping action which keeps the contacts clean. To avoid arcing which may
produce contact corrosion, the open-circuit voltage across the contacts
is limited to about 6 volts d.c.
Generally, the use of nonlocking meter relays is restricted to applications
where the control signal abruptly rises or falls below a predetermined setpoint
so that the make or break period of the contacts occurs quite rapidly.
Locking Meter Relays
To offset the disadvantage of low contact pressure imposed by the nonlocking
arrangement, locking meter relays were developed to provide additional
torque to the signal coil. In this configuration, an auxiliary winding,
referred to as a locking or aiding coil, is integrally wound on the same
form as the signal coil. As shown in Fig. 3B, the locking coil is connected
in series with the load relay circuit across the d.c. power source. When
the indicating pointer reaches setpoint, sufficient current flows through
the locking coil to boost the signal coil rotation, thus maintaining firm
contact pressure (on the order of 2 grams).
Once the load relay is pulled in by the meter-relay contact action, it
remains energized irrespective of the signal current value, so that the
pointer no longer responds to input signals.
To reset the device, a push-button switch, in this case manually operated,
interrupts the d.c. circuit and opens the locked meter-relay contacts. If
the input signal has fallen below the lock-in value, the meter-relay contacts
remain separated and the load relay drops out. However, if the signal level
is above the preset level, the contacts promptly close again.
Since the moving contact is spring loaded, the contacts are kicked apart
forcefully when the load circuit is broken, thus overcoming any tendency
for the contacts to stick. The spring pressure allows operation of locking
meter relays at contact ratings up to 25 ma. at 125 volts d.c. For this
reason, these devices are particularly adaptable to slowly changing input
signals.
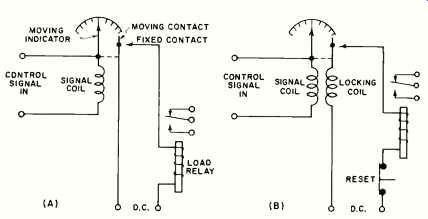
Fig. 3. (A) Basic circuit diagram of the nonlocking type, (B) Locking meter
relay circuit shown here with manual reset.
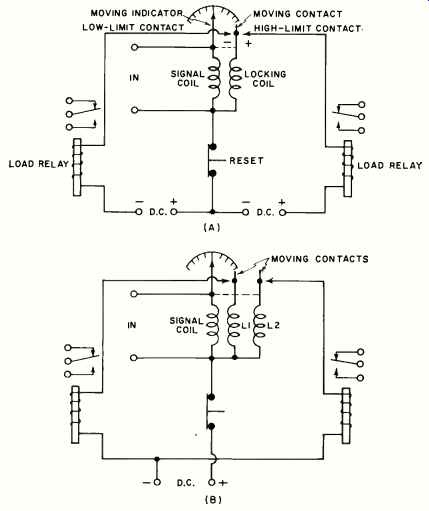
Fig. 4. (A) Double-contact type using a three-terminal power sup ply. (B)
Dual locking-coil arrangement with 2 moving contacts.
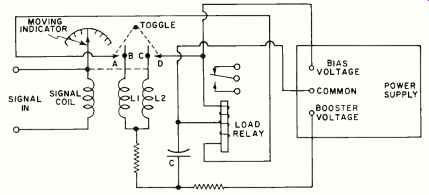
Fig. 5. Continuous-reading type with automatic-reset feature.
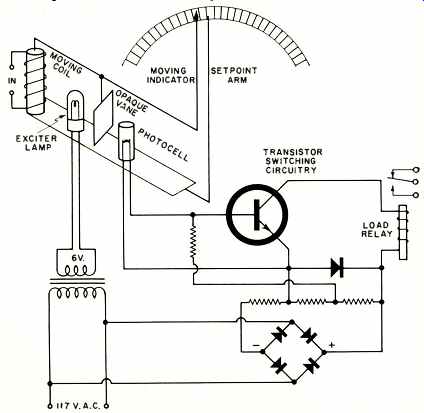
Fig. 6. Pictorial-schematic diagram of an optical meter relay.
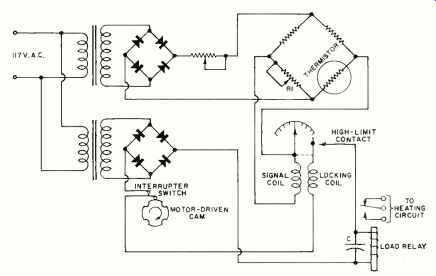
Fig. 7. Automatic temperature controller with high-limit relay.
In applications where both upper and lower limits for a specific current
are required, a double-contact meter relay is employed. This unit is provided
with two setpoint arms whose contacts are adjustable for high- and low-level
operating points. Thus, when an input signal rises or falls to either of
the predetermined control points, a load relay is tripped and control action
is initiated.
In the double-contact arrangement shown in Fig. 4A, both a positive and
negative d.c. power source are required. By this means, the voltages applied
to the fixed contacts are of opposite polarity, so that the locking-coil
torque is properly directed to maintain pressure on either contact. To lock
the high-limit contact upscale, for example, a positive polarity must be
applied to the high-limit contact to permit current to flow up through the
locking coil. Conversely, current must flow through the coil in a reverse
direction to lock the low-limit contact downscale.
Fig. 4B shows an alternate arrangement which employs a single d.c. power
supply but requires dual locking coils. In this circuit, the meter relay
contacts lock with the same polarity on both high- and low-level limits.
The locking coils are wound in opposite directions in order to maintain
the proper direction of force. Since a voltage of the same polarity appears
on each of the fixed contacts, the coil L2 locks in an upscale direction
and the coil L1 locks downscale.
Continuous-Reading Meter Relays
A unique arrangement which combines both the high contact pressure of the
locking meter relay and the instantaneous reset of the nonlocking type,
is the continuous-reading device shown in Fig. 5. The resettability feature
of this unit eliminates the need for interruption circuits and provides
a continuous indication of the monitored variable both above and below setpoint.
In the continuous-reading design, a V-shaped toggle arm is mounted on the
setpoint arm in such a way that it pivots behind the indicating pointer.
The toggle carries a pair of contacts (A and D) which form two separate
circuits through a center-tapped load relay. In addition, the moving pointer
has two isolated contacts (B and C) positioned so that moving contact C
touches toggle contact D when the pointer reaches setpoint in the upscale
direction; and contact A touches contact B as the meter moves downscale.
A d.c. power source is connected to the load relay which provides a biasing
current of sufficient amplitude to hold the load relay in, but not enough
to energize it initially.
When the moving pointer reaches setpoint in the upscale direction, capacitor
C discharges through one half of the load relay and the resultant current
surge pulls the relay in.
Simultaneously, booster coil L2 is energized and drives the pointer further
upscale so that enough torque is added to the pointer to trip the toggle.
This action opens the booster circuit to the load relay, but the biasing
current holds the relay in.
When the pointer returns downscale, contacts A and B close, and capacitor
C discharges through the other half of the load relay, thus bucking the
biasing current. At the same time, booster coil L1 is energized, which drives
the pointer further downscale, snaps the toggle back to its original position,
and opens the bucking circuit. By this particular sequence of action, the
moving pointer indicates input signal values continuously while the booster
circuits provide positive make and break action of the associated circuits.
Optical Meter Relays
A recent development in meter-relay design is the optical or contactless
type which provides continuous indication above and below setpoint without
the use of physical contacts. Fig. 6 illustrates a typical optical meter
relay which achieves its non-physical contact action through the use of
a light beam and photoresistive cell. In this configuration, the setpoint
arm carries both an exciter lamp and photoconductive cell arranged so that
the light source is projected on the sensitive surface of the photocell.
When the moving pointer is below setpoint, the light beam falling on the
cell causes its resistance to drop, which cuts off the transistor switching
circuitry and maintains the load relay in an unenergized state. When the
pointer reaches setpoint, a low-mass aluminum vane carried by the indicator
interrupts the beam of light illuminating the cell. The resulting increase
in cell resistance allows the transistor switch to conduct, which pulls
in the load relay and initiates control action. To obtain a high/low setpoint
meter relay, a separate light source and photocell are provided for each
setpoint arm that is employed in the device.
Automatic Control Applications
In many complex automation processes, it is necessary to maintain a variable,
such as temperature, at a given level by "on-off" control of associated
circuitry. Since meter relays of the locking type do not drop out when current
through the signal coil is reduced, an automatic interrupter circuit may
replace the manual reset button to periodically separate the locking contacts.
This "on-off" action allows the meter relay to intermittently
sample the process being controlled in order to determine whether further
control action is required.
Fig. 7 shows a temperature control unit utilizing a locking meter relay,
in which the contact action provides high-limit automatic control and the
indicating element gives direct readings in both Fahrenheit and centigrade.
In this circuit, a thermistor sensing element ( de signed for negative-temperature
coefficient) forming one arm of a d.c.-energized bridge, is mounted near
the source of heat to be controlled.
Initially, the bridge is balanced by R1 to provide the desired operating
point and the setpoint arm is adjusted for the required high-temperature
limit. Control action begins when an increase in temperature ( as small
as .075°F) unbalances the bridge and causes a current flow through the meter
relay signal coil.
This action causes the load relay to pull in and switch off the heating
circuit.
When the temperature drops below the control point, the load relay drops
out and the heat is switched on again.
To test the temperature periodically, the sampling interrupter switch is
actuated by a notched cam which, in turn, is continuously driven by a small
synchronous motor. The frequency of interruption is determined by the speed
of the motor (usually 1 rpm) and the number of notches on the cam. To avoid
breaking the load relay circuit during the brief periods of interruption,
capacitor C is placed across the relay coil to hold in the relay when the
sampling switch is open.
A common application of meter relays in industrial automation is the control
of positioning devices as a function of mo tor current. During an automatic
grinding operation, for example, a meter relay can utilize the fluctuating
load current of a drive motor to precisely regulate the grind-pressure applied
to a work-holding fixture. The fixture is positioned by a feed motor which,
in turn, is driven by a pair of load relays ( RL1 and RL2 in Fig. 8) which
operate from a low-limit and high-limit contact, respectively.
In this application, an a.c. signal de rived from the current drawn by
the grinding wheel drive motor is rectified to d.c. and fed to the signal
coil of a double-contact meter relay. Initially, the meter-relay setpoint
arms are adjusted for minimum and maximum drive cur rents. In normal operation,
with the proper drive motor current applied to the rotary grinding wheel,
the correct pressure is applied to the workpiece and no control action occurs.
However, when the drive motor cur rent decreases below the normal range
(indicating that grinding pressure is too light), the moving indicator and
the low-limit contact lock downscale and load relay RL1 is energized. The
load contacts start the feed motor in a direction which advances the fixture
toward the grinding wheel. Simultaneously, the normally closed pulsing contacts
of RL1 intermittently make and break the low-limit locking circuit so that
continuous sampling of the drive motor current occurs. This "on-off" pulsing
action continues as long as the meter relay is at or below the low setpoint;
and the resultant corrective action ceases when the signal is restored to
normal range.
Conversely, when the drive motor current increases above normal value (indicating
that grinding pressure is too heavy), the high-limit contact locks upscale
and load relay RL2 is pulled in.
The feed motor now retracts the fixture from the grinding wheel. At the
same time, the pulsing contacts of RL2 sample the input signal until the
drive motor current again reaches normal value.
Ordinarily, the opening of the pulsing contacts would result in de-energizing
the relay coils so that the load contacts would be released instantly. Load
re lays RL1 and RL2, however, are kept energized during each pulsing cycle
for a period of time determined by the R1C1 time constant in the low-limit
circuit and the R2 C2 combination in the high-limit circuit. R1 and R2 must
be sufficiently high (on the order of 3000 ohms) to limit the peak current
in the locking coils which otherwise may cause arcing of the meter-relay
contacts.
Pulsing rate is also a function of the characteristics of the load relays
and is generally designed so that interruptions occur two times per second.
The over all effect of the holding action is to keep the feed motor operating
steadily during pulsing periods in order to apply corrective positioning
of the fix ture and, at the same time, to allow the meter-relay contacts
to respond to drive-motor current changes.
Meter relays are now being assigned more and more critical tasks in the
field of automation.
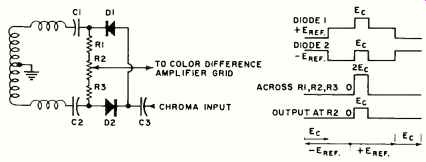 Fig. 8. Pulsing meter relay for automatic machining process.
|