Authors: B. V. PISHA and GEORGE ALEXANDROVICH
On the evening of November 2, 1920, radio station KDKA in East Pittsburgh,
Pa. broadcast to a tiny but eager national audience the results of the Harding/Cox
presidential election. That is the date given in history books as the official
birthday of commercial radio broadcasting. As other stations followed suit
with nation al hookups, the word was that the phonograph record, a mere 43-year-old,
had not long to live. Why listen to "canned" music on phonograph
re cords when you could hear live orchestras playing from hotel ballrooms,
symphony orchestras performing in concert halls, and operatic personalities
singing from famous opera venues? Despite these divinations, the phonograph
record endured, and in fact it became even more popular as a direct consequence
of radio broad casting.
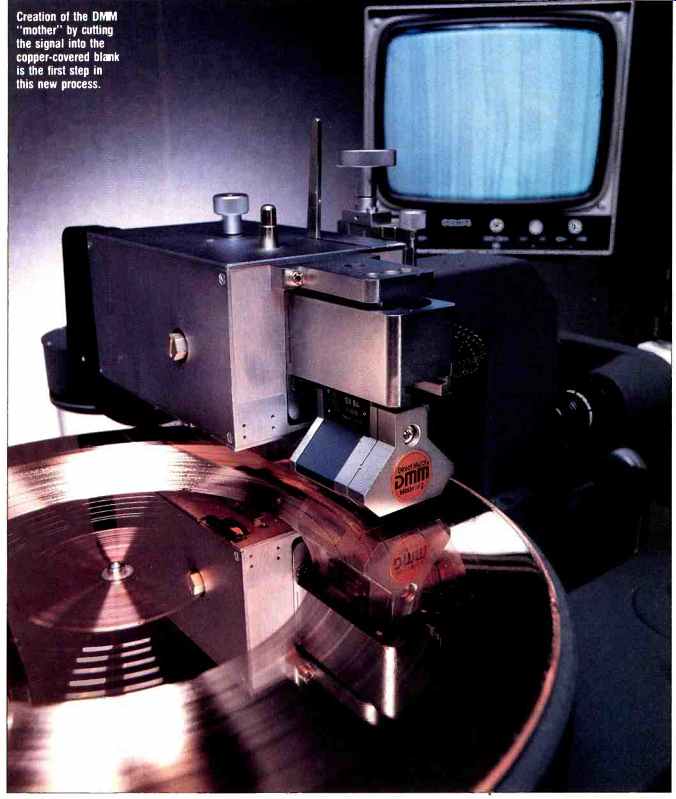
-----Creation of the DMM "mother" by cutting the signal into the
copper-covered blank is the first step in this new process.
Introduction of the monophonic reel to-reel tape recorder in the American
marketplace back in the late 1940s, and its growing popularity in the '50s
as a stereo sound format, sparked an other flurry of predictions that the
phonograph record was doomed. But those predictions turned out to be similarly
incorrect.
Enter North American Philips to spread the gospel of the audio cassette,
at first in a mono format which evolved into stereo. Following improvements
in blank-tape technology and the advent of Ray Dolby's consumer noise-reduction
system, the cassette moved up the scale to establish itself as a true high-fidelity
medium. Recently, just a couple of years ago, sales of prerecorded cassettes
topped those of LP records. Rumors again flowed rampant and the doomsayers
had an other field day, proclaiming that the phonograph record was heading
for the graveyard. Not so! Comes the digital Compact Disc with all its technological
bravura, and the rumors are again flying that the phonograph record is about
to die.
(We amend that; people are saying the analog phonograph record is about
to die.) But as Bing Crosby crooned it in his days with Paul Whiteman (on
Columbia picture record 1444-D), " 'Tain't So, Honey, 'Tain't So."
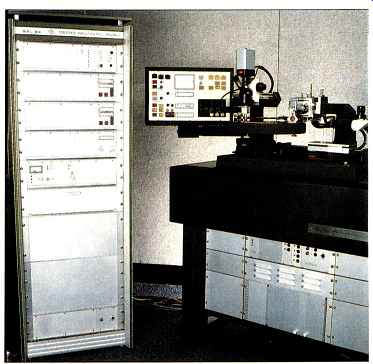
----The equipment used in the DMM system includes a Neumann VMS 82 lathe
with an SX 82 cutterhead, TV groove monitor, SAL 84 cutting amps, and a computer
to control the variable pitch and depth.
During this half-century plus, the makers of phonograph records were not
sleeping. They moved from the Acoustical Era, with its 78-rpm shellacs (actual
speeds ranged from 67.92 to 87.80 rpm), to the Electrical Era, then into
the Vinyl Mono LP Era, then the Stereo LP Era. Then came the Direct-to-Disc
Era (a new version of the old direct-to-disc recording approach that was
used in the days of 78s) and finally the Digital/Analog Era.
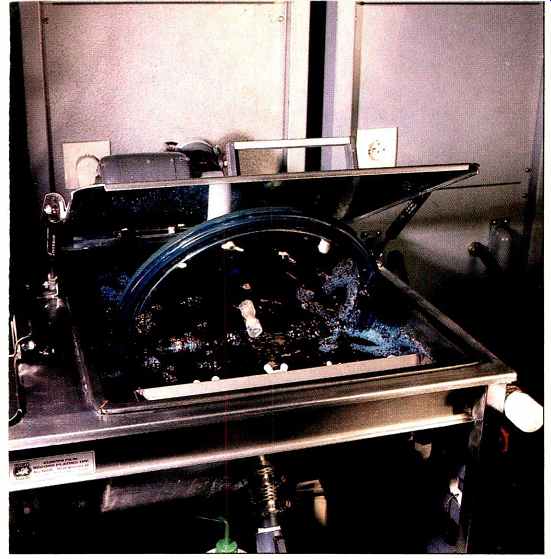
-----Europadisk does both cutting of masters and plating in near clean-room
conditions, which keeps possible contamination of the record groove down
to the minimum.
Concurrently, during that half-century, audio equipment manufacturers were
also not sleeping. R&D labs kept busy, designing better record-playing
equipment-namely automatic changers, then better turntables and tonearms,
and along the way, better cartridges. Manufacturers stopped producing steel
and cactus phonograph "needles," replacing them with sapphire-tipped
styli. These evolved into models with multi-faceted diamond tips, some costing
hundreds of dollars.
And now, we predict-with perhaps a trace of trepidation in our temerity
that the analog record will survive! Away with ye, doomsayers! What is the
basis for such defiance of the establishment? A simple acronym-DMM.
DMM stands for Direct Metal Mastering (or Direct Metal Master), a technology
introduced in 1981 that effectively moves the analog phonograph record into
a new era. First came tinfoil (circa 1877) as the mastering material, then
beeswax shortly thereafter, then shellac somewhat later, then finally lacquer
(acetate). DMM technology moves the phonograph record into the Copper Master
Era.
That in itself might not seem like an important change, but its significance
lies in what copper mastering means to the listener/consumer. According to
Europadisk, Ltd., the first DMM licensee in the United States, DMM leads
to finished phonograph records which have:
Up to 15% more playing time (as much as 40 minutes total per side);
Substantially reduced noise and distortion (10 dB less over the entire frequency
range). The signal-to-noise ratio is typically 75 dB;
Noticeably improved high-frequency and transient response;
Improved groove depth and spacing between grooves, to prevent stylus "skipping";
A marked increase in stereo separation, particularly in the low frequencies
(e.g., greater than 20 dB at 100 Hz and below); and
Cleaner, tighter bass response.
Additionally, it provides these benefits at no increase in price. (The retail
cost differential between analog and CD continues to be in favor of analog,
even when DMM is used.) To the recording fraternity, says Europadisk, DMM
means:
Elimination of lacquer-related problems such as swishes, echo, tickiness,
and other sound blemishes;
No cutting "horns";
No lacquer-plating or lacquer-aging problems;
Virtual elimination of the need for re-cuts; and
Faster stamper production (as a consequence of bypassing two plating steps).
In effect, DMM is analog gone state of-the-art, or the highest form of analog
phono record. While DMM technology is not perfect-and neither is CD technology
at its highest point yet-DMM records can be said to be at the same level
as CDs in terms of their ascendancy toward the goal of perfect sound reproduction.
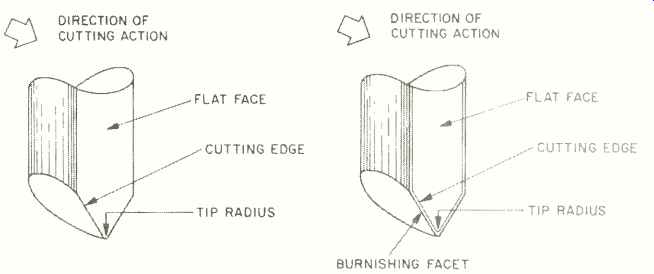
(left) Fig. 1-Cutting stylus for Direct Metal; (right) Fig. 2-Cutting stylus
for conventional Mastering. lacquer mastering.
------------------
Table 1--Performance data for playback of DMM masters, measured by Teldec,
using a Shure V15 Type V pickup.
Frequency Response: 20 Hz to 20 kHz, ± 1 dB, over entire cutting radius
from outer rim to innermost allowable modulation diameter. No losses up to
wavelengths of 10 µm.
FIM (DIN 45511): Less than 0.3% (315 Hz/3.15 kHz, 4:1) for 5 cm/S peak recorded
velocity, re: RIAA equalization for 1 kHz. (Note: Distortion is for single-channel
recordings at 11-inch/280-mm recording diameter; distortion wilt be higher
for playback at smaller diameters.)
THD (DIN 45503): Less than 0.5% for 5
cm/S peak recorded velocity at 1 kHz. (See note above.)
Twin-Tone IM (DIN
45503, IEC 268): Less than 0.1% for 1.000 and 1200 Hz at 5 cm/S peak
recorded velocity. (See note above )
S/N: Greater than 70 dB (typically 75
dB), A-weighted (per DIN 45633, IEC 179). re 10 cm/S peak recorded velocity.
See Figs. 3A and 38 for spectral distribution.
Groove Echo Attenuation: Greater than 65 dB for 10µm land between grooves
and greater than 75 dB for 150 µm land, re: 8 cm/S peak recorded velocity
at 1 kHz, single channel.
Recording Losses for Small Wavelengths: See Figs. 5 and 6.
Transient Response: See Figs. 7A and 7B.
------------------
Just as some golden-ear audiophiles continue to tout vacuum-tube equipment,
so too are many golden-ears claiming that analog LPs sound far more natural
than CDs, despite all the attributes of the CD format. Do DMM LPs live up
to the claims made by the recording fraternity? We say yes-with an exclamation
point. If any thing, we feel that the claims for DMM are somewhat understated.
On comparing DMM discs with traditionally produced records, we first noticed
the extreme quiet in the lead-in grooves and during pianissimo pas sages.
The minimal remaining noise is totally free of annoying ticks and pops.
Additionally, there are no pre- or post-echoes on DMM discs, such as can
be heard on traditionally mastered LPs.
The suppression of groove deformation noticeably improves the impulse response,
so that instruments rich in harmonics remain free of coloration even at high
levels. Frequency response ranges from 2 Hz to 23 kHz with extremely little
roll-off. (For readers interested in DMM's more technical details, the data
presented in Table I were provided by Teldec.)

---Separation of the plated stamper from the metal master reveals the surface
which will actually do the work.
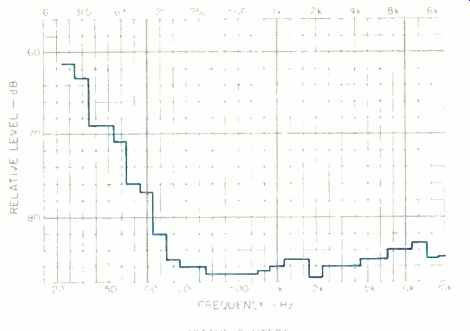
Fig. 3--Noise spectrum of unmodulated groove of a DMM mother (0 dB = 10 cm/S).
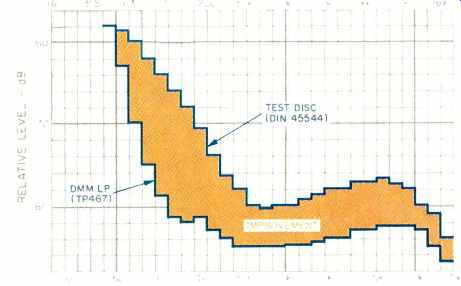
Fig. 4--Comparative noise spectra of test discs cut from lacquer master (top
curve) and DMM master (bottom curve).
About the only negative comment we can make is that occasionally one will
hear a slight "edge" or "sizzle" in high-frequency sounds
(the same sort that one hears, but more often, on early Compact Discs). This
anomaly is easy to put up with, since it generally occurs for only brief
periods in most music.
While CDs are superior in their dynamic range, which can go up to 90 dB,
the DMMs provide an easily accepted 75 dB (versus less than 60 dB for "old" analog-type
records derived from lacquers). It is conceivable that DMM can go a bit farther
in dynamic range as more and more companies get involved with it and put
their collective minds to extending that range. In the meantime, many music
lovers who have been able to make direct comparisons between DMM analog and
CD versions of favorite works frequently prefer the DMM analog version.
The DMM process was developed, under the aegis of technical director Dr.
Horst Redlich, by Telefunken-Decca Schallplatten GmbH (Teldec) of West Germany,
in conjunction with Georg Neumann GmbH, the latter owned 25% by Teldec.
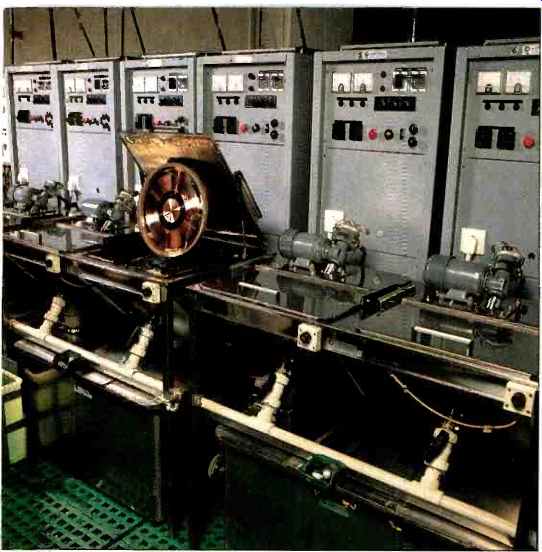 -- Europadisk is also licensed to produce the blank copper masters in
addition to doing the cutting, plating and pressing.
The DMM process is based upon Teldec's pioneering work, done in connection
with their videodisc research, to develop a copper deposition, on a stainless-steel
substrate, that would be suitable for cutting. The TED disc, introduced by
Teldec in 1976, was the first commercial videodisc, and it used the DMM manufacturing
process.
Since the initial development of the DMM process, continued research has
brought further improvements. In order to meet the requirements for analog
audio LPs, an improved copper was introduced. This "Type 2" copper,
yielding a signal-to-noise ratio in excess of 70 dB for a 40-micron groove,
has been adequate for most types of programs. However, for certain difficult
programs (containing large amounts of out-of-phase, low-frequency information)
it was desirable to make further refinements, and so an improved cop per
deposit was developed which yielded signal-to-noise in excess of 75 dB. An
additional advantage has been an increase in the uncut masters' shelf life
(re-crystallization time) from several weeks to many months. (This is not
a concern once the master has been cut.) Europadisk will now produce both "Type
2" and "Special" copper carriers. "Special" carriers
will be more ex pensive than "Type 2" because of an increase in
plating time and greater expense in maintaining the electro-forming bath
in which the copper is deposited.
Since the introduction of DMM, at least 40 record producers around the world
have begun to use DMM equipped lathes. While DMM is only a recent "happening" in
the U.S. (where there are more than 20 companies in DMM production, and others
about to start), well over 100 million records pressed from DMM masters have
been sold worldwide. (Teldec's DMM equipment is imported and distributed
in the U.S. and Canada via Gotham Audio of New York City.) Because the DMM
processing system differs markedly from that of lacquer-master processing,
and the resultant "family relationship" nomenclature is also different,
a delineation of those differences is in order.
It is possible to produce only a single negative (the master mold or "father")
from each cut lacquer master.
Since a large number of pressing stampers are needed for producing the records
themselves, this master mold must, in turn, provide several "mothers" (positive,
.playable metal parts), which then create the "sons" (pressing
stampers/negatives). The re cord which is sold is therefore actually the "granddaughter" of
the lacquer original. A cut copper master, on the other hand, can create
numerous "fathers" which may be used directly as the pressing stampers.
The purchased DMM record is then a "daughter" of the DMM original.
This shorter path not only speeds the process up, but precludes quality deterioration.
===========================
DMM FOR CDs TOO!
LEONARD FELDMAN
[Editor's Note: We are indebted to the Audio Engineering Society, Messrs.
Horst Redlich and Guenter Joschko, and to Teldec for allowing us to quote
extensively from their preprint (No. 2372) from the 81st AES Convention.-E.P.]
Although CD players are in ample supply (some say oversupply), CDs themselves
have not kept pace with demand. This accounts, in part, for the fact that
prices of CD players have plummeted faster than anyone would have predicted
a few years ago, .but prices of discs have gone down only marginally or not
at all.
Among other things, one prerequisite for more economical manufacturing of
Compact Discs would be the economical production of masters and stampers
for pressing them. To date, laser recording technology has been the only
method available for manufacturing CD masters.
This technology makes use of a photoresist method derived from semiconductor
manufacturing techniques. Although this technology lends itself to recording
and subsequent molding of the kind of signal that is read by laser-beam pickups,
it is extremely expensive. In fact, it has been estimated that the investment
a re cord company has to make to produce CDs is 10 times greater than that
for an equivalent installation to produce vinyl analog records. Part of the
increased cost is because all major manufacturing steps must be performed
in a clean-room environment. Furthermore, the personnel working in most disc-cutting
facilities and pressing plants don't have the back ground or experience needed
for this type of technology. Therefore, CD mastering is presently performed
in comparatively few locations around the world.
Given these facts, it is not surprising that the most exciting development
at the last AES convention was Teldec's announcement that they had extended
their system of Direct Metal Mastering (DMM) so that it could be applied
to Compact Discs, just as it has been applied to analog LP production, to
the earlier Telefunken videodisc, and, more recently, to the RCA SelectaVision
videodisc. In short, as Bert Whyte reported in "Behind the Scenes" in
February, the Teldec DMM method makes it possible to record information on
a CD master in much the same way as it is done on an analog record master-by
mechanical means, employing a piezoelectric transducer with a bandwidth of
several MHz.
Conventional Disc-Mastering Techniques
In order to understand the new Teldec DMM system, it will be helpful to
review some of the more common methods used to mechanically cut the vertical
modulations on analog master discs. (We'll ignore how the analog masters'
lateral modulations are cut, since CDs have no lateral component.) Figures
B1, B2, and B3 illustrate three different principles. In Fig. B1, the cutterhead
is fastened to an arm which moves the head across the disc;
this arm is also pivoted vertically, permit ting it to follow variations
in the height of the disc surface. Pressure is applied to the head. While
cutting a stereo groove, the pressure is varied by the signal so that the
groove's depth is proportional to the signal's amplitude. This will prevent
the stylus from rising out of the groove when heavy vertical modulation increases
its vertical travel in relation to the cutterhead.
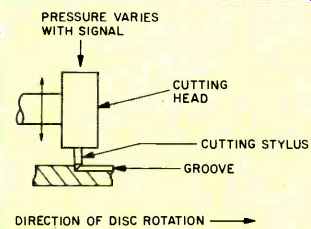
Fig. B1--In this analog disc-cutting system, groove depth is controlled
by pressure applied to the cutterhead.
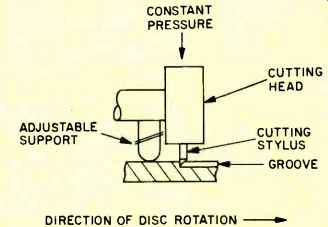
Figure B2 shows an older arrangement.
Here, the pressure is applied so that an adjustable support (the "advance
ball") rests on the surface of the blank disc. The cutterhead follows
the medium's surface, and the groove depth is determined by the support's
height relative to the adjacent cutting stylus; vertical adjustment for groove
amplitude is accomplished within the cutterhead. This method and the one
described above are used primarily for recording phonograph discs.
Figure B3 shows a cutting system for high-density storage, such as videodisc
recording; it was used to cut grooves only 0.1 µm deep for the Teldec and
RCA videodisc systems. In contrast to the other two arrangements, the cutterhead
is held at a fixed height. Since this prevents the cutter from following
motions of the disc's surface, its height is set so that the tip of the cutting
stylus will always be below that surface. Thus, more material than necessary
is removed in the cutting process, generating an entirely new surface. Here,
the groove depth depends only on the height of the cutterhead; the groove
width depends upon the groove depth and the included angle of the bottom
facets of the cutting stylus tip. While this method allows very high precision,
it is applicable only if the distance between grooves is constant and if
no "land" is required between adjacent groove segments. Neither
of these requirements is met by the CD format.
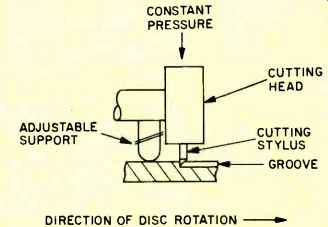
Fig. B2--1n the "advance-ball" method, groove depth is controlled
by the height of the adjustable support.
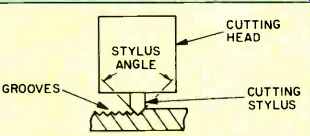
Fig. B3--In this system, used for videodiscs and other high-density recordings,
the cutting head is set at a constant height; the stylus cuts away the original
disc surface to create an entirely new surface.
Mastering the Pits
The pits on a CD can be thought of as constituting a spiral groove which
is interrupted according to the digital data stream applied. In other words,
it consists of very short groove segments of different lengths. At first
glance, one might think that the arrangement of Fig. B2 could be modified
for this type of recording. That is, the difference in height between the
sup port and the cutting tip could be adjusted so that the cutter would dig
into the surface when a pit was required and lift off the surface when a
land or absence of pit was called for. Unfortunately, because of Fig. B4-In
the DMM system, the expansion and contraction of a piezoelectric transducer
raises and lowers the cutting stylus rapidly, creating pits in a CD master.
the microscopic dimensions of the pits involved in the CD format, it is
a practical impossibility for the support to follow variations of the disc
exactly without causing damage to the surface structure.
Figure B4 illustrates a possible solution to the problem. A piezoelectric
transducer has a cutting stylus attached to it. When a positive potential
is applied to the upper electrode and a negative potential is applied to
the lower electrode, the piezo electric element expands (as shown at the
left). Conversely, with reverse potentials applied, the piezoelectric element
con tracts (as shown at the right). The force needed to produce this dimensional
change is very great and is generated by an electrical field. The assembly
rests on the disc, and the cutting stylus enters into its surface due to
gravity. The gravitational force required to cut sufficiently deep into the
surface of the disc is very small. Since the piezoelectric element contracts
more rapidly than gravity can shift the cutting stylus, the stylus lifts
off the disc temporarily. The pulses are so short that the stylus does not
have time to fall to the disc's surface during a negative pulse. Instead,
it cuts into the disc during a positive pulse, generating the desired pattern
of pits in the master.
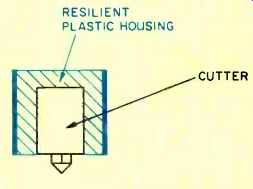
Fig. B5--A resilient plastic housing holds the piezoelectric transducer
in position while accommodating the transducer's changes of shape.
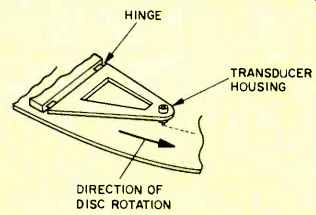
Fig. B6--A DMM cutter assembly for Compact Discs, showing the transducer
housing and floating support.
Of course, the piezoelectric element can't be suspended in midair and held
at its center of gravity, so a support (shown in Fig. B5) was developed.
The transducer element is embedded in a plastic material which is soft enough
at the operating frequency of the transducer to permit the expansion and
contraction described. Effectively, this plastic structure provides a "floating" support.
The complete assembly takes the form shown in Fig. B6. The floating transducer
is mounted in a triangular bracket which is secured on one side and is free
to move in a vertical direction. The tip rests with some of its weight on
the disc. Dynamic parameters of the assembly are carefully sized so that
the housing of the floating transducer follows vertical changes in the surface
of the disc over a range of several µm.
Embossing Rather Than Cutting
Using DMM to cut pits into the surface of the CD metal master creates a
problem:
The chips created by the cutting are too small to be vacuumed off the disc
surface during cutting (as is done when cutting analog masters). Teldec therefore
suggests embossing the signal pits into the surface of the master disc, rather
than cutting them in. The diamond tool attached to the piezoelectric transducer
is of a different shape for embossing than for cutting. Although pits generated
by the embossing process create a different modulation of the reflected laser
beam as received by the optical system during playback, the method fulfills
the most important prerequisite for Direct Metal Mastering technology as
applied to the compact Disc, namely full compatibility with conventional
CD players.
Making a DMM CD Master
Since a metal surface is used as the original recording medium, final pressing
tools or stampers can be generated directly in a galvanic process without
any intermediary steps. A round glass disc is prepared with a thin separation
layer. A layer of copper approximately 300 nanometers thick is evaporated
onto the disc.
The pits are recorded onto this copper surface as previously described.
Because the pits are generated directly, it is possible to control them more
accurately than is the case with the photoresist/laser cut ting method used
until now.
Once the copper layer is embossed with the required pit pattern, the copper
surface is coated with a thin layer of precious metal. This metal package
is then reinforced in a nickel bath until a thickness of about 0.25 mm is
achieved. The metal package can now be used as a "father" (from
which "mothers" and stampers will be produced) or, if the number
of CDs required is not too large, the package can itself be used as a stamper,
good for anywhere from 10,000 to 15,000 pieces. In the latter case, according
to Manfred K. Atzert, managing director of Teldec, CD pressing can begin
within about two hours after completion of the mastering process.
The thin separation layer on the glass disc allows the metal package to
be re moved easily from the glass, which can be used again. The recording
itself is completely protected between the copper and precious-metal layers.
This galvanic "sandwich" technique therefore provides an excellent
and safe medium for storage and shipping.
The last step in the DMM-CD process is the release of the electroplate from
the sandwich. Both the separation layer and the copper layer consist of non-precious
metals, so it is fairly simple to remove them without damaging the precious-met
al surface on the nickel backing. Then, using the metal backing as a "father," more "mother" and
stamping tools can be manufactured using the same galvanic process.
Breaking the Cost Bottleneck
Teldec, in describing this new technique, cited five major benefits that
accrue from the DMM-CD method. First, the expensive clean-room environment
is not required when making a master recording. Accordingly, less physical
space is needed for the mastering process. There are fewer production steps,
and production is therefore more efficient. A faster turnaround is possible,
which should help make the number of CD titles equal to the number available
in black vinyl in a shorter time period. Finally, the entire pro cess is
easier to handle. It all adds up to a lower investment for the software makers.
So if you have been holding off on the purchase of a CD player because of
un availability of your favorite records in CD format, you won't have this
excuse to fall back on for quite as long as you may have supposed. Ali of
which bodes well for the future of audio, graphics, video, and text data
storage in the CD format.
===========================
------------
Table II-Standard data of DMM technology.
Maximum Recording Level: As for lacquer cutting Maximum Groove Width During
Modulation: 180 µm.
Cutting Stylus Utilization Period: 20 LP sides per re-polishing.
Cutting Stylus Life Time: 50 re-polishings, minimum.
Storage Time of Copper Blanks Before Recording: 3 months.
Storage Time of Copper Master After Recording: No limit.
Number of Stampers by Direct Matrix: 20, minimum.
Number of Stampers by Three-Step Plating: Equivalent to standard processing.
Groove Integrity: High, due to fact that formation of "horns" is
completely avoided.
-----------
To permit the previously mentioned "father" to be made from a
lacquer, its surface must be made conductive and this process must not alter
the modulated grooves. The conductive surface (of silver) must be extremely
thin and must not attack the lacquer surface.
Furthermore, the silver molecules must be evenly applied to minimize the
creation of impulse-type interference, which can no longer be corrected.
Nickel is plated onto the silver surface, and this can seriously deform
the grooves in the lacquer through mechanical stress. Therefore, the mastering
engineer must make the groove walls thicker than really necessary be cause
of the instability of the lacquer coating, on the one hand, and the danger
of deformation resulting from the nickel-plating process on the other.
This reduces playing time. But despite this precaution, pre- and post-echoes
are still audible in classical records.
The metal cutting surface of DMM avoids all of these disadvantages. For
the tape-to-disc cutting room, DMM provides a distinct advantage: The 20%
rejection rate which has been traditional in lacquer cutting and subsequent
plating is reduced to less than 2% with DMM. Further, the 10 to 20% rejection
rate in choosing lacquer discs suitable for cutting is bypassed.
The overall DMM system is a complex one, involving many interrelation ships
among chemical, thermal, electrical, electronic, and mechanical processes
as well as human judgment factors. We'll attempt to delineate them by recounting
what we learned during a trip through the facilities of Europadisk, in downtown
Manhattan. Our guide was James P. Shelton, the company's president. (For
additional de tails, see Table II, provided by Teldec.) Before the tour got
underway, we were told that Europadisk is, in effect, a "one-stop" operation
in that it is licensed for all DMM processes-mastering, plating, and pressing,
as well as the production of master discs (copper blanks) for use by Europadisk
and other DMM licensees. In fact, Europadisk is the only source in the U.S.
and Canada for the copper master-disc blanks.
(Of course, they can also be bought directly from Teldec.) To earn the right
to place the DMM logo on a record album, a record company must have all the
DMM work done by licensees, such as Europadisk.
The first thing that Shelton pointed out was the "clean-room" ambience
typical of well-run establishments producing high-tech products. "It's
only natural," he stated. "If you've seen the clean-room surroundings
where digital Compact Discs are produced, and if you want to compete with
the CD people, you should be as good as they are in terms of your own production
facilities or even better. Maintaining a clean operation means that the possibility
of record-groove contamination in cut ting, plating, or pressing is almost
eliminated." The main area that we visited was the cutting room, where
the required equipment was housed. It included a Neumann VMS 82 cutting lathe
with an SX 84 cutterhead, a TV monitor for viewing the cut groove, SAL 84
cutting amplifiers, and a variable pitch and depth computer. Some DMM licensees
utilize VMS 80 cutting lathes, which can be upgraded, if desired, to VMS
82 equivalents.
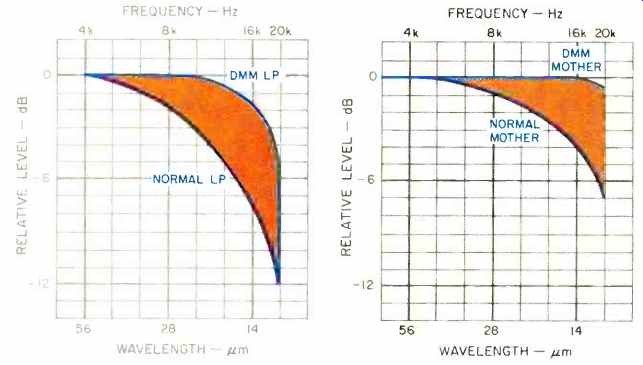
[left] Fig. 5-Comparison of frequency response for small wavelengths on LPs
pressed by Teldec from lacquer and DMM masters, at 130-mm groove diameter,
using Shure V15 Type V cartridge. [right] Fig. 6-Same as Fig. 5 but for playback
of DMM and normal (lacquer) mothers.
The SAL 84 amplifier drive system used for DMM is completely free of transformers.
The frequency response of the system extends to 2 Hz on the low end. This
expansion of the frequency response by about two octaves (compared to the
older lacquer system) is not meant for cutting signals in that portion of
the spectrum but rather serves to linearize the phase response in the audio
range, which lies quite a bit above this frequency. The practical result
is significantly higher feedback at low frequency, thus improving the phase
response and also improving crosstalk between channels.
Phase shift at 20 Hz is less than 20°, and stereo separation at 100 Hz is
greater than 30 dB. At the high end of the spectrum, the frequency response
extends to 23 kHz, with a gentle roll-off above that.
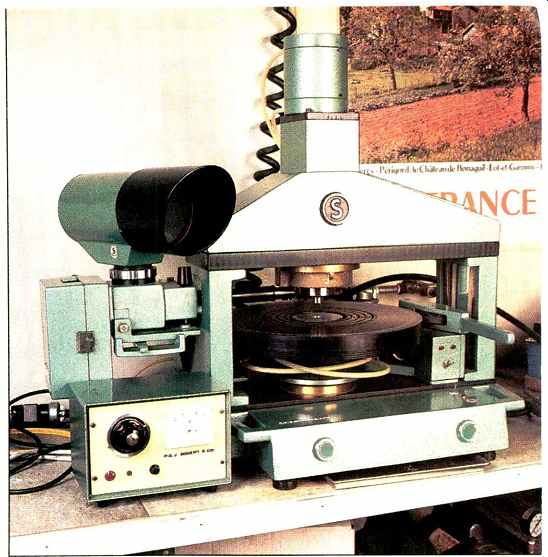
-------- Here the stamper is being center-punched for an accurate location
on the pressing machine.
Separation between channels below 100 Hz is also much better than lacquer,
due to differences in the DMM lathe's electronic control system. The conventional
cutterhead suspension, engineered to appear stiff at frequencies above 20
Hz, allows the cutter-
head to float at frequencies below that point in order the surface of the
master blank. Unfortunately, this floating effect reduces channel separation
at low frequencies.
In DMM systems, special circuitry applies a counteracting depth-control
force which is in proportion to the low-frequency signal amplitude. The result
is that the cutter remains stiff for all audio signals, even below the suspension
resonance point. This yields 20 dB of channel separation to 20 Hz and lower,
which is far superior to conventional lacquer cutting. In fact, the low-frequency
stereo separation is one of the first things people notice about DMM masters.
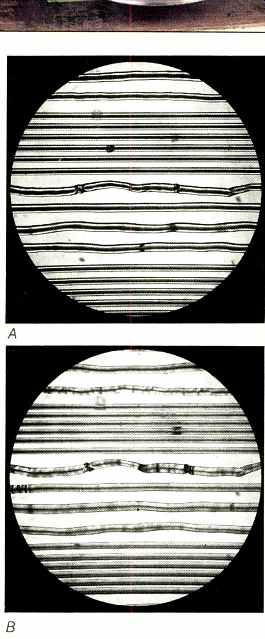
Fig. 7--Mothers from lacquer (A) and DMM (B) masters. Note rounding off of
transients in (A) due to heating and burnishing facets required for lacquer
masters. Sharper transients in (B) result from "feather edge" on
DMM cutting stylus.

----- The last step before mounting the stamper in the record press is
to form its shape so that the proper record profile will then be pressed.
DMM technology is centered on the ability of the Neumann cutting lathes
to cut into a 4-mil-thick (100-micron) coating of amorphous copper layered
onto a 300-mil stainless substrate, in stead of the traditional aluminum
lacquer-coated disc. Shelton explained that cutting copper masters is substantially
different from cutting those with a lacquer coating. The material is much
harder and is five to 10 times more resistant to the cutting stylus than
lacquer. "It would be impossible to cut a copper disc at 20° off perpendicular,
the angle that is appropriate to lacquer mastering and which is the standard
for playback tracking relative to consumer phono cartridges.
The stylus would 'ride' the groove it was cutting, in effect not cutting
deep enough. Therefore, Teldec designed the VMS 82 to cut a master at a near-0°
angle-about 5°." This approach reduces the required cutting force to
an adequate level so that the cutter needs only normal cutting-amp power.
Essentially, the rotational force of the VMS 82 turntable is concentrated
against the face of the cutting stylus, attempting to break it rather than
to push it up and away from the master surface.
Helping to keep the rotational force within normal cutting-amp power limits
is the shape of the new Teldec diamond cutting stylus (Fig. 1). This stylus
has no burnishing facets and thus avoids the high-frequency amplitude losses
that occur at the innermost grooves of LP records.
While a 5° cutting angle is employed, the IEC standard playback angle for
consumer phono cartridges is 20°, and this must be factored into the DMM
process. In addition, the grooves must be cut to meet that standard; other
wise, playback would be severely distorted. Teldec gets around this dilemma
by adding a tracking-correction element to the cutting signal. Said Shelton, "The
deviation from the usual value of the vertical tracking angle is corrected
by means of an electronic delay equalizer that is part of the system's electronics.
It is called a Vertical Tracking Angle Converter, and it provides the correct
playback angle for a typical phono cartridge through time delays." Shelton
went on to explain that there is a marked difference between the styli and
between the procedures used in cutting lacquer masters and DMM masters. "In
creating a lacquer master, the sapphire cutting stylus must be heated to
reduce hiss noise during cut ting. The recording engineer must strike a compromise
between too little and too much heat. Too little increases noise, while too
much erases the highest frequencies as they are cut and generates 'horns'
[crests on the groove edges]. Horns degrade the quality and complicate the
production of stampers, and create molding problems at the record press that
lead to waste and higher production costs." Styli designed for lacquer
cutting in corporate burnishing facets which smooth the groove wall for a
quiet cut (Fig. 2) but also erase and distort high-frequency content on inner
diameters.
By employing copper material, eliminating cutting-stylus burnishing facets
and doing away with stylus heating, the DMM process avoids the horns that
can cause the clicks common to lacquer mastering. This simplifies both plating
and pressing of DMM product, since the costly and potentially de grading
horn-removal treatments (polishing/buffing) used in lacquer master production
can be bypassed.
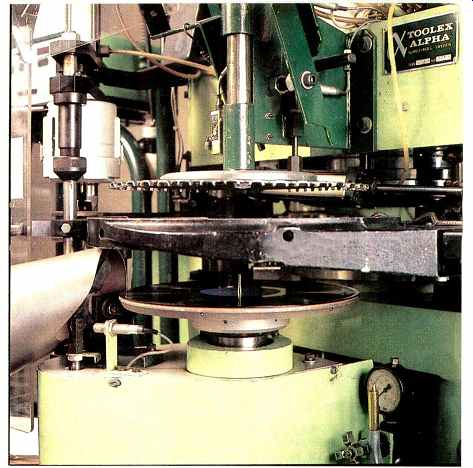
--- Actual pressings of standard LP discs can be out of the press in
less than two hours following cutting of the DMM copper master.
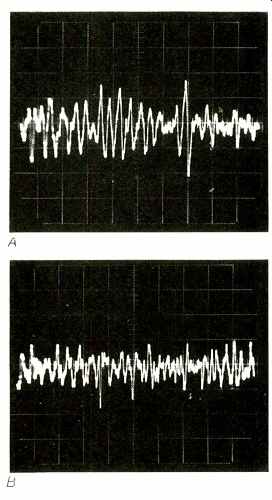
Fig. 8--Rumble recorded on a standard LP test record (A) and DMM test record
(B). Records are DIN 45544 and DMM TP467, respectively.
Although copper as a mastering medium presents significant advantages, it
also presents difficulties to the master-cutting lathe, Shelton observed.
"Despite its apparent hardness, cop per exhibits a viscous-like behavior
in regard to cutting tools, tending to stick to them. Teldec has overcome
these difficulties by imposing supersonic vibrations (mechanical chatter)
in the 60- to 80-kHz range on the cutting stylus, which has a feather edge.
The ultrasonic oscillations also ease the movement of the cutting stylus
through the copper carrier. This action, similar in basic principle to ultrasonic
cleaning, separates the copper chip residue from the diamond cutting stylus
and results in a smooth, gleaming, high-definition groove wall that guarantees
a high signal-to-noise ratio." It
is important to note that while the DMM process is beneficial to performing
artists and the listening public, it also holds important economic advantages
for record manufacturers. In fact, several of the largest European pressing
plants have converted completely to DMM and no longer accept lacquer masters.
The economic benefits include the following:
The expensive, complicated, and hard-to-control silvering and nickeling
processes required for lacquer masters are completely eliminated. Savings
in the plating process alone amount to between $40 and $60 per record side;
The 20% rejection rate common in lacquer master production is reduced to
less than 2%;
Twenty or more stampers can be made directly from a DMM master, with no
reduction in sound quality. Considering that an average stamper has a life
of 1.500 pressings, the DMM pro cess is particularly economical for re leases
of up to 30,000 LPs: and First pressings can be made in less than two hours
after conclusion of the cutting process.
Shelton pointed out that, during the cutting stage, the Neumann VMS 82's
computer translates the preview cut ting signal into lateral and vertical
(groove width and depth) signals for control of depth and pitch. This precise
control increases the potential for additional grooves per record side. In
operation. the computer is. in effect. sampling the preview signal and then
storing, summing, and calculating the next groove position. Often the "land" space
between grooves can be reduced remarkably, to a width of virtually zero,
permitting recording times of up to 40 minutes per side. Additionally, since
the cutting-depth corrections are necessary only for short. lateral signal
bursts. the DMM system permits cuts with a smaller basic groove depth than
in the lacquer mastering process. for better transient response and greater
dynamic range.
Shelton said that an attribute of interest to record producers is that
after DMM mastering and a protective process called "passivation," the
cut-cop per discs have a virtually unlimited shelf life because the amorphous
cop per surface returns to its original crystalline state. "On the other
hand," he added, "the optimum time to plate a lacquer disc after
cutting is more on the order of a few hours. Otherwise, high-end losses may
occur, in addition to pre- and post-groove echo. If a lacquer master is not
plated within one week, it may have degraded to such a point that it is not
feasible to plate it." In a parting comment, Shelton declared, "No
matter how much time and care and effort you put into mastering--be it lacquer
or state-of-the-art DMM copper-the ultimate record quality hinges in large
part on the quality of vinyl used in the final stage. Here at Europadisk,
for our 'Ultimate Audiophile' designation, we use at least 150 grams of virgin
Teldec vinyl to make a dense. elegant pressing at least 30% heavier than
ordinary records. It's equal or superior to any LH pressing made anywhere." The
firm also offers two series weighing in at 130 grams, one called "Audiophile" and
the other "Europa-Classical." Both
use Teldec vinyl.
Notwithstanding all the recent gains in phonographic technology such as
digital sound, DMM, and the Compact Disc, the audio industry has not been
able to annihilate an old bugaboo that has plagued records since their ad
vent, first as Edison cylinders then as flat Berliner discs. et al. That
bugaboo is none other than dirt and grime.
Whether one opts for standard analog, DMM. or CD, there's no choice but
to keep those discs clean!
(Source: Audio magazine, Apr. 1987)
= = = =
|