(source: Electronics World, Apr. 1968)
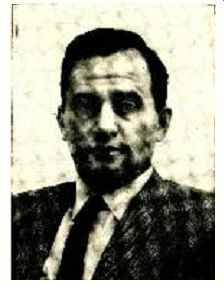
By BENJAMIN BARRON /former Director of Engineering Data and Controls Div.,
Lear Siegler, Inc.
The author received his MEE from Polytechnic Institute of Brooklyn in
1952. His major field of interest has been in solid-state control and
servo systems. He has developed various d.c. and a.c. power conditioners
for military and aerospace use. He is now Director of Research and Development
for Cox & Co.
Guidelines in selecting and specifying the proper d.c. to
a.c. inverter and d.c. to d.c. converter, along with precautions in
using and designing these sources.
A POWER inverter or converter converts d.c. to a.c. at some point in
its operation. The power inverter delivers an a.c. output that is either
sinusoidal or some type of switched wave. The power converter, usually
called a "d.c. to d.c. converter ", converts d.c. to a.c., transforms
the resultant a.c. voltage to another level, and then rectifies and filters
the waveform to produce a new d.c. voltage, differing in value from the
input d.c.
The inverter may also be used to convert a.c. from one frequency to another.
In this case, the input a.c. is first converted into d.c., usually by
rectification; then the d.c. is converted into a.c. of another frequency,
which is used as output.
Before the advent of power transistors and silicon controlled rectifiers,
methods for converting d.c. to a.c. were mechanical, either through the
use of mechanical vibrators, motor-generator sets, or power vacuum tubes,
thyratrons or ignitrons. Most of these systems were characterized by short
life, unreliability, or inefficiency. With the advent of aerospace programs,
the need for lightweight, efficient inverters developed. The solid-state
or static inverter came into being and has since found application in
many other areas.
The most commonly used solid-state devices are SCR's or switched power
transistors acting as the power converting elements. This article deals
exclusively with circuits using these devices.
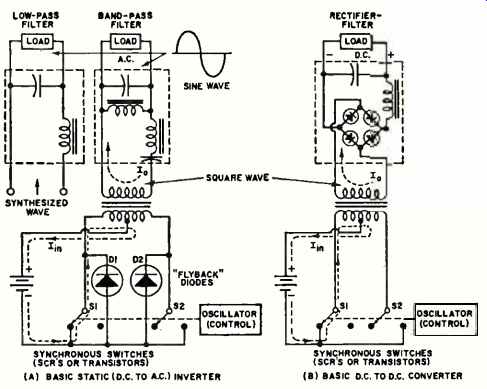
Fig. 1. Basic configurations of (A) inverter and (B) converter.
Direction of electron current flow is indicated by dashed arrows.
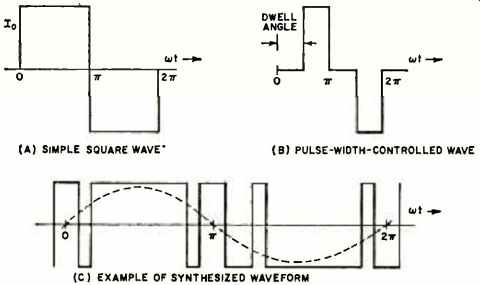
Fig. 2. A number of typical switched waveforms are shown here.
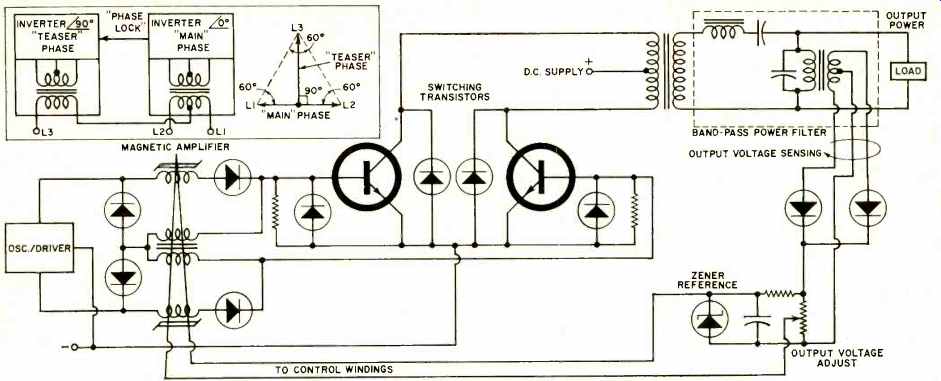
Fig. 3. Simplified schematic of single-phase, pulse-width-controlled
inverter with regulation and sinusoidal output. Inset circuit shows how
two such inverters can be employed to produce 3-phase output.
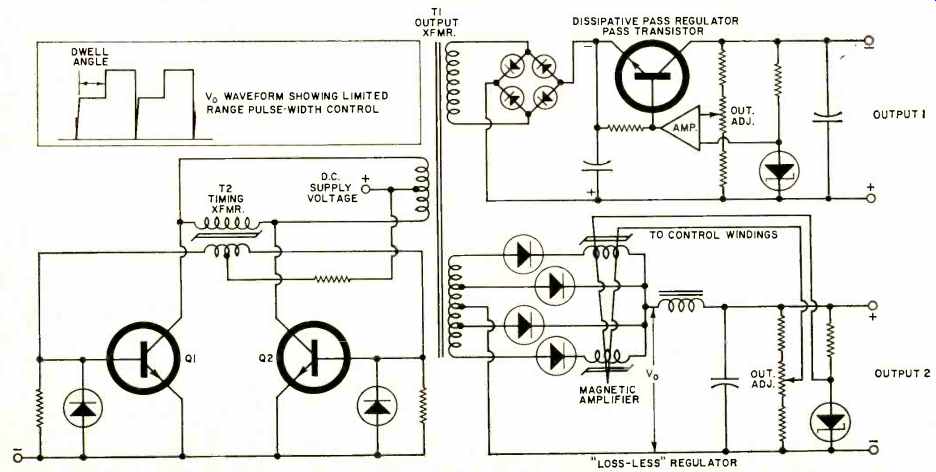
Fig. 4. Self-oscillating d.c. to d.c. converter followed by a dissipative
pass regulator and "lossless" regulator.
Applications of Inverters, Converters
In the missile and satellite fields, static inverters are used as precision
a.c. supplies for gyroscopes, accelerometers, synchros, servo controls
for guidance and attitude controls, and synchronous motors for timing.
In military or industrial areas, static converters are used for: battery
or fuel cell-powered emergency supply to critical systems in the event
of power-line failure; sonar transducer and driver supply; antenna spinner
supply; precision a.c. power for remote clocks; frequency changers for
operation of high-speed machine tools; a.c. sources for automotive and
marine use; and high-frequency a.c. lighting from d.c. or low frequency
sources.
D.c. to d.c. converters are used in missiles and satellites for the conversion
of d.c. to one or more isolated levels to be regulated and conditioned
in order to power delicate controls and sensing systems. Large converters
are used for solar-powered ion engine drives. In military or industrial
areas, converters are used for high-frequency, lightweight, high-efficiency
power supplies; for portable battery-powered equipment; and in fuel-cell
converters and regulators. Converters are used to permit battery operation
of portable electronic devices, such as television systems, instruments
and recorders, and miniaturized computers and displays.
Operating Characteristics & Circuit Designs
Silicon controlled rectifiers and transistors, when used in the switching
mode, have three inherent characteris1 tics that make them suitable for
use in the static inverter and d.c. to d.c. converter. They have very
low resistance when turned "on" (low forward drop) , very high
impedance when turned `off" (low leakage) , and they change state
very rapidly. These characteristics result in high conversion efficiency
and good load regulation. High reliability is inherent because static
inverters and converters have no moving parts, they require no high-temperature
heaters in their operation, and the semiconductors are mechanically rugged.
Properly designed units, with sufficient protection systems built into
them. can stand abuse and mishandling. It can be assumed that they will
outlast the systems they are powering.
Both the static inverter and converter use semiconductors as switching
elements to alternately connect a load to a d.c. source. Fig. 1 shows
the basic configuration.
S1 and S2 represent switching transistors or SCR's that are driven from
an oscillator. As can be seen, the input current, Ii,,, is first connected
to one half of the transformer primary and then to the other. As a result
of this action, the output current from the transformer I. keeps alternating
its polarity in synchronism with the driving source oscillator. S1 and
S2 may be simply switched "on" and "off," with 180°
duty cycle, to produce a simple square wave output. Control of the output
can be accomplished by delaying the action of the switches so that the
second switch does not come on immediately after the first is turned off.
The period of time that is delayed is called the "dwell angle ",
as is shown in Fig. 2.
When a sinusoidal output is required from a static inverter. the resultant
square wave can be fed through a passive band-pass filter. Other methods
are used to produce sinusoidal waveforms. For instance, Si and S2 can
have multiple switch actions to produce the quasi-square waveform of Fig.
2C. This is then applied to a low-pass filter. The flyback diode is used
here since it is essential to provide a path for reactive current back
to the d.c. source. Such current will occur when the load is reactive.
Since the current cannot flow back through the SCR's or switching transistors
when their anode or collector voltages are reversed. an alternate path
must be provided through the diodes.
In the case of the d.c. to d.c. converter, the square wave is rectified
and filtered. If simple pulse-width power control is used, a choke input
filter is required.
Fig. 3 is an inverter for aircraft and missile application.
A nuclear-radiation-hardened version is shown on the cover of this issue.
The power transistors are switched "on" and "off" by
base-to-emitter voltages generated by the oscillator-driver. Magnetic
amplifiers are provided in the base circuits of the pair of switching
transistors. In this manner, the transistor switching as well as the dwell
angle are controlled from a single source. The amount of dwell angle is
controlled by output voltage feedback to the zener diode circuit in order
to provide the desired output voltage regulation. The resultant pulse-width-controlled
wave is filtered to produce a sine :wave output at the load.
It was further desired to obtain three-phase power. To accomplish this,
two similar inverters are used and phase locked 90° apart. By suitable
interconnection using the "Scott T" configuration, the two phases
are combined to produce three phases.
Fig. 4 shows a self-oscillating d.c. to d.c. converter followed by two
kinds of post regulators. Timing transformer T2 is designed to saturate
readily. The phasing of this transformer is such that the secondary feeds
back positively to the bases of Q1 and Q2. The frequency of oscillation
is governed by the number of turns, the magnetic properties of the core
material of T2, and the value of line-voltage input.
Output #1 is used where d.c. with precise voltage regulation and low
output impedance is required. For precise regulation with limited range
for the output impedance characteristic, a "loss-less" stepped-wave
controller is used (output #2) . The dwell angle produced by magnetic
amplifier control over a limited range produces the stepped waveform shown.
This type of operation reduces the amount of output filtering required
and thus optimizes the response attainable from the pulse-width controller.
The output is sensed and compared to the reference zener diode and fed
back to the control windings of the magnetic amplifier to accomplish the
desired voltage regulation.
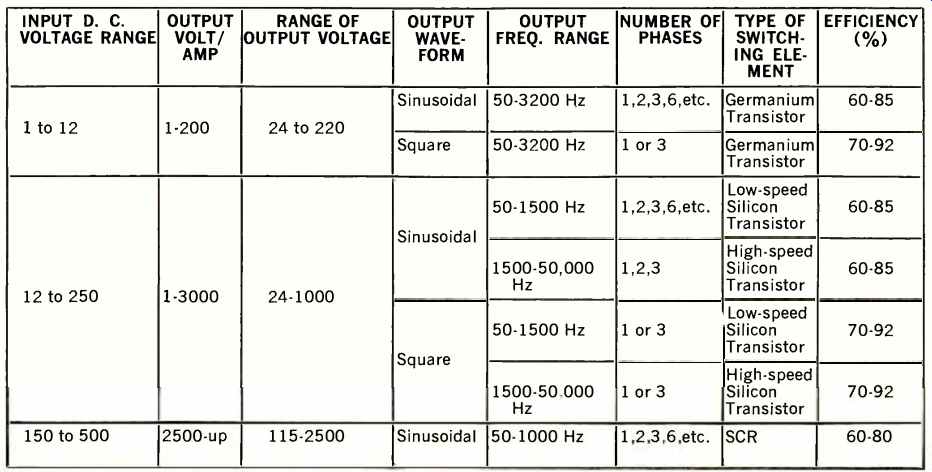
Table 1. Performance characteristics of static inverters with a wide
range of inputs and outputs.
Important Precautions
There are certain precautions to be followed when applying inverters
and converters to systems.
1. Adequate cooling: Often the user is vague as to the actual method
he intends to use to remove heat from the unit. Some method must be decided
upon long before the system is installed. Conduction cooling is done by
bolting the device to a surface from which the heat will be removed in
some manner (such as with a heat sink) . Thermal characteristic in degrees
rise per watt of dissipation into the heat sink must be known and taken
into account.
If self-cooling is contemplated, determine if convection cooling is adequate.
For inverters over 100 watts. it is usually not adequate. Cooling by radiation
is usually useless. If fans are to be used, it should be noted that cooling
decreases rapidly with altitude. It is best to select the fan for the
maximum altitude condition.
2. D.C. input lines: Such lines are usually highly reactive.
Contrary to the usual assumptions, batteries and d.c. generators are
not low-impedance sources for high frequencies.
Furthermore, the inductance of the power line between the d.c. source
on the unit is not negligible. The power switching elements pull current
from the power line in surges at twice the output frequency. This can
give rise to damaging transient voltages on the unit input. In almost
all installations, a large capacitor should be included across the d.c.
input terminals of the inverter or converter.
Often, it is best to build the line-stabilizing capacitor directly into
the unit.
3. Germanium vs silicon transistors: Except for low voltage applications,
always use silicon power switching transistors.
4. Grounding: Power switching devices are electrically noisy. They are
usually a.c.-coupled to the chassis through the capacitance of the heat-sink
insulator and through transformer and wiring magnetic fields. Consequently,
short-duration pulse voltages, called "needles ", tend to appear
in the outputs of d.c. to d.c. converters. If at all possible, ground
the systems to the converter itself.
This is very important when the intended use for the d.c. to d.c. converter
is for high-speed digital circuits. Grounding at the converter will greatly
reduce these disturbances.
5. Skill of personnel: It is obvious that as the skill of personnel
decreases, the chances for mishandling and thus damaging the units increase.
This should be taken into account. Careful attention should be given to
the specification of the protection systems that must be built into converters
and inverters for such use.
6. System discipline: Because of habit, sinusoidal sources are often
specified for transformer-rectifier power supplies, the sinusoidal power
being produced by a static inverter.
If the ultimate need for the a.c. is for a set of d.c. supplies, either
produce the various d.c. levels directly within the d.c. to d.c. converter
or supply a pre-regulated square wave to the a.c. distribution system.
Maintain control of the d.c. levels required for the circuits being designed
by various engineers for later integration into an over-all system. Lack
of design discipline usually results in the creation of unnecessarily
complex power systems. Multiple-output d.c. to d.c. converters, with the
necessary output characteristics, often become nearly as complicated as
the systems they are powering. Their cost becomes a significant percentage
of the over-all system cost. Whenever possible, the systems manager should
specify a minimum number of available d.c. levels before circuit design
commences.
7. Specifying: Do not over-specify the output power of inverters or converters.
It is a common error for users to assume that an inverter or converter
will run much cooler when operated at reduced loading. Losses in a properly
designed device vary from about 1.5 to 1 in going from full load to no
load. Safety factors are put into the devices when originally designed.
Do not call for more accuracy or less distortion than is actually required
for the system. Proper specifications result in savings of power, weight,
and cost.
Guidelines for Specifying
The following is a list of the critical parameters that should be included
when selecting or specifying static inverters (see Table 1) or d.c. to
d.c. converters.
A. Output Static Inverter.
1. Volt-amps: minimum, maximum
2. Power factor variation: Minimum, maximum
3. Output frequency: Minimum, maximum. Stability with line, load. temperature,
time.
4. Phase: Number needed. tolerance with load unbalance, phase stability
with line, load, temperature.
5. Output waveforms: Square: Rise, fall times, flatness, symmetry. Sine:
Distortion in percent, maximum percentages for various unwanted harmonics,
crest factor.
6. Transient response: Line, load steps.
B. Output-D.C. to D.C. Converter
1. Number of outputs required: Isolation between outputs to ground.
2 Output voltage: Variation of set-point stability with line, load, temperature,
time.
3. Output current: Minimum, maximum, ripple content, step variation.
4. Ripple, noise: Maximum in peak-to-peak. Bandwidth to be observed.
5. Transient response: Line, load steps, overshoot, undershoot. and recovery
time.
C. Input D.C. Line Voltage: Minimum, maximum, transient surges, line
impedance for various frequencies allowable, reflected noise from the
inverter back to the line (See the appropriate MIL-Spec, if it is given.)
D. Mechanical: Size, weight, required shape, connectors.
E. Protection: Overload, short-circuit, overvoltage, reverse voltage,
over-temperature.
F. Available Cooling: Self-convection, heat sink, fan or air blast, liquid.
Define the method.
G. Environment: (See MIL-Spec, if given.)
1. Temperature: maximum, minimum operating and storage. Allowable warm-up
time.
2. Shock: Impulse height, shape, time duration, number.
3. Vibration: Sinusoidal, amplitude vs frequency, duration at various
frequencies and axis.
4. Random: Bandwidth, spectral content.
5. RFI, EMI: (See MIL-Spec, if given.) Limits of conducted, radiated
for various test frequencies.
6. Altitude: Temperature vs altitude.
POTENT POWER PACKS
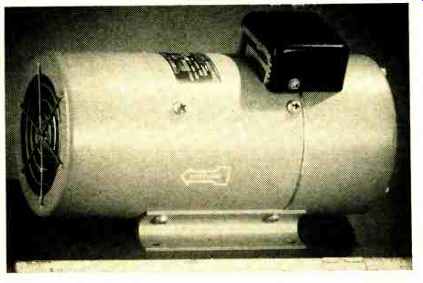
IT is the package that counts, in the air and on the ground.
The problem with most high-current power conversion equipment is that
it is bulky, heavy, and hard to manage. In airborne systems particularly,
power units often take up most of the available equipment space. One of
the companies specializing in reducing the size of power packs is the
Tung-Sol Division of Wagner Electric Corp.
The 100-ampere ground power (GP) supply in the photograph is ultra lightweight
and compact; it weighs less than eight pounds and is only 8 1/2" l.
x 4" w. x 5 1/8" h., although it handles more power than some
units twice its size.
Physically, the ground power unit is similar to the airborne version.
The cylindrical housing and circular heat sinks, which are constructed
of rigid extruded aluminum, enable the power supply to be mounted in any
position. An internal blower and a modified pressure cooling system is
used to dissipate heat.
Basically, the circuit is a double-Y delta transformer with silicon rectifiers
which operate from a 120 /280-volt, 400-Hz, 3-phase a.c. input. Original
equipment manufacturers can obtain ground power units having outputs of
28 volts at 100, 200, 300, and 400 amps. Twenty-eight-volt airborne units
are available with output currents of 50 to 200 amps. A similarly constructed
60-Hz, 50 to 200 amp unit for portable field use will be introduced.
Communications equipment manufacturers who prefer rack mounted supplies
can use the CR 27.5 series of high-current d.c. units. These solid-state
controlled magnetic amplifiers were developed especially for marine single-sideband
systems. They have a highly regulated (better than 1 %) voltage output
of 27.5 V and currents of 25 to 150 amps, and operate from a 50/60 Hz
line.
IF it's modules the equipment manufacturer needs, he might try the LC
solid-state power packs developed by Electronic Research, Inc. There are
five models which cover current ranges of 0-750 mA, and 01, -2,-5, and
-10 amperes. Each individual module can be set to any desired output voltage
in the 4-32-volt d.c. range.
The LC modular power packs incorporate special circuitry to take full
advantage of the properties of silicon semiconductors. The regulator is
a silicon transistor emitter-follower circuit in series with the rectified
and filtered d.c. source. The series regulator is controlled by a feedback
amplifier loop which is referenced to an independent constant voltage
source. Changes in the output voltage caused by load variations are compared
with the constant voltage source and amplified error signals control the
emitter-follower in such a manner as to compensate for the load and line
changes. In order to obtain the sensitivity necessary to provide closed-loop
regulation, stabilized gain stages are utilized in the feedback loop.
The sensing source at the output of the regulator is a bridge circuit
with one of its arms containing the constant voltage reference. The referenced
voltage is, in turn, provided by an independently controlled zener diode.
The modular supplies range from 4" x 4" x 6 1/2" h. to
8 3/4" l. x 9 1/2" w. x 7 1/4" h. The a.c. input and d.c.
output connections are made to terminal strips. Voltage and current adjustments
are made on transformer voltage taps and slotted screwdriver adjustments.
All models operate at 105/125 Hz, but 400-Hz operation is available by
means of a simple tap adjustment.
|