THE BASIC SYSTEM
In principle, the recording of an alternating electrical signal as a series
of magnetic fluctuations on a continuous magnetizable tape would not appear
to be a difficult matter, since it could be done by causing the AC signal to
generate corresponding changes in the magnetic flux across the gap of an electromagnet,
and these could then be impressed on the tape as it passes over the recording
electromagnet head.
In practice, however, there are a number of problems, and the success of tape
recording, as a technique, depends upon the solution of these, or, at least,
on the attainment of some reasonable working compromise. The difficulties which
exist, and the methods by which these are overcome, where possible, are considered
here in respect of the various components of the system.
MAGNETIC TAPE
This is a thin continuous strip of some durable plastics base material, which
is given a uniform coating of a magnetizable material, usually either 'gamma'
ferric oxide (Fe203), chromium dioxide (CrO2), or, in some recently introduced
tapes, of a metallic alloy, normally in powder form, and held by some suitable
binder material. Various 'dopants' can also be added to the coating, such as
cobalt, in the case of ferric oxide tapes, to improve the magnetic characteristics.
To obtain a long playing time it’s necessary that the total thickness of the
tape shall be as small as practicable, but to avoid frequency distortion on
playback it’s essential that the tape shall not stretch in use. It’s also important
that the surface of the tape backing material shall be hard, smooth and free
from lumps of imperfectly extruded material (known as 'pollywogs') to prevent
inadvertent momentary loss of contact between the tape and the recording or
play-back heads, which would cause 'dropouts' (brief interruptions in the replayed
signal). The tape backing material should also be unaffected, so far as is
possible, by changes in temperature or relative humidity.
For cassette tapes, and other systems where a backup pressure pad is used,
the uncoated surface is chosen to have a high gloss. In other applications
a matt finish will be preferred for improved spooling.
The material normally preferred for this purpose, as the best compromise between
cost and mechanical characteristics, is biaxially oriented polyethylene terephthalate
film (Melinex, Mylar, or Terphan). Other materials may be used as improvements
in plastics technology alter the cost/performance balance.
The term 'biaxial orientation' implies that these materials will be stretched
in » both the length and width directions during manufacture, to increase the
surface smoothness (gloss), stiffness and dimensional stability (freedom from
stretch). They will normally also be surface treated on the side to which the
coating is to be applied, by an electrical 'corona discharge' process, to improve
the adhesion of the oxide containing layer. This is because it’s vitally important
that the layer is not shed during use as it would contaminate the surface or
clog up the gaps in the recorder heads, or could get into the mechanical moving
parts of the recorder.
In the tape coating process the magnetic material is applied in the form of
a dope, containing also a binder, a solvent and a lubricant, to give an accurately
controlled coating thickness. The coated surface is subsequently polished to
improve tape/head contact and lessen head wear. The preferred form of both
ferric oxide and chromium dioxide crystals is needle-shaped, or 'acicular',
and the best characteristic for audio tapes are given when these are aligned
parallel to the surface, in the direction of magnetization. This is accomplished
during manufacture by passing the tape through a strong, unidirectional magnetic
field, before the coating becomes fully dry. This aligns the needles in the
longitudinal direction. The tape is then demagnetized again before sale.
Chromium dioxide and metal tapes both have superior properties, particularly
in HF performance, resistance to 'print through' and deterioration during repeated
playings, but they are more costly. They also require higher magnetic flux
levels during recording and for bias and erase purposes, and so may not be
suitable for all machines.
The extra cost of these tape formulations is normally only considered justifiable
in cassette recorder systems, where reproduction of frequencies in the range
15-20 kHz, especially at higher signal levels, can present difficulties.
During the period in which patent restrictions limited the availability of
chromium dioxide tape coatings, some of the manufacturers who were unable to
employ these formulations for commercial reasons, put about the story that
chromium dioxide tapes were more abrasive than iron oxide ones. They would,
therefore, cause more rapid head wear. This was only marginally true, and now
that chromium dioxide formulations are more widely available, these are used
by most manufacturers for their premium quality cassette tapes.
TBL. 1 Tape thicknesses (reel-to-reel)
Tape Thickness (in.)
'Standard play' 0.002
'Long play' 0.0015
'Double play' 0.001
'Triple play' 0.00075
'Quadruple play' 0.0005
Composite 'ferro-chrome' tapes, in which a thinner surface layer of a chromium
dioxide formulation is applied on top of a base ferric oxide layer, have been
made to achieve improved HF performance, but without a large increase in cost.
In 'reel-to-reel' recorders, it’s conventional to relate the tape thickness
to the relative playing time, as 'Standard Play', 'Double Play' and so on.
The gauge of such tapes is shown in TBL. 1. In cassette tapes, a more straightforward
system is employed, in which the total playing time in minutes is used, at
the standard cassette playing speed. For example, a C60 tape would allow 30
minutes playing time, on each side. The total thicknesses of these tapes are
listed in TBL. 2.
For economy in manufacture, tape is normally coated in widths of up to 48
in. (1.2 m), and is then slit down to the widths in which it’s used.
These are 2 in. (50.8 mm), 1 in. (25.4 mm), 0.5 in. (12.7 mm) and 0.25 in.
(6.35 mm) for professional uses, and 0.25 in. for domestic reel-to-reel machines.
Cassette recorders employ 0.15 in. (3.81 mm) tape.
High-speed slitting machines are complex pieces of precision machinery which
must be maintained in good order if the slit tapes are to have the required
parallelism and constancy of width. This is particularly important in cassette
machines where variations in tape width can cause bad winding, creasing, and
misalignment over the heads.
TBL. 2 Tape thicknesses (cassette)
Tape Thickness ( µm)
C60 18 (length 92 m)
C90 12 (length 133 m)
C120 9 (length 184 m)
Tape base thicknesses 12 µm, 8 µm and 6 µm respectively.
For all of these reasons, it’s highly desirable to employ only those tapes
made by reputable manufacturers, where these are to be used on good recording
equipment, or where permanence of the recording is important.
THE RECORDING PROCESS
The magnetic materials employed in tape coatings are chosen because they possess
elemental permanent magnets on a sub-microscopic or molecular scale. These
tiny magnetic elements, known as 'domains', are very much smaller than the
grains of spherical or needle-shaped crystalline material from which oxide
coatings are made.
Care will be taken in the manufacture of the tape to try to ensure that all
of these domains will be randomly oriented, with as little 'clumping' as possible,
to obtain as low a zero-signal-level noise background as practicable. Then,
when the tape passes over a recording head, shown schematically in FIG. 1,
these magnetic domains will be realigned in a direction and to an extent which
depend on the magnetic polarity and field strength at the trailing edge of
the recording head gap.
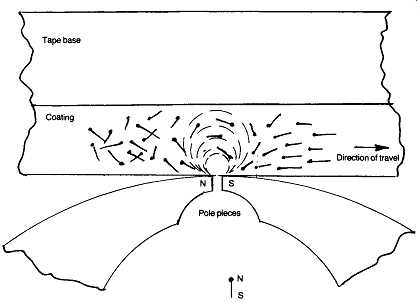
FIG. 1 The alignment of magnetic domains as the magnetic tape passes over
the recording head.
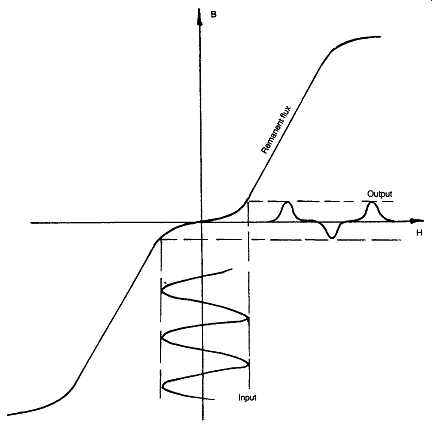
FIG. 2 The effect of the B-H non-linearity in magnetic materials on the recording
process.
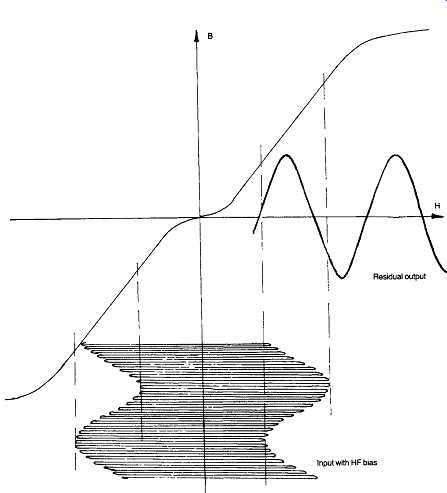
FIG. 3 The linearizing effect of superimposed HF bias on the recording process.
This is where first major snag of the system appears. Because of the magnetic
inertia of the material, small applied magnetic fields at the recording head
will have very little effect in changing the orientation of the domains. This
leads to the kind of characteristic shown in FIG. 2, where the applied magnetizing
force, (H), is related to the induced flux density in the tape material, (B).
If a sinusoidal signal is applied to the head, and the flux across the recording
head gap is related to the signal voltage, as shown in Fig. 2, the remanent
magnetic flux induced in the tape - and the consequent replayed signal - would
be both small in amplitude and badly distorted.
This problem is removed by applying a large high-frequency signal to the recording
head, simultaneously with the desired signal. This superimposed HF signal is
referred to as 'HF bias' or simply as 'bias', and will be large enough to overcome
the magnetic inertia of the domains and take the operating region into the
linear portion of the BH curve.
Several theories have been offered to account for the way in which 'HF bias'
linearizes the recording process. Of these the most probable is that the whole
composite signal is in fact recorded but that the very high frequency part
of it decays rapidly, due to self cancellation, so that only the desired signal
will be left on the tape, as shown.
When the tape is passed over the replay head - which will often be the same
head which was used for recording the signal in the first place - the fluctuating
magnetic flux of the tape will induce a small voltage in the windings of the
replay head, which will then be amplified electronically in the recorder. However,
both the recorded signal, and the signal recovered from the tape at the replay
head will have a non-uniform frequency response, which will demand some form
of response equalization in the replay amplifier.
CAUSES OF NON-UNIFORM FREQUENCY RESPONSE
If a sinusoidal AC signal of constant amplitude and frequency is applied to
the recording head and the tape is passed over this at a constant speed, a
sequence of magnetic poles will be laid down on the tape, as shown schematically
in FIG. 4, and the distance between like poles, equivalent to one cycle of
recorded signal, is known as the recorded wavelength.
The length of this can be calculated from the applied frequency and the movement,
in unit time of the tape, as '?', which is equal to tape velocity (cm/s) divided
by frequency (cycles/s) which will give wavelength (?) in cm.
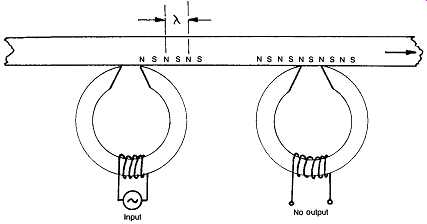
FIG. 4 The effect of recorded wavelength on replay head output.
This has a dominant influence on the replay characteristics in that when the
recorded wavelength is equal to the replay head gap, as is the case shown at
the replay head in FIG. 4, there will be zero output. This situation is worsened
by the fact that the effective replay head gap is, in practice, somewhat larger
than the physical separation between the opposed pole pieces, due to the spread
of the magnetic field at the gap, and to the distance between the head and
the center of the magnetic coating on the tape, where much of the HF signal
may lie.
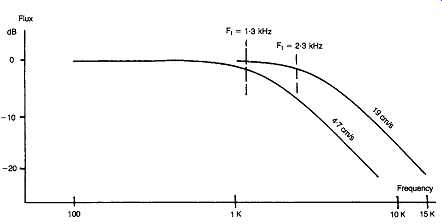
FIG. 5 Effect of tape speed on H F replay output.
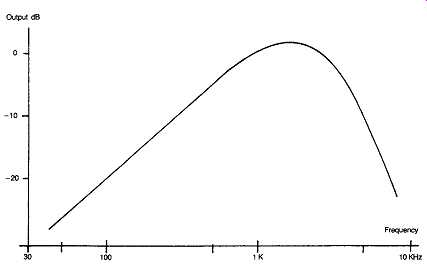
FIG. 6 The effect of recorded wavelength and replay head gap width on replay
signal voltage.
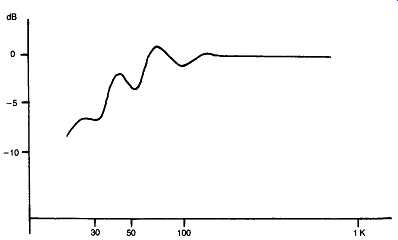
FIG. 7 Non-uniformity in low-frequency response due to pole-piece contour
effects.
Additional sources of diminished HF response in the recovered signal are eddy-current
and other magnetic losses in both the recording and replay heads, and 'self-demagnetization'
within the tape, which increases as the separation between adjacent N and S
poles decreases.
If a constant amplitude sine-wave signal is recorded on the tape, the combined
effect of recording head and tape losses will lead to a remanent flux on the
tape which is of the form shown in FIG. Here the HF turnover frequency (Ft)
is principally dependent on tape speed.
Ignoring the effect of tape and record/replay head losses, if a tape, on which
a varying frequency signal has been recorded, is replayed at a constant linear
tape speed, the signal output will increase at a linear rate with frequency.
This is such that the output will double for each octave of frequency. The
result is due to the physical laws of magnetic induction, in which the output
voltage from any coil depends on the magnetic flux passing through it, according
to the relationship V = L.dB/dt. Combining this effect with replay head losses
leads to the kind of replay output voltage characteristics shown.
At very low frequencies, say below 50 Hz, the recording process becomes inefficient,
especially at low tape speeds. The interaction between the tape and the profile
of the pole faces of the record/replay heads leads to a characteristic undulation
in the frequency response of the type shown in FIG. 7 for a good quality cassette
recorder.
RECORD/REPLAY EQUALIZATION
In order to obtain a flat frequency response in the record/replay process,
the electrical characteristics of the record and replay amplifiers are modified
to compensate for the non-linearities of the recording process, so far as this
is possible. This electronic frequency response adjustment is known as 'equalization',
and is the subject of much misunderstanding, even by professional users.
This misunderstanding arises because the equalization technique is of a different
nature to that which is used in FM broadcast receivers, or in the reproduction
of LP gramophone records, where the replay de-emphasis at HF is identical in
time-constant (turnover frequency) and in magnitude, but opposite in sense
to the pre-emphasis employed in transmission or recording.
By contrast, in tape recording it’s assumed that the total inadequacies of
the recording process will lead to a remanent magnetic flux in the tape following
a recording which has been made at a constant amplitude which has the frequency
response characteristics shown in FIG. 8 , for various tape speeds. This remanent
flux will be as specified by the time-constants quoted for the various international
standards shown in TBL. 3.
These mainly refer to the expected HF roll-off, but in some cases also require
a small amount of bass pre-emphasis so that the replay de-emphasis -- either
electronically introduced, or inherent in the head response -- may lessen 'hum'
pick-up, and improve LF signal-to-noise (S/N) ratio.
The design of the replay amplifier must then be chosen so that the required
flat frequency response output would be obtained on replaying a tape having
the flux characteristics shown.
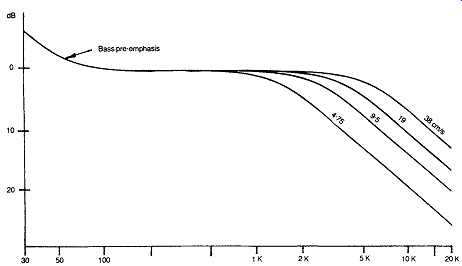
FIG. 8 Assumed remanent magnetic flux on tape for various tape speeds, in
cm Is.
This will usually lead to a replay characteristic of the kind shown in FIG.
Here a -6 dB/octave fall in output, with increasing frequency, is needed to
compensate for the increasing output during replay of a constant recorded signal
- referred to above - and the leveling off, shown in curves a-d, is simply
that which is needed to correct for the anticipated fall in magnetic flux density
above the turn-over frequency, shown in FIG. 8 for various tape speeds.
However, this does not allow for the various other head losses, so some additional
replay HF boost, as shown in the curves e-h, of FIG. 9, is also used.
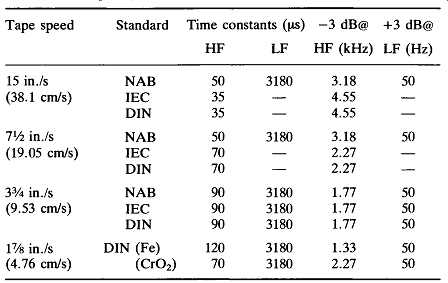
TBL. 3 Frequency correction standards---Tape speed Standard Time constants
(\ns) - 3 dB@ +3 dB@
The recording amplifier is then designed in the light of the performance of
the recording head used, so that the remanent flux on the tape will conform
to the specifications shown in TBL. 3, and as illustrated in Fig. 8. This
will generally also require some HF (and LF) pre-emphasis, of the kind shown
in FIG. 10. However, it should be remembered that, especially in the case of
recording amplifier circuitry the component values chosen by the designer will
be appropriate only to the type of recording head and tape transport mechanism
- in so far as this may influence the tape/head contact - which is used in
the design described.
Because the subjective noise level of the system is greatly influenced by
the amount of replay HF boost which is employed, systems such as reel to-reel
recorders, operating at relatively high-tape speeds, will sound less 'hissy'
than cassette systems operating at 1.875 in./s (4.76 cm/s) , for which substantial
replay HF boost is necessary. Similarly, recordings made using Chromium dioxide
tapes , for which a 70 us HF emphasis is employed, will sound less 'hissy'
than with Ferric oxide tapes equalized at 120 µ8, where the HF boost begins
at a lower frequency.
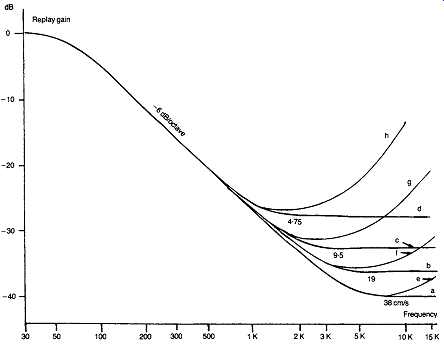
FIG. 9 Required replay frequency response , for different tape speeds.
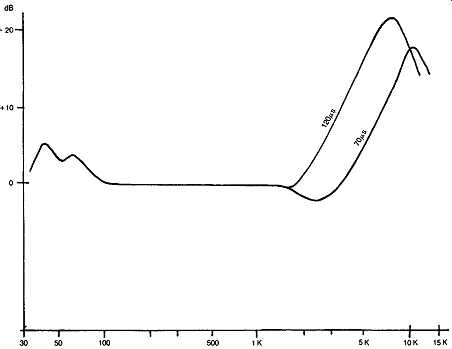
FIG. 10 Probable replay frequency response in cassette recorder required
to meet flux characteristics shown .
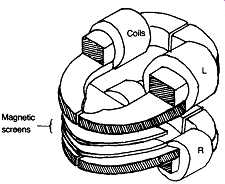
FIG. 11 General arrangement of cassette recorder stereo record I replay head
using Ferrite pole pieces.
HEAD DESIGN
Record/replay heads
Three separate head types are employed in a conventional tape recorder for
recording, replaying and erasing. In some cases, such as the less expensive
reel-to-reel and cassette recorders, the record and replay functions will be
combined in a single head , for which some design compromise will be sought
between the different functions and design requirements.
In all cases, the basic structure is that of a ring electromagnet, with a
flattened surface in which a gap has been cut, at the position of contact with
the tape. Conventionally, the form of the record and replay heads is as shown
in FIG. 11, with windings symmetrically placed on the two limbs, and with gaps
at both the front (tape side) and the rear. In both cases the gaps will be
filled with a thin shim of low magnetic permeability material, such as gold,
copper or phosphor bronze, to maintain the accuracy of the gap and the parallelism
of the faces.
The pole pieces on either side of the front gap are shaped, in conjunction
with the gap filling material, to concentrate the magnetic field in the tape,
as shown schematically in FIG. 12, for a replay head, and the material from
which the heads are made is chosen to have as high a value of permeability
as possible , for materials having adequate wear resistance.
The reason for the choice of high permeability core material is to obtain
as high a flux density at the gap as possible when the head is used for recording,
or to obtain as high an output signal level as practicable (and as high a resultant
S/N ratio) when the head is used in the replay mode. High permeability core
materials also help to confine the magnetic flux within the core, and thereby
reduce crosstalk.
With most available ferromagnetic materials, the permeability decreases with
frequency, though some ferrites (sintered mixes of metallic oxides) may show
the converse effect. The rear gap in the recording heads is used to minimize
this defect. It also makes the recording efficiency less dependent on intimacy
of the tape to head contact. In three-head machines, the rear gap in the replay
head is often dispensed with, in the interests of the best replay sensitivity.
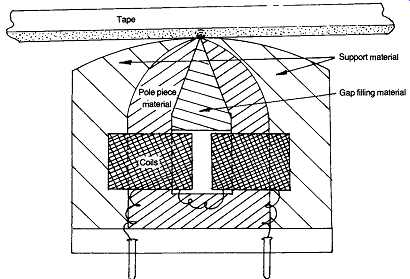
FIG. 12 Relationship between pole-pieces and magnetic flux in tape.
Gap filling material
Practical record/replay heads will be required to provide a multiplicity of
signal channels on the tape: two or four, in the case of domestic systems,
or up to 24 in the case of professional equipment. So a group of identical
heads will require to be stacked, one above the other and with the gaps accurately
aligned vertically to obtain accurate time coincidence of the recorded or replayed
signals.
It is, of course, highly desirable that there should be very little interaction,
or crosstalk, between these adjacent heads, and that the recording magnetic
field should be closely confined to the required tape track. This demands very
careful head design, and the separation of adjacent heads in the stack with
shims of low permeability material.
To preserve the smoothness of the head surface in contact with the tape, the
non-magnetic material with which the head gap, or the space between head stacks,
is filled is chosen to have a hardness and wear resistance which matches that
of the head alloy. For example, in Permalloy or Super Permalloy heads, beryllium
copper or phosphor bronze may be used, while in Sendust or ferrite heads, glass
may be employed.
The characteristics of the various common head materials are listed in TBL.
4. Permalloy is a nickel, iron, molybdenum alloy, made by a manufacturing process
which leads to a very high permeability and a very low coercivity. This term
refers to the force with which the material resists demagnetization: 'soft'
magnetic materials have a very low coercivity, whereas 'hard' magnetic materials,
i.e. those used for 'permanent' magnets, have a very high value of coercivity.
====
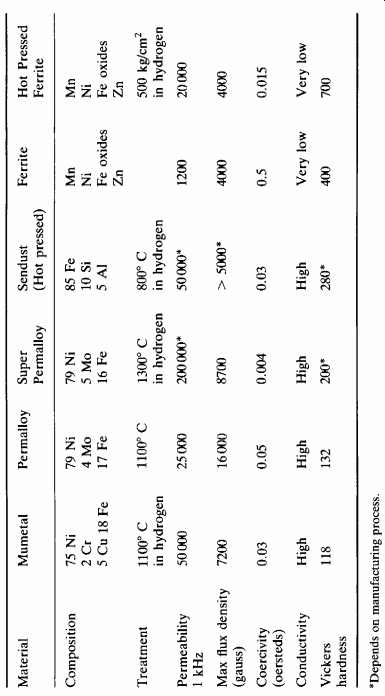
TBL. 4 Magnetic materials for recording heads. Material Composition Treatment
Permeability
=====
Super-Permalloy is a material of similar composition which has been heat treated
at 1200-1300° C in hydrogen, to improve its magnetic properties and its resistance
to wear. Ferrites are ceramic materials, sintered at a high temperature, composed
of the oxides of iron, zinc, nickel and manganese, with suitable fillers and
binders. As with the metallic alloys, heat treatment can improve the performance,
and hot pressed ferrite (typically 500 kg/cm2 at 1400° C) offers both superior
hardness and better magnetic properties.
Sendust is a hot-pressed composite of otherwise incompatible metallic alloys
produced in powder form. It has a permeability comparable to that of Super
Permalloy with a hardness comparable to that of ferrite.
In the metallic alloys, as compared with the ferrites, the high conductivity
of the material will lead to eddy-current losses (due to the core material
behaving like a short-circuited turn of winding) unless the material is made
in the form of thin laminations, with an insulating layer between these. Improved
HF performance requires that these laminations are very thin, but this, in
turn, leads to an increased manufacturing cost, especially since any working
of the material may spoil its performance.
This would necessitate re-annealing, and greater problems in attaining accurate
vertical alignment of the pole piece faces in the record/replay heads. The
only general rule is that the better materials will be more expensive to make,
and more difficult to fabricate into heads.
Because it’s only the trailing edge of the record head which generates the
remanent flux on the tape, the gap in this head can be quite wide; up to 6-10
µm typical examples. On the other hand, the replay head gap should be as small
as possible, especially in cassette recorders, where high quality machines
may employ gap widths of one µm (0.00004 in.) or less.
The advantage of the wide recording head gap is that it produces a field which
will penetrate more fully into the layer of oxide on the surface of the tape,
more fully utilizing the magnetic characteristics of the tape material. The
disadvantage of the narrow replay gap, needed for good HF response, is that
it’s more difficult for the alternating zones of magnetism on the recorded
tape to induce changes in magnetic flux within the core of the replay head.
Consequently the replay signal voltage is less, and the difficulty in getting
a good S/N ratio will be greater.
Other things being equal, the output voltage from the replay head will be
directly proportional to the width of the magnetic track and the tape speed.
On both these counts, therefore, the cassette recorder offers an inferior replay
signal output to the reel-to-reel system.
The erase head
This is required to generate a very high frequency alternating magnetic flux
within the tape coating material. It must be sufficiently intense to take the
magnetic material fully into saturation, and so blot out any previously existing
signal on the tape within the track or tracks concerned.
The design of the head gap or gaps should allow the alternating flux decay
slowly as the tape is drawn away from the gap, so that the residual flux on
the tape will fall to zero following this process.
Because of the high frequencies and the high currents involved, eddy-current
losses would be a major problem in any laminated metal construction. Erase
heads are therefore made from ferrite materials.
A rear air gap is unnecessary in an erase head, since it operates at a constant
frequency. Also, because saturating fields are used, small variations in the
tape to head contact are less important.
Some modern cassette tape coating compositions have such a high coercivity
and remanence (retention of impressed magnetism) that single gap heads may
not fully erase the signal within a single pass. So dual gap heads have been
employed, particularly on machines offering a 'metal tape' facility. This gives
full erasure, (a typical target value of -70 dB being sought for the removal
of a fully recorded signal), without excessive erase currents being required,
which could lead to overheating of the erase head.
It’s important that the erase head should have an erase field which is closely
confined to the required recorded tracks, and that it should remain cool. Otherwise
unwanted loss of signal or damage to the tape may occur when the tape recording
is stopped during the recording process, by the use of the 'pause' control.
In some machines provision is made for switching off the erase head, so that
multiple recordings may be overlaid on the same track. This is an imperfect
answer to this requirement, however, since every subsequent recording pass
will erase pre-existing signals to some extent.
This facility would not be practicable on inexpensive recorders, where the
erase head coil is used as the oscillator coil in the erase and 'bias' voltage
generator circuit.
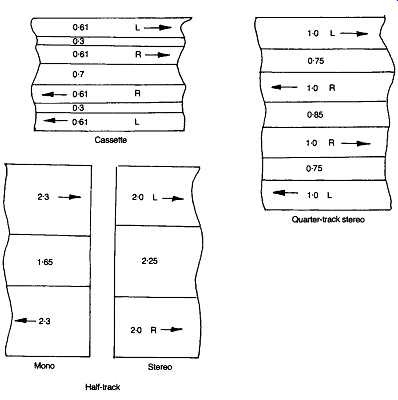
FIG. 13 Tape track specifications. (All dimensions in mm.)
RECORDING TRACK DIMENSIONS
These conform to standards laid down by international agreements, or, in the
case of the Philips compact cassette, within the original patent specifications,
and are as shown in FIG. 13.
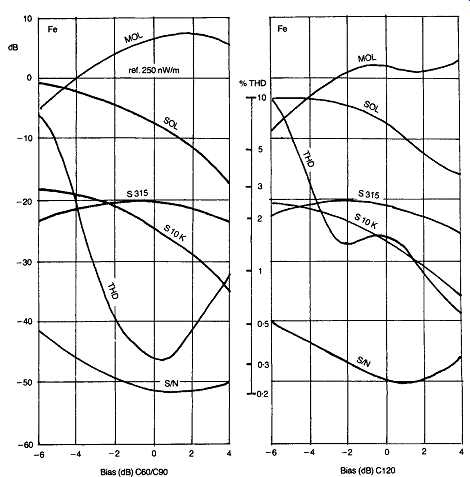
FIG. 14 The influence of bias on recording characteristics. (C60/90 and C120
Ferric tapes.)
HF BIAS
Basic bias requirements
As has been seen, the magnetic recording process would lead to a high level
of signal distortion, were it not for the fact that a large, constant amplitude.
HF bias waveform is combined with the signal at the recording head. The basic
requirement for this is to generate a composite magnetic flux, within the tape,
which will lie within the linear range of the tape's magnetic characteristics,
as shown FIG.
However, the magnitude and nature of the bias signal influences almost every
other aspect of the recording process. There is no value for the applied 'bias'
current which will be the best for all of the affected recording characteristics.
It’s conventional, and correct, to refer to the bias signal as a current, since
the effect on the tape is that of a magnetizing force, defined in 'ampere turns'.
Since the recording head will have a significant inductance - up to 0.5 H in
some cases - which will offer a substantial impedance at HF, the applied voltage
for a constant flux level will depend on the chosen bias frequency.
The way in which these characteristics are affected is shown in Figs 14 and
15 , for ferric and chrome tapes. These are examined separately below, together
with some of the other factors which influence the final performance.
HF bias frequency
The particular choice of bias frequency adopted by the manufacturer will be
a compromise influenced by his own preferences, and his performance intentions
for the equipment.
It’s necessary that the frequency chosen shall be sufficiently higher than
the maximum signal frequency which is to be recorded that any residual bias
signal left on the tape won’t be reproduced by the replay head or amplifier,
where it could cause overload or other undesirable effects.
On the other hand, too high a chosen bias frequency will lead to difficulties
in generating an adequate bias current flow through the record head. This may
lead to overheating in the erase head.
Within these overall limits, there are other considerations which affect the
choice of frequency. At the lower end of the usable frequency range, the overall
efficiency of the recording process, and the LF S/N ratio is somewhat improved.
The improvement is at the expense of some erasure of the higher audio frequencies,
which increases the need for HF pre emphasis to achieve a 'flat' frequency
response. However, since it’s conventional to use the same HF signal for the
erase head, the effectiveness of erasure will be better for the same erase
current.
At the higher end of the practicable bias frequency range, the recorded HF
response will be better, but the modulation noise will be less good.
The danger of saturation of the recording head pole-piece tips will be greater,
since there is almost invariably a decrease in permeability with increasing
frequency. This will require more care in the design of the recording head.
Typically, the chosen frequency for audio work will be between four and six
times the highest frequency which it’s desired to record: it will usually be
in the range 60-120 kHz, with better machines using the higher values.
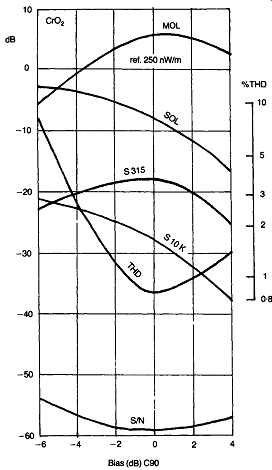
FIG. 15 The influence of bias on recording characteristics. (C90 Chrome tape.)
HF bias waveform
The most important features of the bias waveform are its peak amplitude and
its symmetry. So although other waveforms, such as square waves, will operate
in this mode quite satisfactorily, any inadvertent phase shift in the harmonic
components would lead to a change in the peak amplitude, which would affect
the performance.
Also, it’s vitally important that the HF 'bias' signal should have a very
low noise component. In the composite signal applied to the record head, the
bias signal may be 10-20 times greater than the audio signal to be recorded.
If, therefore, the bias waveform is not to degrade the overall S/N ratio of
the system, the noise content of the bias waveform must be at least 40 times
better than that of the incoming signal.
The symmetry of the waveform is required so that there is no apparent DC or
unidirectional magnetic component of the resultant waveform, which could magnetize
the record head and impair the tape modulation noise figure. An additional
factor is that a symmetrical waveform allows the greatest utilization of the
linear portion of the tape magnetization curve.
For these reasons, and for convenience in generating the erase waveform, the
bias oscillator will be designed to generate a very high purity sine wave.
Then the subsequent handling and amplifying circuitry will be chosen to avoid
any degradation of this.
Maximum output level (MOL)
When the tape is recorded with the appropriate bias signal, it will have an
effective B-H characteristic of the form shown in FIG. 16. Here it’s quite
linear at low signal levels, but will tend to flatten-off the peaks of the
waveform at higher signal levels. This causes the third harmonic distortion,
which worsens as the magnitude of the recorded signal increases, and effectively
sets a maximum output level for the recorder/tape combination.
This is usually quoted as 'MOL (315 Hz)', and is defined as the output level,
at 315 Hz. It’s given some reference level, (usually a remanent magnetic flux
on the tape of 250 nano-Webers/m , for cassette tapes), at which the third
harmonic distortion of the signal reaches 3%. The MOL generally increases with
bias up to some maximum value, as shown in Figs 14 and 15.
The optimum, or reference bias:
Since it’s apparent that there is no single best value for the bias current,
the compromise chosen for cassette recorders is usually that which leads to
the least difficulty in obtaining a flat frequency response. Lower values of
bias give better HF performance but worse characteristics in almost all other
respects, so the value chosen is that which leads to a fall in output, at 10
kHz in the case of cassettes of 12 dB in comparison with the output at 315
Hz.
In higher tape speed reel-to-reel recorders, the specified difference in output
level at 315 Hz and 12.5 kHz may be only 2.5 dB. Alternatively, the makers
recommended 'reference' bias may be that which gives the lowest value of THD
at 1 kHz.
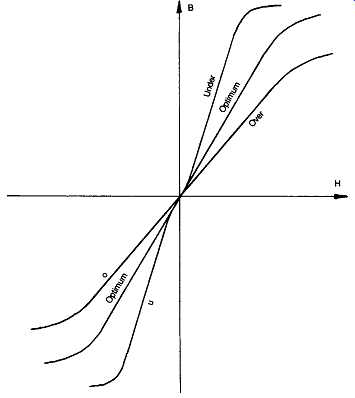
FIG. 16 Relationship between remanent flux, B, and applied magnetic field
at 315 Hz in a biased tape, showing linearization and overload effects.
Sensitivity
This will be specified at some particular frequency, as 'S-315 Hz' or 'S-10
kHz' depending on the frequency chosen. Because of self-erasure effects, the
HF components of the signal are attenuated more rapidly with increasing HF
'bias' values than the LF signals. On the other hand, HF signals can act, in
part, as a bias waveform, so some recorders employ a monitoring circuit which
adjusts the absolute value of the bias input, so that it’s reduced in the presence
of large HF components in the audio signal.
This can improve the HF response and HF output level for the same value of
harmonic distortion in comparison with a fixed bias value system.
Total harmonic distortion (THD):
This is generally worsened at both low and high values of 'bias' current.
At low values, this is because inadequate bias has been used to straighten
out the kink at the center of the ?-?' curve, which leaves a residue of unpleasant,
odd harmonic, crossover-type distortion. At high values, the problem is simply
that the bias signal is carrying the composite recording waveform into regions
of tape saturation, where the B-H curve flattens off.
Under this condition, the distortion component is largely third harmonic,
which tends to make the sound quality rather shrill. As a matter of practical
convenience, the reference bias will be chosen to lie somewhere near the low
point on the THD/bias curve. The formulation and coating thickness adopted
by the manufacturer can be chosen to assist in this, as can be seen by the
comparison between C90 and C120 tapes in FIG. 14.
The third harmonic distortion for a correctly biased tape will increase rapidly
as the MOL value is approached. The actual peak recording values for which
the recorder VU or peak recording level meters are set is not, sadly, a matter
on which there is any agreement between manufacturers, and will, in any case,
depend on the tape and the way in which it has been biased.
Noise level
Depending on the tape and record head employed, the residual noise level on
the tape will be influenced by the bias current and will tend to decrease with
increasing bias current values. However, this is influenced to a greater extent
by the bias frequency and waveform employed, and by the construction of the
erase head.
The desired performance in a tape or cassette recorder is that the no signal
replay noise from a new or bulk erased tape should be identical to that which
arises from a single pass through the recorder, set to record at zero signal
level.
Aspects of recording and replay noise are discussed more fully below.
Saturation output level (SOL)
This is a similar specification to the MOL, but will generally apply to the
maximum replay level from the tape at a high frequency, usually 10 kHz, and
decreases with increasing bias at a similar rate to that of the HF sensitivity
value.
The decrease in HF sensitivity with increasing bias appears to be a simple
matter of partial erasure of short recorded wavelength signals by the bias
signal. However, in the case of the SOL, the oscillation of the domains caused
by the magnetic flux associated with the bias current appears physically to
limit the ability of short wavelength magnetic elements to coexist without
self-cancellation.
It’s fortunate that the energy distribution on most program material is high
at LF and lower middle frequencies, but falls off rapidly above, say, 3 kHz,
so HF overload is not normally a problem. It’s also normal practice to take
the output to the VU or peak signal metering circuit from the output of the
recording amplifier, so the effect of pre-emphasis at HF will be taken into
account.
Bias level setting
This is a difficult matter in the absence of appropriate test instruments,
and will require adjustment for every significant change in tape type, especially
in cassette machines, where a wide range of coating formulations is available.
Normally, the equipment manufacturer will provide a switch selectable choice
of pre-set bias values, labeled in a cassette recorder , for example, as types
T (all ferric oxide tapes, used with a 120 µS equalization time constant),
'2' (all chromium dioxide tapes, used with a 70 uS equalization), '3' (dual
coated 'ferro-chrome' tapes , for 70 µs equalization) and ‘4’ (all 'metal'
tapes), where the machine is compatible with these.
Additionally, in the higher quality (three-head) machines, a test facility
may be provided, such as a built-in dual frequency oscillator, having outputs
at 330 Hz and 8 kHz, to allow the bias current to be set to provide an identical
output at both frequencies on replay. In some recent machines this process
has been automated.
THE TAPE TRANSPORT MECHANISM
The constancy and precision of the tape speed across the record and replay
heads is one of the major criteria for the quality of a tape recorder mechanism.
Great care is taken in the drive to the tape 'capstans' to smooth out any vibration
or flutter generated by the drive motor or motors. The better quality machines
will employ a dual-capstan system, with separate speed or torque controlled
motors, to drive the tape and maintain a constant tension across the record
and replay heads, in addition to the drive and braking systems applied to the
take-up and unwind spools.
This requirement can make some difficulties in the case of cassette recorder
systems, in which the design of the cassette body allows only limited access
to the tape. In this case a dual-capstan system requires the use of the erase
head access port for the unwind side capstan, and forces the use of a narrowed
erase head which can be fitted into an adjacent, unused, small slot in the
cassette body.
The use of pressure pads to hold the tape against the record or replay heads
is considered by many engineers to be an unsatisfactory practice, in that it
increases the drag on the tape, and can accelerate head wear. In reel-to-reel
recorders it’s normally feasible to design the tape layout and drive system
so that the tape maintains a constant and controlled position in relation to
the heads, so the use of pressure pads can be avoided.
However, in the case of cassettes where the original patent specification
did not envisage the quality of performance sought and attained in modern cassette
decks, a pressure pad is incorporated as a permanent part of the cassette body.
Some three-head cassette machines, with dual capstan drive, control the tape
tension at the record and replay position so well that the inbuilt pressure
pad is pushed away from the tape when the cassette is inserted.
An essential feature of the maintenance of any tape or cassette recorder is
the routine cleaning of the capstan drive shafts, and pinch rollers, since
these can attract deposits of tape coating material, which will interfere with
the constancy of tape drive speed.
The cleanliness of the record/replay heads influences the closeness of contact
between the tape and the head gap, which principally affects the replay characteristics,
and reduces the replay HF response.
TRANSIENT PERFORMANCE
The tape recording medium is unique as the maximum rate of change of the reproduced
replay signal voltage is determined by the speed with which the magnetized
tape is drawn past the replay head gap. This imposes a fixed 'slew-rate' limitation
on all reproduced transient signal voltages, so that the maximum rate of change
of voltage cannot exceed some fixed proportion of its final value.
In this respect it differs from a slew-rate-limited electronic amplifier,
in which the effective limitation is signal amplitude dependent, and may not
occur on small signal excursions even when it will arise on larger ones.
Slew-rate limitation in electronic amplifiers is, however, also associated
with the paralysis of the amplifier during the rate-limited condition. This
is a fault which does not happen in the same way with a replayed magnetic tape
signal, within the usable region of the B-H curve. Nevertheless, it’s a factor
which impairs the reproduced sound quality, and leads to the acoustic superiority
of high tape speed reel-to-reel machines over even the best of cassette recorders,
and the superiority of replay heads with very narrow head gaps , for example
in three-head machines, in comparison with the larger, compromise form, gaps
of combined record/ replay heads.
It’s possibly also, a factor in the preference of some audiophiles for direct-cut
discs, in which tape mastering is not employed.
A further source of distortion on transient waveforms arises due to the use
of HF emphasis, in the recording process and in replay, to compensate for the
loss of high frequencies due to tape or head characteristics.
If this is injudiciously applied, this HF boost can lead to 'ringing' on a
transient, in the manner shown , for a square-wave in FIG. 17. This impairs
the audible performance of the system, and can worsen the subjective noise
figure of the recorder. It’s therefore sensible to examine the square-wave
performance of a tape recorder system following any adjustment to the HF boost
circuitry, and adjust these for minimum overshoot.
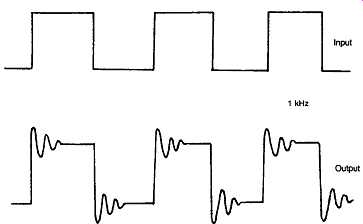
FIG. 17 'Ringing' effects, on a 1 kHz square-wave, due to excessive HF boost
applied to extend high-frequency response.
TAPE NOISE
Noise in magnetic recording systems has two distinct causes: the tape, and
the electronic amplification and signal handling circuitry associated with
it. Circuit noise should normally be the lesser problem, and will be discussed
separately.
Tape noise arises because of the essentially granular, or particulate, nature
of the coating material and the magnetic domains within it. There are other
effects, though, which are due to the actual recording process, and these are
known as 'modulation' or 'bias noise', and 'contact' noise -- due to the surface
characteristics of the tape.
The problem of noise on magnetic tape and that of the graininess of the image
in the photographic process are very similar. In both cases this is a statistical
problem, related to the distribution of the individual signal elements, which
becomes more severe as the area sampled, per unit time, is decreased. (The
strict comparison should be restricted to cine film, but the analogy also holds
for still photography.) Similarly, a small output signal from the replay head,
(equivalent to a small area photographic negative), which demands high amplification,
(equivalent to a high degree of photographic enlargement), will lead to a worse
S/N ratio, (equivalent to worse graininess in the final image), and a worse
HF response and transient definition, (image sharpness). For the medium itself,
in photographic emulsions high sensitivity is associated with worse graininess,
and vice versa. Similarly, with magnetic tapes, low noise, fine grain tape
coatings also show lower sensitivity in terms of output signal. Metal tapes
offer the best solution here.
A further feature, well-known to photographers, is that prints from large
negatives have a subtlety of tone and gradation which is lacking from apparently
identical small-negative enlargements. Similarly, comparable size enlargements
from slow, fine-grained, negative material are preferable to those from higher
speed, coarse-grained stock.
There is presumably an acoustic equivalence in the tape recording field.
Modulation or bias noise arises because of the random nature and distribution
of the magnetic material throughout the thickness of the coating. During recording,
the magnetic flux due to both the signal and bias waveforms will redistribute
these domains, so that, in the absence of a signal, there will be some worsening
of the noise figure. In the presence of a recorded signal, the magnitude of
the noise will be modulated by the signal.
This can be thought of simply as a consequence of recording the signal on
an inhomogeneous medium, and gives rise to the description as 'noise behind
the signal', as when the signal disappears, this added noise also stops.
The way in which the signal to noise ratio of a recorded tape is dependent
on the area sampled, per unit time, can be seen from a comparison between a
fast tape speed dual-track reel-to-reel recording with that on a standard cassette.
For the reel-to-reel machine there will be a track width of 2.5 mm, with a
tape speed of 15 in./s (381 mm/s), which will give a sampled area equivalent
to 2.5 mm x 381 mm = 925 mm^2 /s. In the case of the cassette recorder the
tape speed will be 1.875 in./s (47.625 mm/s), and the track width will be 0.61
mm, so that the sampled area will only be 29 mm^2/s.
This is approximately 32 times smaller, equivalent to a 15 dB difference in
S/N ratio.
This leads to typical maximum S/N ratios of 67 dB for a two-track reel to-reel
machine, compared with a 52 dB value for the equivalent cassette recorder,
using similar tape types. In both cases some noise reduction technique will
be used, which will lead to a further improvement in these figures.
It’s generally assumed that an S/N ratio of 70-75 dB for wideband noise is
necessary for the noise level to be acceptable for high quality work, though
some workers urge the search for target values of 90 dB or greater. However,
bearing in mind that the sound background level in a very quiet domestic listening
room is unlikely to be less than +30 dB (reference level, 0 dB = 0.0002 dynes/cm2
) and that the threshold of pain is only +105-110 dB, such extreme S/N values
may not be warranted.
In cassette recorders, it’s unusual for S/N ratios better than 60 dB to be
obtained, even with optimally adjusted noise reduction circuitry in use.
The last source of noise, contact noise, is caused by a lack of surface smoothness
of the tape, or fluctuations in the coating thickness due to surface irregularities
in the backing material. It arises because the tape coating completes the magnetic
circuit across the gap in the heads during the recording process.
Any variations in the proximity of tape to head will, therefore, lead to fluctuations
in the magnitude of the replayed signal. This kind of defect is worse at higher
frequencies and with narrower recording track widths, and can lead to drop-outs
(complete loss of signal) in severe cases.
This kind of broadband noise is influenced by tape material, tape storage
conditions, tape tension and head design. It’s an avoidable nuisance to some
extent, but is invariably present.
Contact noise, though worse with narrow tapes and low tape speeds, is not
susceptible to the kind of analysis shown above, in relation to the other noise
components.
The growing use of digital recording systems, even in domestic cassette recorder
form, is likely to alter substantially the situation for all forms of recorded
noise, although it’s still argued by some workers in this field that the claimed
advantages of digitally encoded and decoded recording systems are offset by
other types of problem.
There is no doubt that the future of all large-scale commercial tape recording
will be tied to the digital system, if only because of the almost universal
adoption by record manufacturers of the compact disc as the future style of
gramophone record.
This is recorded in a digitally encoded form, so it’s obviously sensible to
carry out the basic mastering in this form also, since their other large scale
products, the compact cassette and the vinyl disc, can equally well be mastered
from digital as from analogue tapes.
cont to part 2 >>
|