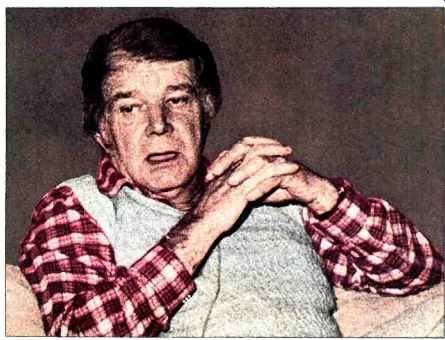
Most of us are familiar with the founding fathers of high fidelity. Pioneers
like Avery Fisher, Rudy Bozak, Frank McIntosh, H.H. Scott, Walter Stanton and
others, whose dedication to the quest for high-quality sound reproduction resulted
in their manufacturing the first hi-fi audio components for the consumer market.
Needless to say, this fledgling activity in the consumer hi-fi market was
complemented by parallel developments in the fields of professional audio and
re cording. There were pioneers in both these fields as well, but within the
relatively circumscribed world of profession al audio, few people achieved
high visibility and their accomplishments have largely gone unrecognized.
One of the most gifted of those early pioneers in professional audio is Milton
T. (Bill) Putnam, currently Chairman of the Board of United Recording Corp.
in Hollywood, California. URC encompasses United/Western Studios, Coast Recorders,
Teletronix, and its manufacturing arm UREI (United Recording Electronics Industries).
Bill Putnam founded Universal Recorders and built his own studios in Chicago
in 1946. It must be remembered that in those days, most recording studios were
constructed with only rudimentary knowledge and little application of acoustic
treatment. Typical studios of 15,000 to 35,000 cubic feet used draping and
perforated acoustic panels, quite often applied directly to boundary surfaces
with no provision for air space be hind them. Some used rock-wool batts behind
perforated Celotex. For the most part, there was inadequate low-frequency absorption
with the ratio of indirect-to-direct sound in the low-frequency instruments
causing a distinct lack of separation and presence and an unpleasant coloration
of the sound. Add to this the fact that the off-axis response of many micro
phones (even bidirectional or cardioid types) caused time-related and spectral
colorations of a signal arriving after the direct sound. Of course, at the
low frequencies below 125 Hz, all the directional mikes became virtually omni-directional,
further contributing to the muddiness of the sound.
In marked contrast to this common studio environment, Bill Putnam's studio
at Universal Recorders was constructed with the specific goal of increasing
instrumental separation, and he accomplished this by lowering the overall reverberation
time, with particular attention to substantial absorption of the low frequencies.
To this end, diaphragmatic panels in convex splays were used, and the thickness
of rock-wool batts behind perforated panels was increased by fur ring out frames
for greater depth. Separation screens and rugs were used for absorption of
higher frequency reflections.
An early type of absorptive roll-around isolation vocal booth was used, which
also was occasionally used for a drum set--a fore runner of today's drum cage.
A roll-around band shell was constructed with interior poly-cylindrical diffusers
to pre vent focusing, especially of strings. Instrumental positioning and mike
placement in the studio were radically altered from the hand-me-down practices
of early broadcasting and recording, with a view towards more separation and
definition. (Remember, this was before the days of multi-track and overdubbing.)
Having achieved better instrumental separation by lowering studio reverb time,
Bill did not want a dead or dry overall sound, so he experimented with feeding
his output signal to various types of reverberation rooms. (Note that this
was before electronic echo chambers.) Bill was looking for a reverberation
room which had a smooth decay, would eliminate periodicity, and have low coloration.
Bill experimented with delaying the signal sent to the reverb room to more
effectively simulate early sound. He realized the importance of the control
room in his studio, and it was acoustically treated. This led to measuring
monitor-speaker response in the room and even some attempts at room/speaker
equalization.
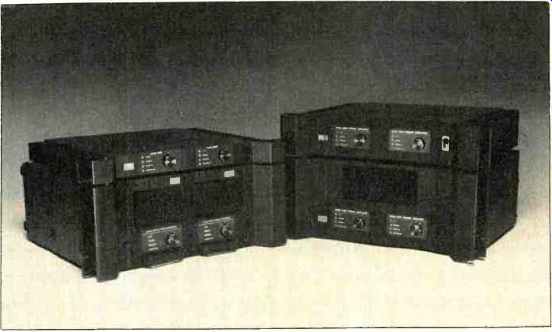
Above: UREI's power amplifiers, Models 6150, 6500, 6250 and 6400.
Because of all the factors in studio design and recording practices Bill
had incorporated into his Universal Recorders studios, he developed a distinctive
and easily recognized high-quality sound which generated considerable business.
In the early and mid-fifties, the advent of exotic high-quality condenser
microphones such as the Telefunken U-47, along with greatly improved mono
feed back cutterheads such as the Westrex 2B and Grampian, resulted in rapid
advances in the quality of recordings. Bill Putnam adopted these and other
aids to high-quality mastering, and in competition with several other studios,
the "Hi-Fi Spectacular" record was a new specialty product for what
was called the audiophile market! Imagine that, way back in 1955! As tape recorders
and tape formulations improved, permitting greatly extended high-frequency
response, the battle to produce even more spectacular hi-fi records intensified.
In 1955, Bill managed some neat technical one-upmanship by recording at 30
inches per second and mastering the tapes at half speed. Shades of Mobile Fidelity
back then! I had the pleasure of meeting Bill Putnam in 1951 in Chicago, where
I was in technical sales and served as music di rector for Magnecord, one of
the pioneer manufacturers of tape recorders. This is where stereophonic sound
enters the picture. I had been recording in stereo for some time, and Bill
had been experimenting with stereo too. The Magnecord stereo recorder used
a staggered head configuration which gave adequate stereo separation but also
caused certain problems. Bill recorded some stereo in this format. Ever the
innovator, in 1954, in cooperation with the Pentron Corp. of Chicago, he used
a recorder with eight channels on standard quarter-inch tape in a staggered
head configuration to record an instrumental group. In the eight-channel playback,
eight loud speakers were arrayed in the listening room in the same positions
in which the instruments had originally been recorded.
Portents of a future as yet unrealized. In 1958, Bill Putnam moved to Hollywood,
California, formed United Recorders and constructed the first purpose built
studio for stereophonic recording.
The studio was an amalgam of Bill's original ideas, with important new acoustic
design work by Michael Rettinger. In later revisions, the Time Delay Spectrometry
(TDS) measurement system of Audio's own Richard Heyser was extensively employed,
as were some of Don Davis' pioneering ideas on room equalization. John Eargle
contributed new data on monitor speaker response in acoustically treated control
rooms. Bill Putnam and Ed Long (a frequent contributor to Audio) collaborated
on a joint R&D pro gram to upgrade the quality of monitor speakers. The
result was a speaker which was designated a "Time Aligned" studio
monitor. The technique takes into consideration the time (phase) response of
the speaker, and by proprietary de sign of the crossover network and the placement
of the loudspeaker driver elements, the system is said to be "Time Aligned" and
free of group time-delay anomalies. In essence, there is near-perfect alignment
of the frequency components in a complex transient waveform'.
Bill Putnam had formed a company -- United Recording Electronics Indus tries,
UREI--to manufacture specialized equipment for the professional re cording
market, and the new "Time Aligned" studio monitor was to be built
at this facility. UREI has been in existence for some years now and is one
of the most successful of Bill's companies.
I have used a number of UREI's more exotic products, and when I was invited
to visit their new plant, I gladly accepted.
The UREI plant is a modern one-story building in Sun Valley, one of those
pleasant little towns in the San Fernando Valley, and just a short drive to
the United Recording studios in Hollywood.
DeWitt "Bud" Morris, President of UREI, is an old friend. He's an
easygoing and genial man, but nonetheless runs a tight ship at UREI, aided
by Brad Plunkett, Chief Engineer, and Ray Combs, V.P.
Work flow is very well organized, beginning with in-house testing of incoming
parts, then sub-assembly build-up and unit fabrication on various dedicated
technology assembly lines. While vendors supply many parts, whenever possible
and economically feasible, UREI makes their own. For example, most transformers
and certain coils are made on the premises. UREI is subject to the same inordinately
long delivery times on parts as most companies these days, but they invest
heavily in quantity buying and as a consequence are usually in a strong inventory
position. Thus, most of the equipment they make is readily available from stock.
In addition to a well-equipped R&D lab, a modern test lab monitors quality-control
procedures. Fortunately, subjective testing of many UREI products is given
high priority and is carried out in a purpose-built, acoustically treated listening
room. Currently UREI is producing a new generation of "Time Aligned" monitor
speakers, the 811 A (single 15-in. woofer with exponential HF horn), the 813A
(same as 811 A with addition of another 15-in. woofer in a large enclosure),
and 815A (same as 811 A with two 15-in. woofers in a still larger enclosure).
The HF horns are newly designed for improved frequency response and dispersion
characteristics. The "Time Aligned" crossover network has been redesigned
for more power transfer to the speaker driver.
UREI is now heavily committed to amplifier production. Their big brute, Model
6500, was introduced at the May, 1980 AES Convention, and I described it in
the August, 1980 issue of Audio. At the November, 1980 New York AES, the 6500
was joined by the 255 W/channel Model 6400, the 150 W/channel Model 6250, and
a slim-line design, only 1 3/4-in. high, the Model 6150 with 76 W/channel.
All of these units are 19-in. rack-mountable and are of highly rugged construction.
UREI continues to produce such specialized items for professional recording
as limiters and compressors and various types of equalizers and filters. A
new electronic crossover is currently in the works, and UREI still makes their
invaluable Model 200 XY plotter and recorder with the Model 2000 frequency
response module, the Model 2010 level and frequency detector module, and the
new Model 21 warble generator for room measurements. When I was visiting the
UREI plant, a huge new Neve mixing console with the Necam automated mix-down
feature was undergoing tests prior to installation in Bill's studio at United
Recorders.
Over the years, Bill Putnam has al ways tried to stay just a bit ahead of
cur rent recording technology. His early experiments with time delay and subsequent
manufacture of the Cooper Time Cube is an example, as was his issuing of four-channel
matrix evaluation test records. Bill's quadraphonic recordings of the late
Stan Kenton and his orchestra are among the very best ever done in this medium.
Today Bill Putnam continues in his pursuit of recording excellence, and his
UREI company translates many of his ideas into products that find favor in
professional audio.
-----------
(Source: Audio magazine, Mar. 1981;
Bert Whyte
)
= = = =
|