Removing the Six “Straight Wire” Kinks: Prologue to a Better Preamp
Here are some — perhaps forgotten — tips on preamp design.
I finally needed to replace my “preamp,” which was nothing more than a stepped
attenuator and four jacks in a small aluminum frame. It just didn’t look right,
and was a bit limiting when changing sources. Plugging and unplugging cables
have just too many disadvantages.
It’s often said that the best preamplifier is a “straight wire with gain.”
But I don’t think we should set our sights that low.
Electric circuit theory is a simplification of how circuits behave. Even in
the limited scope of this theory, wire has three characteristics of concern:
resistance, capacitance, and inductance. Many audio effects are not well covered
by this approach— For example, what happens when a semi-conducting crystal
forms in a conductor—but circuit theory is a good starting place.
FACTORS
It may be simplistic to assume that you want the lowest resistance possible
without considering the actual use. The source impedance of most consumer audio
gear is about 100 at low frequencies rising at higher frequencies, designed
to be loaded by at least a 10,000 load.
When you have resistance in the “straight
wire” conductor, there is a loss of signal level. Three feet of 24-gauge wire
loaded by 10,000 has a loss of about 0.0000779dB. Increasing the wire to 10
gauge drops the loss to 0.00000258dB. In audio there are gifted people who
do hear more than others, but not in this case.
The second concern is capacitance loading the signal source. The 3’ cable
loads the source causing a loss of about 0.011dB for low source impedance to
1.16dB with a rising to high source impedance. The phase shift may run from
just under 10 to more than 7° at the upper frequencies.
In the worst case this is something a critical listener could hear. When you
consider that the signal probably goes through two or more cables (they may
be longer than 3’), the signal source probably does not drive capacitive loads
as nicely as pure resistive loads, and the capacitance may even be nonlinear,
then you begin to see where one “straight wire” problem lies.
The issue of inductance is a bit different. Resistive losses don’t vary with
frequency. Capacitive losses increase with frequency, as do series inductive
losses. The difference is that capacitive losses load the source, while inductive
losses raise the load impedance. Inductive losses are also greater at high
frequencies. In the 3’ cable you see a loss of about 0.00785dB at high frequencies compared to 0.00000000785dB at the lowest frequencies. Is it possible some
could hear this? Probably not!
MORE CONCERNS
The next problem of the “straight wire” are the six sources of noise it’s
susceptible to: radio frequency interference (RFI), capacitive coupling, magnetic
coupling (or mutual inductance), common source impedance, vibration, and moisture.
I treat RFI as a separate source because it’s usually from a far-off source.
In reality it’s a combination of capacitive coupling and magnetic coupling.
The cure is to shield the wire and gear, even though that adds capacitance
and signal loss. Shields also have the problem known as skin effect—the lower
the frequency of the RFI, the farther it can penetrate the shield. RH often
shows up as added noise or grit to the sound.
Capacitive coupling of noise can be treated by field theory or approximated
by circuit theory. For the circuit theory approach, assume there is a small
capacitor hidden in the circuit that couples the “straight wire” to the noise
source. You can also model a capacitor to ground from the conductor and even
allow for some attenuation from a shield.
Magnetic coupling depends on the area of the conductor and strength of the
field. Moving the power transformer away from sensitive areas is always a good
idea. Making circuit paths shorter also provides benefits. If the “straight
wire” is a real cable grounded at both ends, it’s almost certain that you will
have a magnetically induced voltage.
Common source impedance is why lights flicker when a motor starts. When the
desired signal shares a signal path with something else, the other signal causes
a voltage drop in that path. If the other signal varies—say, from noise or
even signal—that variation and its companion voltage drop shows up in the signal
path.
Vibration is always present. Insulated wires will have triboelectric noise.
Capacitors will react by modulating the spacing between electrodes and hence
their capacitance, resulting in an AC voltage from any bias placed across them.
Inductors may have movement in their windings, causing value shifts. Even some
resistors may generate noise from movement.
Moisture, of course, can cause corrosion. Whenever two different metals touch
and moisture is present, you produce a small noisy battery. Many folks find
always leaving their gear on makes it sound better. Some of this is due to
heat reducing the moisture in components such as resistors and capacitors.
Both are affected to a small degree by moisture. Of course, the biggest problem
can occur in switches, where the moisture may cause oxidation of the contacts.
Sulfur or other compounds in the air make this even worse.
The final issue in the “straight wire with gain” is gain. If you are using
an iPhone, CD player or tuner as your music source, both of these are capable
of delivering 1V RMS. Some high-powered professional amplifiers will produce
fill power with less than that. Even a low gain (26dB) power amplifier will
deliver 50W with that input. So for many cases you don’t need gain— you need
loss! Of course, if you have inefficient loudspeakers or perhaps want tone
control, then you may want some gain.
SHIELD SOLUTIONS
It’s misleading to think of gain as only voltage amplification. You may wish
to increase the current available to the load. This helps to reduce the effect
of capacitance or other loads inside the power amplifiers or connecting cables.
It turns out there is a nice simple solution that will almost completely eliminate
capacitive loading of interconnecting cables, increase the effective attenuation
of the shield, and add almost no noise of its own.
That solution is the driven shield. In stead of surrounding the signal carrying
wire with a grounded shield, use one that carries the same signal! Now the
capacitance is not to ground but to the same voltage. The insulation can be
nonlinear, because there is no voltage across it, no nonlinearity. The inductance
of the wire is very slightly reduced by solenoid effect and some reverse capacitive
coupling, although this is not really of practical value.
For RFI the interference now must travel through an extra isolated shield,
so this one change multiplies the loss of a single shield. Same deal for any
capacitively coupled noise.
To get even trickier, you can now cover this shield with a second insulated
shield, which will prevent the signal from inside leaking out and contaminating
the ground or return reference signal. If you twist a single conductor wire
around this second shield and use this as the ground reference, this will help
to reduce magnetic coupling. You get some of the advantages of a balanced line
in the single-ended cable.
Of course, to keep the RFI out of the ground, you should add a third shield.
To minimize the undesired energy, the second and third shields are grounded
only at the driven end. This prevents mutual impedance of the shielding system
from entering the signal path.
You can add a buffer amplifier at your source to power the driven shield.
Of course, if you don’t want to modify your existing gear, an easier way is
to put all the buffers in a new preamp. The buffers need to be decent, but
not great amplifiers. After all, they will be attenuated by the amount that
used to be ad equate just for noise. This is a good place for amplifiers such
as the TL072 or any FET input amplifier, because they are less susceptible
to RFI. Of course, you probably can even get away with a gold en oldie such
as an NE1558. I mixed them up to see whether I could hear a difference.
In my design I used several small cards to become input or output circuits
( Fig. 1). The sending source can be a CD player, DVD, tuner, and so on.
I designed two versions of the buffer card. One is a send card designed to
bridge the output and provide a modest current signal to the first active shield.
It also tries to make sure all common mode currents are accounted for properly.
It does this by grounding the source of the active shield’s current at the
source. The return signal wire, which was the ground and shield in a normal
cable, is now just a wire going to the common of both connectors. The final
outer third shield is there to try and scare RFI away.
The send card can take either a direct wired input or a signal from an optional
RCA jack. The output is on a stereo 1/4” jack with a case grounded binding
post for the outer shield. The connecting cable has a matching ¼” stereo phone
plug and a wire lead on one end and a standard RCA on the other.
The receive version of the card works by making it easier to literally suck
more signal from the source. It requires a special cord that has an RCA plug
for the input and a phone plug for the output. The received center conductor
signal is buffered and sent backwards on the active -shield. The next shield
is now grounded at the receive end, where the induced current originated. The
outer shield is connected to the send side be cause any noise from an outside
source is best dealt with from the stronger signal side. However, the receive
end of this shield is connected to the case through a small capacitor.
The capacitor to the case keeps any RFI shielded, or at least all of the components
at the same potential inside a Faraday cage. There is also a capacitor (C4)
from the buffer common to the case.
PARTS SELECTION
One problem quickly showed up. It seems that some designers have tweaked their
designs to work into a capacitive load! Some outputs are of such high impedance
that the shield buffer acts as positive feedback. So placing a small capacitor
47 to 330pF silver mica (C1 and C2) between the signal lead and buffer / preamp
common when needed will restore the source signal to flat.
A second problem is that a rail-to-rail op amp does not want to work into
a capacitive load, so don’t use one.
I used gold-plated Neutrik NRJ6HF- AU phone jacks for the 1%” phone jacks.
These come without mounting nuts, so be sure to order some. They fit nicely
into a 0.46” hole. Neutrik also makes gold-plated NP3Xb phone plugs. I did
not use anything fancy for the third shield binding posts.
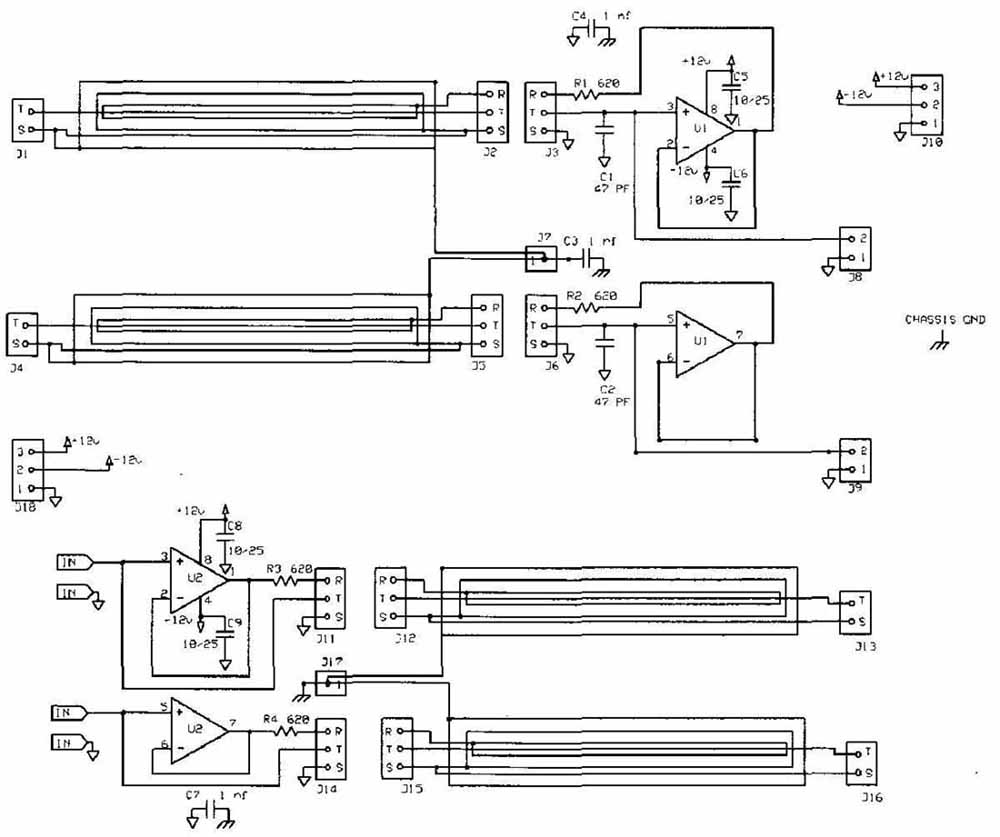
Above: Fig. 1: Input and output shield drivers.
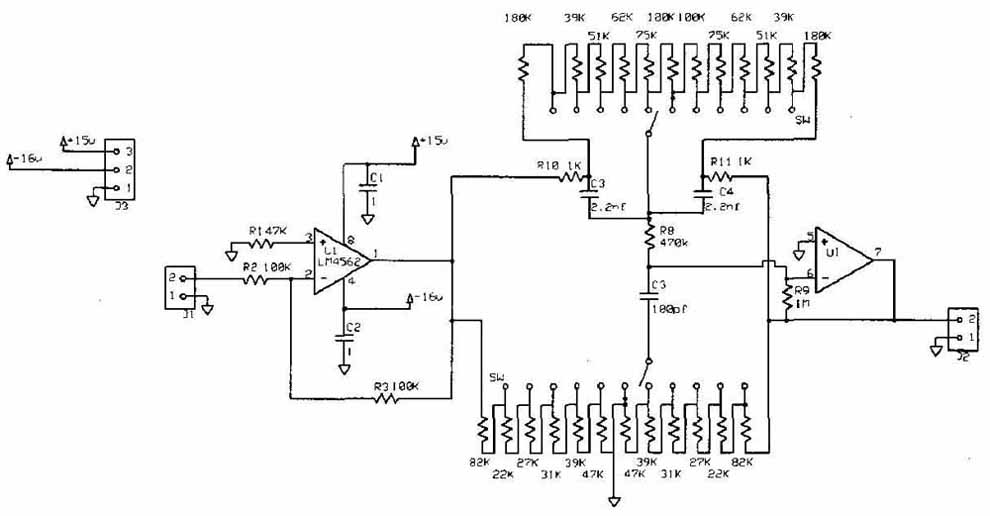
Above: Fig. 2: Tone control circuit.
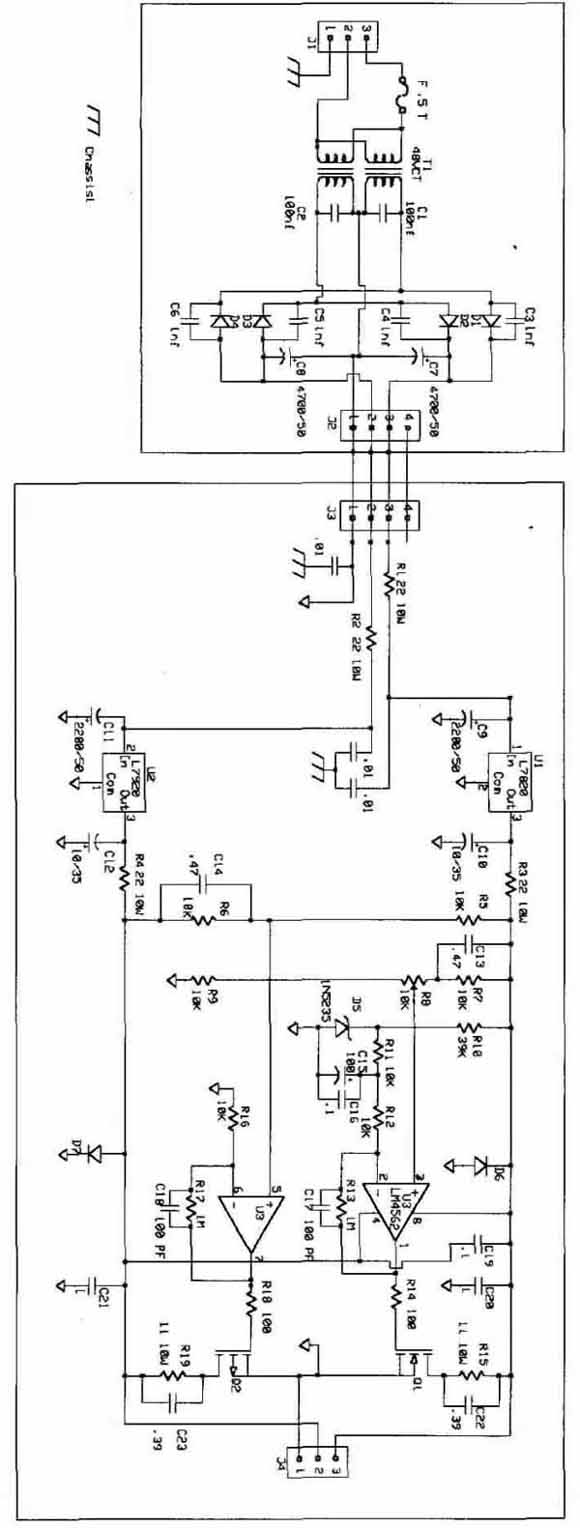
Above: Fig. 3: Power supply regulator.
For the RCA connectors I tried three different types: all gold-plated audiophile
types. You can pick your favorite here; just be sure it can handle a large
diameter cable.
To construct some of the cables I used silver or silver-plated stranded Teflon
insulated wire. For others I cheated and started with a piece of shielded audio
cable cut from a decent premade RCA- RCA cord. The quality of the signal conductors
does affect the final product. I have found that thinner better metals do have
an advantage.
The shield braid used to be a common item. I could only find it in the larger
size at McMaster Carr (part #5537K26 and 5537K14).
I used a third-hand jig to hold the connector and cable while soldering. I
did not want any motion while the solder cooled because theory suggests that
this promotes crystal formation.
After soldering the RCA end center silver 22-gauge conductor, I slipped over
½” heat shrink, cooked it, and then placed the rear cover. Next to go on was
a thin shield braid that did not quite extend into the cover. I added a small
jumper connected to this at the non RCA end. Tape kept it in place so it would
not short to the center conductor.
A layer of ½” heat shrink that did go into the cover was next. More thin braid
went over this, but again not into the cover. The jumper went to the RCA end
for the send cables, the far end for the others. I wrapped a silver or silver-plated
insulated wire around this and soldered it to the shell terminal. If this is
a send cable, you need to connect the jumper and a short bit of uninsulated
wire. The next piece of ½” heat shrink covered this.
I connected the phone plug to the other end. I needed to cut the strain relief
short and ream it a bit to fit the cable. The larger shield braid goes over
the completed connectors, and then trimmed and soldered to the appropriate
jumpers. A bit of tape held this in place and Techflex tubing in red or black
covered the outer shield. This was held in place at each end by more ¾” heat
shrink tubing that also covered the rear shells of the connectors.
It was easy to push the braid and Techflex over the cable, but the heat shrink
sometimes was difficult. It was easier to push a stiff wire through the heat
shrink and use it to pull the cable through. On long runs you can use a brass
wire and solder it to the silver wire. After you clean the connectors with
De-oxit, the cables are complete.
Of course, if you are using audio cable for the core, you can skip a step.
I positioned the send and receive modules so that two receive and one send
fit on an Expresspcb mini-card. There is nothing special about the cards, which
don’t handle high-quality signals. I did isolate their power supplies from
the audio circuits by using two 10-ohm resistors for each card.
You can use the cards and cables as standalone devices. I used one as a guitar
cable buffer, which resulted in noticeably better high end. I also chose to
build these cards into my new preamp.
In my preamp the signal lead from each input card goes to a selector switch
via a piece of un-insulated dead soft silver wire, which is attached to nylon
standoffs to minimize vibration-induced signals. I used a 12-pole double throw
(12PDT) rotary switch for the selector. It’s a military surplus silver-plated
large diameter ceramic rotary switch. I treated the contacts with Deoxit. The
signal return or “ground” leads from each input go directly to the output send
buffer card, where I establish my common ground reference point. A better point
would be at the return end of the attenuator, but I did not figure that out
until I finished.
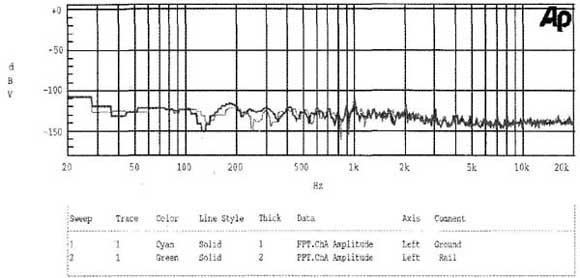
Above: Fig. 4: Power supply top input, middle after regulator, bottom after
shunt regulator.
The output of the selector switch goes to a stepped attenuator. I had a leftover
24P4T Alps switch made for this purpose. I made PC cards to hold 1206 size
1/3W surface mount resistors, a size that can be soldered without magnification.
I used 94 of the IRC PFC-W1206LF- 03-XXXX-B tantalum nitride 0.1% 25 ppm/C
non-magnetic resistors to make the attenuator. I selected these because as
high-end audio parts go, these are reasonably priced. I like the 1206 size
because they are easier to solder. My attenuator has 10K input impedance and
varies on the output. I learned from my previous “preamp” that most of my listening
is done about 20dB down, so I jiggled my step sizes to have more resolution
in that range.
After doing all this, I realized next time I will buy an attenuator already
assembled, which is easier, works the same or a bit better, and actually costs
less! The output of the attenuator originally went to the output card. An outboard
±36V DC power supply fed an internal shunt regulator to power the buffer cards.
A direct run went to each card establishing a second common ground at the power
supply, reducing any mutual impedance signals. A single connection coupled
the output card to the power supply.
I used a shunt regulator modified to have more AC response; in this use with
a known load and good shielding, RFI should not be a problem. Measurements
showed the shunt had more than 20dB additional noise attenuation than with
just the regulator. The power transformer, bridge rectifier, and first filter
caps are in a small steel box 6’ away from the rest of the gear.
The downside of this shunt regulator is that it draws a higher startup current
than a series regulator. So it’s best to use a time delay fuse.
TONE CONTROL CIRCUIT
You need a tone control to complete the preamp. The tone control was actually
the trickiest part. In the late 70s, when mixing boards were becoming common,
the tone control issue re-emerged. Initially it was more a question of how
to make an effective low-cost tone control, but once the knockout punch was
published by P. J. Baxandall in 1952, there was only quibbling about variations.
By the 70s, with cheap parts, ICs, and biquad or other new filter topologies,
the issue became how should the knob change the sound?
The problem now was not so much designing the circuit, but getting the “feel”
right. When you give the bass knob a quarter turn, you expect certain changes.
More or less change is awkward. As loudspeakers improved, the apparent effect
of the control was greater.
What was once a fine treble control now is too harsh on a modern tweeter.
A bass control that was fine on a tight suspension woofer becomes tabby on
many around today.
The standard Baxandall circuit for a two-knob tone control is three capacitors,
two variable resistors, and a few fixed resistors. To get smooth action the
controls needed to be linear. A later takeoff used log pots and different capacitor
values to get a better feel. The disadvantage of the Baxandall was that it
required a center-tapped pot and a pentode to provide the negative feed back.

Above: Fig. 5: Not so good DIY cable top, bottom preamp and cables. Note
HF rolloff and noise level hides THD inherent in test equipment.
Above: Fig. 6: Tone control curves.
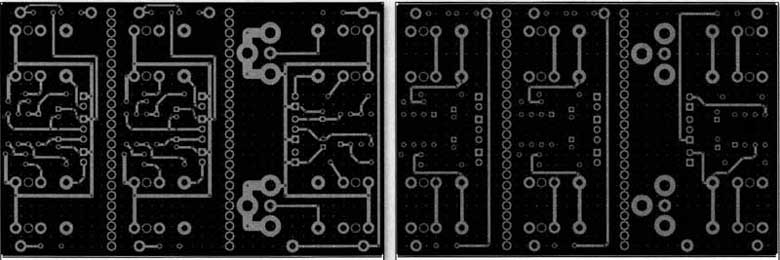
Above: Fig. 7: Bottom PC layout.
Above: Fig. 8: Top copper layer.
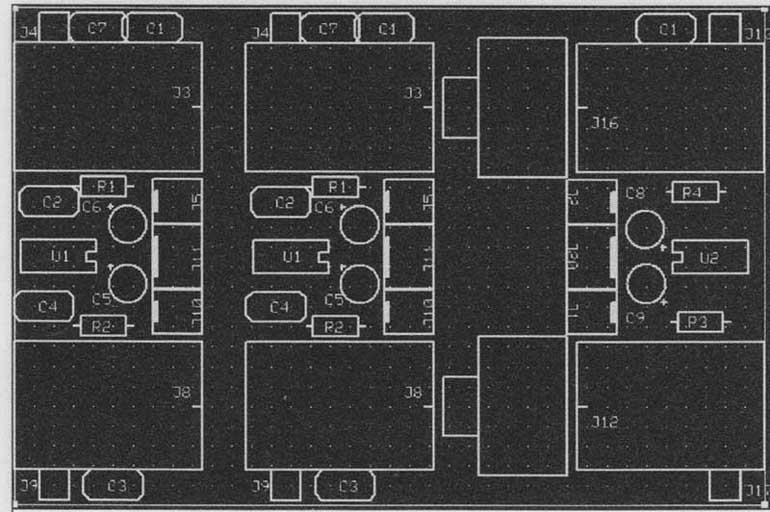
Above: Fig. 9: PC cards silkscreen layer.
Today negative feedback is not a novel application. Stereo, however, has placed
a few more demands on a tone control. A stereo potentiometer with good tracking,
high resistance, and a center tap is really hard to find. Using switches and
resistors gives me a great advantage. I can select the resistor values to give
me logarithmic control and still use matching capacitors.
I used regular carbon film resistors for the control switches. Once my crew
and I have used the control a bit, it will be practical to home in on the useful
range and pick exact values. Then I will change to better switches and resistors.
The circuit I used is deliberately very close to the original design and is
shown in Fig. 2.
I used an LM4562 op amp, silver mica capacitors, and precision resistors for
the tone control cards because I need to only change the switches later. The
PC cards for the tone control are stacked on top of each other to maintain
a similar level of wire lead path length and vibration level.
To keep out vibration I made some feet out of two aluminum discs and two different
foam rubbers. Both are quite soft—40 00 durometer for one and a bit firmer
for the other. The impedance mismatch helps to reduce vibration. I mounted
the feet to a sub-plate ½” deep and added a bit of foam to seal this chamber
to the chassis. I used 6-32 screws with pieces of auto store ½” ID rubber hose
as flexible spacers to attach the plate.
I punched a 1” matrix of holes in the bottom of the chassis to make mounting
components easy. The sub-plate now sealed the chassis. Inside was silica gel
to keep moisture down and as a bonus the loose fill absorbs vibrations. The
final environmental control was a strip of silver tarnish paper to remove sulfur
and keep the silver shiny new.
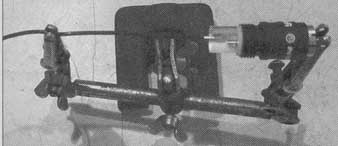
PHOTO 1: Helping hand holding parts to be soldered.
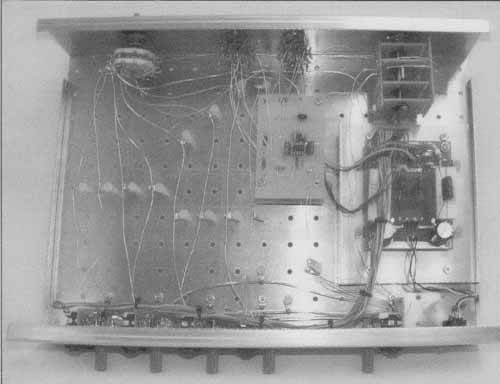
PHOTO 2: Chassis wiring.
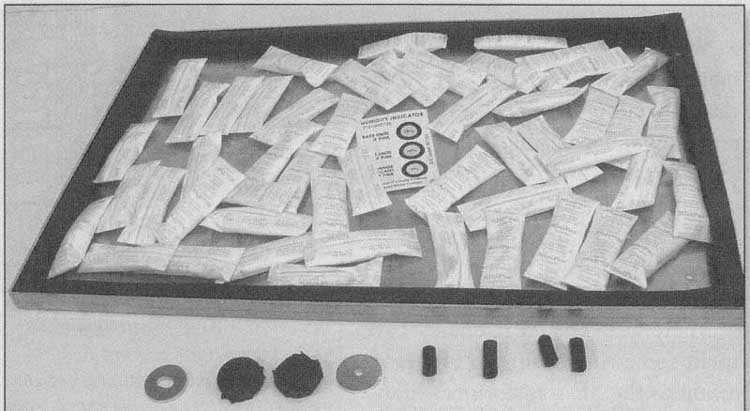
PHOTO 3: Bottom pan with gasket and silica gel, foot parts, and rubber tubing
spacers.
RESULTS
Measurements of the preamp showed that it was actually better than one web
DIY cable design. It was as good as a jumper cable across the test equipment
for most of the audio band. There was a higher level of 60Hz hum than from
a short jumper. This was interesting because the fundamental of the power supply
was 120Hz, which was 105dB down at the output of the regulator. So I suspect
this is due to the longer cables and greater area in the possible magnetic
field.
When I first turned on the new pre amp, I heard a noticeable buzz in the sound.
Then I realized the preamp was set to tuner for a sports-talk station. The
buzz was just normal for them! On everything else the system seems dead quiet.
So it’s possible to do better than a “straight wire with gain.” You can have
less noise, lower losses, higher output current, selection ability, gain, and
tone controls.
|