To play a record, the turntable or device to rotate the disc at the required
speed is needed. This is the basic requirement for all turntables. The construction
and execution of the requirement may differ greatly between the models and
the designs of different manufacturers.
The history of evolution of the record drive mechanisms takes us from the
days of hand-cranked cylinder machines, through the age of spring-wound phono
graphs with mechanical governors for speed control, and into the age of electrically
driven machines with electronic control. Today the accuracy of turntable speed
is measured in small fractions of 1% in deviation from the desired speed.
1 Drive Systems
Turntables are driven by electric motors. The method by which the power from
the motor is transferred to the turntable platter classifies the drive mechanism.
The turntable platters can be belt driven, puck or idler driven, and driven
direct.
The first category, the belt-driven type, encompasses all models that have
motors mounted to the side of the platter with the belt stretched over the
motor pulley and outer rim of the platter, FIG. 4A. Some platter designs have
an additional internal rim to hide and to protect the belt.
Many turntables have synchronous motors or motors with some type of speed
control mechanism, such as a centrifugal switch that disconnects the power
to the motor when the speed exceeds the preset value. The later types of motors
are usually low-voltage, battery-driven motors used in portable equipment.
Also, in portable turntables there is electrical feedback to control the speed
of the low-voltage motor.
Another version of the same idea uses a low-voltage ac motor driven by a self-contained
crystal-controlled oscillator allowing variation of the speed of the platter
and achievement of great speed precision. The only source of speed variation
can come from belt slippage or a defective belt. Belt-driven turntables are
normally the quietest turntables. The speed selection of the belt-driven turntable
can be accomplished either by changing the speed of the motor or by having
the stepped pulley on the motor and by shifting the belt from one pulley onto
another.
The second type of turntable is a puck-driven or idler-driven turntable, FIG.
4B. The coupling between the platter and the motor shaft is achieved through
the intermediate idler wheel or puck, which has the outer edge covered with
neoprene rubber or polyurethane for positive drive and to isolate the motor
vibration from the platter. The idler wheel rotates on the shaft that is attached
to a sliding bracket. When one side of the idler pulley (or puck) is in contact
with the inner side of the rim of the platter and on the other side with the
motor shaft, the idler wheel will transmit the motor rotation to the turntable
platter. The mechanism is designed so when the motor is turned off the idler
wheel retracts away from the motor shaft to protect the rubber ridge from forming
a flat spot.
The advantage of the rim drive is that it provides positive torque to the
platter, and if the motor is strong enough, it can bring the turntable to the
desired speed almost instantly. The mechanism is simple, and it is the most
reliable type of drive. Unfortunately it is also the noisiest because of the
positive coupling between the motor and the platter idler or puck that transmits
a certain amount of the motor vibrations to the platter and consequently to
the record, as shown in FIG. 4C.
The third kind of turntable drive is the direct drive where the motor drives
the shaft of the platter directly.
There are also variations of the design. Some turntable designs are very sophisticated,
using the platter itself as a rotor of the motor and drive is provided by the
self-contained, quartz-controlled oscillator. The motion is extremely accurate
and the speed of rotation may be displayed on the digital display, which is
part of the control panel. There is also a weak point in this seemingly perfect
drive. Because of the slow speed at which the turntable rotates, and because
the motor has a finite number of poles, there is a slight cogging action in
the platter motion, which may manifest itself with increased loads. This handicap
is only related to turntable platters with fairly small mass and small moments
of inertia. If the platter is heavy, it will overcome this problem.
The performance of the turntable depends very little on the type of drive
used but more on the correct execution of the design by understanding the problems
involved. The ideal turntable should have the following properties:
• It will start fast without hesitation.
• It will rotate with exact speed without variations.
• There will be no motor noises or vibrations heard while the system is in
operation, they will not be transmitted to the platter.
• The turntable should be adequately shock mounted and isolated from the surface
on which it sits to prevent the transmission of rumble and vibrations from
the room. These loud sounds can actually shake the platter and the tonearm.
• The platter should be treated against ringing either by using a turntable
mat with damping properties or by undercoating the platter.
• The turntable must be easy to maintain and to repair.
Not many turntables meet all these criteria; there fore, in order to know
how to evaluate the unit, it is important to know how they work.
======
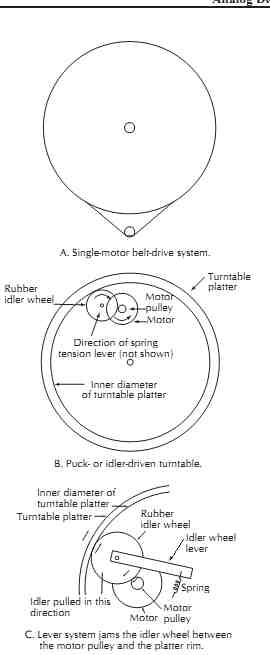
FIG. 4. Various types of drive mechanisms. A. Single-motor belt-drive system.
B. Puck- or idler-driven turntable. C. Lever system jams the idler wheel between
the motor pulley and the platter rim.
COMPONENTS include: Motor; Motor pulley; Turntable platter; Inner diameter
of turntable platter; Rubber idler wheel; Spring; Idler wheel lever; Rubber
idler wheel; Turntable platter; Motor pulley; Motor; Direction of spring
tension lever (not shown); Inner diameter of turntable platter; Idler pulled
in this direction
=======
Speed of Rotation. Before evaluating the entire system, there are tests that
can be performed on the turntable alone. The first one is speed of rotation.
There are many ways of checking the speed of rotation, but the simplest one
is by using the stroboscopic disc.
A stroboscopic disc is a circular disc containing a number of black-and-white
bars, which are used for checking the speed of turntables and other rotating
machines, Fig. 5. The disc is placed on the turntable, and the bars are observed
under a fluorescent or neon light source fed from the normal ac lighting circuits.
When the speed of the turntable is correct, the black bars appear to stand
still. If the table is turning too fast, the bars speed up and drift in the
direction of rotation.
When running slow, the reverse takes place. Stroboscopic bars may be painted
around the rim of a turntable and illuminated by a 115 Vac neon light mounted
close to the table edge for constant observation. The equation for calculating
the number of bars on a 60 Hz stroboscopic disc is:
bars = 2f60/ rpm
where, f is the frequency of the strobe light used to observe the bars,
rpm is the speed of the turntable in revolutions per minute.
Starting Time. Starting time is the time it takes for the
platter to reach its operating speed from a complete stop. This time period
is important to know for professionals who have to begin playing the song or
selection at the exact moment. To check the starting time requires either a
stop watch or timing device and a strobe disc or the test record. As soon as
the lines on the strobe disc appear stationary, the turntable has reached its
operating speed. In playing the record test tone, the pitch changes as the
correct speed is attained. Starting time may vary anywhere from a fraction
of a second to two or more seconds, depending on the construction of the turntable.
Turntables used by disc jockeys have to start as fast as possible without
overshoot, which means that the speed should not, even for a moment, exceed
the desired speed. If this overshoot occurs as the program material is already
being transmitted, the variations of the speed will be most objectionable.
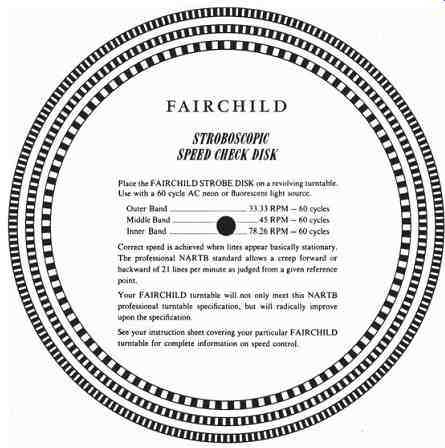
FIG. 5. A stroboscopic disc used for checking the rotational speed of a turntable.
Fairchild Recording Equipment Corp.
Acoustical Noise. The third test concerns the acoustical
noise the motor and the turntable are producing.
Normally, this test can be easily performed in a quiet listening room when
everything is turned off and only the turntable is energized. If the turntable
noise is clearly heard and it overshadows the normal room noise, turntable
drive is below an acceptable performance level. A second part of the same test
is conducted when the turntable is turned off and the system is adjusted to
a normal listening level. When the record with the quiet groove is placed on
the turntable, a slight hiss can be heard when putting your ear to the loud
speakers. When the record with the quiet groove is placed on the turntable
and the stylus is placed into the groove, listening to the increase in noise
will show the extent to which the turntable transmits the building rumble.
If the power to the turntable is turned on, the noise contributed by the motor
drive can be measured.
During this test, slightly tapping the base of the turn table can determine
if the shock mounting is adequate and whether or not loud music will add coloration
to the signal being reproduced. In summary, what is required from the good
turntable is that it reproduces only what is recorded on the disc and is insensitive
to all other sources of vibration.
2 Turntable Design in the 21st Century
One of the most important features of turntable design is the ability to keep
noise and rumble created by motors and bearings from being picked up by the
cartridge stylus. Many inexpensive turntables have a direct drive between the
motor and the platter and inexpensive bearings, allowing motor noise and vibration
to be transmitted to the platter and then to the cartridge stylus.
Remember, it doesn't make any difference to the signal whether it comes from
the stylus moving versus the disc or the disc moving versus the stylus.
VPI turntables, FIG. 6 use inverted bearings instead of conventional bearings.
In this design the bearing assembly is in the platter rather than in a bearing
well below the platter. The spindle and ball are attached to the chassis and
the bearing well is inverted and placed in the platter itself. With this design
the drive belt pulls through the center of the bearing assembly rather than
many inches away from the center of the assembly, reducing teeter-totter effects
to near zero for better stability.
All motor assemblies are completely separated from the turntable platter and
tonearm, so there is no mechanical connection between the motor and the chassis
except through the belt. This gives much lower noise levels due to isolation
from the source of noise.
The VPI HR-X turntable uses a dual motor flywheel assembly to drive the platter.
Two synchronous motors, driven by a perfect sine-wave ac power supply, drive
a 14 lb flywheel spinning at 300 rpm, which in turn drives the platter. In
this configuration the platter is driven by a non-electromotive source as opposed
to other tables that are driven by the motor or combination of motors.
Running the platter with no motor or multiple motors produces a velvety black
background and perfect speed stability.
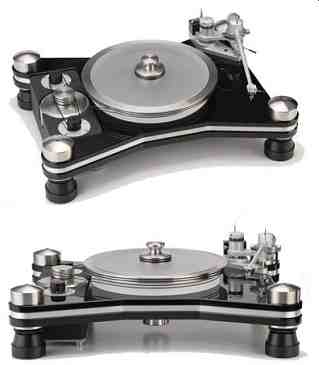
FIG. 6. High-quality noiseless turntable. VPI Industries, Inc.
|