GIVING RECORDS THE BRUSH-OFF
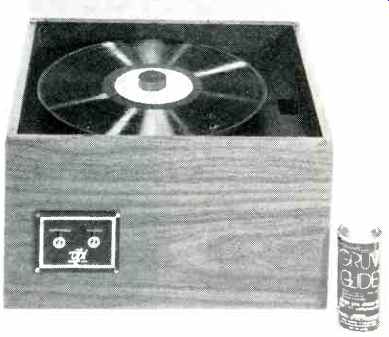
above: Pristine surfaces result from treatment with the HW-16 cleaning machine
followed by Gruv-Glide.
This month some brief reports on diverse items of audio equipment which I
have found to be particularly interesting and worthwhile.
The vinyl phonograph record can be a wondrous thing. If the requisite tender
loving care has been applied in the plating and pressing processes and the
vinyl is virgin and of unquestioned purity, one can enjoy rock or Rachmaninoff
from immaculate record surfaces, blissfully free of the snaps, crackles, pops
and other extraneous noises that plague record playback.
Unfortunately, the vinyl record is also an extremely fragile thing. The vinyl
is relatively soft and is particularly prone to the generation of electrostatic
charges. This attracts dirt and dust, which is deposited into the record grooves.
To make matters worse, even at a tracking force of one gram, enormous instantaneous
pressure and heat are generated at the stylus tip and the dust is ground into
and welded to the record grooves. Surely, no thinking person handles records
so carelessly that they are covered with oily, dust catching fingerprints.
However, people do leave records on turntables after playback, where dust can
settle on them. Even the mere act of withdrawing and replacing the record in
its protective sleeve can induce static charges. Cigarette smokers create their
own particular problems. Some years ago, the late Percy Wilson of that venerable
British journal "The Gramophone" made a series of studies which showed
that fly ash produced by cigarette smoke was readily attracted by static charges
on records. He also noted that heavy smokers created enough smoke so that various
tars and other contaminants were deposited on vinyl records. From these studies,
the well-known Keith Monks record-cleaning machine evolved. The efficacy of
Keith Monks machines have been well documented and many of them are in use
throughout the world. However, the high price of the Keith Monks cleaner has
made it an item more for institutional and commercial use than for audio consumers.
An "economy" model of the Keith Monks cleaner was introduced, but
at $995.00 it is still beyond the reach of most audiophiles.
The average audiophile appears to be fairly conscientious in caring for his
records, a fact which has produced a myriad of commercial record-cleaning and
anti-static devices and chemical agents. Many of these products are long on
exaggerated claims of efficacy and short on actual results. Some are close
to being outright frauds. Most.
merely rearrange the dust, and few indeed are those which are genuinely helpful.
The main problem with most of these agents is their tendency to leave sticky
residues in the record grooves, thus further exacerbating the dust problem.
It also makes the stylus more prone to pick up this amalgam of grunge.
For some months now, I have been enjoying the benefits of immaculately clean
records through the use of the HW-16 record-cleaning machine made by VPI Industries
of Ozone Park, N.Y. Harry Weissfeld, the entrepreneurial head of VPI, has come
up with a device that embodies many of the basic essentials of the Keith Monks
machine, albeit in much simplified form. The HW-16 measures 15 1/2 in. W x
14 1/4 in. D x 9 in. H. The cabinet is walnut veneer, and the top cover is
of smoked plexiglass. There is a 12-inch turntable platter driven by a very
high torque motor at 18 rpm. The turntable spindle is threaded to accept a
1 1/4-inch Lucite hold-down clamp. The turntable is activated by a toggle switch
on the front panel of the unit. On the underside of the plexiglass cover is
a vacuum suction chamber, and when the lid is in the closed position the chamber
is connected to a high-capacity vacuum pump. A four-inch brush with a high
density of specially shaped nylon bristles is supplied, as is a plastic squeeze
bottle of 25% isopropyl alcohol. When using the HW-16, a record is snugly clamped
to the turntable by the threaded Lucite clamp. The brush is saturated with
the alcohol (I also dribble a thin stream of alcohol around the middle of the
modulated portion of the record) and positioned so that the tips of the bristles
engage the grooves in the direction of record travel. The turntable is switched
on and the brush held against the record for about 20 seconds. The brush is
then removed, the top cover closed, and the vacuum device activated by another
front-panel toggle switch. I have found in practice that more efficient removal
of the alcohol/dirt sludge can be accomplished by exerting a moderate downward
pressure on the cover in the area over the vacuum device. The vacuum is maintained
for about 15 seconds, and then both turntable and vacuum are switched off.
The record is removed, the brush flushed clean under running water, and the
procedure repeated on the other side.
I have found the HW-16 to be an outstanding performer. The record surfaces
are microscopically clean and are so pristine they look new! It must be noted
that the machine does not attenuate the sounds of scratches or other surface
blemishes, but a lot of the crackly, steady-state noise due to dirt in the
grooves is substantially reduced.
A few notes on my experiences with this unit. Even though the alcohol solution
is on the record surfaces a relatively short time, some slight leaching of
ingredients in the vinyl compound which migrate to the surface does occur.
This causes a slight increase in "stiction" (stick/slip friction)
on the record. This condition can be overcome by a very light application of
GruvGlide. It should also be noted that the alcohol cleaning process is not
antistatic and in fact induces a moderate charge on the record. Thus, the GruvGlide
not only lubricates the grooves but also reduces static on the record.
Alternatively, the freshly cleaned record can be zapped with a Zerostat anti-static
pistol. Brand-new records may look great to the naked eye, but the grooves
are actually full of record jacket lint, cardboard motes, vinyl shreds and
other assorted debris. Run the brand-new record through the HW16 and you'll
have a better chance of getting and keeping quiet record surfaces.
Another point is that ethyl alcohol (ethanol) causes less leaching than isopropyl
or methanol. To get ethanol of the highest purity, one can buy a quart of 100-proof
vodka, which means the fluid is 50% alcohol. Dilute this bottle with a quart
of distilled water and the result is a half-gallon of 25% ethanol. The price
of the HW-16 is $295.00. Not cheap, but obviously it is a good item for an
audio club, or the cost can be shared among several friends with extensive
record collections. The HW-16 is simple, efficient and is most highly recommended.
In the July 1982 issue of Audio, my colleague Barney Pisha gave an excellent
review of the Dennesen ABLT-1 air-bearing linear tracking tonearm. I am also
using one of these remarkable tonearms, and feel that the accolades Barney
gave to this arm are fully justified. It is true the Dennesen ABLT-1 is a bit
tricky to set up. Overhang adjustment must be precise, and the tone arm must
be absolutely level. Satisfy these two parameters, and the air bearing provides
the frictionless tracking that permits the arm to operate without lag or deviation
from true tangency to the record groove.
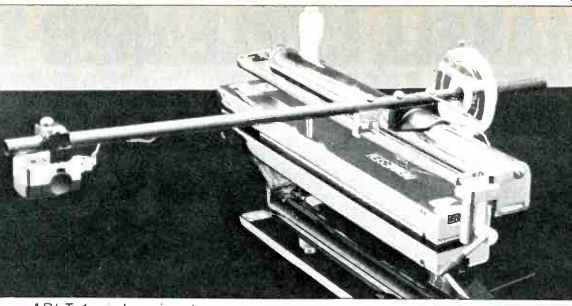
above: Dennesen ABLT-1 air-bearing tonearm.
I bring up the Dennesen tonearm because of a particular incident. In my column
last month I mentioned Professor van den Hul in connection with the new EMT/van
den Hul moving-coil phono cartridge. At the SCES, the Professor had given me
a cartridge to try.
At home, I had mounted it in one of the best conventional pivoted tonearms,
and during a visit the Professor listened to it and pronounced that I had set
it up properly, especially in regard to the all-important azimuth. I was pleased
by his comment. However, I remarked that I really wanted to use the cartridge
in the spare arm tube of the Dennesen tonearm which I had not yet set up. The
Professor promptly called for tiny screwdriver, long-nosed pliers, etc. and
proceeded to install the cartridge in the Dennesen arm.
After everything was adjusted we played the same passage from the Mahler Fourth
Symphony, at the same level as when the cartridge was in the conventional tonearm.
The differences were dramatic. Bass was much fuller and better defined, midrange
had more clarity and projection, the treble was smoother, imaging was more
precise, and the gain in depth perception was marked. This was a most convincing
demonstration of the superiority of the Dennesen air-bearing tonearm. For those
who can afford it, this is unquestionably the tonearm of choice.
-----------
(Source: Audio magazine, Nov. 1982;
Bert Whyte
)
= = = =
|