WHY NECESSARY?
In the majority of cases, the output from an audio system will be fed to
some form of electro-acoustic transducer, such as a loudspeaker (LS) or headphone,
whose purpose is to convert the electrical input signal into a sound pressure
wave which will evoke a response in the ear of the listener.
Ideally, this transducer will have a constant acoustic output , for a given
electrical input signal, over the range 20 Hz to 20 kHz, or whatever the human
ear is supposed to be able to hear.
In practice, there is no known LS driver system (I am using this term in
the sense of the individual moving-coil, magnet and cone assembly, or its
equivalent, rather than the complete unit in wooden box, which I will call
a 'loudspeaker') which is capable of operating completely satisfactorily over
the whole of this frequency span. The loudspeaker manufacturers seek to approach
this ideal by combining a number of individual units with suitable 'crossover'
networks, so that their combined outputs will achieve the desired result.
The units used in such a multiple driver system will mostly be based on moving
coil (m/c) layouts but the same limitations will apply, though in a somewhat
different sense, to electrostatic or ribbon LS systems.
In general, with an m/c driver unit the optimum frequency span, in which
it will be free from major peaks and troughs in its acoustic output, will
cover a range of about ten or perhaps twenty to one, of which the lower frequency
end will be determined, usually, by the natural (bass) resonance of the cone
assembly. This makes it (just) possible to cover the range from 50 Hz to 20
kHz with a two-speaker system, though it may be done more easily, and with
a greater bass extension, with a three-speaker assembly.
The reasons for the inability of the m/c driver unit to provide a constant
acoustic output over a wide frequency range are complex, but, as a simplified
analysis, can be considered as a result of the poor mechanical coupling between
the moving coil and the cone, and the failure of the LS cone itself, when
urged by the coil, to move as a rigid piston to displace enough air to produce
the required acoustic output.
I will consider these 'first-order' problems separately, but the ways in
which adequate - though not perfect - solutions are found to these owes as
much to art and intuition as it does to science or engineering. This is why
there are so many good but different LS designs on sale, and why LS designers
continue to offer new designs.
CONE DESIGN
Effects of cone flexure and cone break-up
In its simplest form, an LS diaphragm is simply a rigid piston, mounted for
operational purposes in an opening, ideally of the same size as the piston,
in an infinitely extended sound-proof wall (acting as a 'baffle' to prevent
the displaced air from simply flowing round the edges of the piston from front
to rear) as shown in FIG. 1(a). When the piston is caused to move, it will
displace a quantity of air which is proportional to its axial movement multiplied
by its surface area.
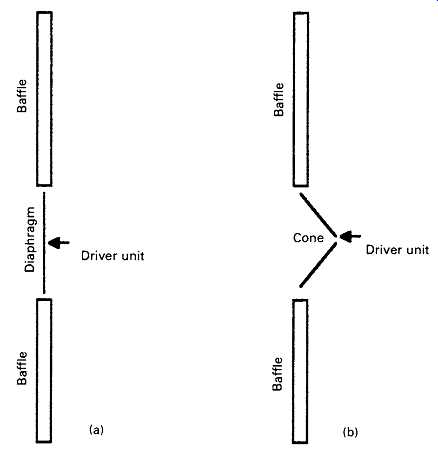
FIG. 1 Basic LS action.
Unfortunately, because no such piston is completely rigid, the part of the
piston to which the actuating mechanism (the coil and magnet) is attached
will move more than the periphery of the piston and this will reduce its efficiency,
especially at higher frequencies, where the effect of the air loading is greater.
Also, the differential movement of the center of the piston in relation to
its periphery due to diaphragm flexure implies that there will be surface
wave motion along the piston. This will complicate the acoustic radiation
characteristics of the system, and this difficulty will be compounded by the
need for some kind of flexible surround to bridge the gap between the edge
of the piston and the aperture in which it’s mounted.
This surround will cause an acoustic mismatch, and will result in any surface
waves being reflected back along the surface of the piston, to disturb yet
further the sound radiation characteristics.
If the diameter of the piston is reduced, this will increase its effective
stiffness, but its axial movement will need to be proportionately increased
if it’s to be able to displace the same volume of air. Some designers claim
that this can cause problems due to Doppler effects (frequency shift through
movement of the sound source) if the same piston is required to handle signals
at different frequencies, simultaneously - especially if one of these signals
is at a low frequency, which requires a larger piston movement. For these
reasons, flat LS diaphragms, which won’t be very stiff, are seldom found,
though some composite structures, based on sandwiches of metal foil and rigid
polystyrene foam, have been used with success as 'woofers' required to cover
only one or two octaves at the bottom end of the audio band.
Although electrical 'crossover' systems will reduce this type of problem,
by limiting the frequency coverage required from any individual LS driver
unit, the normal design approach is to make the piston conical in form, as
shown in FIG. 1(b), rather than flat. This results in a very great increase
in stiffness for a given diameter and thickness of the cone material. However,
while the behavior of the cone is good at the low-frequency end of its usable
frequency range, as the frequency is increased the cone will cease to behave
as a simple piston and the cone surface will tend to break up into various
'ringing' modes, akin to the ringing of a shallow wine glass. These modes
will cause unwanted peaks and troughs in the radiated frequency response.
The most common choices of the LS designer for cone materials are soft, felted
paper; often with some circumferential corrugations to encourage the inner
sections to break away from the outer sections of the cone at high frequencies,
and act as smaller, more rigid, pistons; or cones molded from some inert,
heavily internally damped, thermo-plastic, on the grounds that this won’t
be excited easily into any structural resonances. Alternatively, the cone
may be molded in a somewhat curved or exponential cross-section, because this
is not subject to bell-type resonances. However, although this may extend
the frequency span which can be covered by any individual LS driver unit,
all these solutions result in lower transducer efficiency, which is undesirable.
Rigid cone systems
An alternative approach which has been exploited from time to time, most
notably in the UK by Jordan-Watts Ltd and by the GEC, is the use of cone materials
which have a very high stiffness-to-weight ratio, such as aluminum or titanium,
and then to limit the diameter so that the very prominent HF resonances, which
will inevitably occur in such systems, are high enough in frequency to be
effectively outside the required audio spectrum. The piston area required
to allow useful acoustic outputs at low frequencies is then achieved by connecting
a number of these drive units so that their diaphragms move in unison. The
crossover network in this case is a load-sharing system rather than, as is
more usually the requirement, a frequency band separation arrangement.
Coil attachment and magnet characteristics
For a high LS efficiency , for any given cone structure, the magnetic flux
in the air gap in which the coil moves should be as high as possible. This
is attained, in part, by the use of very high energy magnet systems, based
on exotic alloys, and in part by keeping the air gap between the pole pieces,
in which the coil moves, as narrow as possible. However, this, in turn, leads
to problems because it’s then necessary to provide some centering mechanism
attached to both the coil and the LS frame, to make sure that the coil is
held so that it cannot touch the magnet pole pieces. This inner centering
provides the bulk of the restoring force applied to the cone, and it cannot
be made too stiff or it will increase the fundamental resonant frequency of
the LS to an undesirable extent.
The fundamental resonant frequency of the cone assembly is of importance
because the output will fall at -12 dB/octave below this frequency -- though
cabinet design can arrest this fall somewhat. The sound waveform of signals
below this frequency will become increasingly distorted by the presence of
second and third harmonics of the input signal.
A further aspect of coil construction is that, in high-power units, considerable
power may be dissipated in the coil, and the heat must be either conducted
or radiated away. This can be facilitated by winding the coil on an aluminum
former, which could be bonded to a short aluminum cone, fixed to the center
of the LS diaphragm. However, this generates a further acoustic mismatch in
the cone assembly, which introduces additional output irregularities. An electrically
conductive speech coil former is also of use in assisting in damping the resonances
of the cone, insofar as these are transmitted to the speech coil.
SOUNDWAVE DISPERSION
Even if it were possible to design an LS driver unit which could cover the
whole of the audio frequency band, it would still be necessary for this to
have a relatively large cone area to be able to generate an adequate volume
of sound at the lower audio frequencies. This leads to the difficulty that
where the wavelength of the sound waves becomes small in relation to the width
or height of the radiator, any radiating system will concentrate the energy
of the sound radiated by it into a relatively narrow beam in the horizontal
or vertical sense. This will be unsatisfactory for normal listening, where
, for the comfort or convenience of the listeners, it’s preferred that the
radiated sound shall be dispersed over a wide area.
CROSSOVER SYSTEM DESIGN
In principle, any low-pass or high-pass filter system, or a combination of
these, could be used to select the portion of the frequency spectrum which
is allocated to the bass, mid-range and HF driver units. (Where they are connected
in the LS circuit within the cabinet, they will almost always be based on
LC circuit layouts in order to provide the low circuit impedances needed to
drive m/c LS units.) Examples of first-, second- and third-order LC filter
circuits are shown in FIG. 2 but, in practice, with normal m/c driver units,
only second-order (-12 dB/octave) filter circuits will be used, of the general
kind shown in FIG. 2(b). This is because it’s essential that the electrical
inputs fed to the LS drivers shall be capable of being added together so that
there is no significant hump or trough in the combined LS frequency. This
is only easily possible with second-order layouts.
For the notional 1 kHz crossover frequency which I have chosen for the transfer
of input signal from a low-frequency driver unit, to a mid-range unit, the
low-pass (LF driver) input filter ( FIG. 2(b)) will have an electrical output
(shown as G on the graph) of the kind shown in FIG. 3.
The high-pass (HF driver) input filter will have an output of the kind in
FIG. 4. If these two outputs are added together acoustically by two equally
efficient drive units, their combined output will be as in FIG. 5, which shows
a - 6 dB trough in the gain curve at the crossover frequency, coupled with
an abrupt phase shift (as in the curve labeled P) - a situation which would
not be acoustically satisfactory.
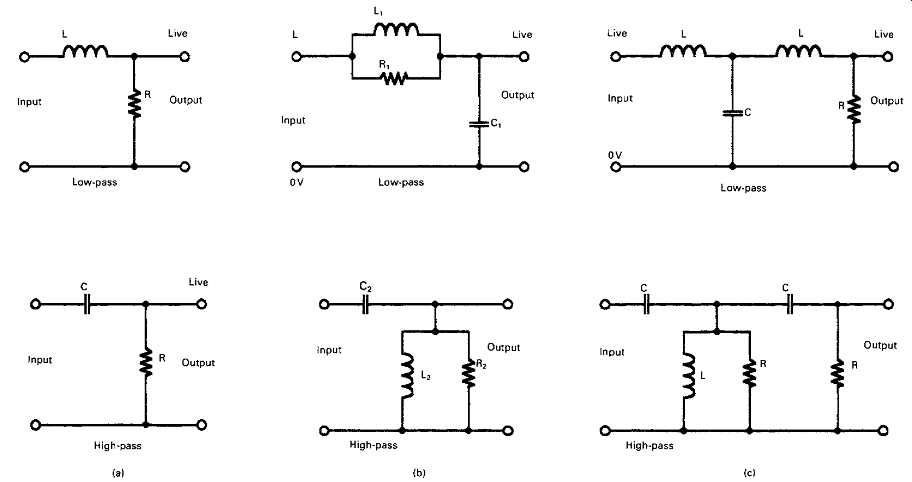
FIG. 2 LC crossover networks.
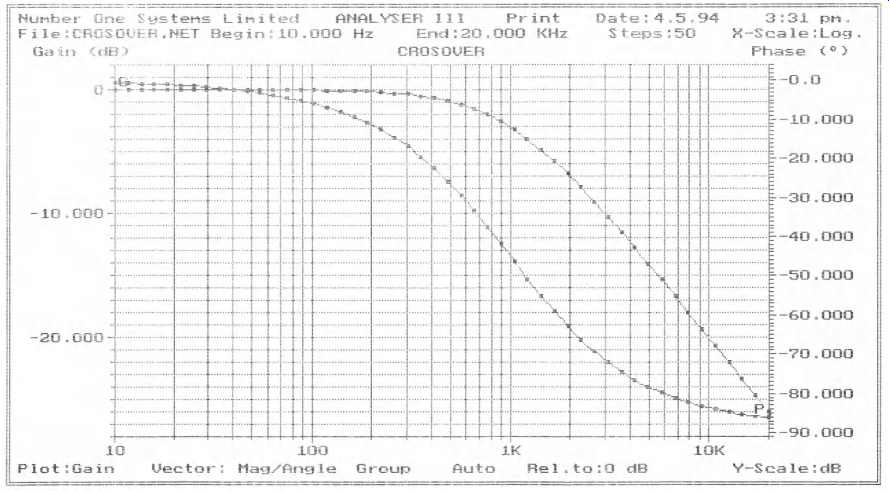
FIG. 3
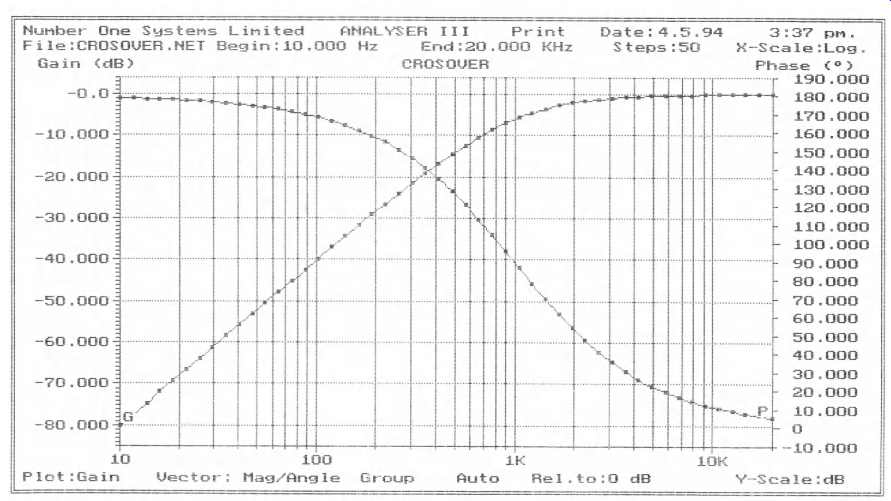 FIG. 4
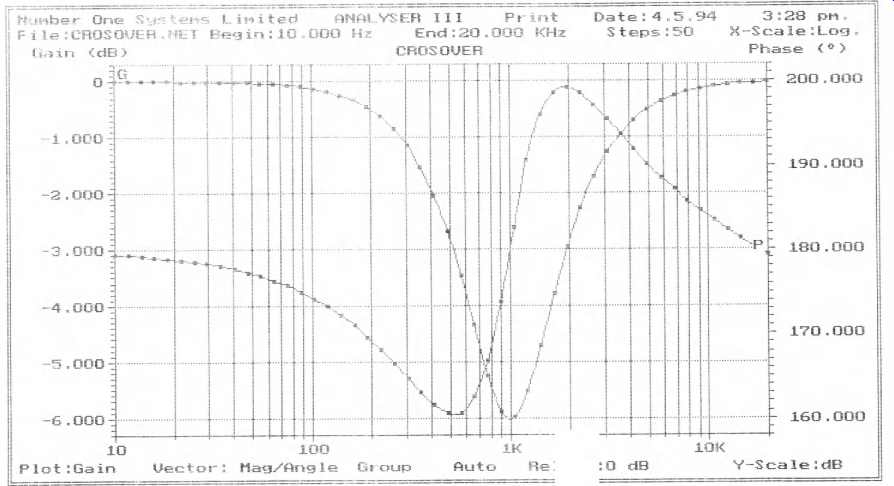 FIG. 5
 FIG. 6
In the case of the second-order filter, however, though not in the first-
or third-order systems, it’s possible to reverse the polarity of the signal
fed to one or other of the LS drivers. In the case illustrated I have exchanged
the lead/terminal connections to the high-frequency unit. This results in
the linear phase characteristics of the result shown graphically in FIG. 6,
where the -6 dB trough is converted into a much more tolerable 0.95 dB hump
in the frequency response. (In practice, the component values of the filter
would be adjusted slightly to move the cut-off frequencies slightly further
apart to reduce this hump to near zero.) The manipulation of crossover network
systems was considered, at some length, by Pramanik of Bang and Olufsen (S.
K. Pramanik, Wireless World, November 1975, pp. 529-532). His explorations
of the various network possibilities showed that while the second-order filter
system was the best of the three listed above, this still left discontinuities
either in gain or in phase. He therefore proposed the use of an active crossover
network, from which a third output was derived which could be fed to a supplementary
driver unit to fill in the troughs resulting from conventional crossover systems.
A problem which will always arise in practice is that the individual driver
units will vary in sensitivity not only from one to another of an apparently
identical type but also, and more understandably, between driver units of
different types, intended to cover different parts of the audio spectrum.
The use of resistors within the crossover networks is to be avoided where
possible because they will dissipate energy (and get hot) and will also reduce
the system efficiency. Those shown in FIG. 2, inserted to improve the theoretical
smoothness of the filter slope, would be dispensed with if the characteristics
of the driver unit or its enclosure contributed enough damping without them.
Therefore the idea of using an output potentiometer to adjust the voltage
drive to the LS unit is quite impracticable.
CROSSOVER COMPONENT TYPES
Although in low-cost, modest performance loudspeaker systems it’s normal
practice to use reversible electrolytic capacitors and iron-cored inductors,
in order to reduce size and the cost of providing the relatively large inductance
and capacitance values needed, the better-quality systems will invariably
use air-cored inductors and non-polar capacitors. The latter should preferably
be made from low-loss dielectric materials such as polycarbonate or polypropylene.
If an adjustment of signal input to one unit relative to another is essential
this will usually be done by a small coupling transformer, and in high-grade
systems this will also need to be an air-cored unit. However, this approach
should be avoided if at all possible since it will probably impair the network
characteristics.
The design of crossover networks is additionally complicated by the fact
that the LS driver unit, within an enclosure, does not present a pure 4, 8
or 15 ohm, frequency-independent, resistance at its input - a condition assumed
as a first approach to the design of the crossover system. In practice, in
addition to the quite significant electrical resistance and inductance of
the speech coil winding, all the mechanical resonances in the LS cone, or
its mounting, or its enclosure, will be combined in its input impedance, together
with the mechanical components of capacitance, resistance and inductance due
to the compliance, factional losses, and mass of all the moving or vibrating
parts of the system.
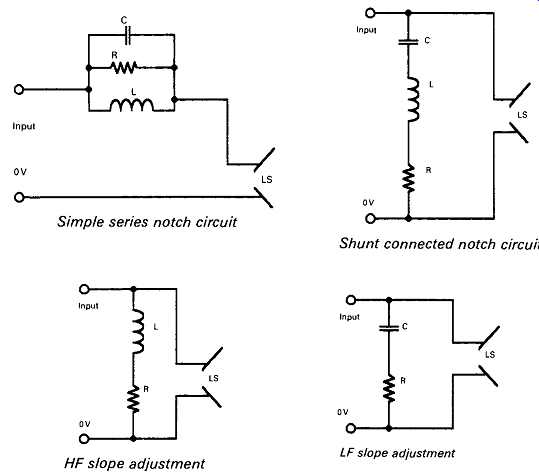 FIG. 7 Response-equalizing circuits. LF slope adjustment ; Simple series
notch circuit ; Shunt connected notch circuit ; HF slope adjustment
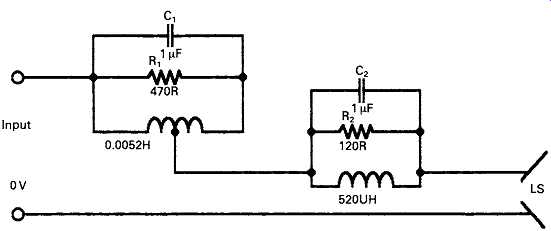 FIG. 8 Baxandal Vs equalizing circuit for ELAC RMI109 LS unit
LS OUTPUT EQUALIZATION
As has been seen, most LS driver units don’t have a constant acoustic output
as a function of frequency for a constant input signal voltage.
However, it’s possible, with most such systems, to electrically equalize
at least partially the response of the driver unit by the insertion of strategically
placed inductors or capacitors in series or in parallel with the driver unit.
Typical circuit arrangements which will produce a dip or a roll off in the
frequency response of the system are shown in FIG. 7. The values of resistors,
inductors or capacitors in the circuit will be chosen to provide the results
required, bearing in mind the complex impedance characteristics of the actual
driver unit, which will affect the final results.
Circuit layouts of this type are often used by commercial loudspeaker manufacturers
to minimize the peaks and troughs which their frequency response measurements
have revealed during prototype testing. An example of this approach was described
by Baxandall (P. J. Baxandall, Wireless World, August 1968, pp. 242-247) with
reference to a design which he had built for his own use with a single 15
ohm, 9 in. x 5 in. ELAC RM/109 LS unit, of which the circuit he used is shown
in FIG. 8. The effectiveness of this approach, in the case of the simple and
inexpensive LS unit employed, was attested by the flattering comments subsequently
made by several experienced hi-fi reviewers.
ACTIVE CROSSOVER SYSTEMS
The difficulty of making precise inductor/capacitor crossover systems, at
LS line impedances, which will nowadays be either 4 or 8 ohms, and the inconvenient
load characteristics of the LS unit itself - which are complicated by the
motional impedances of the unit and its housing, and the LS coil inductance
and resistance - has encouraged the more perfectionist loudspeaker manufacturers
(and experimentally minded hi-fi enthusiasts) to transfer the crossover and
equalization networks to the input of the power amplifier, which is a high
impedance point. This approach leads to the types of layout shown schematically
in Figs 9 and 10. Here an electronic filter system is interposed between the
signal input and the power amplifier, and the output of the power amp is connected
directly to the LS driver units. In hi-fi jargon, these arrangements are commonly
called 'bi-amplification' or 'tri-amplification', depending on the number
of LS units used.
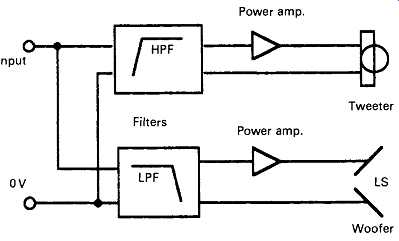 FIG. 9 'Bi-amplifier', layout.
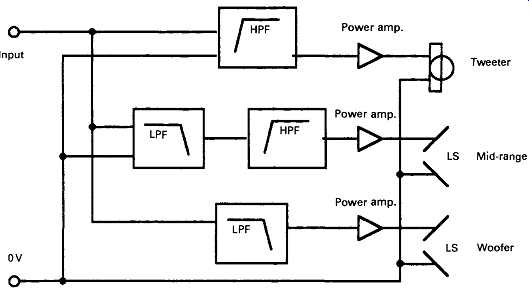 FIG. 10 'Tri-amplifier' system.
There are many advantages in this system, of which the principal ones are
that the LS coil is driven from a very low source impedance. This leads to:
• improved damping of cone resonances
• the filter and equalization arrangements can all be implemented by the
use of low-power components
• the filter designs can have more nearly ideal phase and amplitude characteristics
• the pass-band handled by the individual amplifiers is reduced, which lessens
the exposure of the circuitry to intermodulation distortion effects
• the output power requirements of the individual amplifiers can be tailored
more precisely to the relative energy distribution of the audio signal spectrum
• the relative magnitudes of the signals fed to the driver units can be adjusted,
precisely, by trimmer potentiometers without the loss of energy and the dissipation
of heat which would otherwise be incurred.
Additionally, the power amplifiers can be housed in the loudspeaker enclosures,
which avoids those problems that can occur with external amplifier-LS connector
cables, since the only long connections, in the living room of the user, will
be between the pre-amplifier and filters, and the power amplifiers inside
the loudspeaker units. These will be at high impedance, where any good-quality
screened cable will be entirely adequate.
The only major snags with this approach are that it’s much more expensive
than a conventional system, and that it commits the user to the power amplifier
chosen by the loudspeaker manufacturer.
ACTIVE FILTER DESIGN
Although, in principle, any even-order (e.g. second, fourth, sixth, etc.)
Butterworth response filter will satisfy the requirement for gain uniformity
and phase linearity at the crossover point, the use of higher-order filter
types will generally require that some additional phase compensation should
be included in the crossover circuit. The simplest, and most popular, arrangement
is that in which the filters shown in the schematic layouts of Figs 9 and
10 are second-order Sallen and Key designs of the kind in Figs 11 and 12.
In both the high-pass and low-pass circuits shown in Figs 11(a) and 12, the
- 3 dB 'turnover' frequency (fT) will be given by the relationship:
fT = l^V(C1 C2 RiR2 )) .
For example, in FIG. 11(a) , for Q = C2 = 4n7F, and Rt = 18K and R2 = 56k,
fT = 1 kHz. In FIG. 12, a 1 kHz turnover frequency would be given by Rt =
R2 = 33k, where Q = 8n2F and C2 = 2n7F. For the values shown the circuits
will have a Q of 1/V(2) (0.707). The Q can be increased, giving a somewhat
steeper attenuation rate (but also a greater phase shift at/T) if the gain
of IC2 is increased, as shown in FIG. 11(b). FIG. 11 Second-order high-pass
Sallen and Key filter.
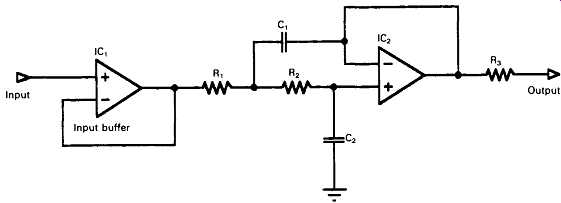 FIG. 12 Second-order low-pass Sallen and Key filter.
ATC Loudspeaker Technology Ltd, who are one of the foremost European suppliers
of professional LS monitor units in which active crossover systems are incorporated
within the loudspeaker housings, precede both the high- and low-pass second-order
filters with a state-variable filter, having a ß of unity, to generate a fourth-order
Butterworth response filter characteristic. They also provide individual pass-band
gain adjustment controls, used to compensate for inequalities in driver unit
sensitivities in setting up the system, and a fast-acting 'soft clipping'
limiter. This serves both to protect the driver units and also to allow the
loudspeakers to be operated at a higher mean sound level without the audibly
unpleasant effects which would arise if the power amplifiers were driven into
'hard clipping'. ATC also incorporate unity-gain phase correcting 'all-pass'
filters, of the kind shown in FIG. 13, in their crossover divider networks.
These allow compensation for the phase errors due to the different sound path
lengths from the driver unit to the ear of the listener, and can also remedy
any imperfections in the gain/phase characteristics due to acoustic superposition
in the crossover region. A photograph of the ATC active crossover system is
shown in FIG. 14.
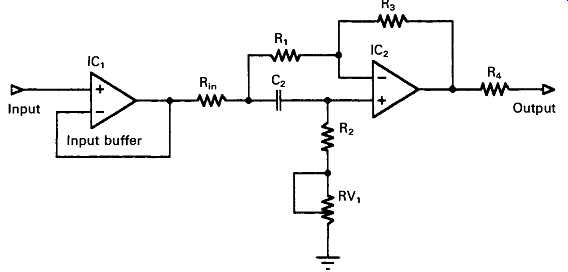 FIG. 13 Phase-correcting filter.
 FIG. 14 ATC active crossover system.
BI-WIRING AND TRI-WIRING
If the cause of the first major parting of the ways of the 'engineers' and
the 'audiophiles' was the audibility of class A type crossover distortion
in transistor-operated audio amplifiers (nothing to do with loudspeakers in
this case) - which the engineers said was either non-existent or negligible,
and the audiophiles said they could hear and disliked - the second was whether
or not loudspeaker cables were audibly important. Once again, the engineers
said that their calculations and measurements proved conclusively that they
were unimportant acoustically, provided that they were of a reasonably low
resistance, and, once again, the audiophiles said that they could hear a difference,
and they were acoustically very important.
My own feeling in this instance is that the audiophiles have overstated their
case but, nevertheless, there is a grain of truth in their claims, as can
be shown by a simple experiment. Let us take the case of a pair of LS units
which have been wired up using a couple of equal lengths of twin-core 10 amp
mains cable. This is a fairly common practice among the more prosaic, or more
frugally minded, members of the audio fraternity (if it had so happened that
their power amplifier did not come complete with a pair of specialty speaker
cables), even when their total expenditure on their equipment was substantial
- and that the position of the channel balance control has been optimally
adjusted to provide a central stereo image.
Now, in the interests of tidiness, let us reduce the length of one of the
LS cables, so that there is less redundant cable between the power amplifier
and the nearer LS unit. Almost certainly it will be found that the position
of the channel balance control for a central stereo image must now be altered
so that less gain is required from the LS unit fed by the shorter LS lead
- a condition which is unaffected by change of amplifiers or LS units.
This outcome would be puzzling to the user, if he or she had previously satisfied
themselves either by measurement or by calculations based on the maker's specification
of resistance per meter, that the resistance of their LS cables was substantially
lower than the quoted impedance of their loudspeakers. Experiment suggests
that the extent to which the central stereo image position is affected by
the relative lengths of the LS cables depends on the goodness (in respect
of lowness of resistance) of the cables, so that the offset of central stereo
image caused by cable length asymmetry is less noticeable with the better
quality cables.
I think that the explanation of this phenomenon is that the LS makers' quoted
impedance values tend to be somewhat notional and that the impedance of most
multiple-driver loudspeaker units can fall to very low levels at parts of
the audio spectrum, especially under dynamic conditions.
Therefore the amplifier and its output leads may be required, under some
conditions, to drive an LS load of less than an ohm, rather than the 'eight
ohms' suggested by the makers.
However, the more enthusiastic members of the hi-fi fraternity, having discovered
that cable types can affect the system performance, have made the presumption,
on the basis of this discovery, that the fewer signal components carried by
the LS cable, the better the system will sound. The logical conclusion from
this belief is that the audio performance of the LS unit will be improved
if the crossover unit within the speaker assembly is designed so that it can
be divided into sections, and so that each section can be individually connected
to the amplifier output by way of its individual cable pair. Systems of this
kind seem to have gained some popularity, but I feel that such bi-wired or
tri-wired set-ups cannot really approach the performance which can be given
by active crossover networks feeding individual amplifiers and driver units.
|