(source: Electronics World, Apr. 1968)
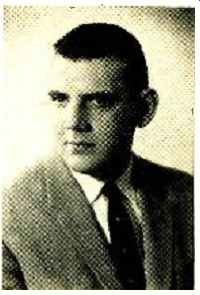
By PAUL S. BIRMAN /Applications Engineer, Kepco, Inc.
The author is engaged in the development and marketing of d.c. regulated
power supplies. He is the author of the "Kepco Power Supply Handbook" and
various magazine articles on regulated power supplies. Prior to his association
with Kepco, he served with the Army Ordnance Corps, attached to the Army
Rocket & Guided Missile Agency (AROMA), Research Branch, at Redstone
Arsenal, Alabama. Preceding this service, he did circuit design in d.c.-d.c.
power supplies with Universal Transistor Products Corp. of Long Island.
He holds a BSEE from the Polytechnic Institute of Brooklyn.
The feedback circuit of the regulator section is well suited
for use in adjusting the supply's output. Such adjustment, called
programming, may be done either locally or at a remote location.
REGULATED power supplies are often used in circuits and systems where
the ability to control, vary, or modulate the output is required. A remarkable
property of the regulator section of the modern power supply is that its
feedback mechanism is just as well suited to the problem of control as
it is to the maintenance of a constant output voltage or current. The
process of varying a power supply's output is called programming.
The output of many power supplies may be programmed by varying a resistance--or
a conductance--or by applying a signal voltage or current. These, in turn,
may be shaped or controlled by a variety of function generators, motor-driven
devices, or may be output-related to the power supply itself to close
a feedback loop.
In general, programming is limited to those power supplies whose design
does not depend on mechanical aids to dissipation limiting. For example,
units employing variable autotransformers as part of their control will
normally be incapable of electronic remote programming (except by the
use of motor-driven or similar mechanisms) . Similarly, some power supplies
that employ range switching-where that switching involves transformer
taps-will usually be limited to external control within the span of any
one range.
Error sensing is also provided with most precision power supplies to
allow the equipment to feed back its corrective signals over a wire path
separate from that used to deliver current to a load. This allows a power
supply to include the drops in its load wiring as part of its own internal
resistance, joining, among other items, the transformer resistance and
rectifier drops. The process of compensating for an unwanted drop in the
load circuit may be considered a form of restricted programming in which
the supply programs itself by the needed amount. Even power supplies using
mechanical control and otherwise not considered programmable, will have
a 0.5 to 1-volt programming range for the sensing circuit. Simpler power
supplies lacking feedback control mechanisms will, of course, not have
even the degree of programming needed for remote error sensing.
Analysis of a power supply in terms of its signal flow rather than its
power flow may be aided by a symbolic diagram (Fig. 1A) which reduces
the supply to three basic elements:
1. A raw d.c. source, the output of a transformer, rectifier, and filter.
2. A regulator element, typically a tube or transistor, in series with
the raw d.c. (An equivalent analysis could also be drawn for a shunt regulator.)
3. A high-gain d.c. comparison amplifier connected to drive the regulator
in such a way as to maintain a null (zero volts) across its input terminals.
(If the amplifier has sufficiently high gain, its feedback voltage is
practically the same as its output voltage so that its input voltage is
vanishingly small, or essentially zero. -Editor)
The amplifier input and the power supply's negative output form a feedback
pair of terminals so that the output voltage will always be equal to the
voltage across this pair (to maintain the input "null") . Several
properties of the feedback pair are significant.
1. It passes negligible current into the amplifier and, therefore, possesses
an apparent high impedance.
2. Any voltage achieved across the feedback pair will program the power
supply's output one-for-one. Programming, then, becomes a matter of controlling
the magnitude of the feedback-pair voltage.
Methods of Programming
The simplest method of programming involves placing a voltage source
directly across the feedback terminals perhaps a battery controlled by
a potentiometer (Fig. 1B). Because of the high impedance, the potentiometer's
wiper will not be loaded, yielding good linearity vs position.
Programmed in this way, power supplies are sometimes used as impedance
transformers. With "input" impedances in the megohm range and
output impedances in the milli ohm region, transformation ratios from
10^9 to 10^12 ohms are common.
Becoming a bit more sophisticated, the feedback voltage might be controlled
by placing a resistor across its terminals and contriving to pass a current
through it. The IR product voltage will then program the output to an
equal, but opposite, level. The current for the feedback resistance may
be obtained from a separate source. If this current is constant, then
the power supply's output voltage will simply be proportional to the resistance.
For example, if the current is 1 milliampere, the output will be 1 volt
for every 1000 ohms of feedback resistance. This is often called the programming
ratio; 1 milliampere control current corresponds to 1000 ohms per volt,
2 milliamperes will give 500 ohms per volt, etc.
Output may also be controlled by varying the current; or the current
and resistance may be varied simultaneously with the power supply's feedback
circuit by simply multiplying the two, with the product being the power
supply's output.
The current for the feedback circuit can be generated by connecting a
current source across the feedback resistance (in which case the current
generator must be capable of supporting the output voltage) or it may
be connected across the amplifier's null terminals. Since the null terminals
support little voltage (because of the gain) , this pair appears to have
a very low, almost zero, input impedance, and so is easily driven by a
current source. Since the current does not flow into the amplifier itself,
the path takes it through the feedback resistor where its passage generates
the IR drop needed to program the power-supply's output (Fig. 1C) . A
current source in this position is readily simulated.
Because the amplifier's input impedance is nearly zero, any voltage in
series with a suitable resistance can be used to generate the needed current.
(Since there is no voltage across the input terminals, the effective impedance
across these terminals is close to zero. This nearly zero input impedance
should not be confused with the very high "input" impedance
of the feedback pair shown previously in Fig. 1B.Editor.) The current
will be the input voltage divided by its series resistor. This current,
and thus the current through Rf, is subject to control by varying either
the source, E,. (the reference) or its series resistor, Rr. Control will
be directly proportional to Er and inversely proportional to Rf. (It is
directly proportional to the conductance Gr = 1 /Rr.) Writing the complete
equation: E,= Ef = Er (Rf /Rr) . The resistance ratio Rf /R, is sometimes
called the operational gain. or closed-loop gain. When either Rf or Rr
is varied to control output, the operation can be considered equivalent
to varying the gain of an amplifier with a fixed input (Er) . If the gain
ratio is allowed to remain constant, output may be varied in the selected
proportion by controlling Er.
Er may, of course, be any voltage level as long as it is used in series
with the appropriate resistor to produce the control current. The current
needed will be dependent on the value selected for Rf, with larger values
requiring the least amount of current.
In most modern power supplies, a shunt-regulated zener source is commonly
used to produce the stable reference (E,.) . The current from it is determined
by a precision series resistor (Rr) and is customarily between 1 mA (1000
ohms per volt) and 10 mA (100 ohms per volt). The feedback resistor (Re)
is made variable and is mounted on the front panel and labeled "voltage
control ". To qualify as a remotely programmable power supply, these
elements are connected to the circuit via appropriate terminals and links,
so arranged that users have access to any or all elements for the substitution
of external components (Table 1). Programming mechanisms ]night include
a remote feedback resistor which is variable, stepped, sequenced, or driven
by a motor; or it might include au external source of voltage substituted
for the reference. This, too, may be variable, derived in whole or in
part from a function generator, sweeper, or sensor output for process
control.
Next, let us consider sonic of the important design parameters that are
involved.
The ability of a power supply to make its output follow a program accurately.
linearly. and with good resolution is largely a function of the comparison
amplifier's gain.
The higher this is the more nearly perfect is the comparison. The gain
is usually reflected in the power supply's load regulation rating with
0.1. to 0.01% supplies requiring 80-100 dB of amplifier gain. Actually,
the significant gain is the open-loop gain (A) less the closed-loop gain
(Rf /Rr). The balance is called the "loop gain" or feedback
return ratio.
Also involved is an analysis of accuracy or linearity are the amplifier's
offsets (residual input voltages and currents) whose presence must be
accounted for in deter mining the precise output.
With modern emphasis placed on varying output (rather than the traditional
power-supply role of maintaining constant output) , the question of a
power supply's dynamics (behavior while varying) becomes significant.
Typically, power supplies have used large capacitors across the output
terminals. These capacitors are characterized by high energy storage,
low a.c. impedance, and resistance to voltage change, making them ideally
suited to the demands of the classical constant-voltage power supply.
These same characteristics, however, make the traditional output capacitor
unsuited to the demands of a variable (modulated) power supply. In particular,
the capacitor affects the programming speed-or stewing rate, the rate
of voltage change following a step command. say from a switched feedback
resistor. (Slewing rate is measured as the chord from the origin to the
first time-constant on the exponential response to a step command, as
in Fig. '2.) The relationship I = C dv /dt, where dv /dt is the voltage
rate-of-change, limits the clewing rate to the current divided by the
capacitance. Typically, for most output filtered supplies, this will be
just a few hundred volts per second.
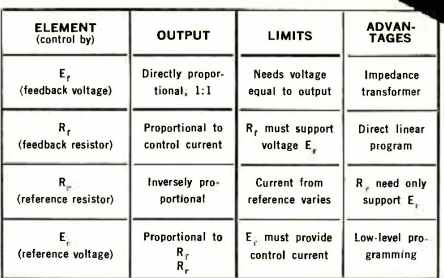 Table 1. Programming is done by varying one of these elements.
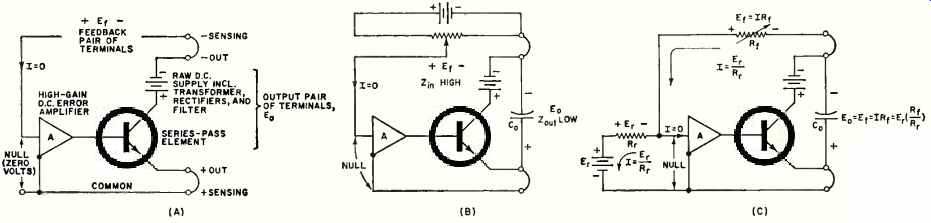
Fig. 1. (A) Simple series dissipative regulator type of power supply
showing signal voltage relationships. E., equals Er. (B) Voltage repeater
1:1 programming produces impedance transformation from very high-Z input
to very low-Z output. (C) A voltage Er in series with R, produces a current
through Rr equal to Er /Rr.
This current times Rr produces program E., = Er 1Rr /Rr1. Current arrows
show direction of electron flow.
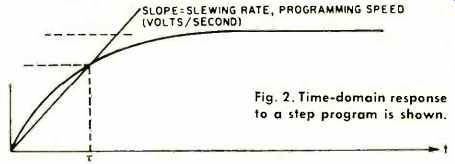
Fig. 2. Time-domain response to a step program is shown
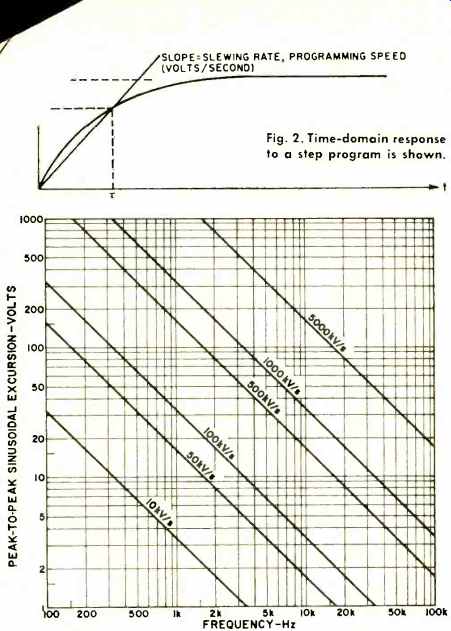
Fig. 3.
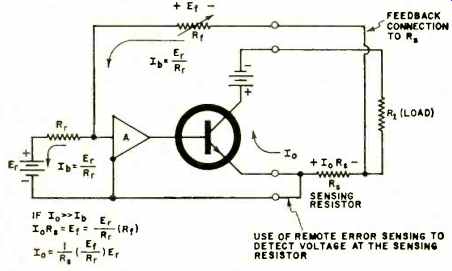 Fig. 4.
Fast-Programming Supplies
Some manufacturers now offer high-speed, or fast-pro-
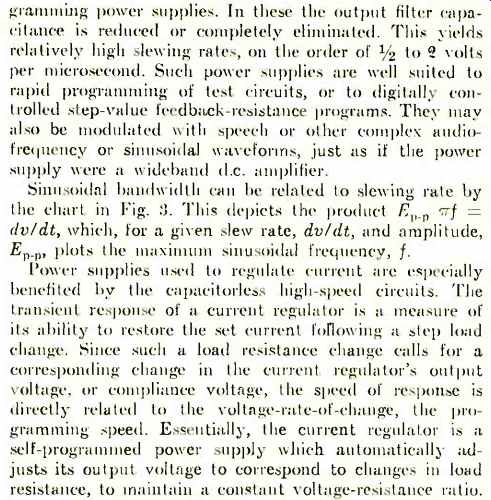
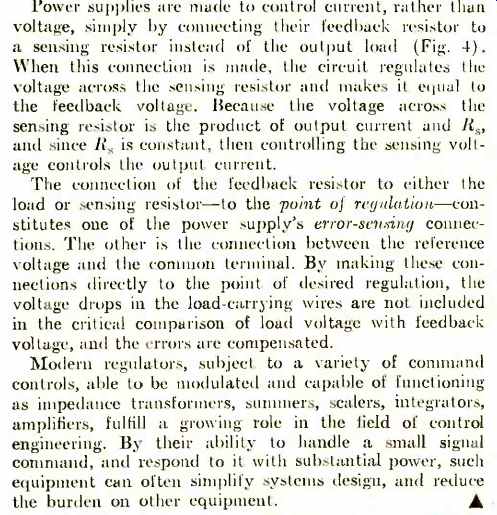
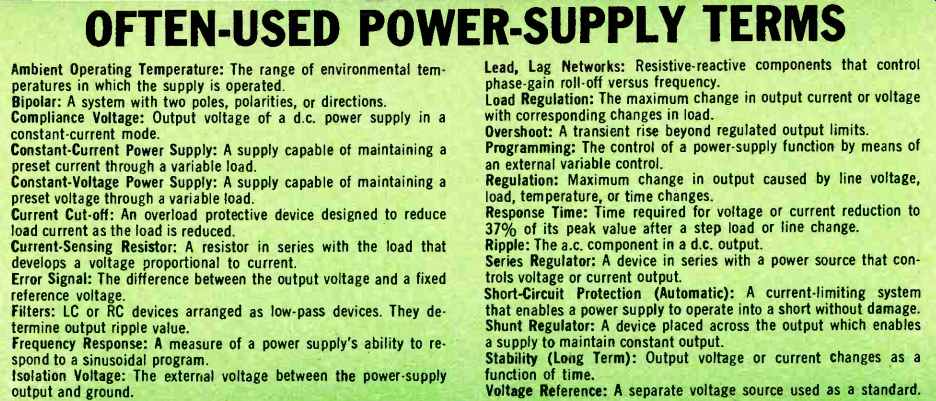
|