Inductors and Transformers
All conductors have inductance, and the longer the conductor, the greater
this will be.
Although in the frequency range of interest in audio the amount of inadvertent
inductance due to things like connecting leads are not likely to be significant,
they may lead to occasional, unexpected, and generally unwanted, high frequency
phenomena--such as HF parasitic oscillation--which can spoil amplifier performance.
If a conductor is wound into the form of a coil, its inductance will be increased,
and if this coil is wound around a core of some ferromagnetic material its
inductance will be increased still further, in proportion to the permeability
(p) of the core material.
If two such coils are placed in proximity to one another, so that their magnetic
fields will interact, then any change in the current flowing through one of
them will cause a voltage to be induced in the other. In general, the shape
of the core of a transformer will be chosen to give the highest practicable
amount of electromagnetic coupling between the windings, a process which is
helped by the use of high permeability core materials.
Transformers have the useful property of converting a small current flow,
at a high impedance, through one of the windings, into a larger current at
a lower impedance, through another winding, and vice versa. Also, because the
conducting coils which form the windings on a transformer can be electrically
isolated from one another, so far as static DC potentials are concerned, they
allow signals or other AC voltages and currents to be transferred from one
circuit to another, even when these circuits operate at widely different DC
voltage levels.
Mains transformers are used in every piece of audio equipment, except those
powered from batteries, to generate the DC power rails used to operate it,
and output transformers are still used in every tube operated audio amplifier
to couple the high impedance level of the tube output stages to the relatively
low impedance levels of the loudspeaker circuit. In all of these applications,
the problems are the same, and require the same measures to reduce their unwanted
effects.
Problems with transformers
Ideally, the changes in magnetic flux, which occur when there is a change
in the current flowing through one winding of a transformer, should interact
completely with the other windings on that transformer, and not at all with
any other external circuits.
The use of a ferromagnetic core material - the term ferromagnetic means a
type of material which will increase the inductance of a coil in which it is
placed- will help to confine the magnetic flux within the transformer, and
increase the effectiveness of coupling from one winding to another. The higher
the magnetic permeability of the core material and the shorter the magnetic
path in its core, the better this will be done.
These materials will have a relationship between magnetic flux and applied
magnetizing field, known as the B-H curve, of the kind shown in FIG. 1, and
the difference (X-Y) between the paths of the magnetization and demagnetization
curves shown in this graph indicates the extent of residual magnetization of
the core, and is known as the magnetic hysteresis of the material. The value
of the magnetic flux (B) for a given magnetizing field (H) is a measure of
the permeability of the core material.
For comparison, the B-H curve for an air (or vacuum) cored system is also
shown in FIG. 1.
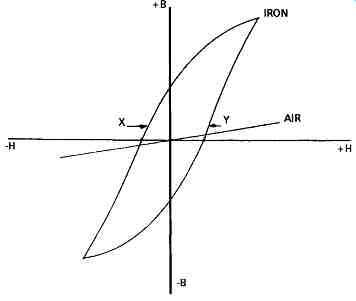
FIG. 1 Magnetic hysteresis curve
There are two broad categories of ferromagnetic material, those which have
a high value of magnetic retentivity, such as cobalt-steel, known as permanent
or hard magnetic materials, and those of low retentivity or soft magnetic materials,
such as iron with low carbon content.
For iron cored inductors or transformers it is essential to use only those
materials which have very low levels of magnetic retentivity, or otherwise
the hysteresis loss which will accompany every flux reversal in the core magnetization
will result in an absorption of input energy which will be released as heat.
Also, even in low retentivity materials, the decay of the magnetic flux, on
removal of the magnetic field, is not instantaneous, so there will always be
an increase in core losses at higher signal frequencies.
The final major source of energy loss is that due to eddy current flow within
the core.
This arises because the core will generally be made of an electrically conductive
metal, such as silicon steel (which has a permeability some 8000 times greater
than air), and any electrically conductive paths in this will look like the
short-circuited turns of a series of secondary windings. This eddy current
loss can be made smaller by constructing the core from a stack of thin sheet
stampings, coated with some insulating material on one or both faces, known
as laminations. These can then be arranged to divide the core block at fight-angles
to the direction of the transformer windings and of the current flow within
them. Thin laminations of high permeability core material give better transformer
performance and lower losses, but they are expensive and fiddly to assemble
within the former on which the coils have been wound. Like hysteresis losses,
eddy current losses increase rapidly with operating frequency.
In the case of eddy current losses, T.H. Collins, Analog Electronics Handbook,
pp. 292-293 (Prentice Hall, 1989), quotes the relationship
P_e = af^2 Bm^2 d^2
where Pe is the power loss, a is a constant, f is the operating frequency,
Bm is the maximum core flux density, and d is the thickness of the laminations.
Toroidal and 'C' core constructions
These types of core are shown in FIG. 2, and allow the practical use of very
thin lamination material. In the manufacture of a C core, shown in FIG. 2a,
the core material is wound into the required shape, and then solidly locked
in this shape by impregnation with epoxy resin, before being sawn into two
sections to allow the windings, on a suitable former, to be set in place. If
the sawn faces are ground fiat, at the correct angle, the two transformer core
sections can be reassembled, and clamped in place, with only a very small residual
gap at their junction. In the case of the toroidal construction shown in FIG.
2b, the core is first wound into a ring form, and impregnated, and the windings
are then wound, in situ, by a suitably designed coil winding machine. Both
of these constructions allow low core losses, low external radiation fields
and low levels of unwanted currents induced in the secondary windings by external
sources.
Toroidal types are widely used as the mains power transformers in high quality
audio amplifiers because their low external 50/60Hz field greatly lessens the
extent to which hum will be induced in nearby low signal level circuitry. Their
high electromagnetic efficiency also provides proportionately higher power
outputs, and lower winding (copper) losses than the older (but less expensive)
designs based on square stacks of laminations.
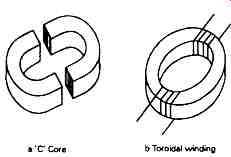
Fig. 2 Waveform distortion in coupling transformers
This arises both because of the non-linearity of the core magnetization curve,
and, in amplifiers, because of core saturation and input overload due to inadequate
primary inductance at low frequencies. At high frequencies, the difficulty
in specifying the transformer behavior and its transformation ratio becomes
much greater, because of the presence of parallel and inter-winding capacitances
and inductances, as the transformer equivalent circuit shown in FIG. 3 will
make clear. In this diagram, Lp and L s are the primary and secondary winding
inductances, LL, P and LL, s are the primary and secondary leakage inductances,
Rp and R s are the primary and secondary winding resistances and Cp and C s
are the internal capacitances of the primary and secondary windings.
The inductance of any coil is determined by a number of factors, as shown
in the equation
L = kN2pa/1
where L is the inductance, k is a constant approximately equal to 8.3 " 10^8
when dimensions are in centimeters, u, is the permeability of the core material,
N is the number of turns of the winding, a is the cross-sectional area of the
core and 1 is the magnetic path length. By far the easiest way of increasing
the inductance of any coil FIG. 3
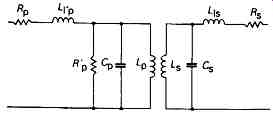 Above: Fig. 3
Spurious electrical components within normal two-winding transformer is by
using a ferromagnetic core material having a high permeability, such as Permalloy
(u = 20, 000- 100, 000) or Mu-metal (p- 30,000- 150,000), but all ferromagnetic
core materials cause waveform distortion, and their permeability decreases
with increasing operating frequency.
A dramatic demonstration of the problems caused by non-linearity in the 'B-H'
characteristics of ferromagnetic materials can be given by placing a ferrite
bead over the output lead between a high quality audio amplifier and its load.
The immediate effect of this is that the distortion in the amplifier output
will be greatly increased and changed from a smooth, low-order harmonic type
to a spiky waveform rich in high-order harmonic components -- distortion which
disappears again if the ferrite bead is removed.
To avoid the distortion caused by the core, in those applications where relatively
low values of inductance are required, as, for example, in the inductors and
transformers used in low impedance loudspeaker crossover networks, air-cored
coils are invariably employed, in spite of their greater physical size.
For good audio performance, in transformer coupled audio amplifiers, it is
necessary to employ negative feedback (NFB) in the amplifier design, and, in
view of the distortion which can arise in the loudspeaker coupling transformer,
it is essential that this component shall also be included in the NFB loop.
For this to be practicable without causing NFB loop instability, the low frequency
performance of the transformer- principally determined by its primary inductance--and
its high frequency characteristics--mainly resulting from the primary/secondary
leakage inductance and the inter-winding capacitances--must also be controlled
within limits set by the gain/phase relationships of the remainder of the amplifier.
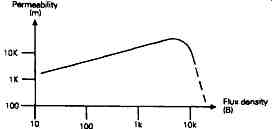
FIG. 4 Typical relationship between permeability and flux density in silicon
steel core material
An intrinsic difficulty in the use of any ferromagnetic material for the core
of an inductor or transformer is that the permeability of the core material,
and hence the inductance of the coil, is dependent on the magnetic flux density
generated by the current flowing in the windings. This leads to the type of
relationship between core inductance and AC excitation voltage shown in FIG.
4. To ensure that the transformer performance is equally good at low signal
levels as at medium levels, this minimum field inductance, known as the incremental
inductance, should be the value specified. The rapid decrease in core inductance
at high excitation levels, also shown in FIG. 4, is a frequent cause of high
power waveform distortion.
Where an inductor was to be used as a unit of impedance, as for example as
a smoothing choke in a power supply circuit, where its high AF impedance could
be used, in conjunction with a large value output capacitor, to assist in smoothing
out the residual AC tipple from a simple rectifier/reservoir capacitor power
supply, it was common practice to leave a deliberate air gap in the core to
lessen the inductance loss due to core saturation by the DC current flow. This
was also normal practice if such an inductor was used as a swinging choke,
connected between the rectifier and the output of a choke input type of power
supply.
An excellent analysis of the design problems which the output transformer
introduces, and a practical approach to the solution of these, was given by
D. T. N. Williamson (Wireless World, April 1947, pp. 118-121) in his article
describing a design for a high quality audio amplifier. In his competitive
amplifier system, P. J. Baxandall (Wireless World, January 1948, pp. 2-6) described
a method (mainly due to C. G. Mayo of the BBC Research Dept.) which simplified
the problems of overall NFB by taking the feedback voltage from a tertiary
transformer winding. In practice, however, this technique gives less good results
than if the NFB is derived from the LS output terminals, and segmented and
interleaved windings are used, as described by Williamson, to reduce the inter-winding
leakage inductance.
All in all, however, the output transformer of a tube audio amplifier is an
awkward component to live with, and it could be argued that one of the major
advantages inherent in low output impedance solid-state designs is that an
output transformer is unnecessary. In the past, AF chokes were occasionally
used as the anode loads of amplifier stages. These components would introduce
similar problems, and are very rarely found in any contemporary designs.
Capacitors
These components can be divided into two main categories -- polar and non-polar
-- and each of these capacitor types has its own set of advantages and snags.
Polar capacitors are those like aluminum and tantalum electrolytics, together
with some exotic ceramic-dielectric components, which are sensitive to the
polarity of any direct voltage applied across them, whereas the non-polar capacitors
are not. All capacitors, in their most basic form, consist of a pair of electrically
conducting plates, or electrodes, separated by a gap filled with air or some
other material, known as the dielectric. The differences between capacitor
types relate to the nature and form of the dielectric material and the type
of electrode used. In electrolytic capacitors, very large values of capacitance
can be provided in relatively small package dimensions, but their actual capacitance
will seldom be specified with any degree of accuracy.
Because a current must flow into, or out of, a capacitor when it is charged
or discharged, if the external circuit resistance is sufficiently high that
no significant current flow can occur in the external circuit, and consequently
no change in the state of charge of the capacitor, then any change in the potential
on one electrode of the capacitor must cause an identical potential change
on the other. This provides a very useful method of transferring a voltage
change from one circuit to another, when a direct connection cannot be made
between them because they are not at the same DC potential. In this sense,
it acts in a similar manner to an inter-stage coupling transformer, but with
very much less signal distortion or sensitivity to the frequency of the signal.
By the same argument, if there is little current flow into the capacitor,
then the potential across it will not change to any great extent. This is the
basis of the use of a capacitor for AF bypass, or smoothing, or decoupling
applications. The effectiveness of a capacitor in these uses becomes greater
if the turnover frequency (f0) due to the value of the capacitor and the resistance
of the external circuit (Rext) is made lower.
This frequency can be found from the relationship:
f0 = 1/(2 Pi C Rext)
Electrolytic capacitors
The capacitance of a capacitor is related to the thickness (d) of the (insulating)
dielectric layer, and the relative dielectric constant (k) of that layer (as
compared with a vacuum) by the equation:
C = MkA/d
where M is some constant depending on the type of construction, and A is the
area of the electrodes. The dielectric constant is a measure, analogous to
that of the permeability of a magnetic core material, of the amount by which
the capacitance of a capacitor will be increased by the use of that particular
insulating material instead of a vacuum (or, for all practical purposes, air).
For a given electrode area the capacitance of the capacitor can be increased
by making the dielectric layer thinner, and by using a dielectric with a higher
value of k. The problem with making the dielectric layer thinner is that it
may suffer an electrical breakdown in use, when the capacitor will cease to
be usable, unless some method exists by which it can heal itself. Using a higher
dielectric constant for the insulating layer between the plates is an option
which depends mainly on what is available in a suitable physical form.
The electrolytic capacitor construction attempts to solve all of these problems
by using an electrochemically formed layer of insulation, such as aluminum
oxide on an aluminum foil electrode, or a tantalum oxide layer on a tantalum
foil substrate. Not only do these oxide layers have a high dielectric constant
(k = 9 for Al2 O3, k = 26 for Ta2 O5), but since it is arranged that some electrolyte
will still be present within the capacitor body, electrolytic processes can
continue, so long as there is any voltage (of the correct polarity) between
the electrodes. By this mechanism, any points at which electrical breakdown
has occurred will be healed automatically.
A further advantage of the electrolytic is that when the oxide film is sufficiently
thick to prevent further current flow the film growth stops. This means that
the dielectric thickness is never greater than is needed to arrest the flow
of current at the voltage at which it was formed. Together with the high-k
dielectric layer, this property means that such capacitors will offer relatively
large values of capacitance in very small physical sizes. For example, a solid
dielectric, epoxy resin encapsulated tantalum bead capacitor, having a capacitance
of 100uF at a working voltage of 10V, can be physically only the size of a
pea.
Unfortunately, the oxide insulating film in an electrolytic capacitor will
tend to deteriorate during storage, or in use in applications where there is
no voltage normally present between the plates, as a result of which the leakage
resistance between the plates will decrease. If a voltage is then applied,
a relatively large leakage current will flow, which will decrease as the dielectric
layer slowly heals its weak points. Tantalum electrolytic capacitors are superior
to aluminum based ones in this respect, and may even tolerate short duration
DC polarity reversals, up to one or two volts.
Aluminum electrolytic capacitors dominate the larger capacitance and higher
working voltage capacitor styles, with values in the range 1uF-470,000uF at
working voltages in the range of 4V-600V DC, though, of course, the larger
capacitance values will usually only be available at the lower working voltages.
Unfortunately, leakage currents are always present in electrolytic capacitors,
and these currents are noisy. This limits their use in inter-stage coupling
applications, though leakage currents are usually very low in the tantalum
electrolytics. Aluminum bead capacitor types have been introduced recently
which are similar in physical size and capacitance values to their more expensive
tantalum based equivalents, but they are still not as good in their tolerance
of polarity reversals.
A further problem in electrolytic capacitors is that there is a significant
amount of resistance in series with the capacitor element, either due to the
narrow internal strips of foil which are used to make connection to the wound
foil electrodes, in a spiral wound capacitor, or due to the relatively poor
conductivity of the electrolyte itself.
This inadvertent resistive element is of importance in capacitors used for
power supply applications, and is known as the equivalent series resistance
or ESR, and should be as low as possible in this use.
The other measure of the lack of perfection of a capacitor, its dielectric
loss, also known as dielectric hysteresis loss (roughly analogous to the core
losses in a transformer), is due to the residual hysteresis losses in the dielectric
when the polarity is reversed. Since this loss occurs each time the applied
voltage is reversed the energy loss is roughly proportional to signal frequency,
and, in an equivalent circuit, of the kind shown in FIG. 5, would be represented
by a further resistance in series with the capacitance.
In FIG. 5b, C is the capacitance, and Rk is the dielectric loss, both of which
will depend somewhat on operating frequency, voltage and temperature, Rs is
the equivalent series resistance, due to internal connections, L s is the series
inductance, RE is the leakage resistance of the component, and the CC terms
refer to various internal stray capacitances. The equivalent circuits of FIGs
5c and 5d relate to electrolytic and high-k ceramic capacitors, which have
further problems of reverse conduction and dielectric hysteresis, shown respectively
as D and E_e in the diagrams.
Although each of these spurious effects will be important in some circumstances,
most of them can be ignored for most of the time.
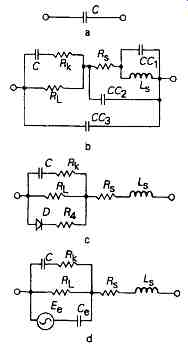
FIG. 5 Spurious components inherent in capacitors
If there is, in use, any leakage current between the capacitor electrodes,
as there will always be in electrolytic capacitors, this will appear as a resistance
in parallel with the capacitor in its electrical equivalent circuit, and will
increase its effective equivalent dielectric loss. This is normally measured
as the tangent of the phase angle (8) between the reactive and resistive components
of an alternating current flow.
Values for tan delta, at 1kHz, range from 0.02 for an electrolytic, down to
0.00008 for an electrical grade polypropylene film. Losses increase with frequency,
but, except in the case of electrolytics, will not alter much throughout the
normal audio frequency range.
Non-polar capacitors
A variety of styles and dielectrics are used in these, mainly dependent on
the working voltages or capacitance values required. Where small, stable, but
precisely known values of capacitance are necessary, capacitors based on a
stack of metallized sheets of mica or on a Swiss roll type of construction
using aluminum foil interleaved with polystyrene film are preferred. These
have low losses and capacitance values which are stable with time.
Where very low values of series inductance are essential, as, for example,
in RF bypass applications, metallized ceramic dielectric types are preferred.
These can offer either large but imprecise capacitance values in a small size,
or very small but accurately defined values. All ceramic capacitors have capacitance
values which are dependent on temperature, usually specified by descriptions
such as N750 or P100, or simply high k (always N type), where the N or the
P refer to their negative or positive temperature coefficient of capacitance,
and the number refers to this temperature coefficient, in parts per million,
per degree centigrade.
By far the most common types of non-polar capacitor are those made from a
spiral wound sandwich of an insulating thermoplastic film dielectric and a
high conductivity metal foil, usually made from high purity aluminum. A wide
range of films have been used for this purpose, of which the most commonly
found are polycarbonate, polyester, polypropylene, polysulphone or PTFE. The
last two of these are mainly found in high temperature and military applications,
where their high cost is acceptable. All wound film/foil capacitors will have
some effective series inductance, because of their construction, as indicated
in FIG. 5b. This is not usually an important factor in the frequency range
typical in audio applications, though some manufacturers squash their wound
structure into a more slab-like form, before encapsulation, to reduce this
inductance.
Self-healing properties can be built into capacitors using thin thermoplastic
insulating materials by using a vacuum metallized layer deposited on the surface
of the dielectric film, instead of a spiral length of metal foil. Then, in
the event of an electrical puncture occurring in the film dielectric, the resulting
spark discharge will burn away the metallized layer around the point of breakdown
in the manner shown in FIG. 6, and the short-circuit between the electrodes
will then be cleared. This type of capacitor construction allows much thinner
dielectric films to be used with safety, and consequently relatively high values
of capacitance in a small package size, but, because of the thinness of the
conductive layer, such capacitors will always have a high ESR, and a relatively
high value of tan delta.
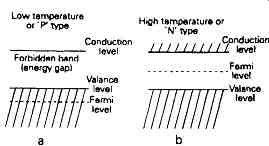
FIG. 6 Effect of self-healing of metallized film capacitor
Waxed paper/foil capacitors were the mainstay of tube amplifier circuitry,
but they always suffered from noisy leakage currents due to the ingress of
moisture. Happily, these capacitors are now almost unknown in small-signal
circuitry.
In audio amplifier applications, the choice will mainly lie between polystyrene
(k = 2.5), polycarbonate (k = 2.8-3), polyester (k = 2.8-3.2) and polypropylene
(k = 2.2) film dielectric metal foil components, depending on the requirements
of the circuit application. Of these, polystyrene types will be used where
low capacitance components, having stable and accurate capacitance values,
are needed- as in filter circuitry or frequency response shaping networks.
Polypropylene or polycarbonate capacitors would be the component of choice
where it is to be used in the signal line, and low-cost polyester capacitors
for other, non-critical applications.
Dielectric remanence
In certain dielectric materials the electrical dipoles within the dielectric,
whose change in orientation on the application of an electric field is the
major source of the dielectric constant of that material, can remain locked
in their orientation even after the applied field has been removed, giving
rise to an effective stored charge. In this respect, their behavior is analogous
to the persistence of orientation of the magnetic dipoles in a permanent magnet,
and this effect in an insulating film is called electret formation, and is
deliberately sought to provide materials for use in things such as electret
microphones or headphones. Electrets occur more readily in materials having
a high degree of rigidity in their structure, and are thus more readily formed
in materials having an essentially crystalline structure such as biaxially
oriented polyester and polypropylene films than in essentially limp and amorphous
solution-cast films like those of polystyrene or polycarbonate. The ill effects,
if any, of such stored charges in the audio field are not known, but their
possible existence should be recognized.
A related point concerns the observations of those people who specialize in
the assessment of the quality of audio systems from judgments formed during
personal listening trials, and who have, as a result of these trials, declared
the superiority of one type of component over another in respect of its sound
quality. A particular instance of this kind concerns polypropylene film/foil
capacitors, which are alleged to 'sound better' in audio systems than any other
comparable type.
As it happens, I was employed for many years in the research laboratories
of a large-scale manufacturer of thermoplastic films, whose product range included
several types of polypropylene film, intended for use in both packaging and
electrical applications.
Part of my duty was to provide technical support to the manufacturers of capacitors
using our electrical grade films, and we had a very well-equipped laboratory
for testing films, both in sheet form, and as wound capacitors. During my work,
I visited many capacitor manufacturing companies, and tested their capacitors
for such things as dielectric loss, breakdown voltage and electrical remanence
(stored charge). Part of my employer's product range was a biaxially oriented
polypropylene film, made from very high purity electrical grade polymer granules
on machines which were kept scrupulously clean and free from potentially deleterious
contaminants. This film was, of course, more expensive than the low purity,
and relatively poor electrical quality, packaging grade films, made on machines
principally designed to provide a high film output. The capacitor manufacturers
noted this difference, but often used the cheapest film they could get, either
from my own company, or from competitive suppliers with whose products I was
familiar, because they said their own customers could not tell the difference,
and mainly bought those capacitors which were cheapest.
If there were significant differences in audio sound quality due to electrical
differences, these differences would, I thought, have been exposed by those
who made the pursuit of this quality their business, and would have observed
that one make of polypropylene capacitor sounded better than another.
Resistors
Like capacitors, these are made in a range of types from a variety of materials,
and have qualities which differ somewhat one from another.
Fixed resistors
For low power applications, where small size is generally sought, the most
common construction is that of a small ceramic rod, having a suitable coefficient
of thermal expansion, coated with a film of carbon, or metal, or tin oxide,
or some other resistive glaze. The resistivity and the thickness of the deposited
layer, applied as the first stage of manufacture, is then chosen to give a
somewhat lower resistance to the composite rod- as measured between conductive
metal caps attached at either end of the rod- than the target value, and a
spiral groove is then cut through the resistive coating material, to lengthen
the surface conductive path and increase the resistance value to the required
figure. Connecting wires are then attached to the end caps, the resistor is
dipped in some tough protective lacquer, and finally, the resistor value, and
the tolerance (the manufacturers' permitted margin of error in the actual resistance),
is printed on the body, or, alternatively, these parameters may be shown by
the use of an internationally agreed colour code, as shown in Table 1.
====
In principle, since the dielectric loss factor of a capacitor is frequency
dependent, and in the case of an electrolytic, also dependent on the applied
voltage, it would seem probable that capacitors could introduce waveform distortion
into any audio line which contained them.
However, I have made many measurements of this kind of circuit, and my conclusions
are that the distortion levels due to this effect are too small to be easily
identifiable by conventional test procedures. Unfortunately, not finding any
measurable defects does not guarantee that such performance shortcomings, do
not give rise to effects which may be audible to the perceptive listener.
====
For example, a 47k-ohm, 5% tolerance resistor would be coded with the sequence
of colour bands, starting at one end of the body, of yellow, violet, orange,
gold, where the third band (orange) indicated the number of zeros (3) following
the coded number 47, and the band of gold indicated a +5% tolerance value.
Where higher accuracies are required the number of colour bands is increased,
so that a 47k5-ohm (47, 500 ohm), 1% tolerance resistor would be coded with
yellow, violet, green, red and brown bands, to indicate that there would be
two zeros following the number 475, and the final brown band would denote the
i 1% tolerance specification. (This colour code system has also been used to
indicate the value of capacitors, measured in pF, especially radial lead polyester
block types.)
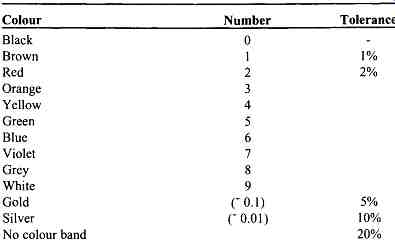
Table 1 The resistor color code system
Metal film resistors are available at dissipation ratings from 0.125 to 0.4
watts, while carbon film types cover the range 0.125-2 watts. For higher power
dissipations, up to, say, 200W, wirewound resistors are available in a variety
of forms.
Because semiconductor circuitry is generally associated with low voltage,
low dissipation devices, it is often forgotten that there will be a maximum
voltage rating as well as a maximum dissipation figure for a resistor, typically
200V for a 0.125W metal film resistor, and up to 700V for a 2W carbon film
one.
All resistors, even wirewound ones, are prone to some irreversible change
in their resistance value if their permitted heat dissipations are exceeded.
This was a particular problem with the wax impregnated carbon-composition rod
types (which were basically fired clay rods containing a proportion of graphite
in their body), whose actual value would not be known, until after the firing.
This value would then be moderately permanent, unless of course they were allowed
to get hot in use, when they would change in their value once more. Luckily,
this type of resistor- widely used in vintage audio systems - is no longer
made, and only found in museum pieces.
All modem fixed value resistors from reputable manufacturers will have resistance
values which are very close to their marked figures, though these can be affected
by heat, so it is generally prudent to avoid heating the body excessively when
soldering, or to make solder joints too close to the resistor body.
Noise
All circuits suffer from thermal or Johnson noise, proportional to the circuit
resistance, its temperature and the effective measurement bandwidth. In addition,
there will be a certain amount of excess or 1/f noise, as a result of the physical
imperfections in the manufacture of the constituent components. There are small
differences in this excess noise between the various types of modem resistors
but these are usually insignificant, except in very low signal level, low-frequency
circuitry. For the purist tin oxide film, metal glaze or wirewound types with
welded end leads are the best. For low powers, metal film resistors are the
next best choice.
Inductance
Most film type resistors are virtually non-inductive. Wirewound types are
inductive, unless otherwise specified, but this is not likely to be important
except in the power output stages of audio amplifiers, or in wirewound variable
resistors.
Potentiometers and variable resistors
It is a common requirement that it should be possible to alter the resistance
between two points in a circuit, or to select the proportion of a voltage occurring
between specific points. For this purpose a range of three-terminal potentiometers
are made, using many of the techniques used in the manufacture of fixed-value
resistors, but with the provision of a sliding contact which allows a connection
to be made to the resistor body at some chosen point along its length.
Predictably, the problem arises that any sliding contact will be less satisfactory
than a fixed one in respect of its noise component or its stability of resistance
value. In high quality systems the best quality potentiometers should be chosen,
since the imperfections in cheap and cheerful components can have a disproportionately
large effect on the system performance. In terms of quality, wirewound potentiometers
are probably the best, with cermet (resistive ceramic) or conductive plastic
track types the next best option. The mainstays of low cost potentiometers
are those with carbon composition tracks, with either graphite rod (better)
or spoon-shaped metal (less good) sliders as the means of making contact to
the track.
There will always be some mechanical wear in the repeated use of any adjustable
component, usually made visible or audible by the slider contact becoming intermittent,
and electrically noisy in its track to slider connection, so the better quality
components should always be employed in those places such as amplifier gain
controls which are likely to experience the most use.
Potentiometers are also available in twin-gang types, to meet the needs of
stereo systems. The tracks of these will nearly always be of relatively low
quality carbon composition type, and there will often be noticeable differences
in these between the proportion of the resistance tapped off by the sliders
in each of the two tracks. This is even more conspicuously the case where each
track of the twin-gang potentiometer is required to have a logarithmic relationship
between the tapped-off resistance and the slider rotation. So, where a high
standard of performance is sought, the style of potentiometer is one of the
areas where particular care should be taken in the choice of components.
Switches and Electrical Contacts
These components are a matter of particular interest in audio amplifier design,
because the operation of any audio system will require the interconnection
of many different units, and the switching of many electrical signal paths
within those units, and this can open the way to a number of potential problems.
In its simplest form, the difficulty is that any conducting metallic surface
which is exposed to the air will, in due course, become coated with grease,
dust, and other non-conducting contaminants. The surface will also suffer from
chemical degradation because of the effects of oxygen, sulphur dioxide, and
other corrosive gases in the atmosphere.
If little or no electrical current passes between such contacts there may
not be enough voltage across the contaminant layer to cause it to break down,
so that an unsuspected high or variable resistance may be introduced in the
circuit. Higher contact currents are obviously preferable from this point of
view, but, on the other hand, chemical changes to the conductor surface may
form thin semiconducting inter-metallic layers which are capable of passing
quite high currents without disruption, but which will distort the signal voltage
waveform.
If the contacts are arranged to slide over one another, as in the case of
a switch, the wiping action will help to keep the contacting surfaces clean,
but if there is much current flow through these, electrical arcing may occur,
which will erode the contact surfaces. Overall, pure silver offers the best
of the lower priced contact materials, while, if cost is unimportant, gold-plated
palladium/nickel alloy contacts offer the best combination of performance with
life expectancy.
Little can be done about such things as fuse-holders in a loudspeaker circuit,
which may have to pass substantial currents, since the fuses themselves will
be relatively crude, low cost components, tin-plated at best. The only really
satisfactory answer is to choose some other type of loudspeaker protection,
such as a high quality, inert gas filled relay, with adequately sized, gold-plated
contacts, or, alternatively, some purely electronic means of protection.
Until comparatively recently, the interconnections between components in a
- which I think to be correct - is that the means of connection are things
which should be considered with equal care, in a high quality audio system,
to any of the components which they join. In particular, the tracks on the
printed circuit boards, or the external wiring, or the mechanical connectors
which join those parts of the circuit which can pass large currents, such as
the leads to loudspeaker outputs, transformers, capacitors or power supply
rectifiers, should be of adequate gauge and of carefully chosen route and type
if signal impairment is to be avoided.
===
|