<<Prev.
3. Magnetic Heads
Although magnetic tape is covered in a later section, the following discussion
of magnetic heads requires a few very simple assumptions regarding the composition
and dimensions of the magnetic tape. First, assume that the magnetic coating
consists of microscopic particles of magnetic materials that have been bonded
to one surface of a thin plastic backing or substrate. Second, each magnetic
particle is assumed to function as a small independent magnet, allowing patterns
of varying magnetic polarity and intensity to be stored along the tape. Last,
the thickness of the magnetic coating for the audio tape example will be assumed
to be 0.6 mil (15 µm).
3.1 Geometric Characteristics
Most of the characteristics of magnetic heads are controlled by the geometry
of the head and the magnetic tape. Since wavelength on tape is determined
by the recorded frequency in hertz and the relative tape-to-head speed, there
can be many combinations of frequency and speed that will result in the same
effects in a head. For example, the wavelength of a 15 kHz tone on a mastering
recorder at 15 in/s will have the same wavelength as a 240 kHz signal on a
high-speed tape duplicator running at 240 in/s. The geometric considerations
for both applications are identical, despite the 16:1 difference in tape speed.
Not all of the characteristics are geometric, however. Eddy current losses,
for example, depend on the frequency in Hz rather than the wavelength.
3.1.1 Gap Length Loss
Each of the tiny magnetic particles on the surface of the tape produces a
magnetic force or flux in the space surrounding the particle. This invisible
magnetic effect, called a magnetic field, will interact with other nearby
magnetic particles. To measure the strength of this field, a flux concentrator
in the form of a reproduce head is scanned along the tape. The resulting electrical
output from the head is dependent on the flux pattern recorded on the tape.
The reproduce head must be able to collect flux selectively from a very small
span of tape. For example, flux patterns on a compact cassette may be as small
as 100 millionths of an inch (100 × 10^-6 in or 2.5 µm) in wavelength. To
achieve this fine resolution, a small gap must be created in a ring of magnetic
material, as shown in FIG. 14A.
The length of the gap ranges from two ten-thousandths of an inch (2 × 10^-4
inch or 5 µm) for studio mastering recorders down to less than 30 millionths
of an inch (30 × 10^-6 inch or 0.75 µm)-the wavelength of red light for cassette
and high-density digital recorders.
Since no slicing technique is available to cut accurate gaps that short,
the core is usually fabricated as two pole pieces that are fastened together
with a shim spacer of the desired dimension inserted in the gap. FIG. 14B
shows a typical studio head core drawn full size, with the critical gap area
at the pole tips and adjacent tape magnified in FIG. 14C.
The operation of the gap, which serves as a sensing aperture, can be analyzed
in terms of a flux pickup focused at the surface of the tape. The amount of
flux picked up by the core, and thus made available to generate an output
voltage in the winding, is determined by the net magnetic flux from pole tip
to pole tip across the gap area. If the tape segment at the gap consists of
a strong magnetization of only one polarity, the flux in the core will be
maximized. If, on the other hand, the segment contains two strong portions
of opposite polarity that cancel each other, the net flux in the core will
be zero.
-----------------
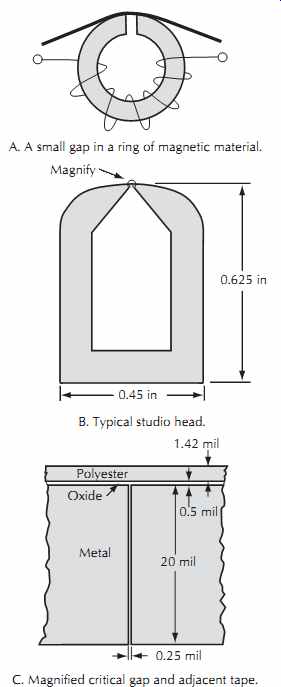 FIG. 14. Ideal and practical magnetic heads.
Metal Polyester Oxide
0.5 mil 1.42 mil 20 mil
0.25 mil Magnify
0.625 in
0.45 in C.
Magnified critical gap and adjacent tape.
A. A small gap in a ring of magnetic material.
B. Typical studio head.
----------------
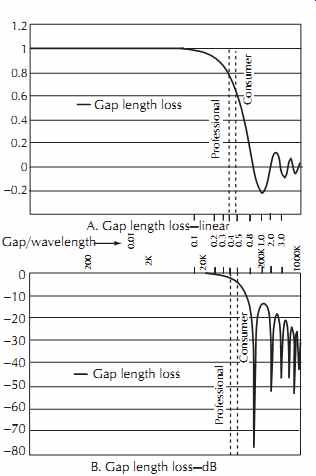 FIG. 15. Loss due to gap length and the ratio of gap length to wavelength.
--------------------
The efficiency of the gap due to this averaging effect is illustrated in
FIG. 15. The output of the head declines, slowly at first, and then quite
rapidly to zero as the wavelength decreases to the length of the gap. As the
gap length becomes longer than the wavelength, an output of opposite polarity
appears. When the wave length drops to half the gap length, another null will
occur. This pattern of diminishing peaks of alternating polarity is repeated
over and over, with nulls occurring at each wavelength that produces an odd
or even number of complete cycles in the gap.
The example recorder at 15 in/s has only 1 dB of gap length loss at 40 kHz
and 3 dB at 67 kHz, certainly not a dominating loss. At 30 in/s these losses
become even more insignificant, with the _1dB and _3 dB frequencies doubling
to 80 kHz and 134 kHz.
Audio recorders are seldom designed to operate beyond the dashed lines shown
in FIG. 15. With this constraint, gap length loss for professional machines
can be held below 1 dB or 2 dB by choosing an appropriate gap length for a
given application and minimum wavelength. Mastering recorders operating at
15 in/s and 30 in/s and broadcast machines operating at 7.5 in/s have playback
gaps ranging from 100-200 µinch, compact cassette machines operating at 1
in/s have gaps of 30-60 µinch.
Mastering recorders may also use the record head for playback in the sync
mode. Since the record heads may have gaps ranging from 250 µinch to 1000
µinch, the sync response may suffer significant high-end loss. For example,
a 1950s vintage recorder with a 1000 µinch record gap will reach its first
null at 15 kHz for a tape speed of 15 in/s. As sync response became more important
in the mid 1960s the recorder manufacturers tightened up the record gaps to
350 µinch or less to improve sync response.
If the gap length is inferred from the first measured null, this effective
gap length may be 10% to 15% longer than the mechanical gap determined by
the shim.
Various proposed explanations include magnetic degradation of the inner surfaces
of the pole tips due to manufacturing stresses and pole tip saturation. When
in doubt, add 10% to the optically measured length or shift the response points
down to 91% (1/1.1) of the theoretical values. For the ATR100 example, the
_1dB and _3 dB points would shift to 36 kHz and 61 kHz.
Use of an excessively short gap will cause an additional loss in overall
head sensitivity due to shunted flux that jumps the gap rather than traveling
through the core, as shown in FIG. 16. For this reason, the repro duce head
gap length is usually chosen to give the largest acceptable loss at the shortest
expected wave length.
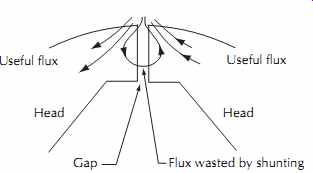 --------- FIG. 16. Gap shunting loss.
Useful flux Head Head Gap Flux wasted by shunting Useful flux
----------
3.2 Spacing Losses and Thickness
The recording process magnetically aligns groups of the tiny randomly oriented
magnetic particles so that they act as if they were a single larger particle.
We could visualize these groups as little bar magnets that have dimensions
determined by the tape and signal. The track width defines the vertical direction
and the tape coating thickness sets the depth. The length is determined by
the wavelength of the recorded signal. To simplify the example, assume that
a 1.5 kHz square wave is recorded at a tape speed of 15 in/s, yielding a wavelength
of 10 mils or 0.010 in. The recorded image is similar to a series of bar magnets
each 5 mils long with alternating polarity.
Actually, gap length loss and shunting loss are only a part of what determines
the performance of an audio recorder. The most critical parameter is the relative
thickness of the magnetic coating on the tape. The ratio of tape thickness
to the shortest wavelength to be recorded has a profound effect on the frequency
response, maximum output, noise, and signal-level fluctuations.
The magnetic particles at the surface of the tape are very tightly coupled
to the core of the head, producing a maximum amount of playback flux in the
core. Particles that are buried below the surface of the tape, however, produce
a weaker flux in the core. The amount of flux that is lost depends on the
spacing distance and the wavelength-just as a small font size is more difficult
to read at a distance than a larger font. An approximate expression for this
spacing loss is:
Spacing loss_dB = 55 x distance/wavelength
(eqn. 4)
One example of the use of this spacing loss formula is to determine the playback
signal loss due to a piece of dirt on the surface of a reproduce head. Assuming
a typical recording studio tape speed of 15 in/s (38 cm/s), a dirt speck only
0.0001 in (2.5 µm) high will produce losses at the following frequencies of
150 Hz spacing loss = 55 x 0.0001 / [15 / 150]
= 0.055 dB
1500 Hz spacing loss = 0.55 dB
15 kHz spacing loss = 5.5 dB
Note that this seemingly insignificant dirt particle has produced a serious
loss in high frequencies.
Spacing loss due to dirt is not the major problem created by the "nearsightedness" of
the gap since proper head cleaning will keep spacing distances to less than
10^-5 inch, which is (0.25 µm), producing virtually no error at studio tape
speeds. The problem is eight times more severe for cassette speeds of 1 in/s
(4.8 mm/s).
The major spacing problem arises within the tape itself since the magnetic
coating thickness spaces most of the particles away from the head with other
particles.
Consider the tape to be composed of several independent layers of oxide,
as shown in FIG. 17. The average spacing loss for each layer, calculated using
the midpoint of each layer to determine the spacing distance, is tabulated
for the example with a typical 0.6 mil (15 µm) coating thickness.
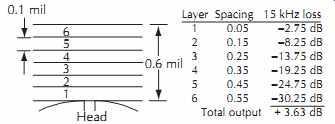 FIG. 17. Tape thickness loss.
The contributions of layers 2 through 6 fall off so rapidly due to spacing
loss that their combined contribution is only equal to layer 1 by itself at
this wavelength.
Indeed, shaving off layer 6, which constitutes 17% of the coating thickness,
would produce a loss of only 2% or 0.18 dB in output at this wavelength.
This coating thickness loss can be expressed as:
Coating thickness loss_dB = 20log x/1-e-x
(eqn. 5)
where,
x is 2 pi × thickness/wavelength.
Although this expression yields a drop of 6 dB per octave, as shown in FIG.
18, this curve is not the same shape as the response of a low-pass filter
made from a resistor and capacitor. The response in Fig. 18 is down 4 dB
at the intersection of the asymptotes rather than the typical 3 dB for a single
pole RC filter.
This difference in shapes means that a simple RC boost circuit will not properly
correct for the thickness loss.
Depending on the choice of RC boost frequencies, the difference in shape
will produce an error of 0.5-1.0 dB in the midband response.
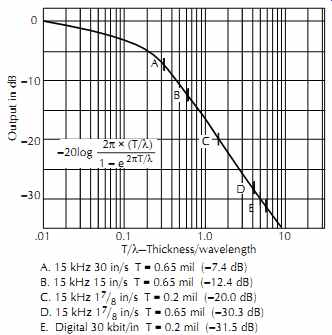
FIG. 18. Loss due to ratio of coating thickness to wavelength.
3.2.1 Equalization Boosts
This thickness loss of FIG. 22, must be corrected by applying compensating
boosts in either the record or reproduce circuitry. Although this loss is
a playback deficiency, the choice of whether to correct the loss during record
or playback is somewhat arbitrary. The amount of record boost is limited by
the magnetic saturation characteristics of the tape; playback boost is limited
by the high-frequency noise characteristics of the tape and the reproduce
head and associated circuitry.
The minimum amount of boosting required to achieve flat response can be considered
to be a necessary equalization. The industry has developed a set of internationally
recognized standards to promote compatibility of tapes. Each standard deals
with the necessary and discretionary equalizations to define the exact characteristics
of the recorded tape. Using the tape flux characteristics as a standard implicitly
specifies the partitioning of equalizations between the recording and reproducing
functions. Table 4 lists the commonly encountered standards.
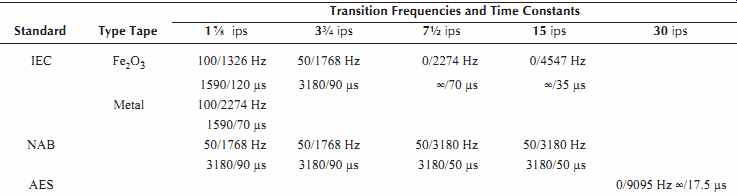 Table 4. Common Tape Record-Playback Equipment Equalization Standards.
Unlike the absolute nature of the reproduce characteristics, the record characteristics
of the recorder must have enough flexibility to accommodate a number of different
tape sensitivities and frequency characteristics.
Once the reproduce section has been calibrated to the standard with a standard
alignment tape, all further adjustments are to produce a recorded tape on
the machine that accurately matches the standard tape.
The amount of thickness loss can always be reduced by utilizing thinner coatings,
but any decrease in thickness also causes an equal drop in low- and mid-frequency
output and SNR. To preserve the existing standards, the tendency has been
to adjust the coating thickness of new tapes to emulate the high-frequency
losses of the older tape types while trying to achieve maximum low- frequency
output. This somewhat self-defeating strategy has been overcome in recent
thin-coat high-energy tapes that retain the low-frequency output capability
of older tapes, but utilize new equalization curves optimized for the new
tape thickness.
3.2.2 Fringing
Spacing loss is evident not only at high frequencies, but it also shows up
at very long wavelengths. Magnetic information that is recorded off to the
sides or fringes of the area normally scanned by the reproduce head core will
begin to be sensed if the wavelength becomes longer than the separation distance.
At studio operating speeds of 15 in/s and 30 in/s (38 cm/s and 76 cm/s), for
which low-frequency wavelengths reach ½ inch and 1 inch (12.7 mm and 25 mm),
this fringing leakage becomes very evident. For example, for the case of an
oversized record track mentioned in Section 2.4.1, the signal level may rise
by the ratio of the track width to the core width. A typical 24 track format
on 2 inch (51 mm) tape would encounter a 1.3 dB rise at frequencies below
500 Hz for record and reproduce cores of 43 mils and 37 mils (1.1 mm and 0.9
mm).
A similar case arises when alignment tapes made with a single full-width
record head are utilized for level and response checks. The sideways fringing
will produce significant level and response errors. The actual amounts of
error depend on both the track format and the playback head design. Some alignment
tape manufacturers roll off the low frequencies in an attempt to offset the
rise in a nominal head, but the amount of this fringing compensation is not
absolutely correct for all head designs.
One additional pitfall to be avoided is the fringing differences between
center tracks and edge tracks. Since the edge cores run very near the physical
edge of the tape, these cores sense only one-half the amount of fringing flux
sensed by the inner cores. During a frequency check from a full-width alignment
tape, the two edge tracks should therefore be slightly lower in output at
the low frequencies than the remainder of the tracks.
3.2.3 Contour Effect
At very low frequencies, the wavelength of the recorded signal may become
as long as the magnetic core of the playback head. These long wavelengths
enter the core at the gap and at the sides and rear of the core. The resulting
flux in the core will consist of the desired flux from the gap plus additions
and/or subtractions of the fringing flux leaking into the core at the sides
and back.
The voltage output of the head, which is dependent on the net flux coupled
into the windings, will undulate at low frequencies as the wavelengths create
varying levels of constructive and destructive interference due to the fringing
flux.
The response curve in FIG. 19 illustrates the nature of the undulations or
head bumps for a typical mastering recorder at 15 in/s (38 cm/s) and 30 in/s
(76 cm/s) using a reproduce head that has a 0.5 inch (12 mm) core face. Two
well-defined head bumps are usually evident for such mastering heads. The
bumps shift up an octave in frequency for each doubling of tape speed, creating
an even more severe problem at 30 in/s (76 cm/s).
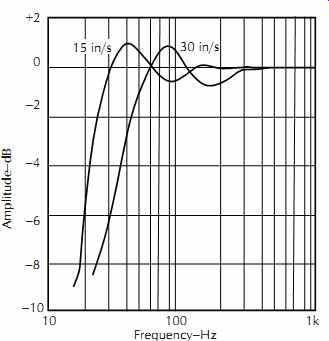 FIG. 19. Contour effect. Courtesy Sony Corporation of America.
Heads with either very small cores or only a small window in the head shielding
at the gap area can produce numerous ripples in the low-frequency response.
Such heads should be avoided unless the tape speed is slow enough to avoid
serious problems within the normal band of audio frequencies.
The exact shape of the head bumps is determined by the size and shape of
the reproduce core, surrounding shielding material, and angle of wrap of the
tape. Since the user cannot adjust these parameters during the normal alignment
procedure, the bumps can only be modified by adding an outboard equalizer,
which cancels the bumps with an inverse response curve.
Recent improvements in the control of head bumps has reduced the magnitude
of the bumps in present-day mastering recorders to less than 1 dB peak-to-peak
at 15 in/s (38 cm/s) and 1.5 dB peak-to-peak at 30 in/s (76 cm/s). Beware
that this level of error will be introduced each time the tape is rerecorded
during mixdown and subsequent protection copying. The total error can easily
reach 5 dB or more for a typical sequence of operations.
3.2.4 Crosstalk
Fringing also produces playback signal leakage or crosstalk between adjacent
tracks at long wavelengths.
The unused area or guard bands between the cores of the head, which are nearly
equal in width to the recorded track, usually provide enough of a physical
gap to prevent flux from spilling from one track to the next. At long wavelengths,
however, the fringing flux will jump the guard band, producing low-frequency
crosstalk.
The crosstalk component due to fringing will initially decrease as the frequency
is increased, but at midband the decrease will eventually bottom out. The
remaining residual level of crosstalk is not due to fringing, but it is a
direct transformer-like coupling of leakage flux between the adjacent cores
in either the record or repro duce head. A layer of magnetic shielding material
is typically placed between the cores of the head as a crosstalk shield to
reduce this flux leakage.
3.3 Frequency Characteristics
3.3.1 Inductive Rise
Up to this point, most of the losses and response anomalies have been governed
by the wavelength performance of the interface between the tape and the head.
An additional set of characteristics due to the internal frequency-dependent
operation of the head must also be considered.
The most striking characteristic in the frequency response of a conventional
coil-and-core playback head is a continuous 6 dB/octave rise in output voltage
with rising frequency. The core and winding of the head form an inductor in
which the output voltage is proportional to the rate of change of the flux
in the core as seen in the equation
head Vout = N Δ Φ / Δ t(eqn. 6)
where,
N is the number of turns in the
winding,
Δ Φ is the change in flux,
Δt is the time interval.
Any ratio of the form Δx/Δt is called a differential with respect to time,
and the device creating this rate of change is called a differentiator.
If a sine-wave signal of frequency f is used for testing the output voltage
of a head, the voltage expression can be further simplified to:
head Vout = 2 pi Nf
x fluxmax (eqn. 7)
3.3.2 Hysteresis Loss
The constantly changing magnetic flux in the core of the reproduce head gives
rise to losses within the core of the head. One source of these losses is
the amount of energy that is required to change the magnetization state of
the core material. Every time the flux in the core reverses polarity, a small
amount of energy is lost in overcoming the magnetic memory or hysteresis of
the core material. The hysteresis power loss increases with both increasing
flux magnitude and frequency.
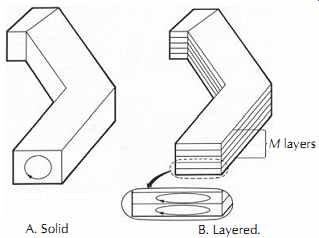 FIG. 20. Eddy current.
3.3.3 Eddy Current Loss
The changing core flux generates a voltage not only in the winding of the
head, but also within the core itself.
If the core is metallic, this voltage will cause a current to flow within
the core, as shown in FIG. 20. The core currents, referred to as eddy currents
because of their similarity to swirling eddies in a stream of water, dissipate
energy that should be going to the reproduce signal.
The amount of power (P) dissipated in the eddy currents is given by the general
power equation:
P = V2 / R (eqn. 8)
= I 2 R
The previous discussion on the inductive rise of voltage with increasing
frequency in the reproduce head also applies to these eddy components, producing
a rapid rise in eddy current power loss.
The eddy currents of the solid core of FIG. 20A rise to an unacceptable level
even before the upper limits of the audio band are reached. Fortunately, this
drastic loss can be decreased by dividing the core into many thin insulated
layers or laminations, as shown in FIG. 20B. For M laminations, each lamination
would generate only 1/M of the core voltage and 1/M2 of the loss power produced
by a solid core. The core resistance for each lamination drops only slightly
since the width of the lamination remains unchanged. The net improvement for
M laminations is a 1/M reduction in the eddy current power loss. (Professional
audio heads, which are typically constructed with laminations 2 mils (50 µm)
thick, will contain 20 to 120 laminations per track, depending on the track
width.) Reducing the core size and using high-resistivity core materials such
as ferrites can achieve even further improvements.
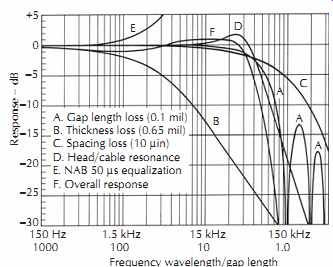 FIG. 21. Playback loss components at 15 in/s for 0.65 mil coating thickness.
3.4 Combined Characteristics
FIG. 21 illustrates some of the individual and composite effects of the
foregoing reproduce head characteristics. The constant 6 dB/octave inductive
rise of the head has been omitted in the illustration to accentuate the undesired
departures from flat response.
Curves A, B, and C illustrate the gap length, tape thickness, and spacing
losses, respectively.
Curve D represents a typical resonant rise due to head inductance and the
capacitance of the head cable and head winding. The playback amplifier high-frequency
response boost dictated by the National Association of Broadcasters (NAB)
equalization standard for 15 in/s (38 cm/s) is represented by curve E. The
combination of all of these effects in curve F yields a response that is flat
within ±1 dB. This simplified model does not include relatively minor contributions
at mastering speeds due to eddy currents and hysteresis, self-demagnetization
effects, recording equalization, and the effects of nonuniform distribution
of recorded flux due to coating thickness. In spite of these omissions, the
dominant nature of the coating thickness loss is readily apparent. The equalization
standards have been chosen primarily to offset this thickness loss.
The composite curve F represents the overall play back performance from an
ideal tape of finite thickness.
All the indicated response anomalies within the audio band must be either
corrected or tolerated. In some cases, one effect can be used to offset others,
such as shaping the resonance curve to compensate for the gap length loss.
(Unlike the resonance, the gap length loss increases with decreasing tape
speed, upsetting the compensation at lower tape speeds.)
3.5 Noise
The useful range of signal levels that pass through the tape recorder is
limited by the maximum signal at which all the magnetic tape particles become
completely magnetized or saturated and also by the amount of noise that remains
when the input signal is removed. Noise in tape recorders has many sources;
the electronics, the tape, and the heads themselves all contribute to the
residual noise.
The distortion content of the signal from a tape recorder rises so dramatically
near tape saturation that the normal operating range must be limited to less-than-maximum
levels. For the purpose of specifying and comparing tape recorders, the distortion-free
maximum operating level is typically considered to be the output signal level
at which the THD, which is dominated by third harmonic and other odd components,
reaches 3%. The ratio of the level for 3% THD at medium wavelength to the
residual noise is defined as the SNR of the recorder.
3.5.1 Track Width
The second factor is the loss in SNR in narrow-track consumer tape formats
due to the dissimilar ways that random noise sources and coherent signals
increase. The noise due to the tape, heads, and electronics is a random combination
of many small independent noise bursts. If two equal and independent random
noise sources of this type are added together, the noise power is doubled,
producing an increase of 3 dB on a voltmeter.
Coherent sources, on the other hand, are merely duplicates of the same waveform.
If two identical sources are added together, the value at each point on the
output waveform is exactly twice the value of either of the input waveforms.
In this case the output voltage is doubled, or a 6 dB increase.
Consider the case of two tracks of a tape recorder that have recorded the
same signal. If the output signals of the two tracks are added, the noise
will add randomly and the signals will add coherently. The combined tracks
have 6 dB more signal and 3 dB more noise, yielding a net SNR improvement
of 3 dB. Using a single track of double the original track width would produce
the same result if the noise sources were statistically independent in nature.
The tape noise will follow the 3 dB per doubling rate if the reproduce amplifier
noise is less than the tape noise. The reproduce amplifier noise typically
remains nearly constant regardless of track width of the head.
The apparent noise will vary, however, as the gain of the amplifier is adjusted
to compensate for changes in the head output due to increased or decreased
track width.
When tracks are made narrower, the amplifier noise that functions as a coherent
source will eventually dominate the tape noise, creating a signal-to-noise
loss of 6 dB per halving of tape width.
FIG. 26 compares the output voltage and signal-to-noise variation for various
track widths, assuming that all noise sources are truly random for a noiseless
preamplifier and a typical preamplifier. When the amplifier noise begins to
dominate the other noise sources, there is a rapid loss of SNR with decreasing
track width.
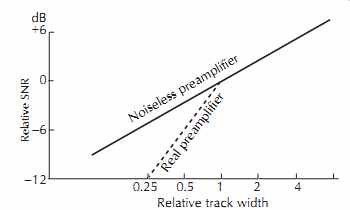 FIG. 22. Noise changes with track width.
3.5.2 Thermal Noise
Both the core and winding of the reproduce head contribute random noise to
the output signal. For the winding, the noise source is due to the thermal
agitation of the atoms in the copper wire. The amount of thermal noise is
given by the expression:
TN = √ 4KTRB (eqn. 9)
= 1.82 x 10-8 √ R volts for a 20 kHz
bandwidth at room temperature
where, TN is the thermal noise, K is the Boltzmann's constant (1.38 × 1023 joules/K), T is the absolute temperature in kelvin, R is the resistance in
ohms, B is the measurement bandwidth in hertz.
A 100-ohm resistor will produce 0.182 µV of noise voltage. Depending on the
core size and number of turns, a playback head may exhibit a resistance from
10-1000 ohm, yielding thermal noise contributions of 0.06-0.6 µV. The increase
in noise due to more turns of finer wire in high-inductance heads is offset
by a rise in head output voltage, producing little net change in SNR.
3.5.3 Barkhausen Noise
Another major noise source is Barkhausen noise, a noise due to jumps in the
magnetic boundaries of the core material. The core metal consists of a collection
of many microscopic magnetic zones or domains. When a magnetic field is applied
to the core, the boundaries or walls of the domains will change as small domains
merge to form larger domains. This merging occurs in discrete steps since
the small domains act as single units that must each merge completely in one
jump. The resulting step change in the magnetic field generates a noise burst
in the head winding. Since the core contains millions of constantly switching
domains, a statistically independent random noise is generated. Reducing the
size of the basic domains will decrease the amplitude of the Barkhausen noise.
3.5.4 Magnetostrictive Noise
The magnetic core material also exhibits magnetostriction-a change in magnetic
field due to stress. The microscopically rough surface of the magnetic tape
will therefore produce a small magnetic field change in the core as the tape
slides across the head. This field change generates a magnetostrictive noise
component in the winding.
Both the Barkhausen and magnetostrictive noises are absent when no tape is
moving over the surface of the head. The residual standby noise, which is
measured under these conditions, is the absolute noise floor for the reproduce
head and amplifier. The comparison of this standby noise level with the bulk-erased
and biased noise levels is covered in the test and maintenance section.
3.6 Record Heads
The magnetic core and gap of a reproduce head obey the principle of reciprocity,
which states that the roles of an excitation source and sensor can be interchanged.
For a head used in the reproduce mode, external flux at the gap produces
a voltage across the head winding. If, instead, a voltage is applied to the
head winding, a concentrated external flux field will be generated at the
gap and can be used to record a signal on a piece of moving tape.
The shape and strength of the magnetic field at the gap is the basis for
the operation of a recording head. The flux generated in the core by the current
in the winding must jump across the gap to complete a closed magnetic path.
The gap, which is a very poor magnetic path compared to the core, produces
an obstruction that forces the flux to spread sideways, as shown in FIG. 23.
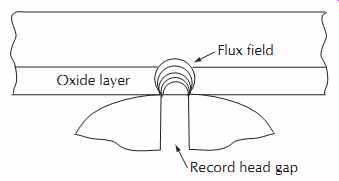
----- FIG. 23. Record head flux field
Flux field Oxide layer Record head gap
---------------
An analogous situation occurs with a crowd of people moving down a hallway.
If the hallway widens for a crossing corridor or small lobby, the crowd will
broaden out into the open area and then narrow down again to reenter the continuation
of the hallway. The broadening will increase if the pressure within the hallway
should increase due to an emergency such as a fire. The stress is greatest
at the transitions between the wide and narrow spaces since this is where
people are squeezing to try to change the shape of the flow.
A magnetic tape passing over a record head gap experiences a similar buildup
and decline in the magnetic recording field as it moves across the gap. To
produce a permanent recording on the tape, the flux must first rise to a level
sufficient to overcome the magnetic memory force of the tape, which normally
keeps the magnetic particles on the tape from changing state spontaneously.
In the central zone of complete excitation, the tape particles will follow
any change in the input signal driving the head. As the tape particles exit
the strong central zone, a well-defined point will be reached at which the
driving flux drops below the memory force, leaving a fixed magnetic image
impressed on the tape. This transition region in which the image freezes at
the trailing edge of the gap is called the trapping plane.
The shape of the trapping plane depends primarily on the gap size and the
thickness and magnetic characteristics of the tape. Since trapping planes
that are narrow and vertical will produce short-wavelength recordings that
are more easily reproduced, several techniques have been developed to sharpen
the transition zone, as shown in FIG. 24.
---------------
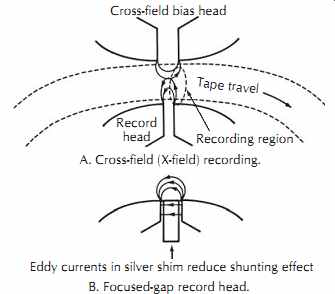 FIG. 24. Focused-gap and cross-field (X-field) head.
Cross-field bias head A. Cross-field (X-field) recording.
Tape travel Recording region Record head B. Focused-gap record head.
Eddy currents in silver shim reduce shunting effect
--------------
The focused-gap technique in FIG. 24B uses a highly conductive gap shim made
of silver to serve as a barrier to flux jumping straight across the gap. Eddy
currents in the shim force the flux away from the shim, squirting the flux
deeper into the tape. The reduction in shunted flux raises the efficiency
of the head by requiring less drive power.
The conductive shim is only effective at high frequencies at which large
eddy currents are generated in the shim. As a result, focused gap recorders
utilize bias frequencies that are approximately ten times higher than conventional
systems.
In practical use the silver shim proved to be a major problem because the
soft silver would smear onto the trailing pole piece of the head and short
the head's laminations together.
A second technique, which yields similar results, is the crossed field or
X-field, FIG. 24A. This method typically places a second bias-only head on
the back side of the tape to create a shaped bias flux field jumping from
one head to the other.
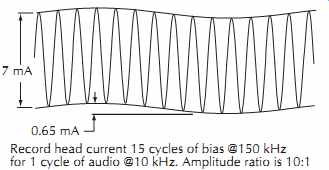 FIG. 25. Record head current.
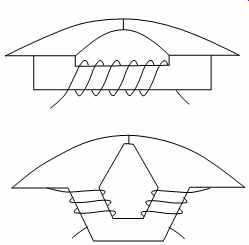 FIG. 26. Hammerhead cores.
3.6.1 Biased or Anhysteretic Recording
The magnetization of the tape particles is not easily changed due to the
memory force or hysteresis of the particles. In fact, the particles have a
form of inertia that must be overcome if a linear transfer is to be achieved.
If a rapidly varying signal of sufficient amplitude to just begin magnetizing
the particles is added to the audio flux signal, the magnetic particles will
more readily conform to changes in the audio waveform. The high-frequency
biasing signal produces a hysteresis-free or anhysteretic recording.
FIG. 25 shows a typical waveform of the current in a low impedance Ampex
record head that is recording 10 kHz at a level of 250 nW/m. The bias component
of 7 mAp-p is approximately ten times larger than the 10 kHz component at
650 µA. (The voltage waveform across the record head would be totally dominated
by the bias component due to the 6 dB/octave rise in head impedance with increasing
frequency, in this case 35 V of bias versus 500 mV of 10 kHz or 70:1.) The
audio and bias signals must be added together in a linear manner without generating
any of the sidebands that are present in either amplitude or frequency modulation
techniques. The short- wavelength bias signal can therefore be easily filtered
out during playback by the gap and thickness losses so that only the audio
signal remains. (The high level of bias signal transformer crosstalk that
is present during sync/overdub operation requires a sharp notch filter in
the playback preamplifier to remove the bias signal.) Typical bias frequencies
range from 100 kHz for slow-speed recorders to over 10 MHz for high-speed
tape duplicators. Although high bias frequencies are desirable to permit easy
filtering and thorough tape excitation, a practical upper limit for mastering
recorders is reached at 500 kHz due to a combination of increased eddy current
and hysteresis losses in the core and the increase in bias drive voltage required
due to the inductance of the head.
Head losses can be reduced by using a very small core to reduce hysteresis
losses and by choosing either thin laminations or a ferrite material to reduce
eddy current losses. If, however, the record head will also be used for the
reproduce function during sync/overdub, a small core will cause serious long-wavelength
contour effects. The compromise hammerhead design shown in FIG. 26 improves
the playback performance of the small core by adding extensions to the face
of the core.
The tips function only to play back low-frequency signals for which core
losses are insignificant.
The bias voltage required to drive a record head doubles each time the bias
frequency is doubled due to the inductance of the record head. To keep the
required bias voltage within the range of common integrated circuits, the
inductance can be lowered either by reducing the number of turns in the winding
or by lengthening the gap. Reducing the number of turns once again degrades
the sync/overdub performance by reducing the playback voltage generated by
the head.
Heads with very low inductance typically require a step-up transformer to
achieve adequate playback SNRs, but the transformer will also contribute some
additional small amounts of distortion, noise, and frequency response anomalies.
Lengthening the record head gap will reduce shunting and give better bias
penetration into the tape, but the short-wavelength sync/overdub response
will suffer greatly.
A more straightforward approach to optimize the record head for both recording
and playback is to use separate flux paths or windings for each of the functions.
One simple method of switching windings and flux paths is to use parallel
paths that can be selectively blocked. As shown in FIG. 27, when the high-inductance
playback winding is shorted, flux will be blocked from the playback shunt
magnetic leg of the core, effectively eliminating this path and thereby forcing
all of the flux from the low-impedance bias winding to the front of the head.
During reproduce, when the bias winding is shorted, the flux picked up from
the tape will pass only through the reproduce winding. Although the cost of
this dual-winding head is significantly higher than for a conventional single-path
design, each coil can be optimized for its intended function without the need
for compromise, yielding playback-to-record inductance ratios of up to 1000:1.
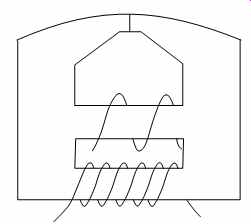 FIG. 27. Dual winding record head.
cont. >>
|