<< prev.
9. DVD and CD readout in detail
The CD medium is designed to be read with a phase contrast microscope, and
so it is correct to describe the deformities on the information layer as a
phase structure. The original LaserVision disk patent 7 contains a variety
of approaches, but in the embodiment used in CD it consists of two parallel
planes separated by a distance which is constant and specifically related to
the wavelength of the light which will be used to read it. The phase structure
is created with deformities which depart from the first of the planes and whose
extremities are in the second plane. These deformities are called pits when
the second plane is below the first and bumps when the second plane is above
the first.
Whilst a phase structure can be read by transmission or reflection, commercial
designs based the Philips medium, such as LaserVision, 8 DVD, CD, CD-Video,
CDROM and prerecorded MiniDisc, use reflective readout exclusively.
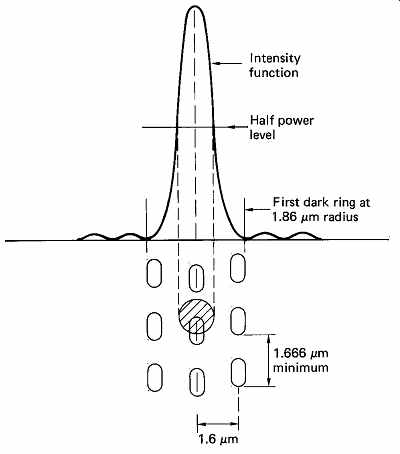
FIG. 26 The structure of a maximum frequency recording is shown here,
related to the intensity function of an objective of 0.45NA with 780nm light.
Note that track spacing puts adjacent tracks in the dark rings, reducing crosstalk.
Note also that as the spot has an intensity function it is meaningless to specify
the spot diameter without some reference such as an intensity level.
Optical physicists characterize materials by their reflectivity, transmissivity
and absorption. Light energy cannot disappear, so when light is incident on
some object, the amounts of light transmitted, absorbed and reflected must
add up to the original incident amount. When no light is absorbed, the incident
light is divided between that transmitted and that reflected. When light is
absorbed, the transmitted and reflected amounts of light are both reduced.
A medium such as a photograph contains pigments which absorb light more in
the dark areas and less in the light areas. Thus the amount of light reflected
varies. A medium such as a transparency also contains such pigments but in
this case it is primarily the amount of light transmitted which varies. Such
a variation in transmitted or reflected light from place to place is known
as contrast.
FIG. 2(a) showed that in CD, the information layer consists of an optically
flat surface above which flat-topped bumps project. The entire surface of the
phase structure is metallized to render it reflective. This metallization of
the entire information layer means that little light is transmitted or absorbed,
and as a result virtually all incident light must be reflected. The information
layer of CD does not have conventional contrast. Contrast is in any case unnecessary
as interference is used for readout, and this works better with a totally reflecting
structure.
Referring to FIG. 26 it will be seen that a spot of light is focused
onto the phase structure such that it straddles a bump. Ideally half the light
energy should be incident on the top of the bump and half on the surrounding
mirror surface. The height of the bump is ideally one quarter the wavelength
of the light in a reflective system and as a result light which has reflected
from the mirror surface has travelled one half a wavelength further than light
which has reflected from the mirror surface. Consequently, along the normal,
there are two components of light of almost equal energy, but they are in phase
opposition, and destructive interference occurs, such that no wavefront can
form in that direction. As light energy cannot disappear, wavefronts will leave
the phase structure at any oblique angle at which constructive interference
between the components can be achieved, creating a diffraction pattern.
In the case of the light beam straddling the center of a long bump the diffraction
pattern will be in a plane which is normal to the disk surface and which intersects
a disk radius. It is thus called a radial diffraction pattern. The zeroth-order
radiation (that along the normal) will be heavily attenuated, and most of the
incident energy will concentrated in the first- and second-order wavefronts.
Some treatments use the word scattering to describe the effect of the interaction
of the readout beam with the relief structure. This is technically incorrect
as scattering is a random phenomenon which is independent of wavelength. The
diffraction pattern is totally predictable and strongly wavelength dependent.
When the light spot is focused on a plain part of the mirror surface, known
as a land, clearly most of the energy is simply reflected back whence it came.
Thus when a bump is present, light is diffracted away from the normal, whereas
in the absence of a bump, it returns along the normal. Although all incident
light is reflected at all times, the effect of diffraction is that the direction
in which wavefronts leave the phase structure is changed by the presence of
the bump. What then happens is a function of the optical system being used.
In a conventional CD player the angle to the normal of the first diffracted
order in the radial diffraction pattern due to a long bump will be sufficiently
oblique that it passes outside the aperture of the objective and does not return
to the photosensor. Thus the bumps appear dark to the photosensor and the lands
appear bright. Although all light is reflected at all times and there is no
conventional contrast, inside the pickup there are variations in the light
falling on the photosensor, a phenomenon called phase contrast.
The phase contrast technique described will only work for a given wavelength
and with an appropriate aperture and lens design, and so the CD must be read
with monochromatic light. Whilst the ideal case is where the two components
of light are equal to give exact cancellation, in practice this ideal is not
met but instead there is a substantial reduction in the light returning to
the pickup.
Some treatments of CD refer to a 'beam' of light returning from the disk to
the pickup, but this is incorrect. What leaves the disk is a hemispherical
diffraction pattern certain orders of which enter the aperture of the pickup.
The destructive interference effect can be seen with the naked eye by examining
any CD under a conventional incandescent lamp. The data surface of a CD has
many parallel tracks and works somewhat like a diffraction grating by dispersing
the incident white light into a spectrum.
However, the resultant spectrum is not at all like that produced by a conventional
diffraction grating or by a prism. These latter produce a spectrum in which
the relative brightness of the colors is like that of a rainbow, i.e. the green
in the center is brightest, the red at one end is less bright and the blue
at the other end is fainter still. This is due to the unequal response of the
eye to various colors, where equal red, green and blue stimuli produce responses
in approximately the proportions 2:5:1 respectively. In the diffracted spectrum
from a CD, however, the blue component appears as strong or stronger than the
other colors. This is because the relief structure of CD is designed not to
reflect infrared light of 780 nm wavelength. This relief structure will, however,
reflect perfectly ultraviolet light of half that wavelength as the zeroth-order
light reflected from the top of the bumps will be in phase with light reflected
from the land. Thus a CD reflects visible blue light much more strongly than
longer-wavelength colors.
It is essential to the commercial success of CD that a useful playing time
(75min max.) should be obtained from a recording of reasonable size (12 cm).
The size was determined by the European motor industry as being appropriate
for car dashboard-mounted units. It follows that the smaller the spot of light
which can be created, the smaller can be the deformities carrying the information,
and so more information per unit area (known in the art as the superficial
recording density) can be stored.
Development of a successful high-density optical recorder requires an intimate
knowledge of the behavior of light focused into small spots. If it is attempted
to focus a uniform beam of light to an infinitely small spot on a surface normal
to the optical axis, it will be found that it is not possible. This is probably
just as well as an infinitely small spot would have infinite intensity and
any matter it fell on would not survive. Instead the result of such an attempt
is a distribution of light in the area of the focal point which has no sharply
defined boundary. This is called the Airy distribution9 (sometimes pattern
or disk) after Lord Airy (1835), the then astronomer royal. If a line is considered
to pass across the focal plane, through the theoretical focal point, and the
intensity of the light is plotted on a graph as a function of the distance
along that line, the result is the intensity function shown in FIG. 26.
It will be seen that this contains a central sloping peak surrounded by alternating
dark rings and light rings of diminishing intensity. These rings will in theory
reach to infinity before their intensity becomes zero. The intensity distribution
or function described by Airy is due to diffraction effects across the finite
aperture of the objective. For a given wavelength, as the aperture of the objective
is increased, so the diameter of the features of the Airy pattern reduces.
The Airy pattern vanishes to a singularity of infinite intensity with a lens
of infinite aperture which, of course, cannot be made. The approximation of
geometric optics is quite unable to predict the occurrence of the Airy pattern.
An intensity function does not have a diameter, but for practical purposes
an effective diameter typically quoted is that at which the intensity has fallen
to some convenient fraction of that at the peak. Thus one could state, for
example, the half-power diameter.
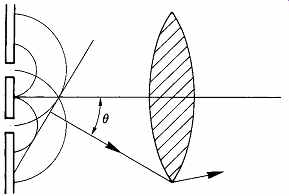
FIG. 27 Fine detail in an object can only be resolved if the diffracted
wavefront due to the highest spatial frequency is collected by the lens. Numerical
aperture (NA) = sin θ, and as θ is the diffraction angle it follows
that, for a given wavelength, NA determines resolution.
Since light paths in optical instruments are generally reversible, it is possible
to see an interesting corollary which gives a useful insight into the readout
principle of CD. Considering light radiating from a phase structure, as in
FIG. 27, the more closely spaced the features of the phase structure,
i.e. the higher the spatial frequency, the more oblique the direction of the
wavefronts in the diffraction pattern which results and the larger the aperture
of the lens needed to collect the light if the resolution is not to be lost.
The corollary of this is that the smaller the Airy distribution it is wished
to create, the larger must be the aperture of the lens. Spatial frequency is
measured in lines per millimeter and as it increases, the wavefronts of the
resultant diffraction pattern become more oblique. In the case of a CD, the
smaller the bumps and the spaces between them along the track, the higher the
spatial frequency, and the more oblique the diffraction pattern becomes in
a plane tangential to the track. With a fixed-objective aperture, as the tangential
diffraction pattern becomes more oblique, less light passes the aperture and
the depth of modulation transmitted by the lens falls. At some spatial frequency,
all the diffracted light falls outside the aperture and the modulation depth
transmitted by the lens falls to zero. This is known as the spatial cut-off
frequency. Thus a graph of depth of modulation versus spatial frequency can
be drawn and which is known as the modulation transfer function (MTF). This
is a straight line commencing at unity at zero spatial frequency (no detail)
and falling to zero at the cut-off spatial frequency (finest detail). Thus
one could describe a lens of finite aperture as a form of spatial low-pass
filter. The Airy function is no more than the spatial impulse response of the
lens, and the concentric rings of the Airy function are the spatial analog
of the symmetrical ringing in a phase-linear electrical filter. The Airy function
and the triangular frequency response form a transform pair10 as shown in Section
3.
When an objective lens is used in a conventional microscope, the MTF will
allow the resolution to be predicted in lines per millimeter. However, in a
scanning microscope the spatial frequency of the detail in the object is multiplied
by the scanning velocity to give a temporal frequency measured in Hertz. Thus
lines per millimeter multiplied by millimeters per second gives lines per second.
Instead of a straight-line MTF falling to the spatial cut-off frequency, a
scanning microscope has a temporal frequency response falling to zero at the
optical cut-off frequency. Whilst this concept requires a number of idiomatic
terms to be assimilated at once, the point can be made clear by a simple analogy.
Imagine the evenly spaced iron railings outside a schoolyard. These are permanently
fixed, and can have no temporal frequency, yet they have a spatial frequency
which is the number of railings per unit distance. A small boy with a stick
takes great delight in running along the railings so that his stick hits each
one in turn and makes a great noise. The rate at which his stick hits the railings
is the temporal frequency which results from their being scanned.
This rate would increase if the boy ran faster, but it would also increase
if the rails were closer together. As a consequence it can be seen that the
temporal frequency is proportional to the spatial frequency multiplied by the
scanning speed. Put more technically, the frequency response of an optical
recorder is the Fourier transform of the Airy distribution of the readout spot
multiplied by the track velocity.
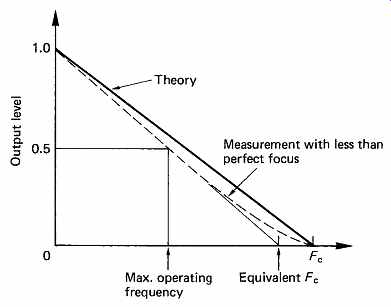
FIG. 28 Frequency response of laser pickup. Maximum operating frequency
is about half of cut-off frequency Fc.
In magnetic recorders and vinyl disk recorders there is at least a frequency
band where the response is reasonably flat. CD is basically a phase contrast
scanning microscope. FIG. 28 shows that the frequency response falls progressively
from DC to the optical cutoff frequency which is given by:
Fc = 2NA/wavelength x velocity
The minimum linear velocity of CD is 1.2m/s, giving a cutoff frequency of:
Fc = 2 x 0.45 x 1.2/780 x 10^-9 = 1.38MHz
Actual measurements reveal that the optical response is only a little worse
than the theory predicts. This characteristic has a large bearing on the type
of modulation schemes which can be successfully employed.
Clearly, to obtain any noise immunity, the maximum operating frequency must
be rather less than the cutoff frequency. The maximum frequency used in CD
is 720 kHz, which represents an absolute minimum wavelength of 1.666 um, or
a bump length of 0.833 um, for the lowest permissible track speed of 1.2m/s
used on the full-length 75min-playing disks. One-hour-playing disks have a
minimum bump length of 0.972m at a track velocity of 1.4m/s. The maximum frequency
is the same in both cases. This maximum frequency should not be confused with
the bit rate of CD since this is different owing to the channel code used.
FIG. 26 showed a maximum-frequency recording, and the physical relationship
of the intensity function to the track dimensions.
In a CD player, the source of light is a laser, and this does not produce
a beam of uniform intensity. It is more intense in the center than it is at
the edges, and this has the effect of slightly increasing the half-power diameter
of the intensity function. The effect is analogous to the effect of window
functions in FIR filters (see Section 3). The intensity function can also be
enlarged if the lens used suffers from optical aberrations. This was studied
by Marechal [11] who established criteria for the accuracy to which the optical
surfaces of the lens should be made to allow the ideal Airy distribution to
be obtained. CD player lenses must meet the Marechal criterion. With such a
lens, the diameter of the distribution function is determined solely by the
combination of numerical aperture (NA) and the wavelength. When the size of
the spot is as small as the NA and wavelength allow, the optical system is
said to be diffraction limited.
FIG. 27 showed how numerical aperture is defined, and illustrates that
the smaller the spot needed, the larger must be the NA. Unfortunately the larger
the NA, the more obliquely to the normal the light arrives at the focal plane
and the smaller the depth of focus will be. This was investigated by Hopkins,
12 who established the depth of focus available for a given NA. CD players
have to use an NA of 0.45 which is a compromise between a small spot and an
impossibly small depth of focus. [13]
The later DVD uses an NA of 0.6 in conjunction with a shorter wavelength laser.
This allows a significant reduction in the size of the recorded bumps and a
corresponding increase in storage density.
Essentially the information layer of DVD is a scaled-down CD.
The intensity function will also be distorted and grossly enlarged if the
optical axis is not normal to the medium. The initial effect is that the energy
in the first bright ring increases strongly in one place and results in a secondary
peak adjacent to the central peak. This is known as coma and its effect is
extremely serious as the enlargement of the spot restricts the recording density.
The larger the NA, the smaller becomes the allowable tilt of the optical axis
with respect to the medium before coma becomes a problem. With the NA of CD
this angle is less than a degree. [13]
Numerical aperture is defined as the cosine of the angle between the optical
axis and rays converging from the perimeter of the lens. It will be apparent
that there are many combinations of lens diameter and focal length which will
have the same NA. As the difficulty of manufacture, and consequently the cost,
of a lens meeting the Marechal criterion increases disproportionately with
size, it is advantageous to use a small lens of short focal length, mounted
close to the medium and held precisely perpendicular to the medium to prevent
coma. As the lens needs to be driven along its axis by a servo to maintain
focus, the smaller lens will facilitate the design of the servo by reducing
the mass to be driven. It is extremely difficult to make a lens which meets
the Marechal criterion over a range of wavelengths because of dispersion. The
use of monochromatic light eases the lens design as it has only to be correct
for one wavelength.
At the high recording density of CD, there is literally only one scanning
mechanism with which all the optical criteria can be met and this is the approach
known from the scanning microscope. The optical pickup is mounted in a carriage
which can move it parallel to the medium in such a way that the optical axis
remains at all times parallel to the axis of rotation of the medium. The latter
rotates as the pickup is driven away from the axis of rotation in such a way
that a spiral track on the disk is followed. The pickup contains a short focal
length lens of small diameter which must therefore be close to the disk surface
to allow a large NA. All high-density optical recorders operate on this principle
in which the readout of the carrier is optical but the scanning is actually
mechanical.
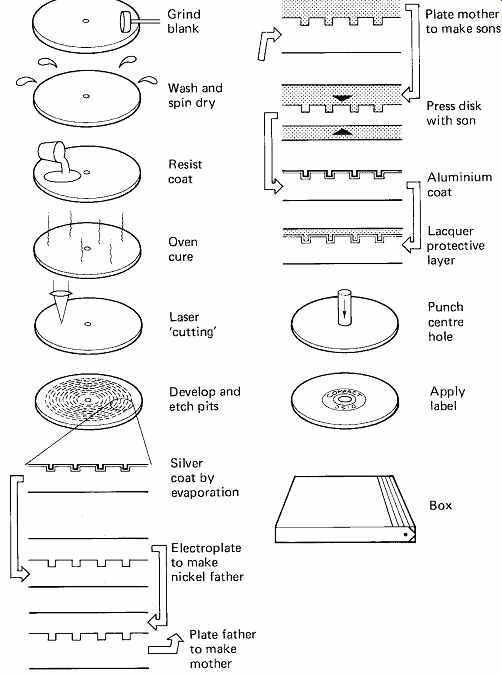
FIG. 29 The many stages of CD manufacture, most of which require the
utmost cleanliness.
10. How optical disks are made
The steps used in the production of CDs will next be outlined.
Prerecorded MiniDiscs are made in an identical fashion except for detail differences
which will be noted. MO disks need to be grooved so that the track-following
system will work. The grooved substrate is produced in a similar way to a CD
master, except that the laser is on continuously instead of being modulated
with a signal to be recorded. As stated, CD is replicated by molding, and the
first step is to produce a suitable mold.
This mold must carry deformities of the correct depth for the standard wavelength
to be used for reading, and as a practical matter these deformities must have
slightly sloping sides so that it is possible to release the CD from the mold.
The major steps in CD manufacture are shown in FIG. 29. The mastering
process commences with an optically flat glass disk about 220mm in diameter
and 6mm thick. The blank is washed first with an alkaline solution, then with
a fluorocarbon solvent, and spun dry prior to polishing to optical flatness.
A critical cleaning process is then under taken using a mixture of de-ionized
water and isopropyl alcohol in the presence of ultrasonic vibration, with a
final fluorocarbon wash. The blank must now be inspected for any surface irregularities
which would cause data errors. This is done by using a laser beam and monitoring
the reflection as the blank rotates. Rejected blanks return to the polishing
process, those which pass move on, and an adhesive layer is applied followed
by a coating of positive photoresist. This is a chemical substance which softens
when exposed to an appropriate intensity of light of a certain wavelength,
typically ultraviolet. Upon being thus exposed, the softened resist will be
washed away by a developing solution down to the glass to form flat-bottomed
pits whose depth is equal to the thickness of the undeveloped resist. During
development the master is illuminated with laser light of a wavelength to which
it is insensitive. The diffraction pattern changes as the pits are formed.
Development is arrested when the appropriate diffraction pattern is obtained.
[14]
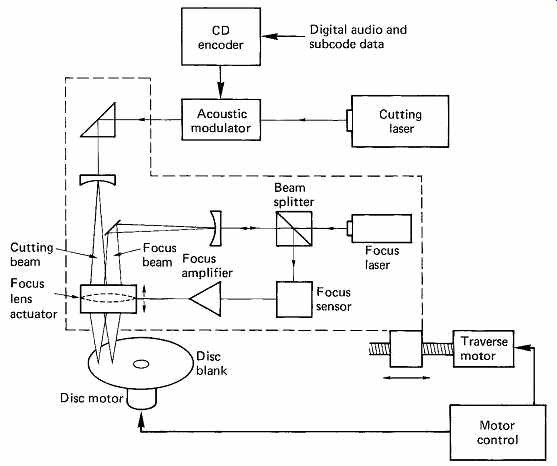
FIG. 30 CD cutter. The focus subsystem controls the spot size of the
main cutting laser on the photosensitive blank. Disc and traverse motors are
coordinated to give constant track pitch and velocity. Note that the power
of the focus laser is insufficient to expose the photoresist.
The thickness of the resist layer must be accurately controlled, since it
affects the height of the bumps on the finished disk, and an optical scanner
is used to check that there are no resist defects which would cause data errors
or tracking problems in the end product. Blanks which pass this test are oven-cured,
and are ready for cutting. Failed blanks can be stripped of the resist coating
and used again.
The cutting process is shown in simplified form in FIG. 30. A continuously
operating helium cadmium-15 or argon ion-16 laser is focused on the resist
coating as the blank revolves. Focus is achieved by a separate helium neon
laser sharing the same optics. The resist is insensitive to the wavelength
of the He-Ne laser. The laser intensity is controlled by a device known as
an acousto-optic modulator which is driven by the encoder.
When the device is in a relaxed state, light can pass through it, but when
the surface is excited by high-frequency vibrations, light is scattered.
Information is carried in the lengths of time for which the modulator remains
on or remains off. As a result the deformities in the resist produced as the
disk turns when the modulator allows light to pass are separated by areas unaffected
by light when the modulator is shut off. Information is carried solely in the
variations of the lengths of these two areas.
The laser makes its way from the inside to the outside as the blank revolves.
As the radius of the track increases, the rotational speed is proportionately
reduced so that the velocity of the beam over the disk remains constant. This
constant linear velocity (CLV) results in rather longer playing time than would
be obtained with a constant speed of rotation. Owing to the minute dimensions
of the track structure, the cutter has to be constructed to extremely high
accuracy. Air bearings are used in the spindle and the laser head, and the
whole machine is resiliently supported to prevent vibrations from the building
from affecting the track pattern.
Early CD cutters worked in real time, but subsequently the operating speed
has been increased dramatically to increase the throughput.
As the player is a phase contrast microscope, it must produce an intensity
function which straddles the deformities. As a consequence the intensity function
which produces the deformities in the photoresist must be smaller in diameter
than that in the reader. This is conveniently achieved by using a shorter wavelength
of 400-500 nm from a helium- cadmium or argon-ion laser combined with a larger
lens aperture of 0.9.
These are expensive, but are only needed for the mastering process.
It is a characteristic of photoresist that its development rate is not linearly
proportional to the intensity of light. This non-linearity is known as 'gamma'.
As a result there are two intensities of importance when scanning photoresist;
the lower sensitivity, or threshold, below which no development takes place,
and the upper threshold above which there is full development. As the laser
light falling on the resist is an intensity function, it follows that the two
thresholds will be reached at different diameters of the function. It can be
seen in FIG. 31 that advantage is taken of this effect to produce tapering
sides to the pits formed in the resist. In the center, the light is intense
enough to fully develop the resist right down to the glass. This gives the
deformity a flat bottom. At the edge, the intensity falls and as some light
is absorbed by the resist, the diameter of the resist which can be developed
falls with depth in the resist. By controlling the intensity of the laser,
and the development time, the slope of the sides of the pits can be controlled.
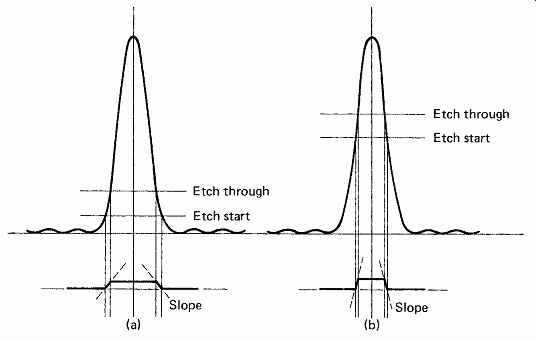
FIG. 31 The two levels of exposure sensitivity of the resist determine
the size and edge slope of the bumps in the CD. (a) Large exposure results
in large bump with gentle slope; (b) less exposure results in smaller bump
with steeper sloped sides.
In summary, the resist thickness controls the depth of the pits, the cutter
laser wavelength and the NA of the objective together control the width of
the pits in the radial direction, and the laser intensity and sensitivity of
the resist together with the development time control the slope. The length
of the pits in the tangential direction, i.e. along the track, is controlled
by the speed of the disk past the objective and the length of time for which
the modulator allows light to pass. The space between the pits along the track
is controlled by the speed of the disk past the objective and the length of
time for which the modulator blocks the laser light. In practice all these
values are constant for a given cutting process except for the times for which
the modulator turns on or off. As a result pits of constant depth and cross-section
are formed, and only their length and the space between them along the track
is changed in order to carry information.
The specified wavelength of 780 nm and the numerical aperture of 0.45 used
for playback results in an Airy function where the half-power level is at a
diameter of about 1m. The first dark ring will be at about 1.9 m diameter.
As the illumination follows an intensity function, it is really meaningless
to talk about spot size unless the relative power level is specified. The analogy
is quoting frequency response without dB limits.
Allowable crosstalk between tracks then determines the track pitch. The first
ring outside the central disk carries some 7 percent of the total power, and
limits crosstalk performance. The track spacing is such that with a slightly
defocused beam and a slight tracking error, crosstalk due to adjacent tracks
is acceptable. Since aberrations in the objective will increase the spot size
and crosstalk, the CD specification requires the lens to be within the Marechal
criterion. Clearly the numerical aperture of the lens, the wavelength of the
laser, the refractive index and thickness of the disk and the height and size
of the bumps must all be simultaneously specified.
The master recording process has produced a phase structure in relatively
delicate resist, and this cannot be used for molding directly.
Instead a thin metallic silver layer is sprayed onto the resist to render
it electrically conductive so that electroplating can be used to make robust
copies of the relief structure. This conductive layer then makes the resist
optically reflective and it is possible to 'play' the resist master for testing
purposes. However, it cannot be played by the cutter, as the beam in the cutter
is too small and it would not straddle the pits. The necessary phase contrast
between light energy leaving the lands and pits would not then be achieved.
Unfortunately the resist master cannot be played by a normal CD pickup either,
because the pits in the resist are full of air, in which the velocity (and
therefore the wavelength) of light is different from the value it will have
in the finished disk when the pits are filled with plastic. Thus the correct
pit depth for a plastic disk is incorrect in air; a third type of optical system
is needed to test play a resist master in which the wavelength is shorter than
the wavelength used in the normal player. This would produce an Airy pattern
which was too small with a conventional lens aperture, and so a lens of smaller
aperture is needed to produce a spot of the correct diameter from the 'wrong'
wavelength.
The electrically conductive resist master is then used as the cathode of an
electroplating process where a first layer of metal is laid down over the resist,
conforming in every detail to the relief structure thereon. This metal layer
can then be separated from the glass and the resist is dissolved away and the
silver is recovered leaving a laterally inverted phase structure on the surface
of the metal, in which the pits in the photoresist have become bumps in the
metal. From this point on, the production of CD is virtually identical to the
replication process used for vinyl disks, save only that a good deal more precision
and cleanliness is needed.
This first metal layer could itself be used to mold disks, or it could be
used as a robust submaster from which many stampers could be made by pairs
of plating steps. The first metal phase structure can itself be used as a cathode
in a further electroplating process in which a second metal layer is formed
having a mirror image of the first. A third such plating step results in a
stamper. The decision to use the master or substampers will be based on the
number of disks and the production rate required.
The master is placed in a molding machine, opposite a flat plate. A suitable
quantity of molten plastic is injected between, and the plate and the master
are forced together. The flat plate renders one side of the disk smooth, and
the bumps in the metal stamper produce pits in the other surface of the disk.
The surface containing the pits is next metallized, with any good electrically
conductive material, typically aluminum. This metallization is then covered
with a lacquer for protection. In the case of CD, the label is printed on the
lacquer. In the case of a prerecorded MiniDisc, the ferrous hub needs to be
applied prior to fitting the cartridge around the disk.
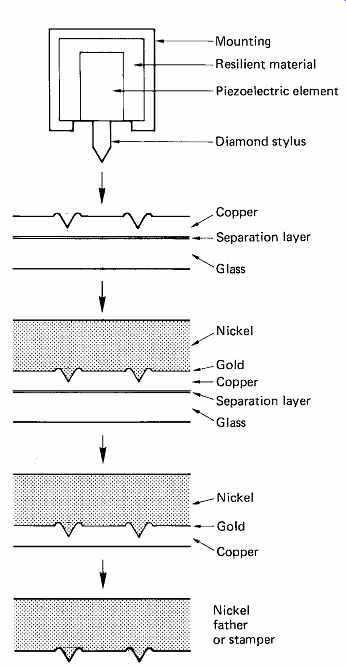
FIG. 32 In direct metal mastering, a piezoelectric element embosses a
copper layer, which is plated over with nickel and subsequently etched away
to make a father, or for direct use as a stamper for short runs.
11. Direct metal mastering
An alternative method of CD duplication has been developed by Teldec. [17]
As FIG. 32 shows, the recording process is performed by a diamond stylus
which embosses the pit structure into a thin layer of copper. The stylus is
driven by a piezoelectric element using motional feedback. The element is supported
in an elastic medium so that its own center of gravity tends to remain stationary.
Application of drive voltage makes the element contract, lifting the stylus
completely off the copper between pits.
Since the channel code of CD is DC-free, the stylus spends exactly half its
time in contact with the copper, and therefore the embossing force is exactly
twice the static force applied. The pits produced are vee-shaped, rather than
the flat-bottomed type produced by the photoresist method, but this is not
of much consequence, since the diffraction-limited optics of the player cannot
determine any more about the pit than its presence or absence. It is claimed
that this form of pit is easier to mold.
A glass master disk is prepared as before, and following a thin separation
layer, a coating of copper about 300 nm thick is sputtered on.
The recording is made on this copper layer, which is then gold-coated, and
nickel-plated to about 0.25mm thick. The resultant metal sandwich can then
be peeled off the glass master, which can be re-used. The recording is completely
buried in the sandwich, and can be stored or transported in this form.
In order to make a stamper, the copper is etched away with ferric chloride
to reveal the gold-coated nickel. This can then be used as an electroplating
father, as before. For short production runs, the nickel layer can be used
as a stamper directly, but it is recommended that the gold layer be replaced
by rhodium for this application.
12. MiniDisc read/write in detail
MiniDisc has to operate under a number of constraints which largely determine
how the read/write pickup operates. A prerecorded MiniDisc has exactly the
same track dimensions as CD so that it can be mastered on similar equipment.
When playing a prerecorded disk, the MiniDisc player pickup has to act in the
same way as a CD pickup. This determines the laser wavelength, the NA of the
objective and the effective spot diameter on the disk. This spot diameter must
also be used when the pickup is operating with an MO disk.
FIG. 33(a) shows to scale a CD track being played by a standard pickup.
The readout spot straddles the track so that two antiphase components of reflected
light can be obtained. As was explained in section 12.10, the CD mastering
cutter must use a shorter wavelength and larger NA than the subsequent player
in order to 'cut' the small pits in the resist. FIG. 33(b) shows that
the cutting process convolves the laser enabling pulse with the spot profile
so that the pit is actually longer than the pulse duration by a spot diameter.
The effect is relatively small in CD because of the small spot used in the
cutter.
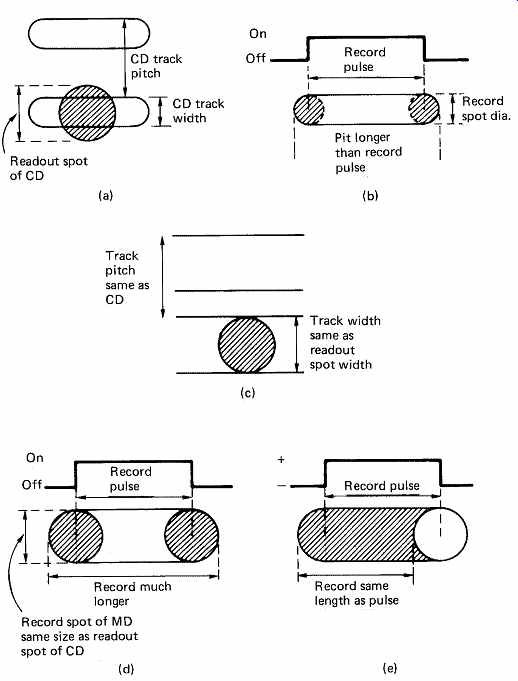
FIG. 33 (a) A CD track and readout spot to scale. (b) The CD track is
cut by a smaller spot, but the process results in pits which are longer than
the pulse duration. (c) An MO track and readout spot to scale. If this spot
is pulsed for writing, the magnetized areas are much larger than the pulse period
and density is compromised as in (d). If, however, the magnetic field is modulated,
as in (e), the recording is made at the trailing edge of the spot and short wavelengths
can be used.
When using an MO disk, the tracks recorded will be equal in width to the spot
diameter and so will be wider than CD tracks as FIG. 33(c) shows. MO writing
can be performed in two ways. The conventional method used in computer disks
is to apply a steady current to the coil and to modulate the laser. This is
because the coil has to be some distance from the magnetic layer of the disk
and must be quite large. The inductance of the coil is too great to allow it
to be driven at the data frequency in computer applications.
FIG. 33(d) shows what would happen if MD used laser modulation. The spot
profile is convolved with the modulation pulse as for a CD cutter, but the
spot is the same size as a replay spot. As a result the magnetized area is
considerably longer than the modulation pulse. The shortest wavelengths of
a recording could not be reproduced by this system, and it would be necessary
to increase the track speed, reducing the playing time.
The data rate of MiniDisc is considerably lower than is the case for computer
disks, and it is possible to use magnetic field modulation instead of laser
modulation. The laser is then on continuously, and the spot profile is no longer
convolved with the modulation. The recording is actually made at the instant
the magnetic layer cools below the Curie temperature of about 180°C just after
the spot has passed. The state of the magnetic field at this instant is preserved
on the disk. FIG. 33(e) shows that the recorded wavelength can be much
shorter because the recording is effectively made by the trailing edge of the
spot. This makes the ends of the recorded flux patterns somewhat crescent-shaped.
Thus a spot the same size as a CD readout spot can be made to record flux patterns
as short as the pits made by the smaller spot of a cutter. The recordable MiniDisc
can thus have the same playing time as a prerecorded disk. The optical pickup
is simplified because no laser modulator is needed.
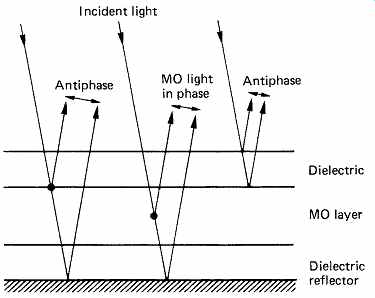
FIG. 34 In MO disks the dielectric and reflective layers are as important
as the magneto-optic layer itself.
The magnetic layer of MO disks should show a large Kerr rotation angle in
order to give an acceptable SNR on replay. A high Curie temperature requires
a high recording power, but allows greater readout power to be used without
fear of demagnetization. This increases the readout signal with respect to
the photodiode noise. As a result the Curie temperature is a compromise. Magnetic
layers with practical Curie temperatures are made from proprietary alloys of
iron, cobalt, platinum, terbium, gadolinium and various other rare earths.
These are all highly susceptible to corrosion in air and are also incompatible
with the plastics used for molded substrates. The magnetic layer must be protected
by sandwiching it between layers of material which require to be impervious
to corrosive ions but which must be optically transmissive. Thus only dielectrics
such as silicon dioxide or aluminum nitride can be used.
The disk pickup is concerned with analyzing light which has returned from
within the MO layer as only this will have the Kerr rotation.
Reflection from the interface between the MO layer and the dielectric overlayer
will have no Kerr rotation. The optical characteristics of the dielectric layers
can be used to enhance readout by reducing the latter reflection. FIG. 34
shows that the MO disks have an optically reflective layer behind the sandwiched
MO layer. The thickness of the dielectric between the MO layer and the reflector
is selected such that light from the reflector is antiphase with light from
the overlayer/MO layer interface and instead of being reflected back to the
pickup is absorbed in the MO layer. Conversely, light originating in the MO
layer and leaving in the direction of the pickup experiences constructive interference
with reflected components of that light. These components which contain Kerr
rotation are readily able to exit the disk. These measures enhance the ratio
of the magneto-optic component to ordinary light at the pickup.
>>
|